Category: Selvedge Jeans
Rivets
With the sewing out of the way, we can finally move on to attaching the rivets. You’ll need an awl, small metal anvil, rivet and backing, optional leather washer, a hammer, and the rivet setting too (not pictured).
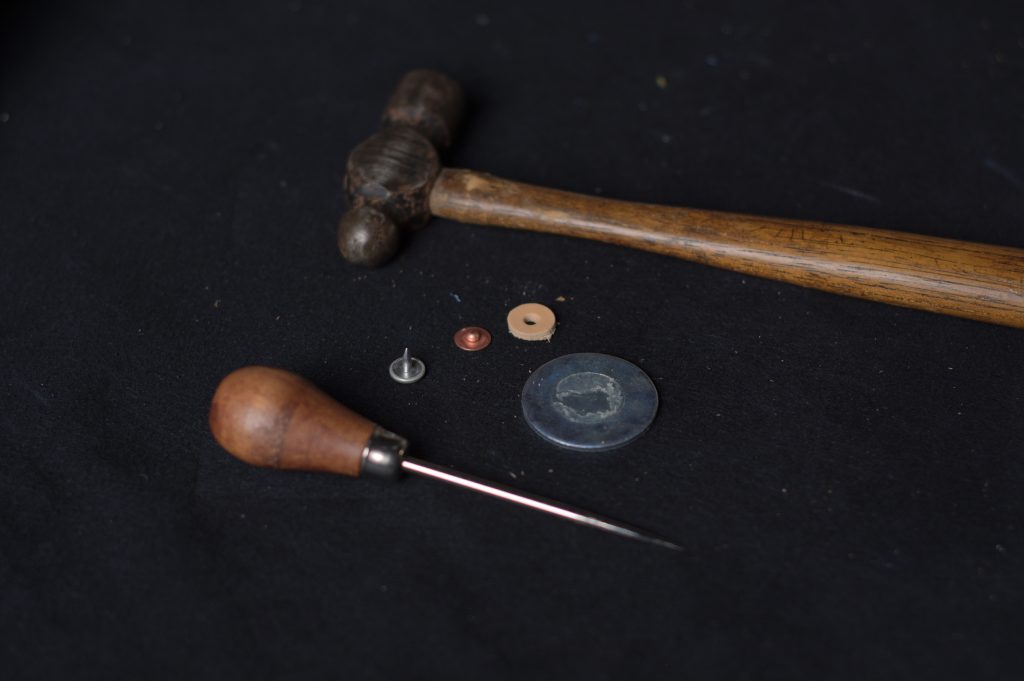
The best way to go about finding the position of the rivets is to use the awl to poke through the fabric from the right side. The first rivet is at the top edge of the front pocket opening, about 1/4″ from the waistband.
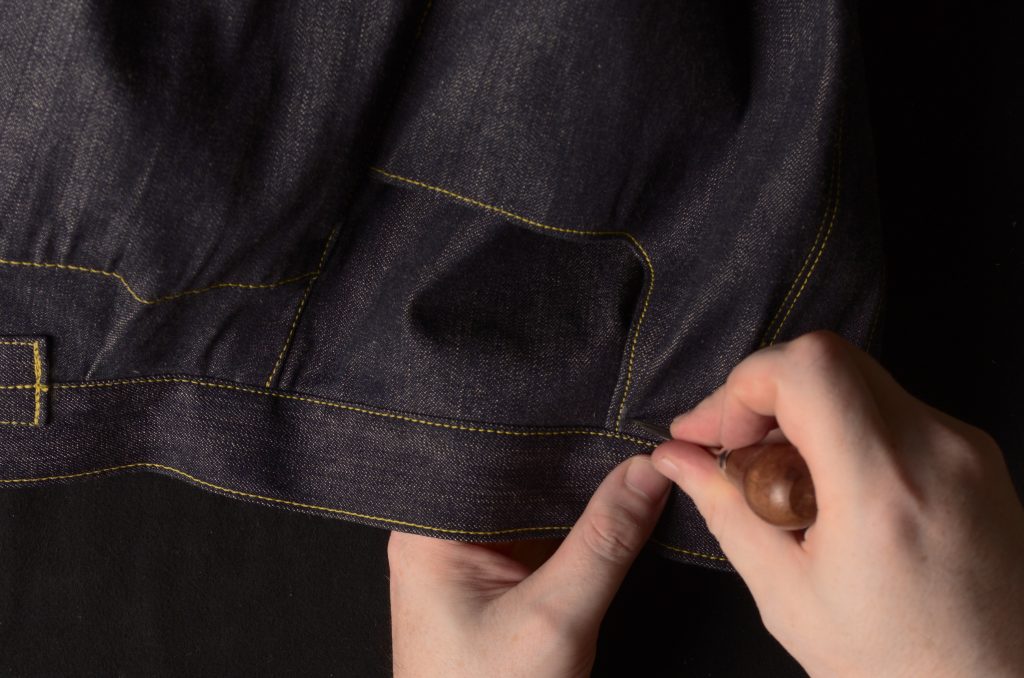
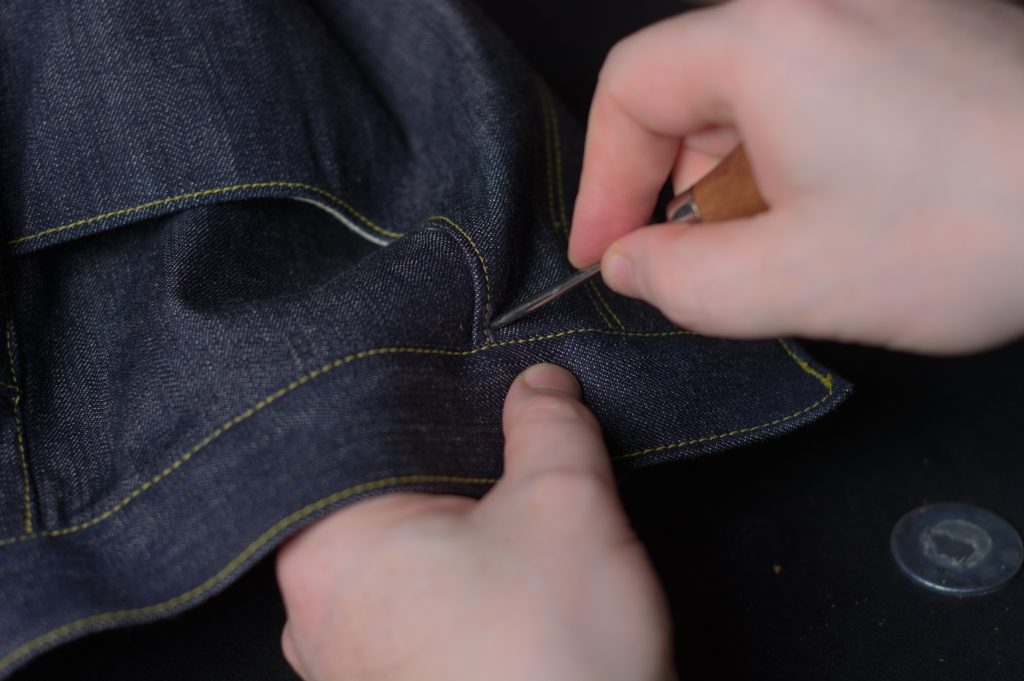
I then like to open the hole from the back as well.
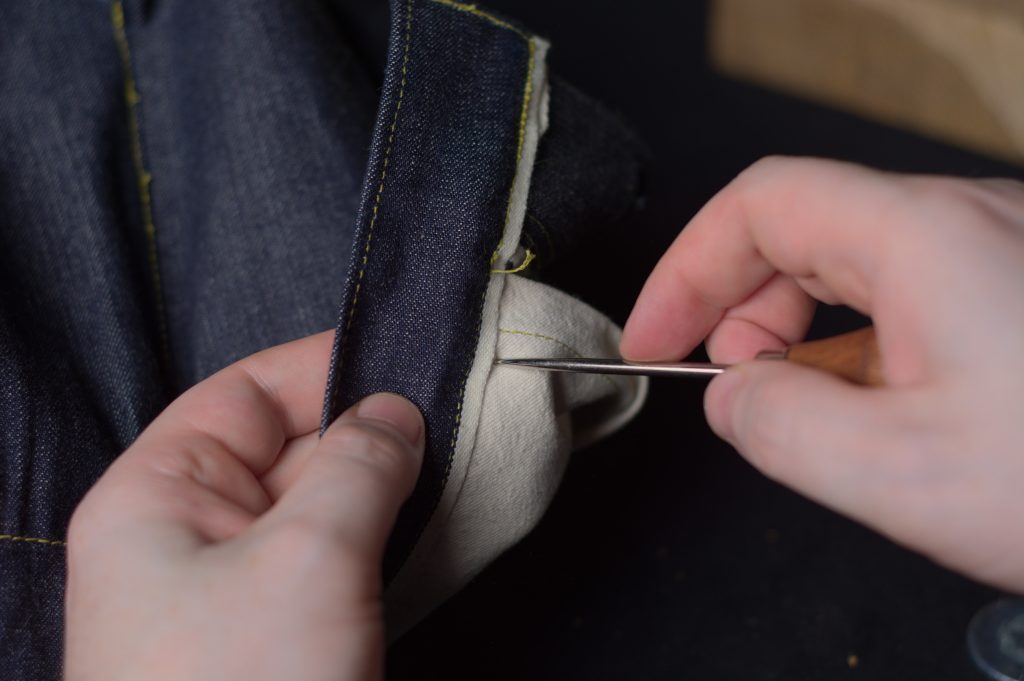
Insert the rivet backing into the leather washer (optional).
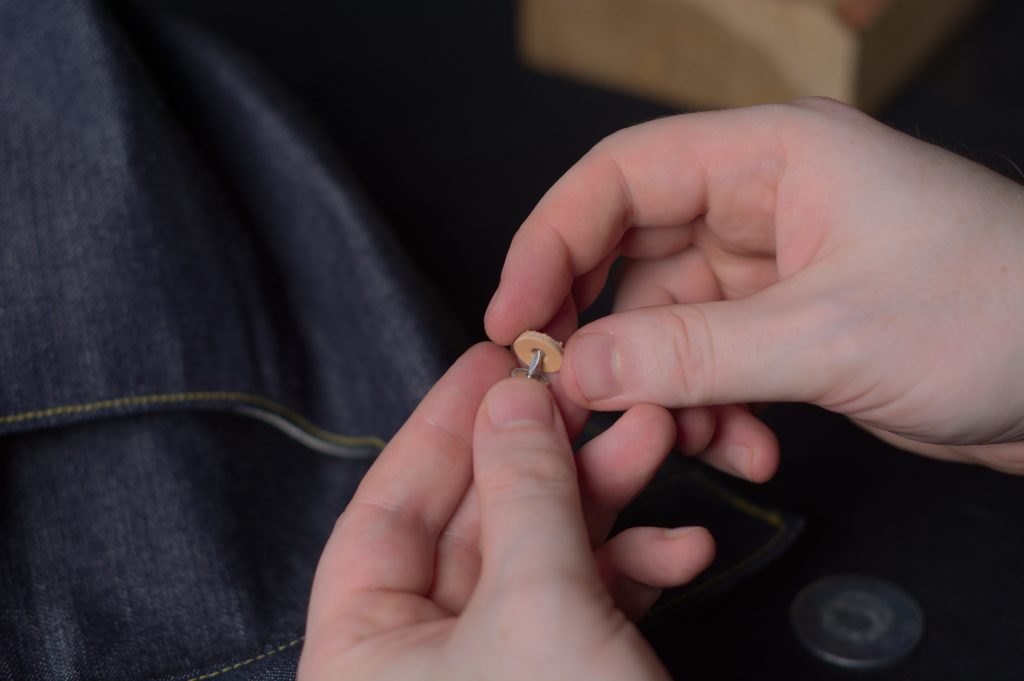
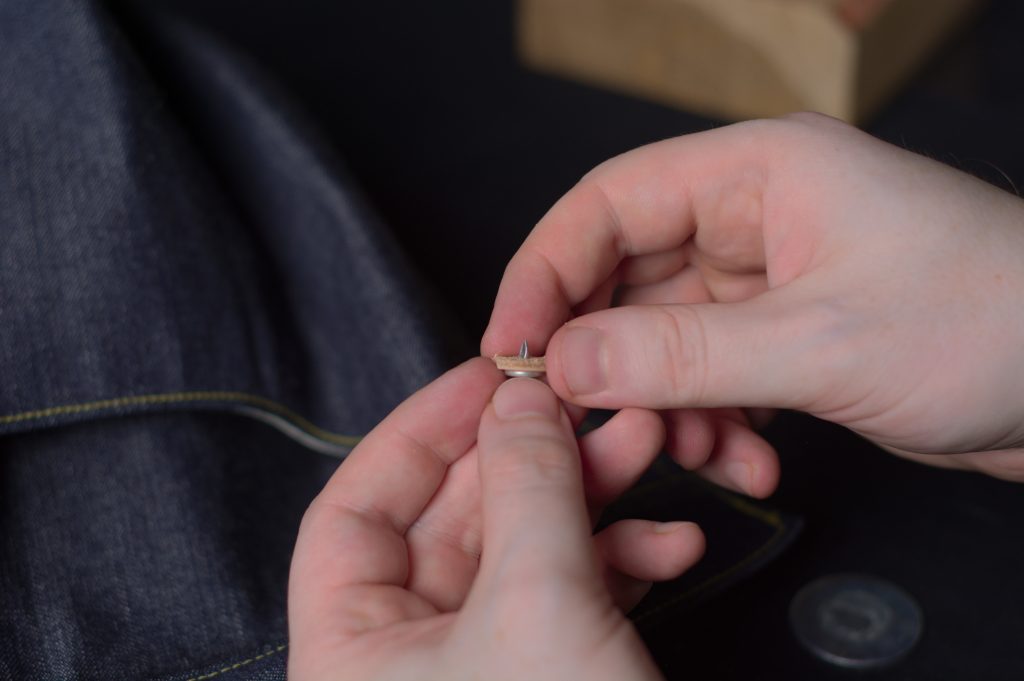
And insert the backer into the hole from the wrong side.
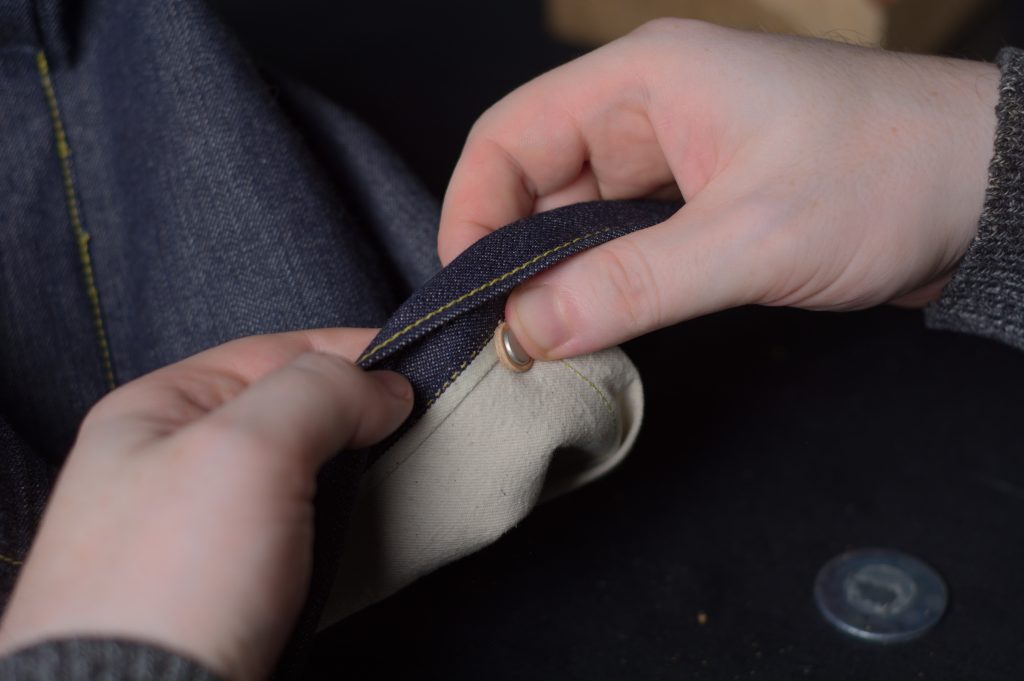
Place the assembly onto the anvil. Using a block of wood is helpful to get a good set to the rivet and avoid damaging the table.
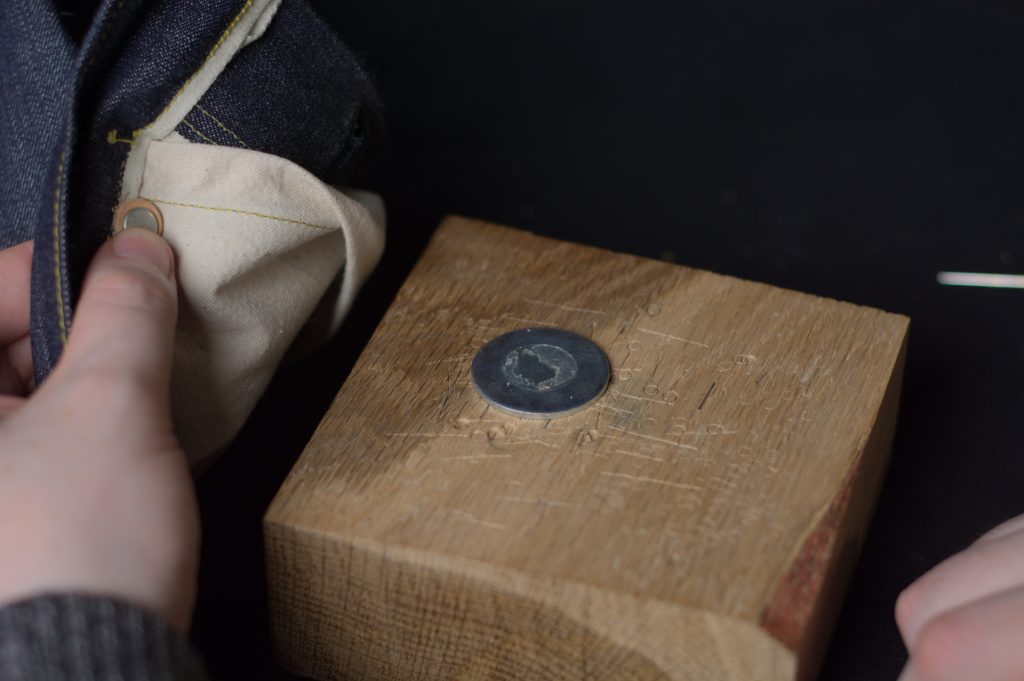
Place the rivet on top of the assembly, and then place the tool over the rivet.
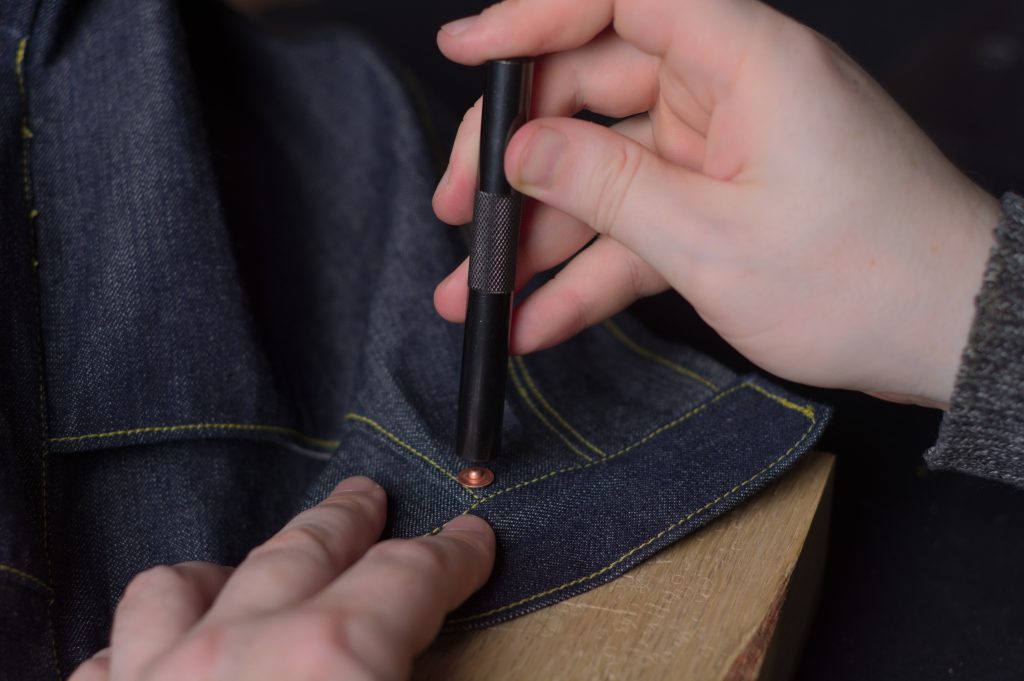
Give the tool a few light taps to start and then firmly secure the rivet. It will compress the fibers underneath, and the backing will spread out under the rivet, hopefully permanently securing it. But if you don’t hit it strongly enough, it is possible for it to come undone.
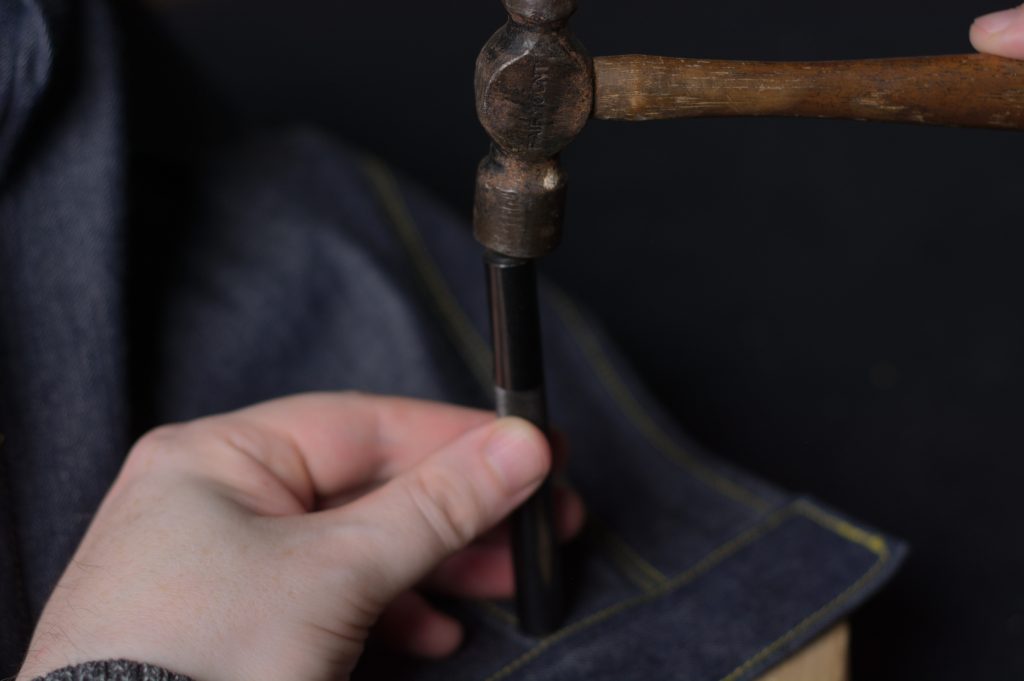
And here’s the set rivet.
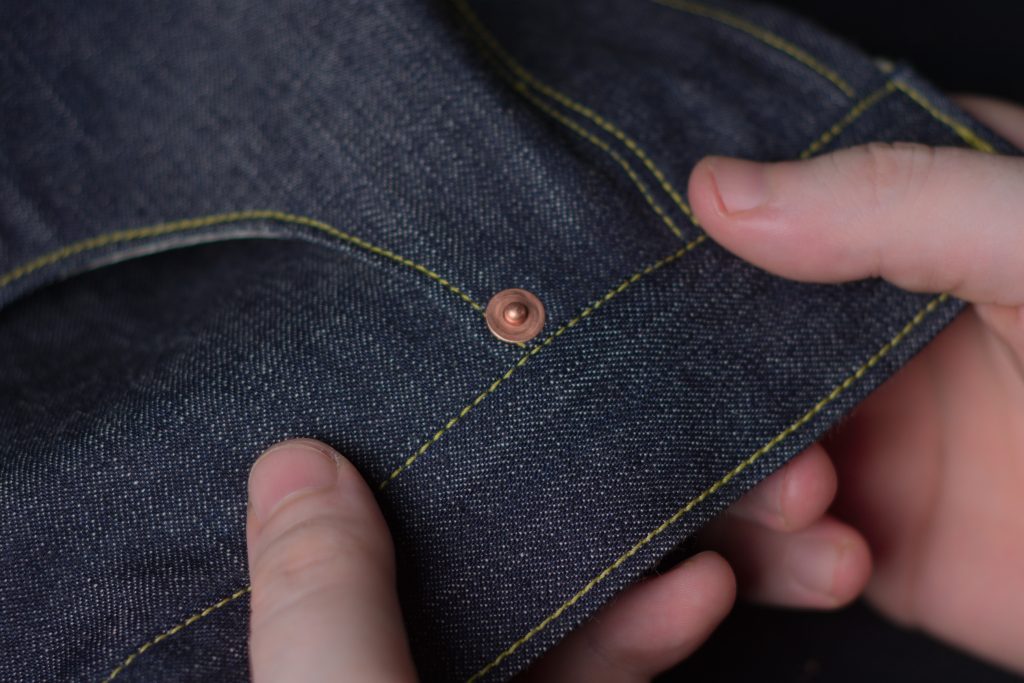
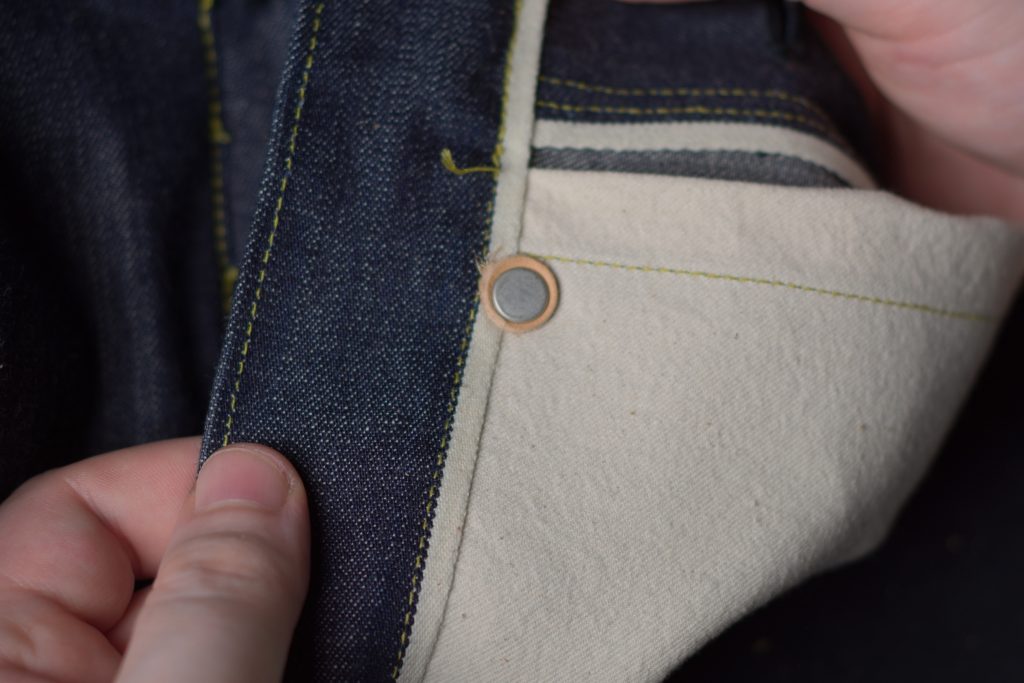
Repeat for the lower half of the front pocket opening, the top of the watch pocket (though not on the 1873, let me check on that . . .), the tops of the back pockets, and optionally the bottom of the fly (for the 1873 version).
The Back Cinch Belt
To put together the back cinch belt, you’ll need your pattern, a length of selvedge denim, and a jeans belt buckle.
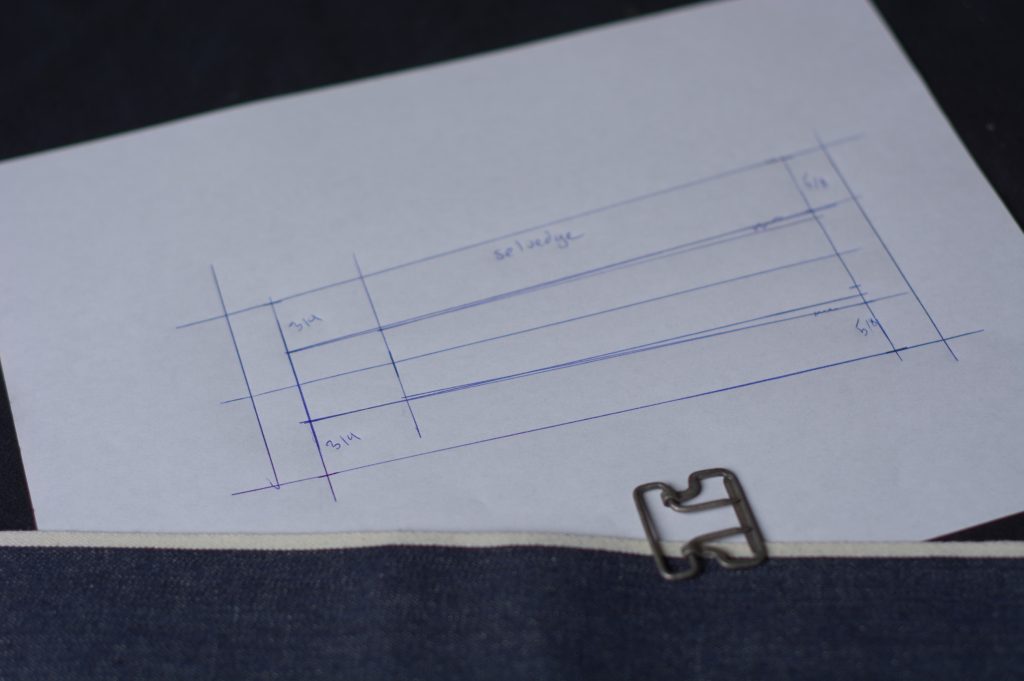
Trace out the pattern onto your denim, being sure to mirror it for the other side, and keeping one edge on the selvedge. You could also add an additional seam allowance for turning under instead of using the selvedge, if you prefer.
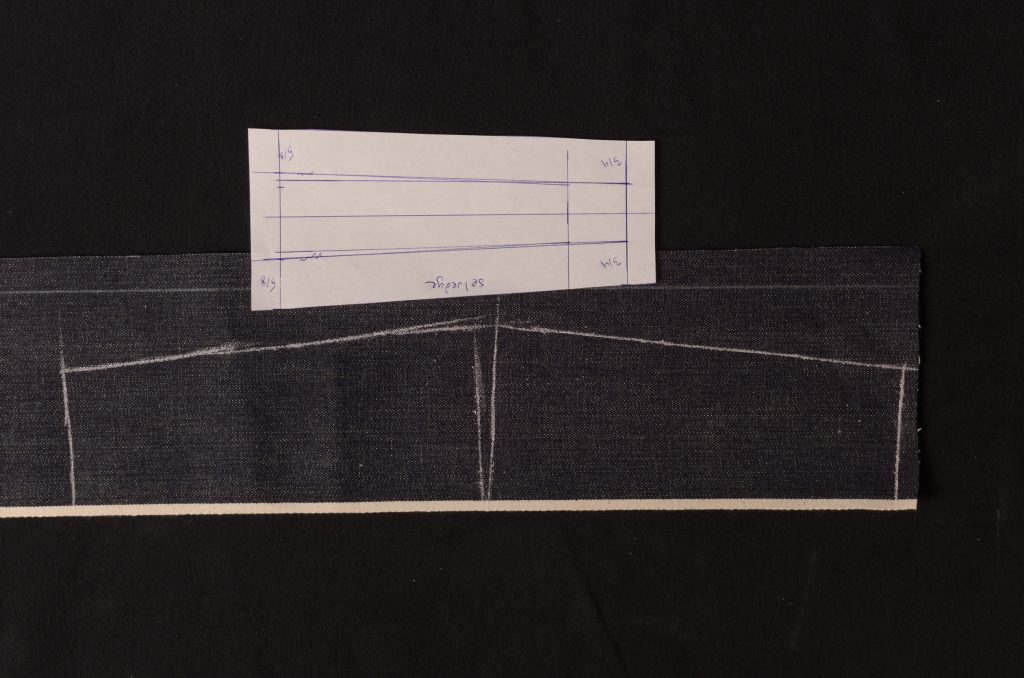
Cut out the pieces, and then place the pattern on top. Align the ruler with a long edge, flip the paper back, and trace the finished seam line onto the denim. Repeat for the other long edge and the two short ends, on both pieces.
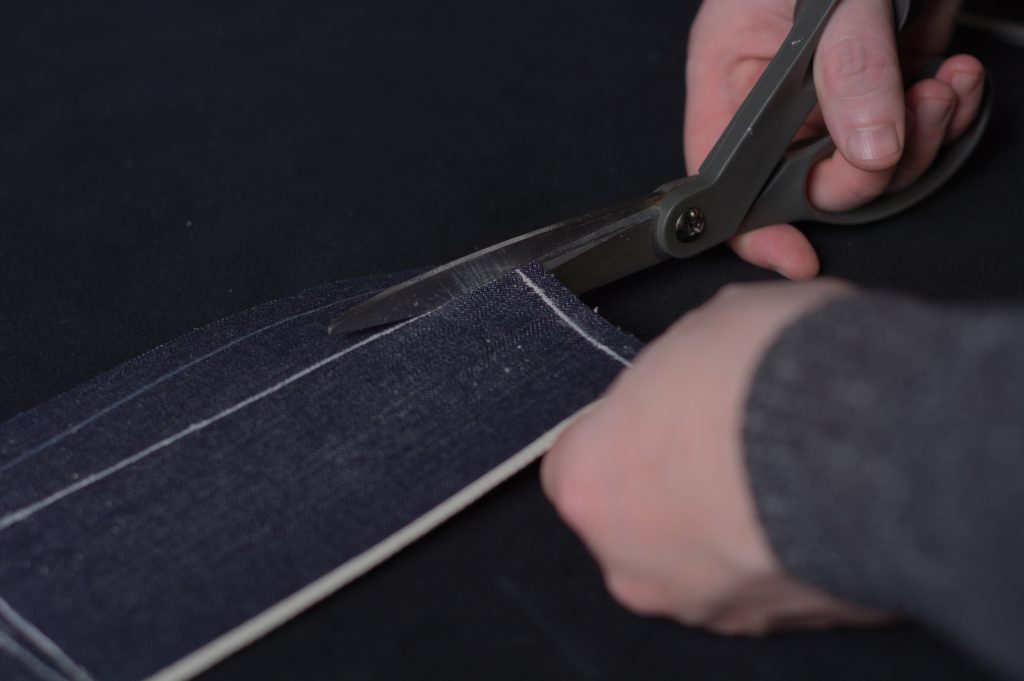
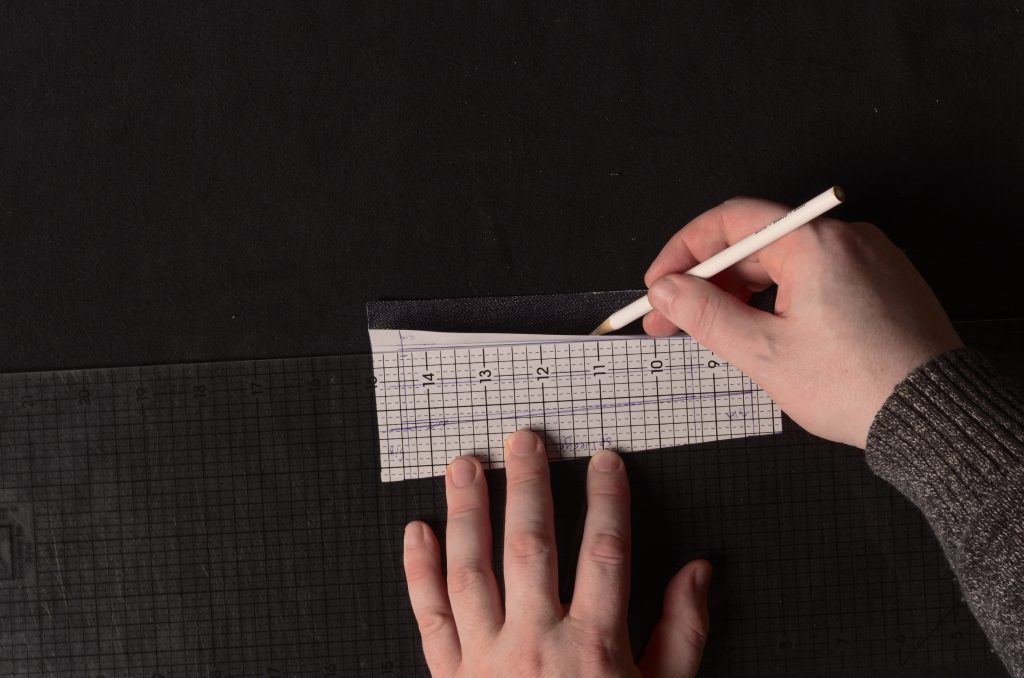
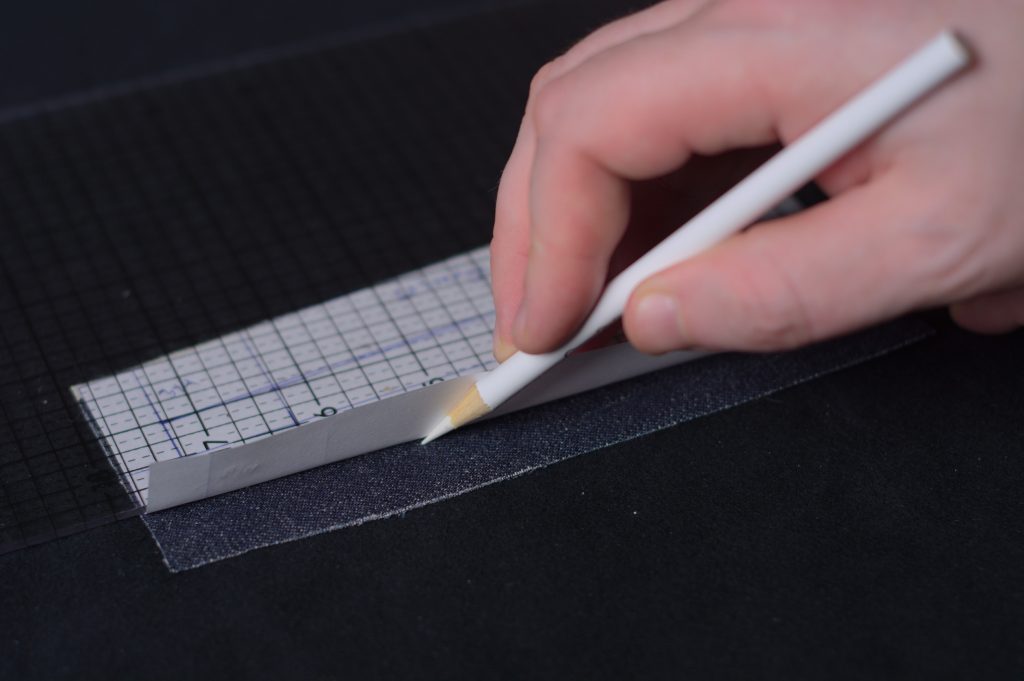
Here’s what you should be left with.
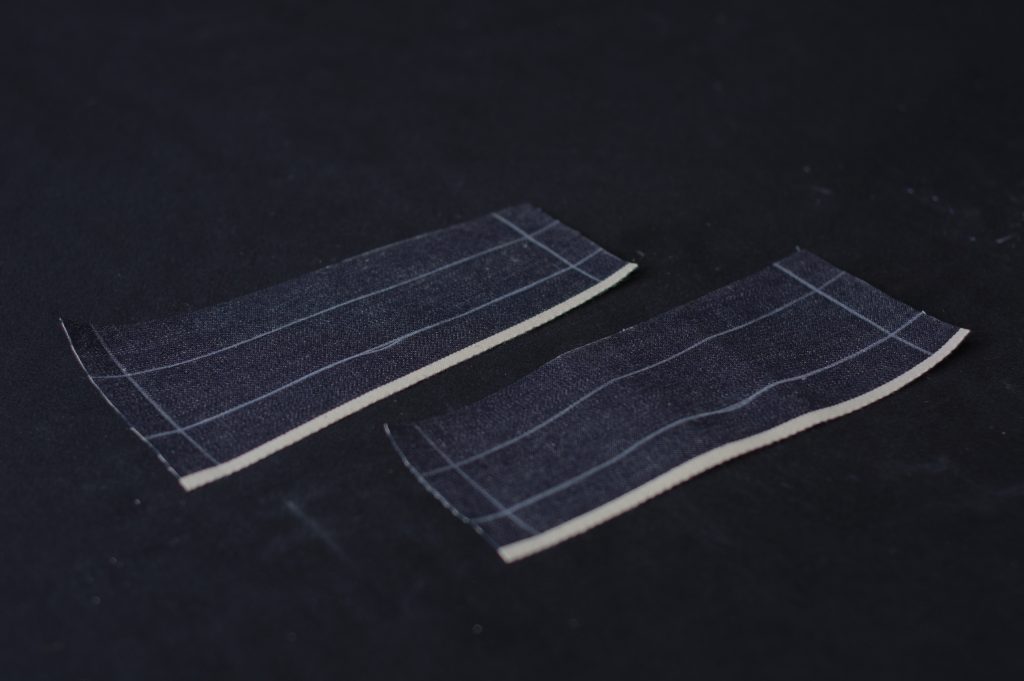
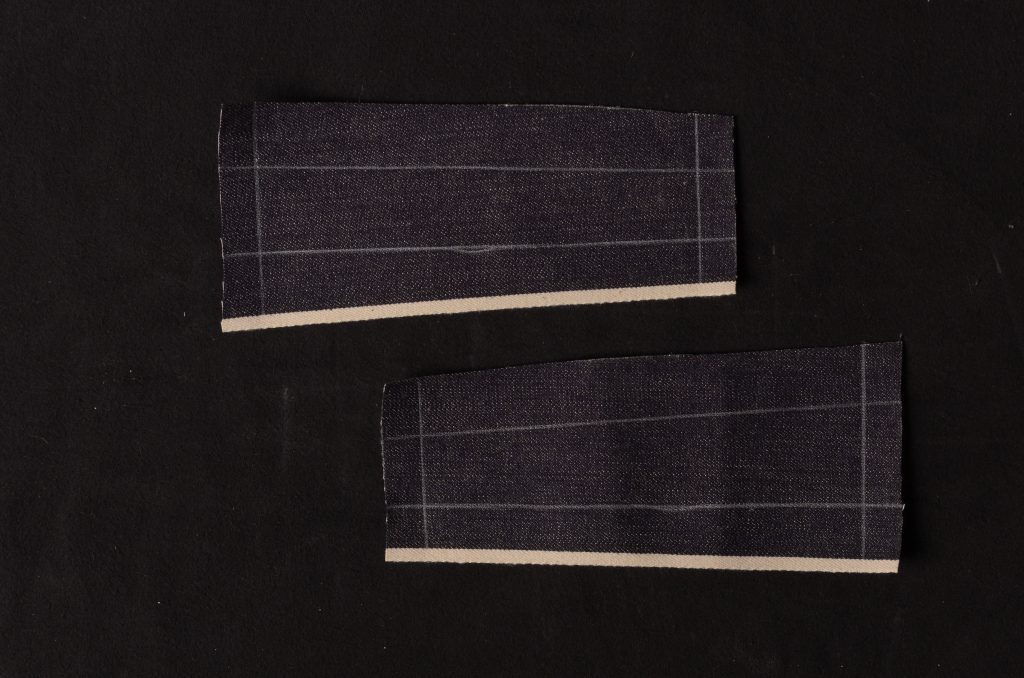
Press over the seam allowances on both ends, just barely bringing the chalk lines to the wrong side.
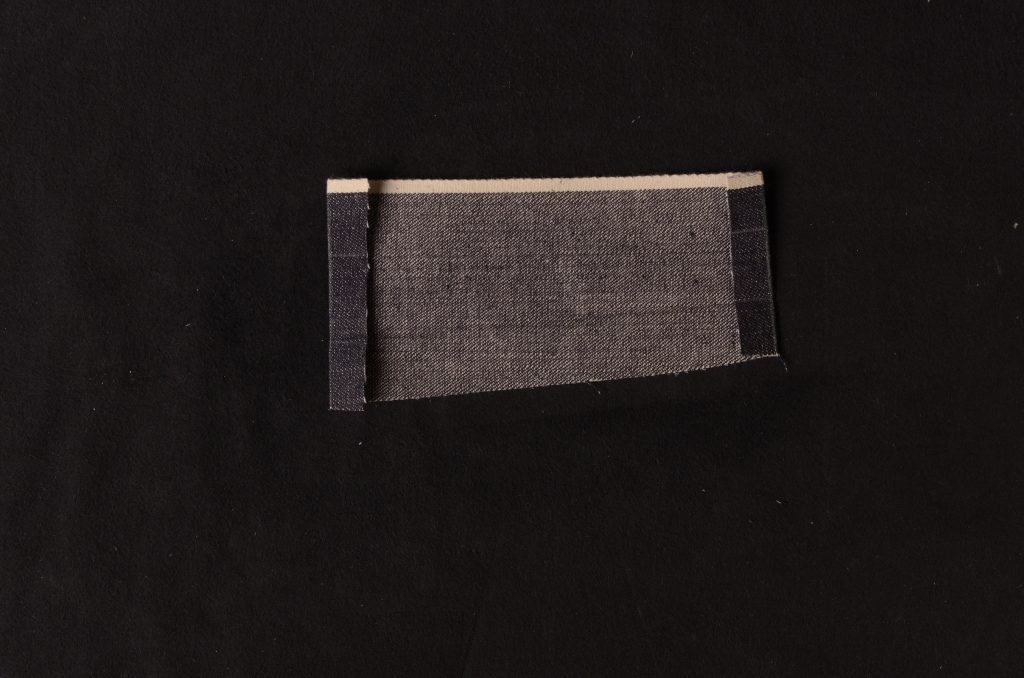
Press over the raw non-selvedge edge.
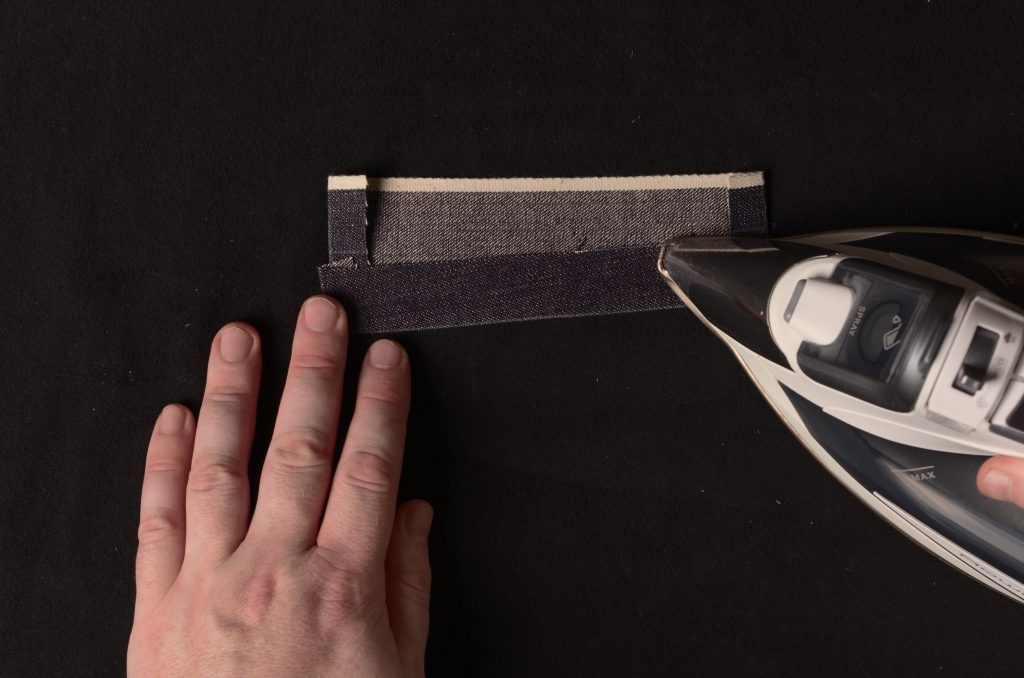
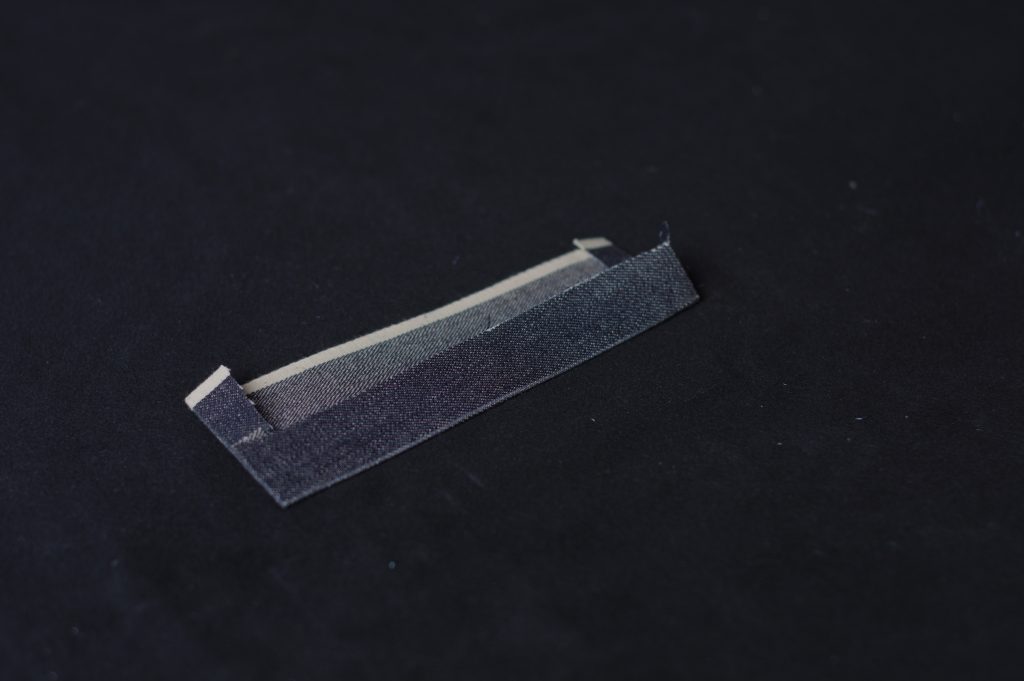
And then fold and press the selvedge seam allowance over everything. Tidy up the ends as necessary.
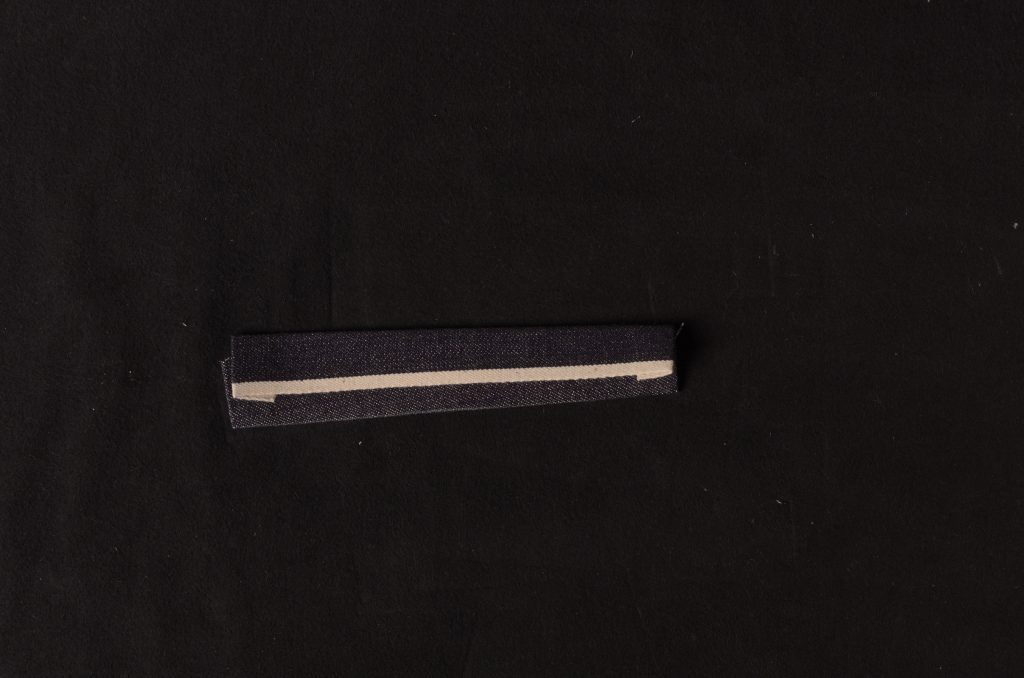
Just tidying up the end here, making sure the seam allowances are all falling into place properly.
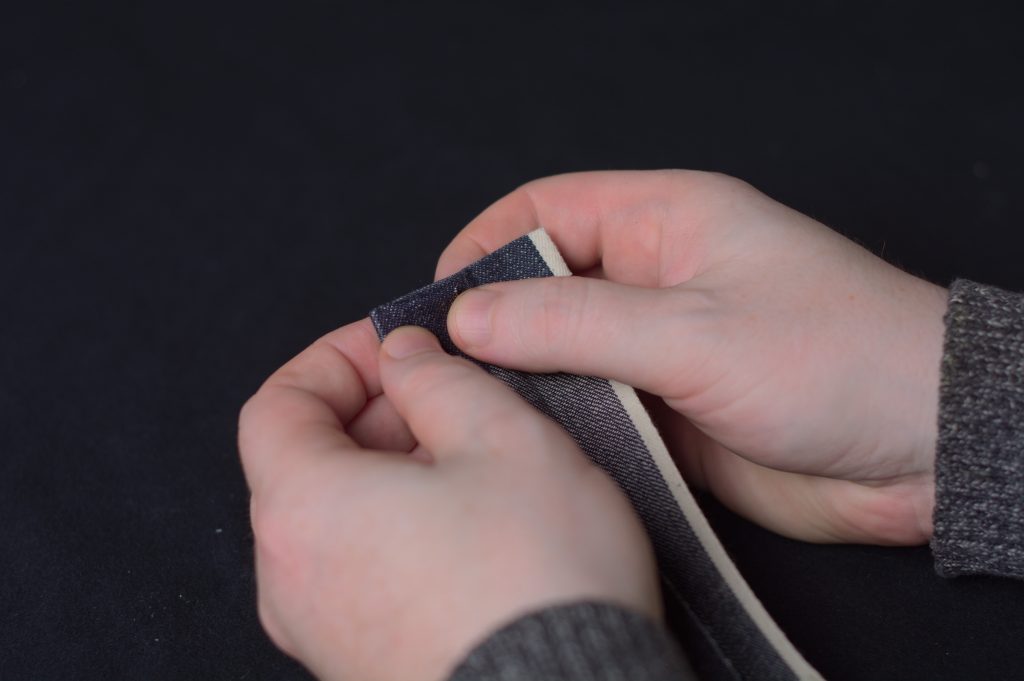
Draw in the center line across the length of the cinch.
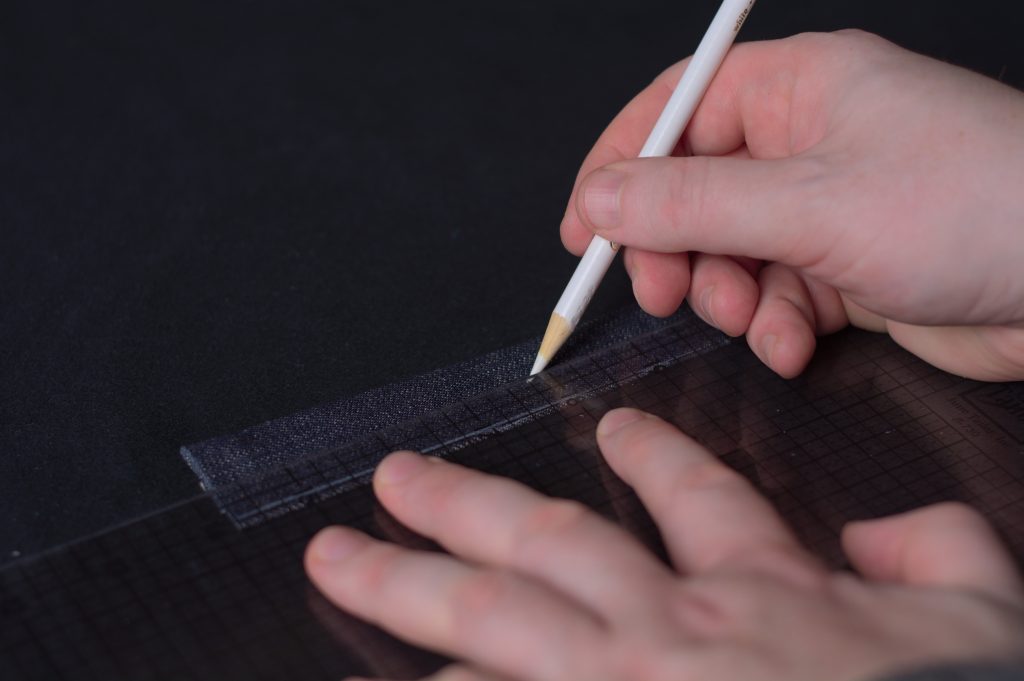
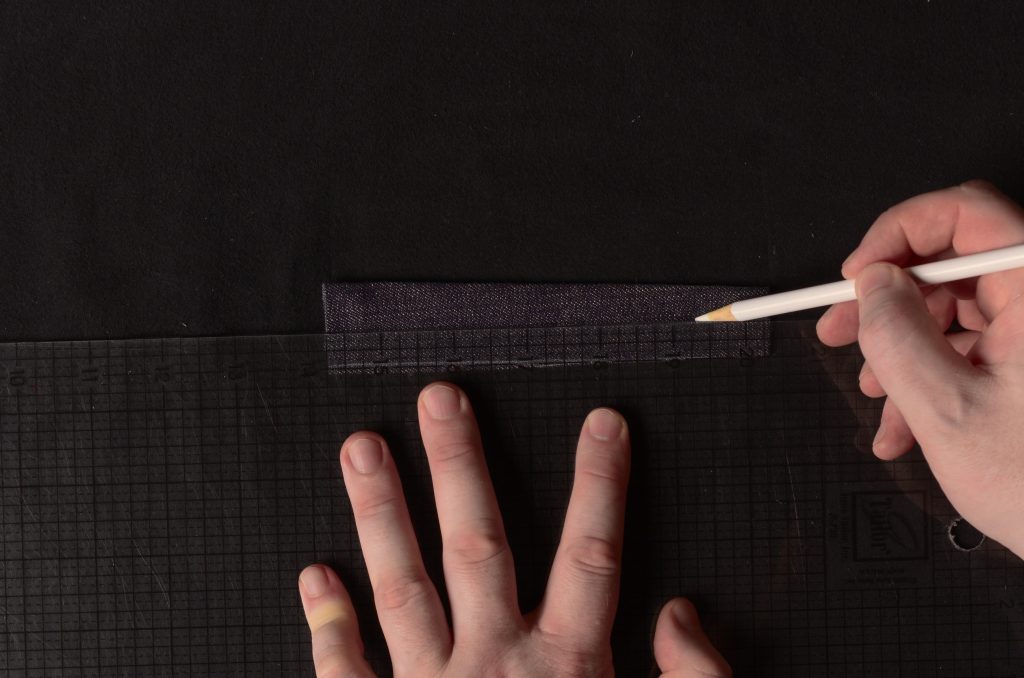
Here are the results so far. You’ll want to make sure both pieces are identical in size, and that the back buckle actually fits, and adjust as necessary. I usually have issues with one or the other.
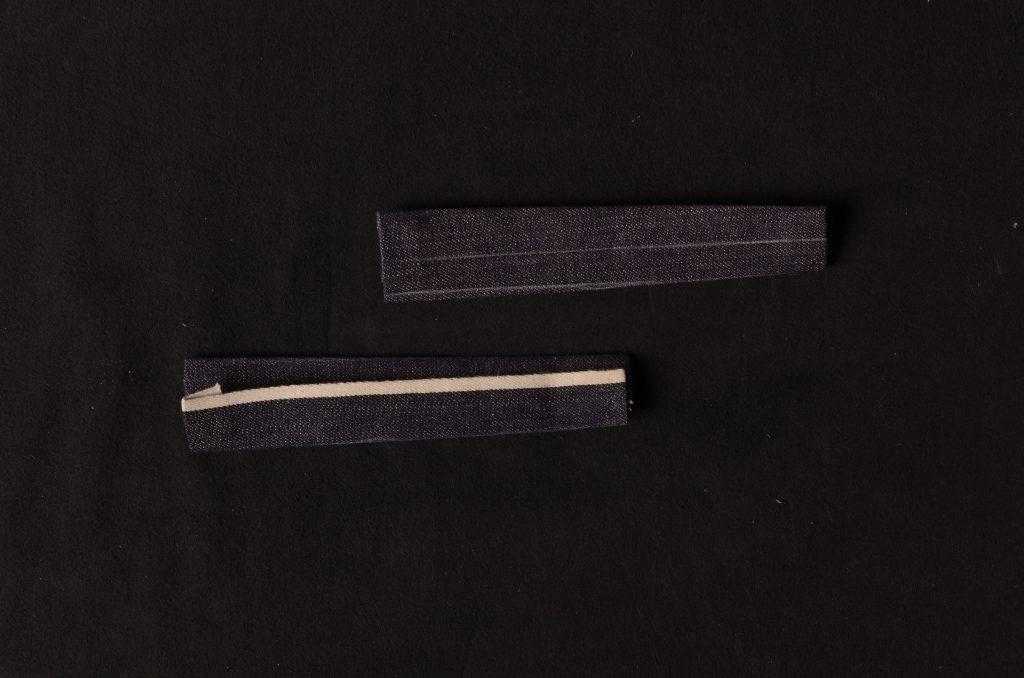
Keeping everything in place firmly using your fingers, sew across the length of the cinch belt from end to end.
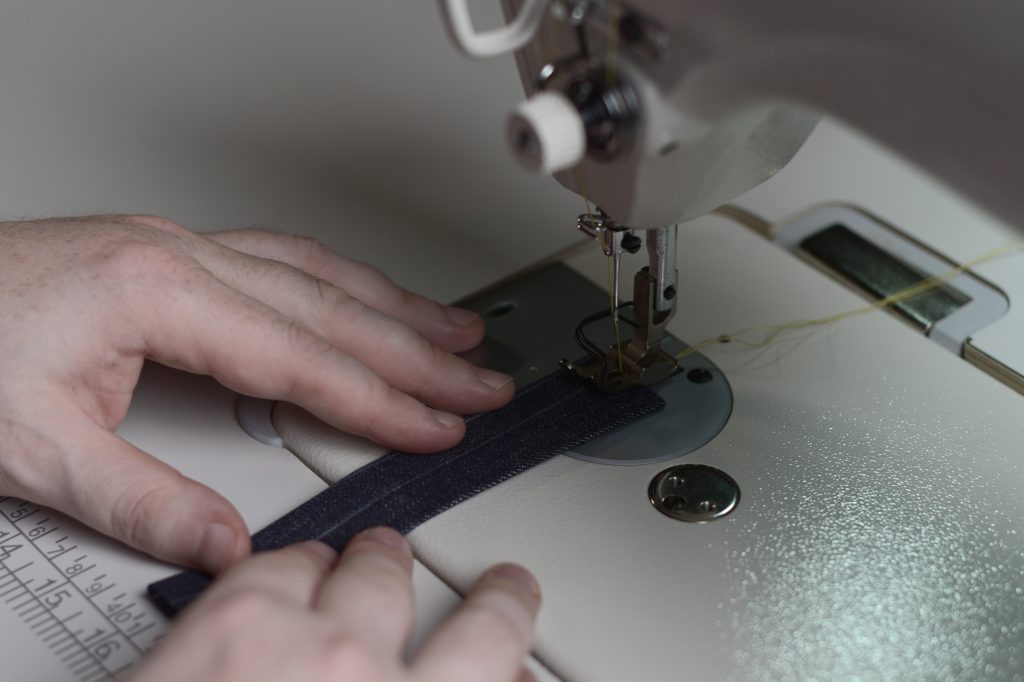

If everything has been drafted correctly, you should have the stitches aligned with the selvedge underneath (yours may have more or less selvedge beyond the stitching than I do).
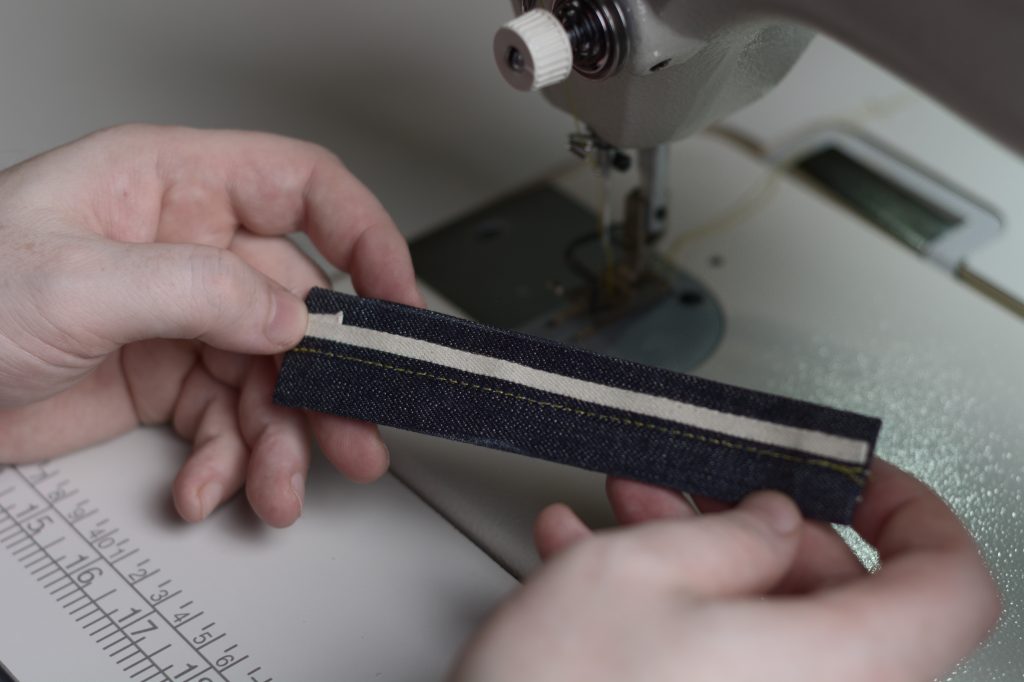
Now take up the left cinch belt (the selvedge should be pointing down when you look at it from the right side).
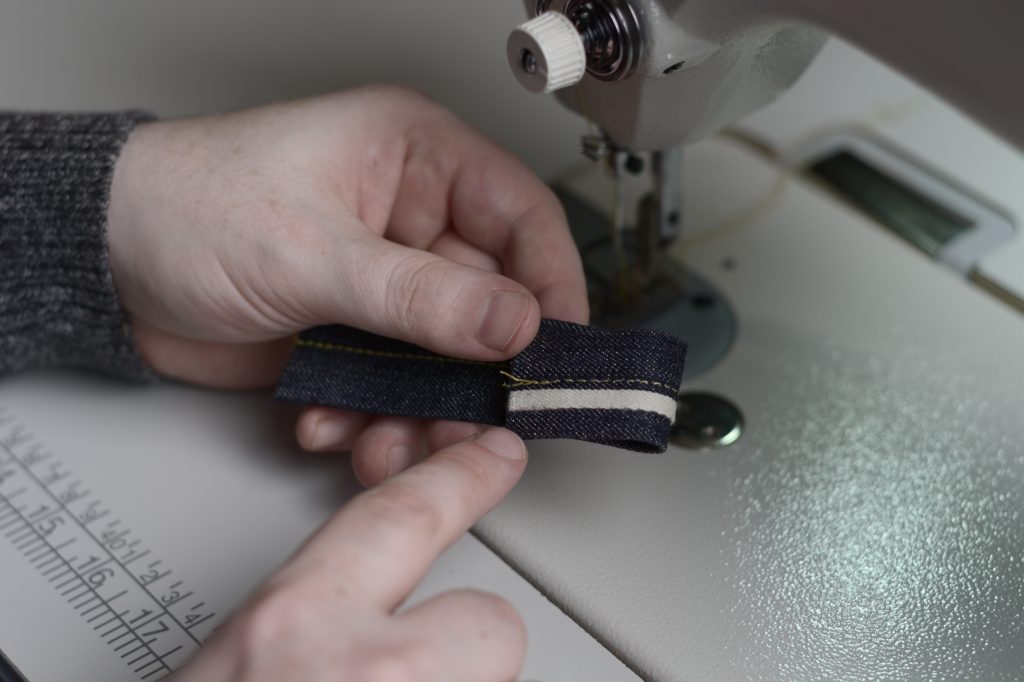
Slide the buckle on, ensuring it’s facing the correct direction, and overlap the back on itself by about 1″.
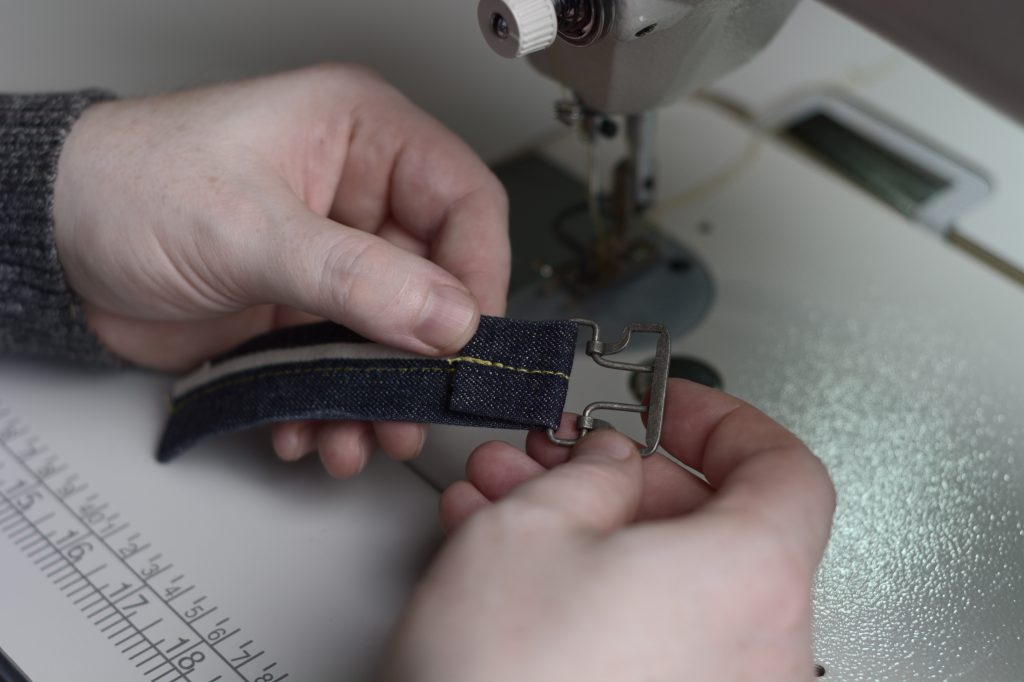
Secure the buckle by top stitching through all layers. If you have a zipper foot, this is a good time to use it, though I tend to use a regular foot and just be super careful about not running into the metal with my machine needle.
For the 1873 jeans, they used a simple box stay here as shown. I like to double back on the stitching to make it extra secure.
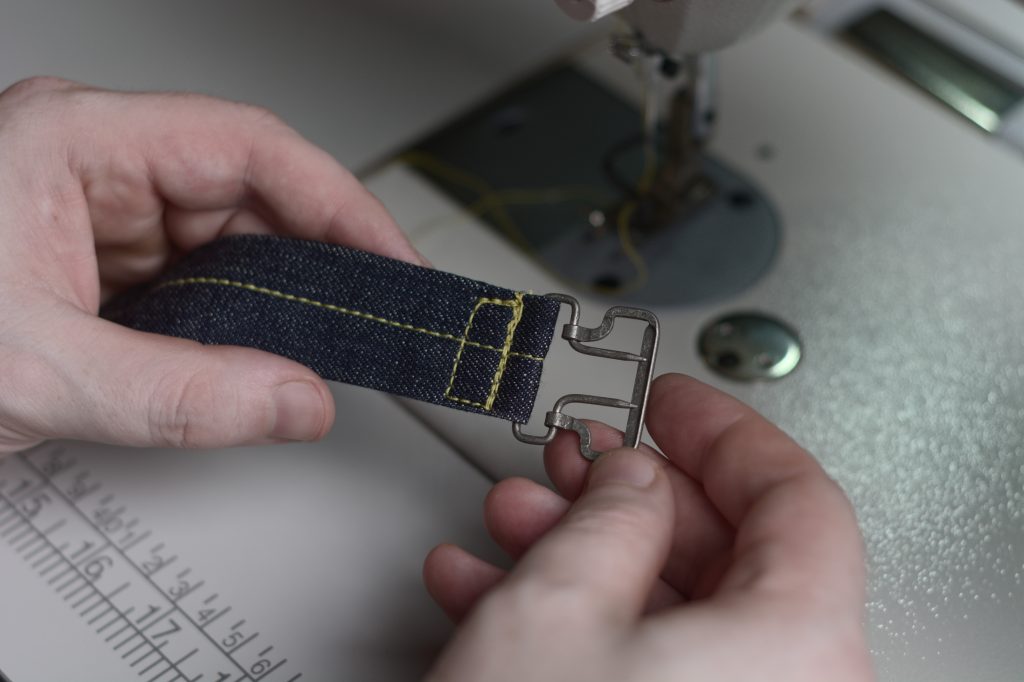
Here’s what it looks like from the wrong side.
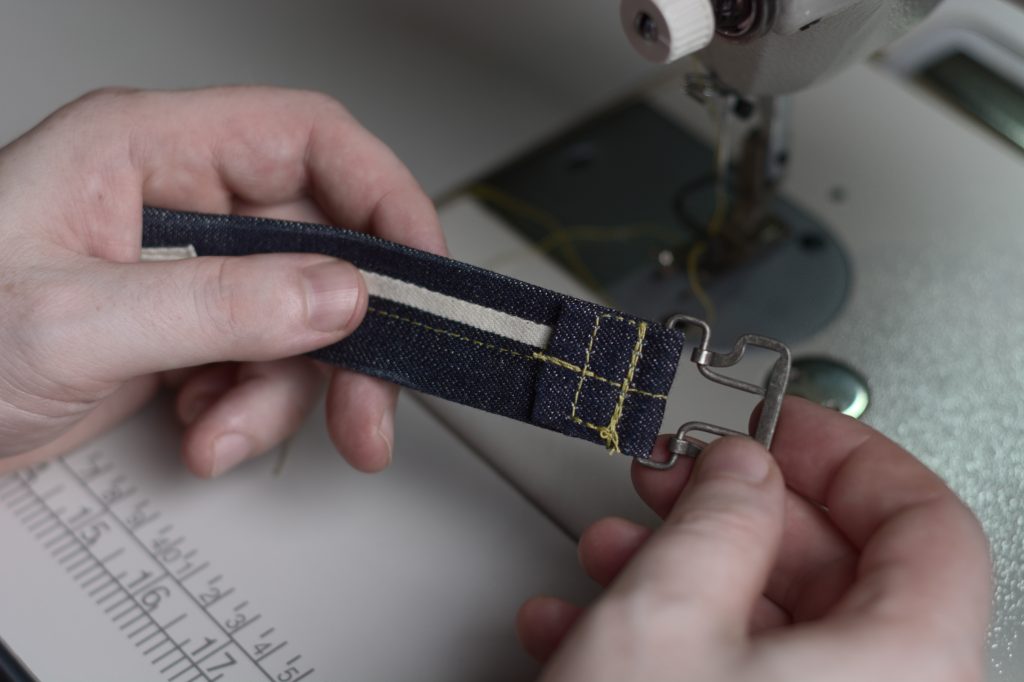
Now with the right cinch belt oriented correctly, secure it in the buckle with about an inch extending past it.
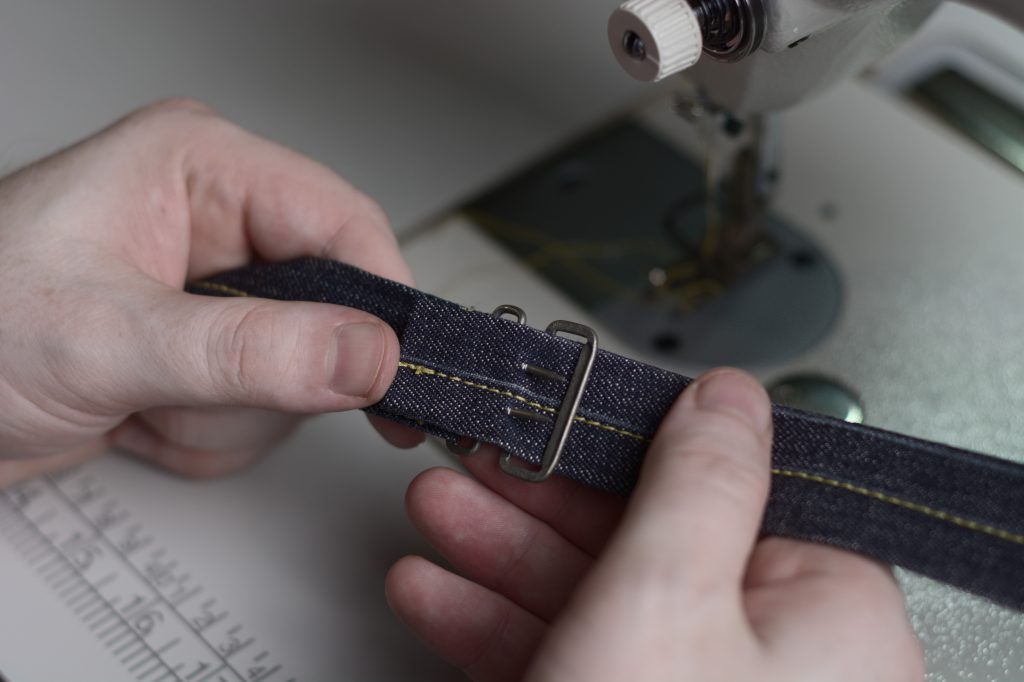
Place the entire back cinch assembly and place it on the jeans, centering it vertically on the waistband seam, and horizontally centering it as well. Take measurements from the center back to each end to ensure they’re the same. When you’re happy with the look, mark the end positions in chalk on the waistband.
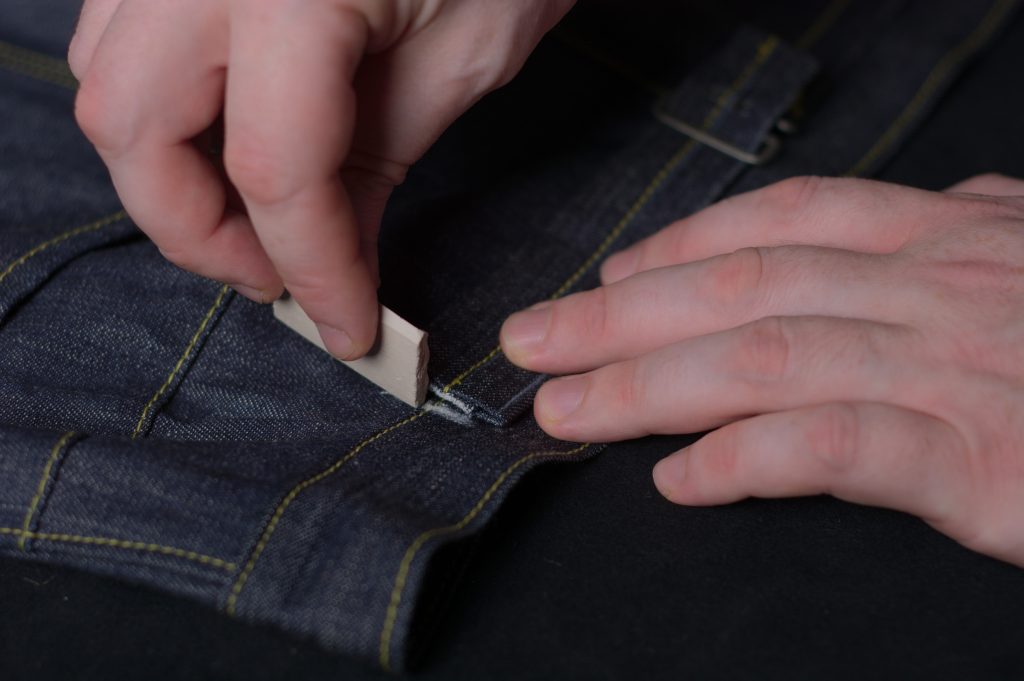
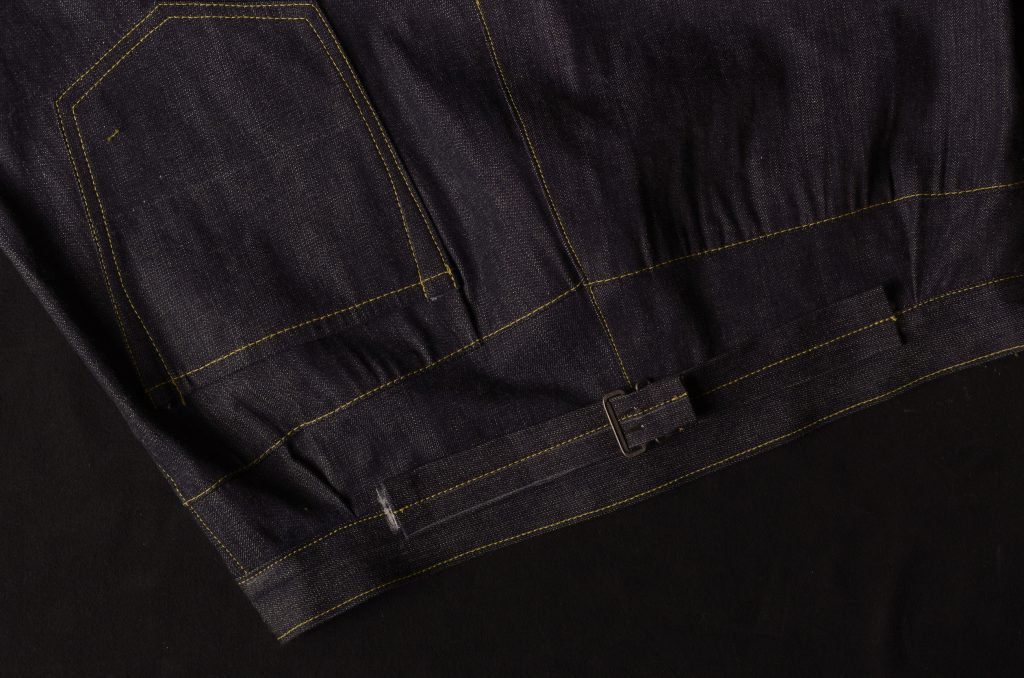
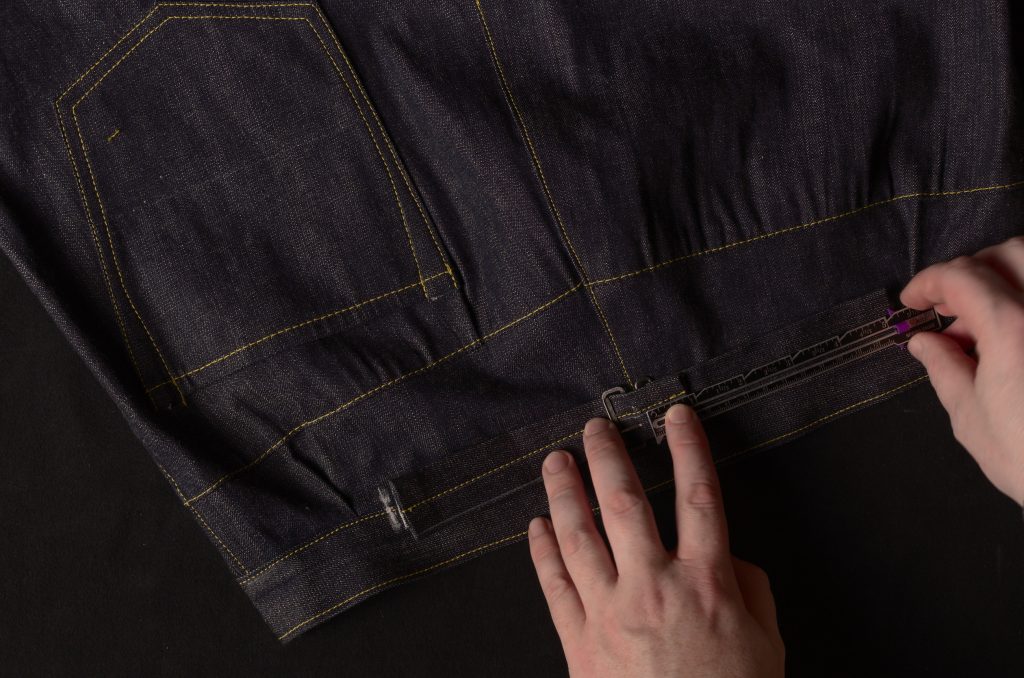
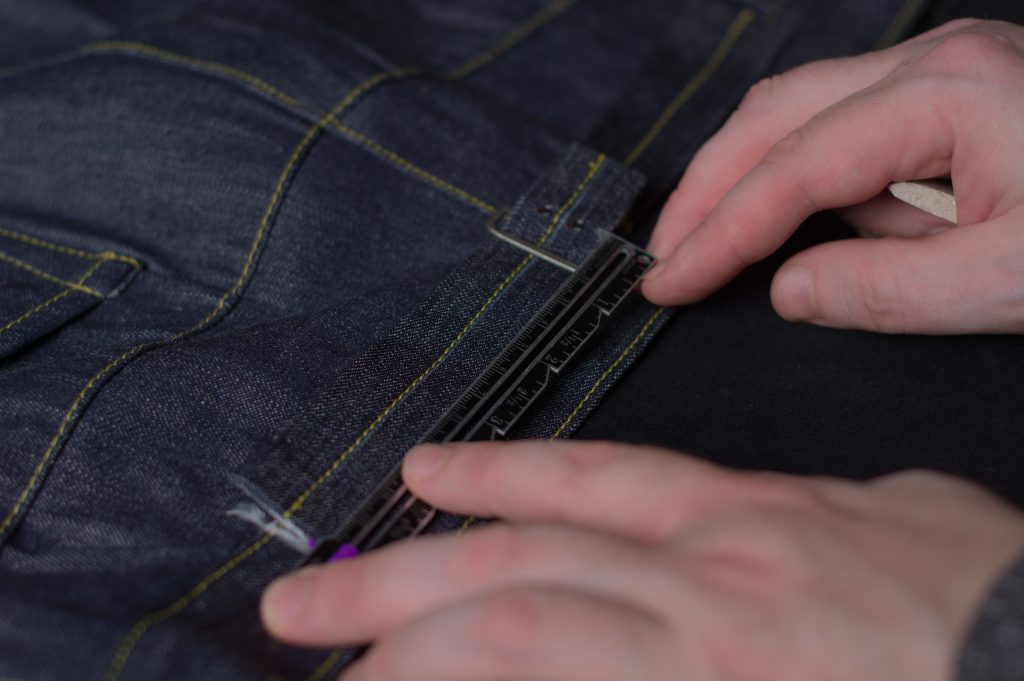
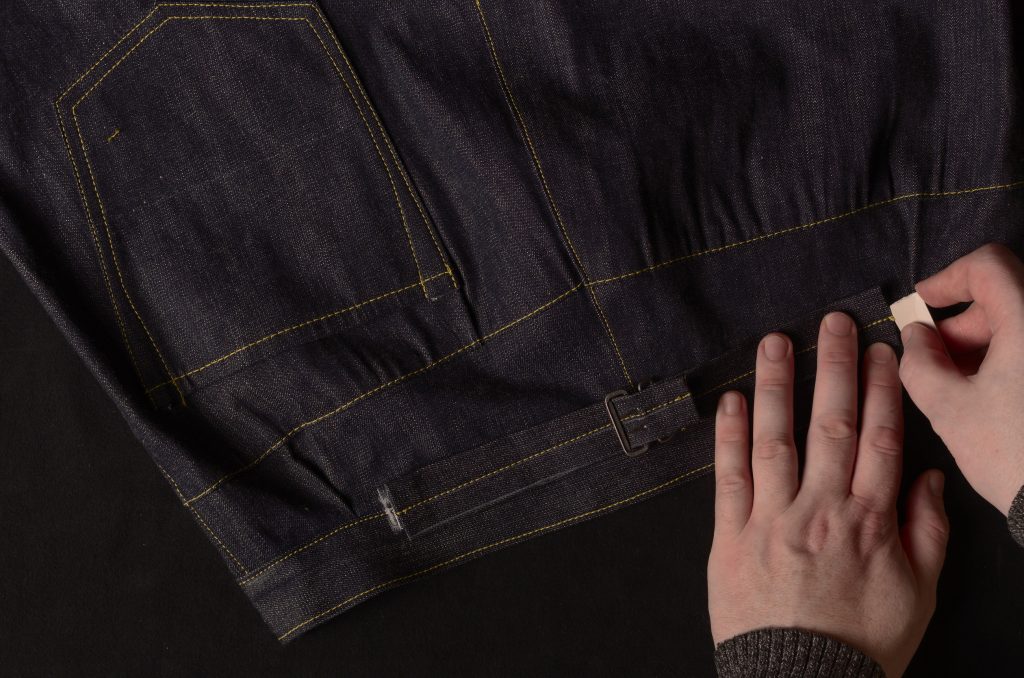
On the back cinch itself, make vertical lines 1″ from each end.
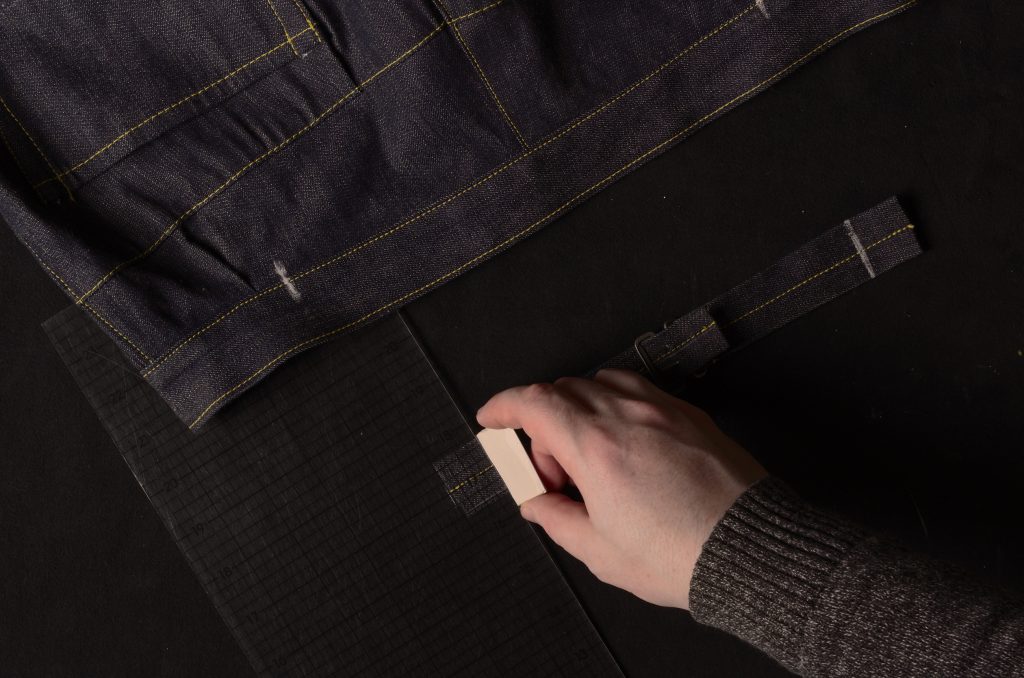
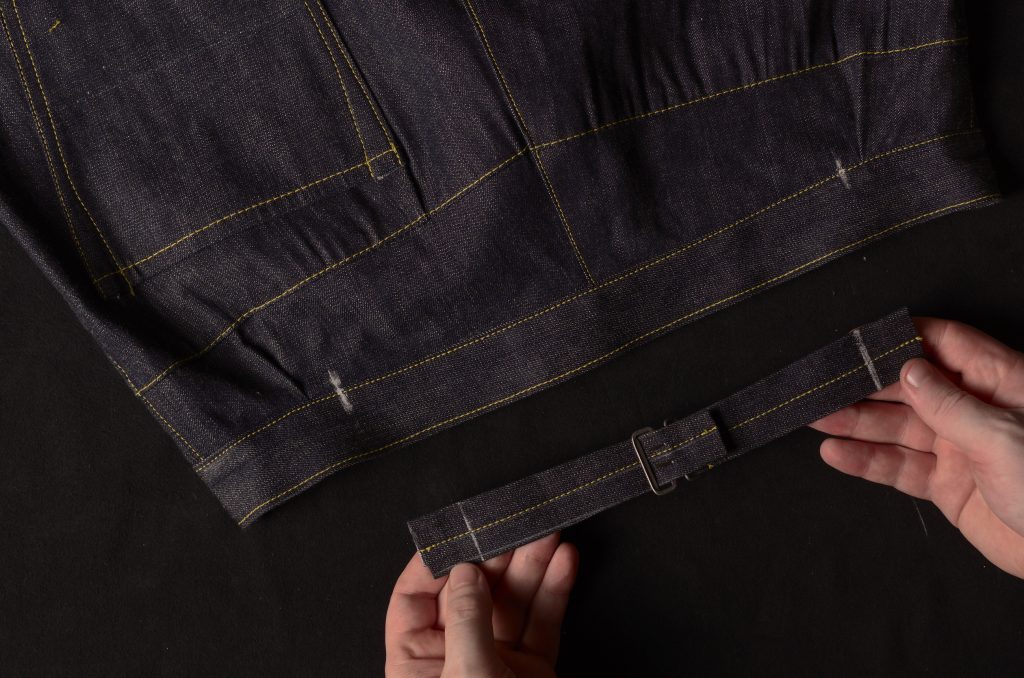
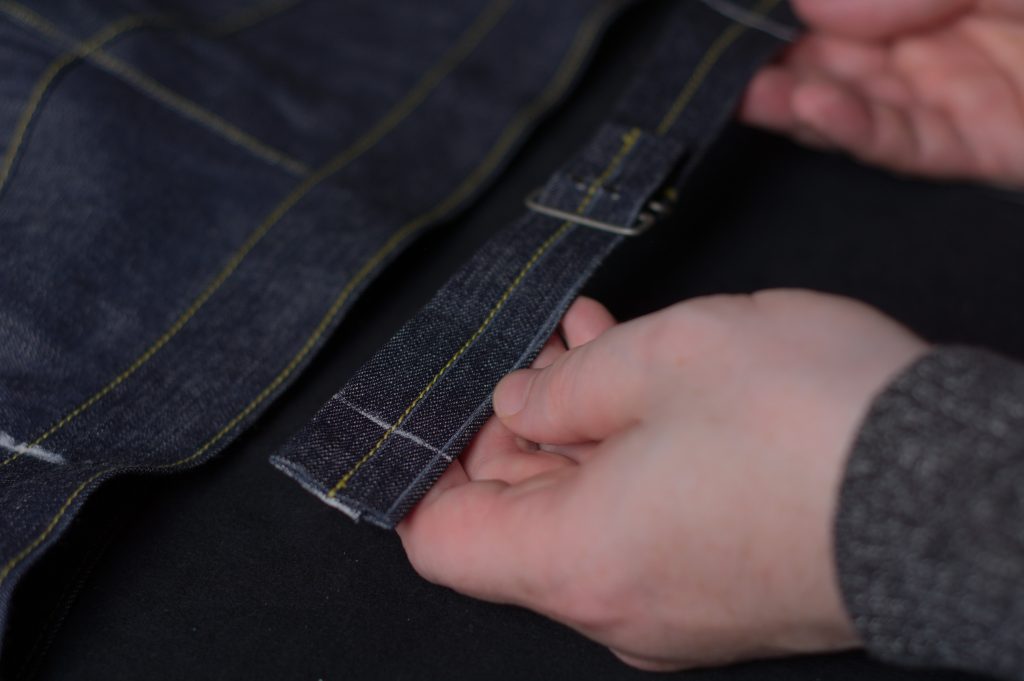
Moving everything over to the sewing machine, make sure your back cinch belts are aligned still, and then sew box stays at each end, about 1/8″ from the edge of the belts, and across the lines you just made.
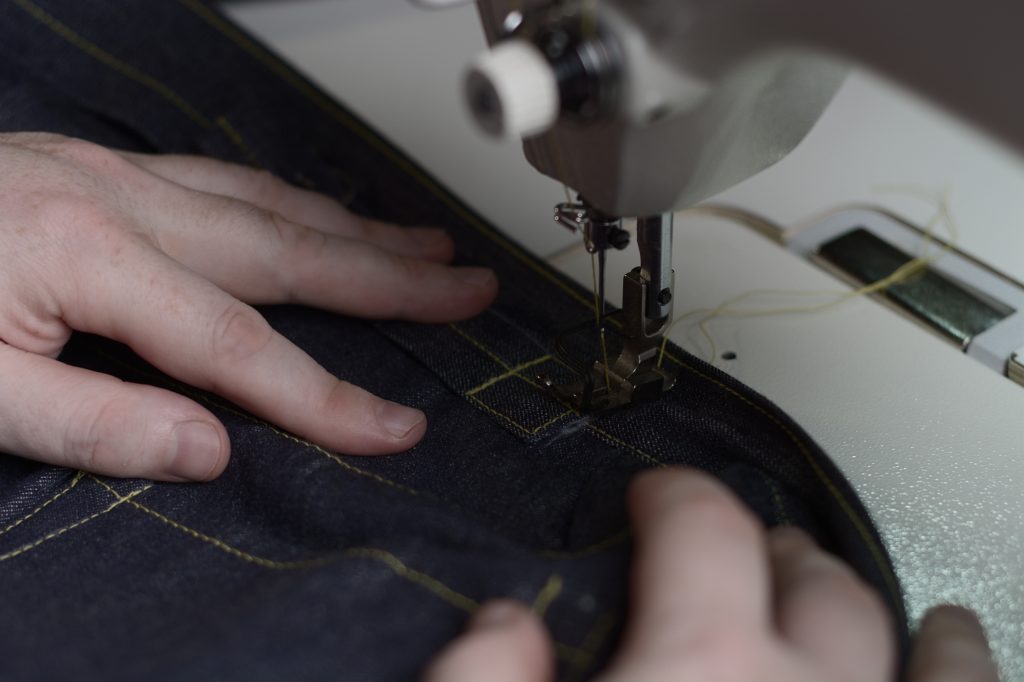
And that completes the back cinch belts, as well as the sewing portion of the jeans construction.
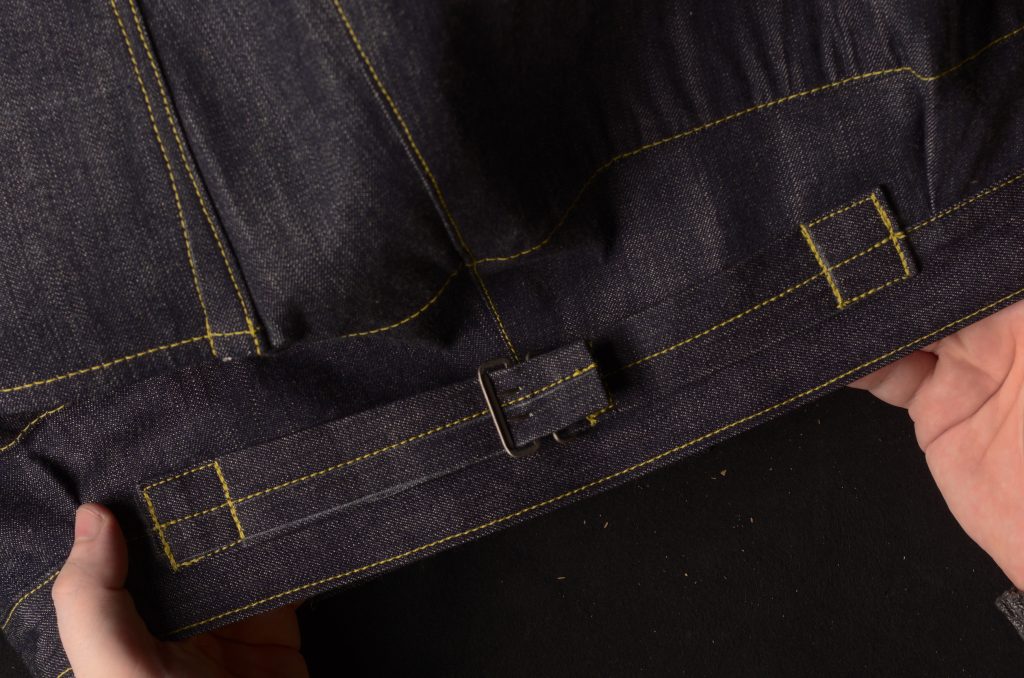
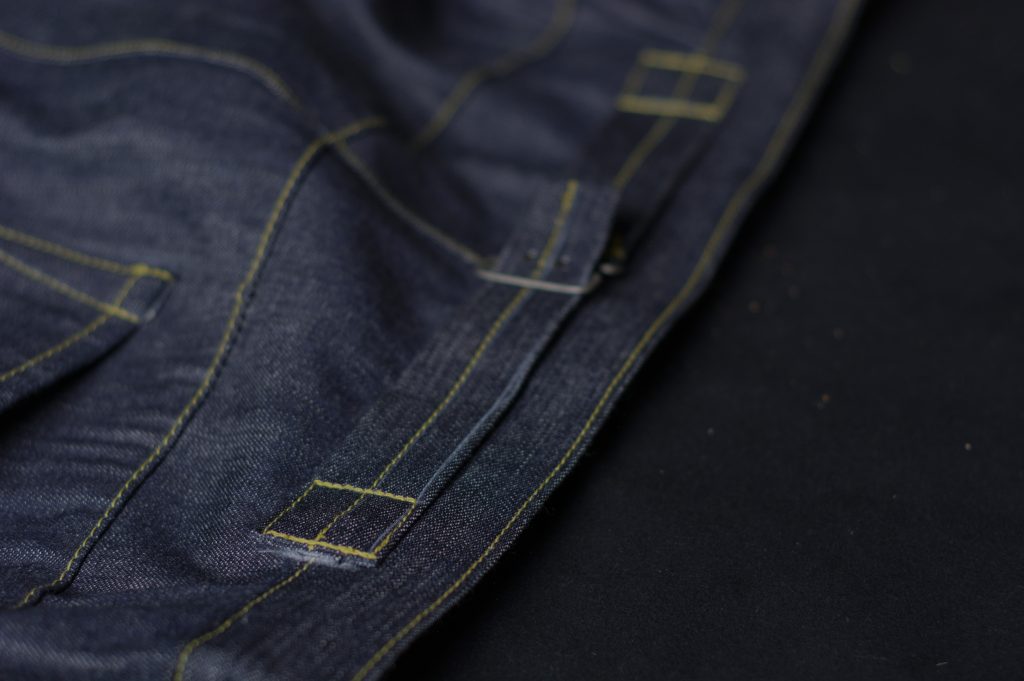
Drafting the Back Cinch Belt
Drafting the back cinch, used on the 1873 model and other more recent models, is pretty simple, with a slightly complex method of adding the seam allowances.
First, draw a horizontal line from 0 to 5″. Five inches is a good length for the back cinch, though for larger sizes you may wish to make this a little longer (or use the graduated rulers to determine the length.
Then mark lines square at each end. From 0 measure 5/8″ up and down, and from 5 measure 1/2″ in either direction. The 1/2″ end is pretty standard, giving you a final 1″ width that fits most buckles, but you can play around with the widths at 0 if you wish.
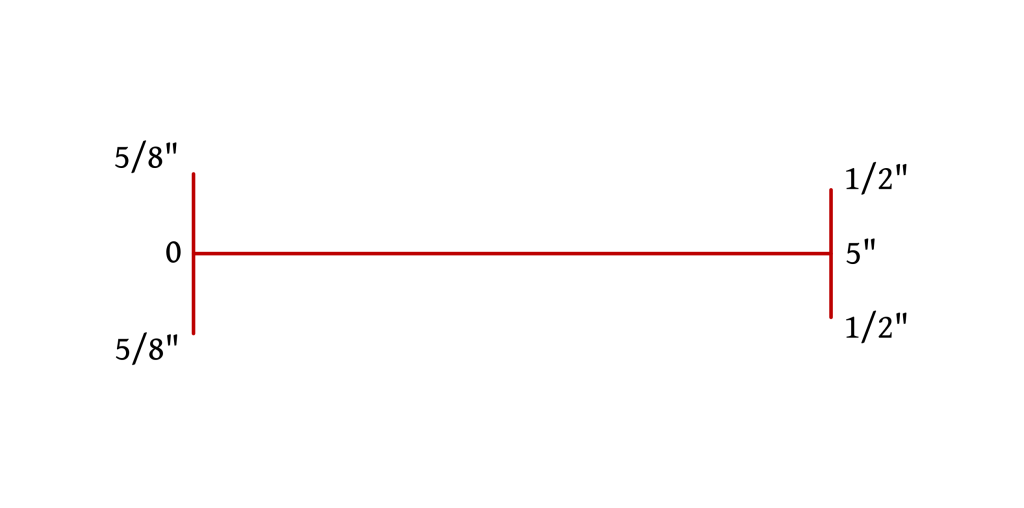
Draw in the outlines as shown. So far you’ve got the entire finished size of the back cinch.
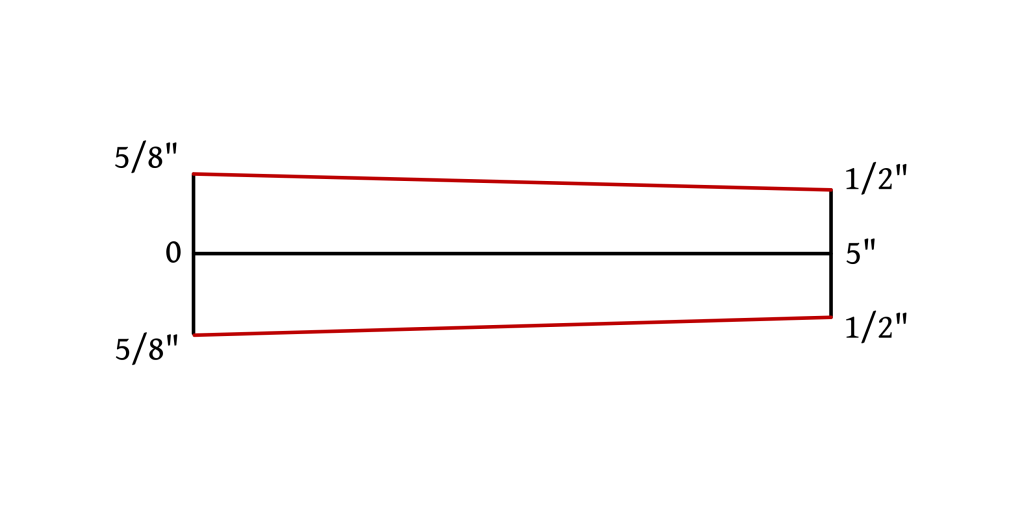
We want the selvedge edge to fall just below the horizontal center line, so that makes for some interesting seam allowances.
- Extend the vertical line from 0, 3/4″ on each side.
- Extend the line from 5 a further 5/8″ on each side.
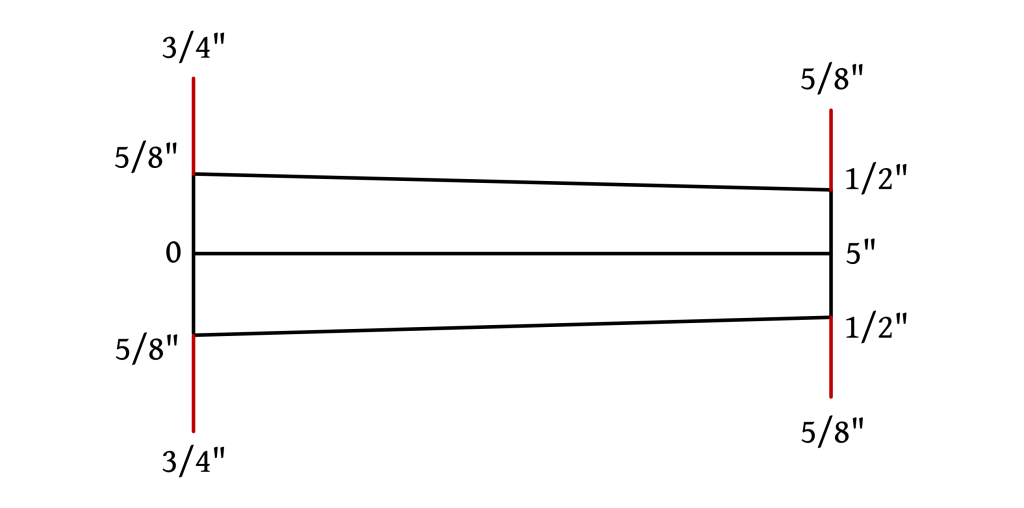
Draw in the top and bottom seam allowances, extending them a bit in both directions.
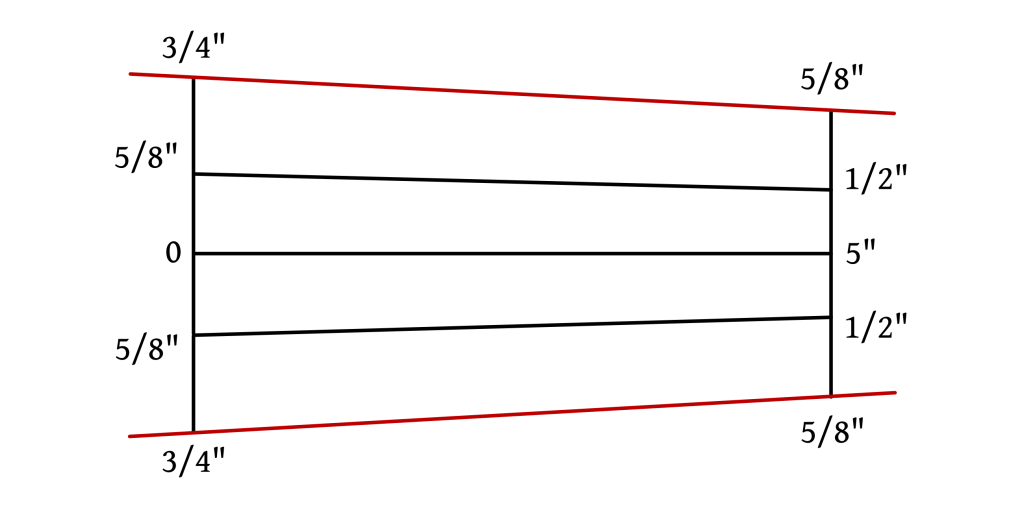
Finally, add a 1/2″ seam allowance on both ends. This completes the draft for the back cinch. You’ll want to cut one of the long edges on the selvedge.
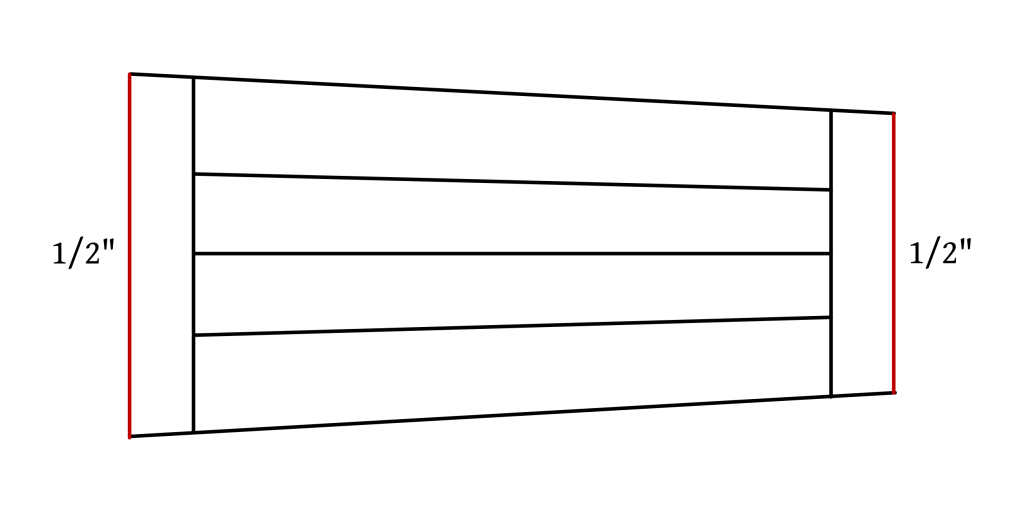
Leather Washers
I like to add some leather washers to the inside of my rivets and buttons to take some of the stress off of the denim and prolong the life of the garment. These are definitely optional, and while not found on the original 1873 jeans, I decided to add them for the benefits given above.
You’ll need some fairly lightweight leather, maybe 2 to 4 ounces in weight, an awl, a 1/8″ hole punch, a large 1/2″ leather punch, and a small hammer or mallet.
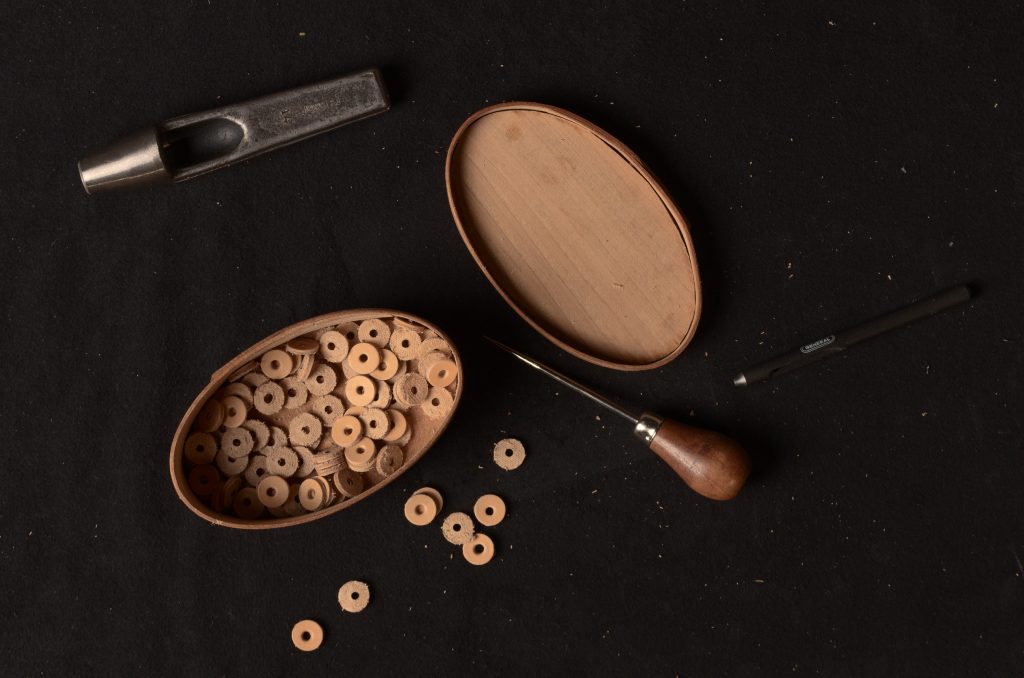
Begin by cutting out the washers using the 1/2″ hole punch.
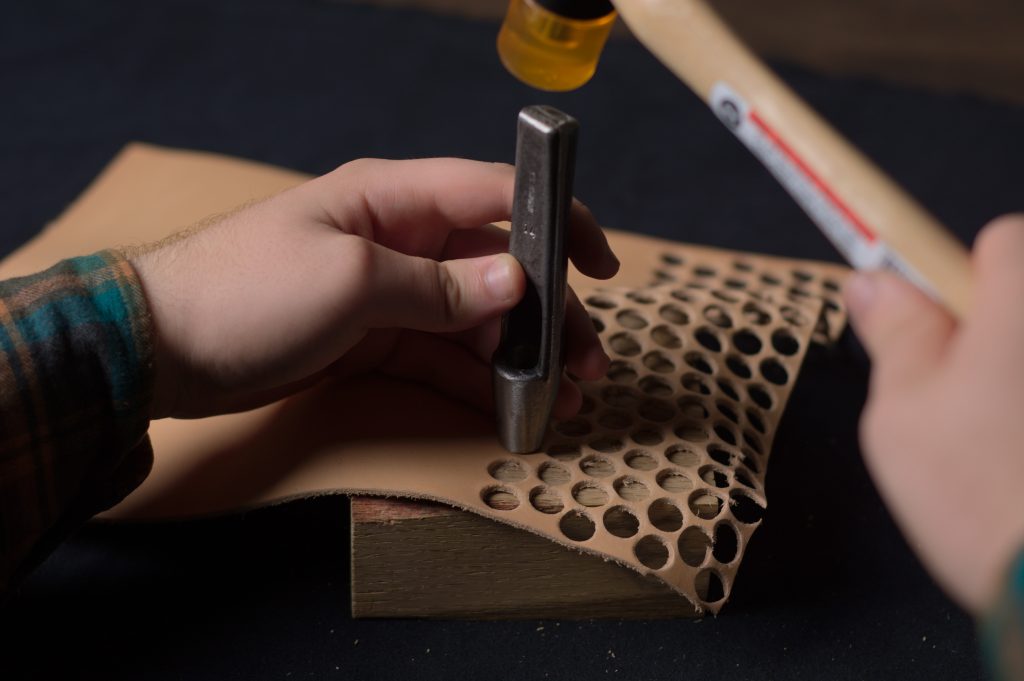
I found finding the exact center with the 1/8″ hole punch to be a little challenging, so I use an awl to find the center instead. It doesn’t have to be perfect but should be as close as possible.
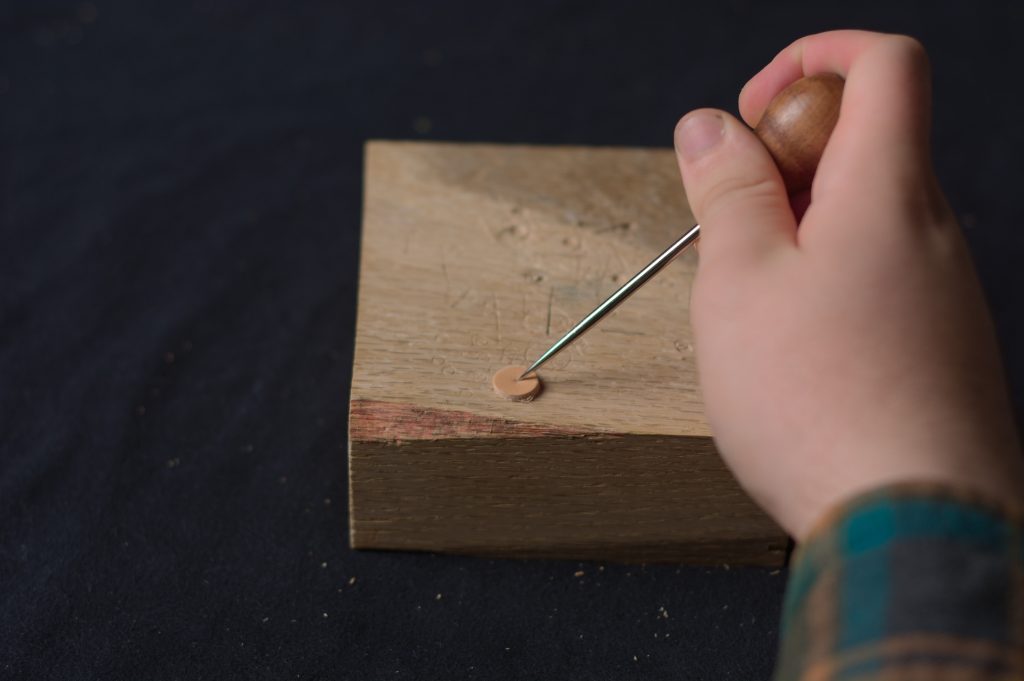
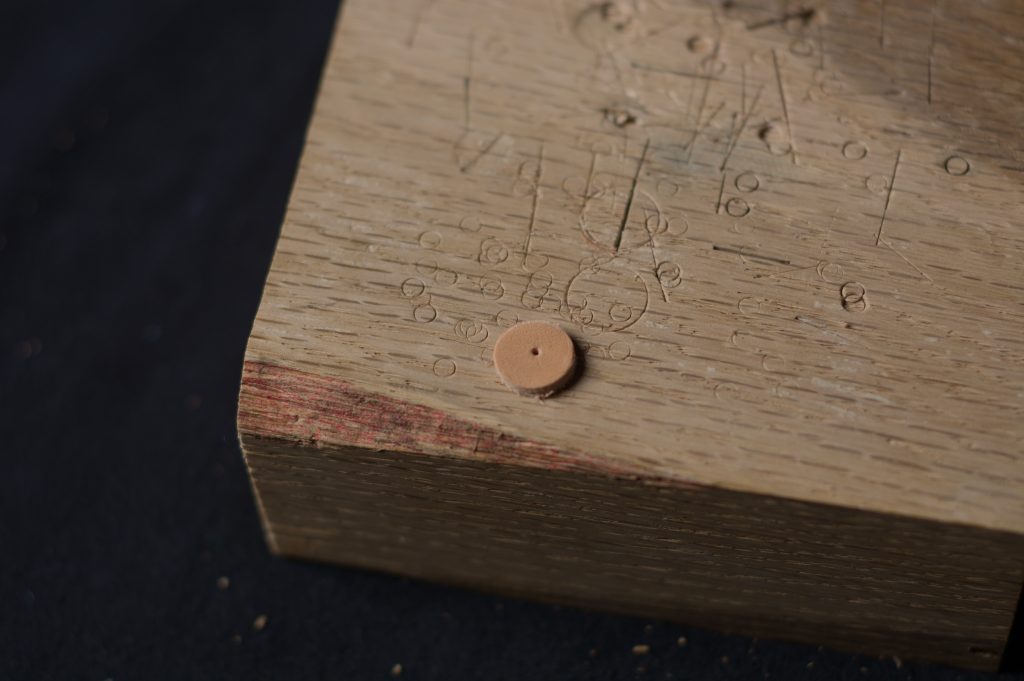
Then center the 1/8″ over the washer, using the hole from the awl as a guide, and chop out the center hole.
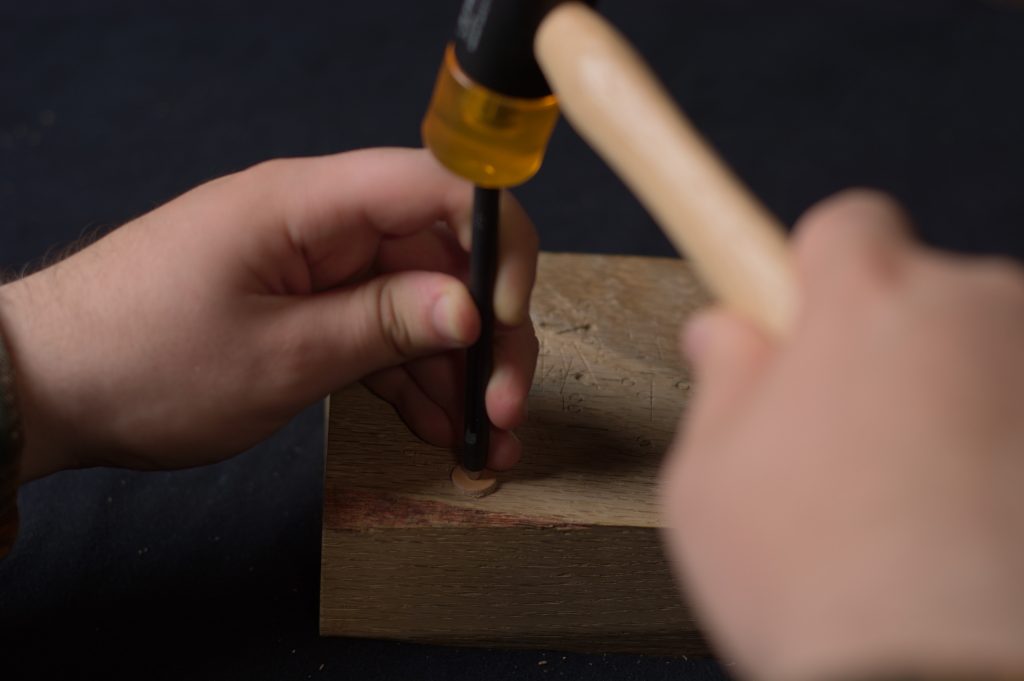
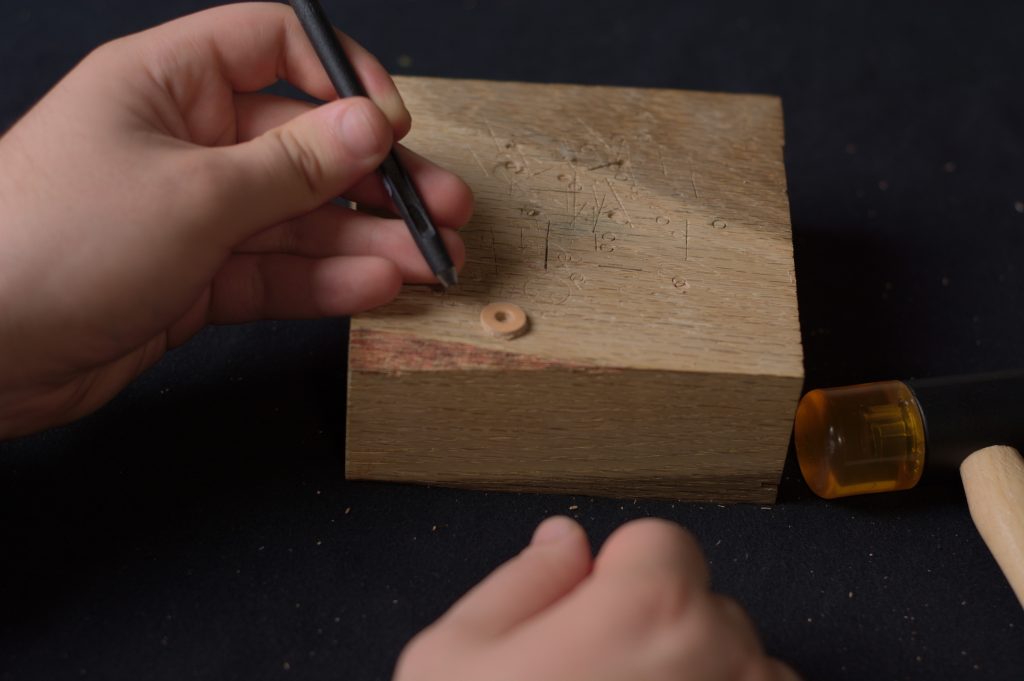
And that’s all there is to it. Cut out as many as you’ll need for all of your rivets and buttons.
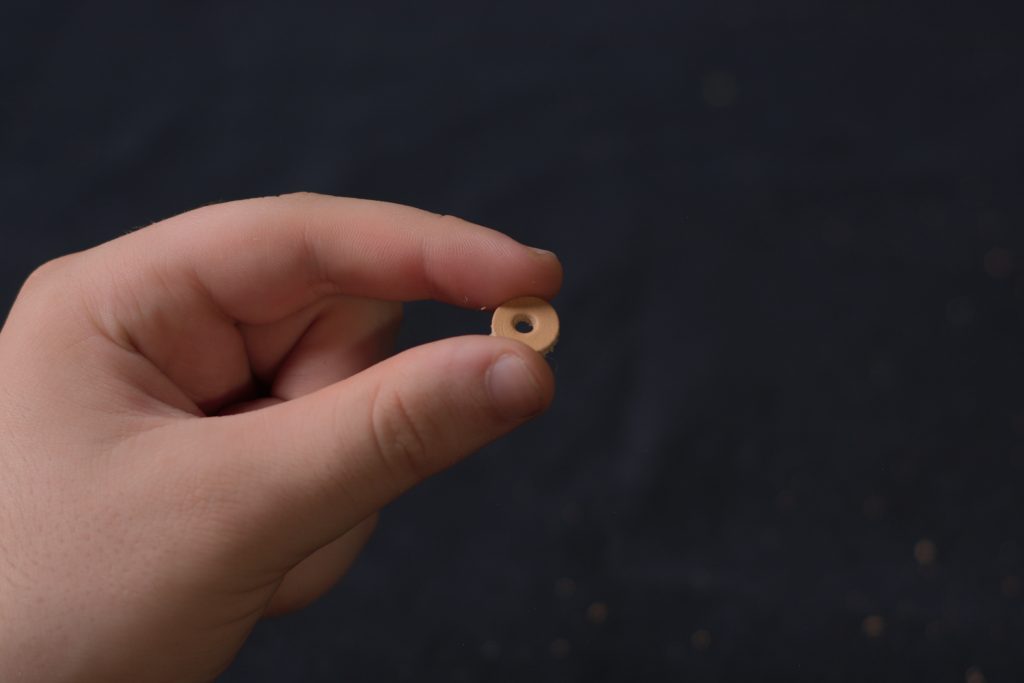
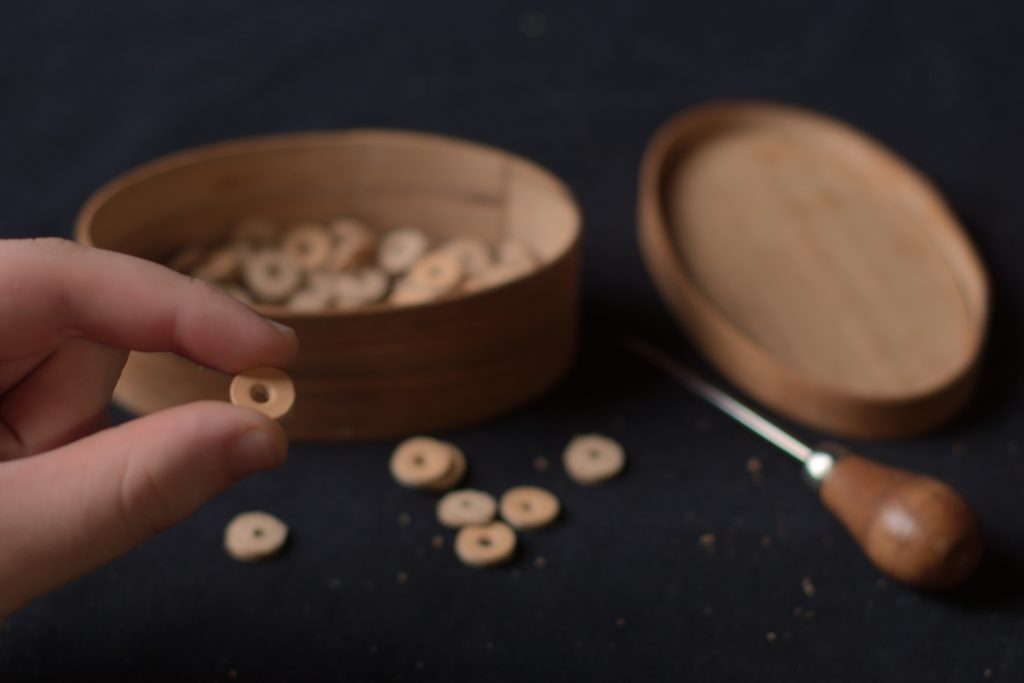
1873 Watch Pocket
These are the instructions for installing the 1873 watch pocket, which while similar to the modern version, extends about halfway up the waistband.
Mark off 1/2″ seam allowances along the sides and bottom edge, and 7/8″ on the top edge of the watch pocket lining.
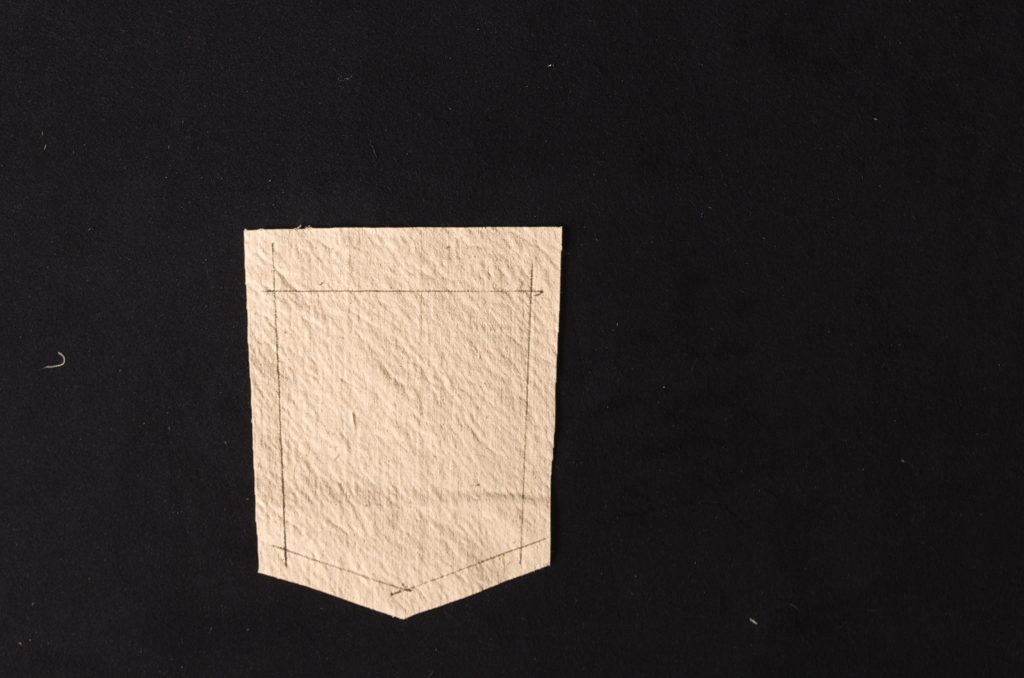
Trim the lining, and then mark out 3/8″ seam allowances on the bottom and sides of the watch pocket, and again 7/8″ along the top edge.
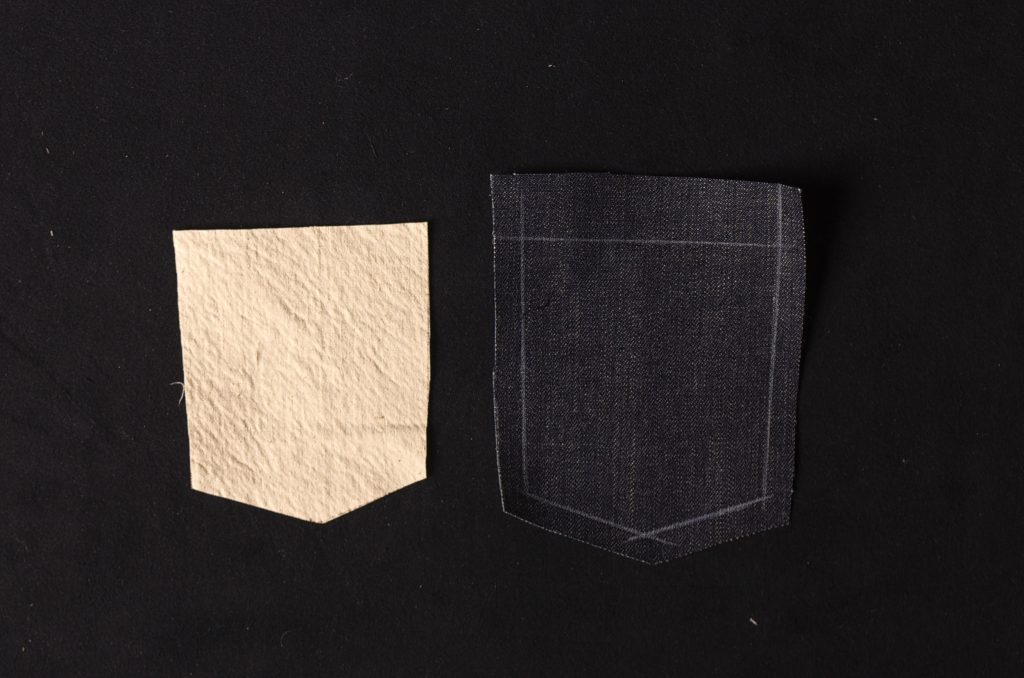
Press the top seam allowance towards the wrong side along the line, and then tuck the raw edge under and press firmly.
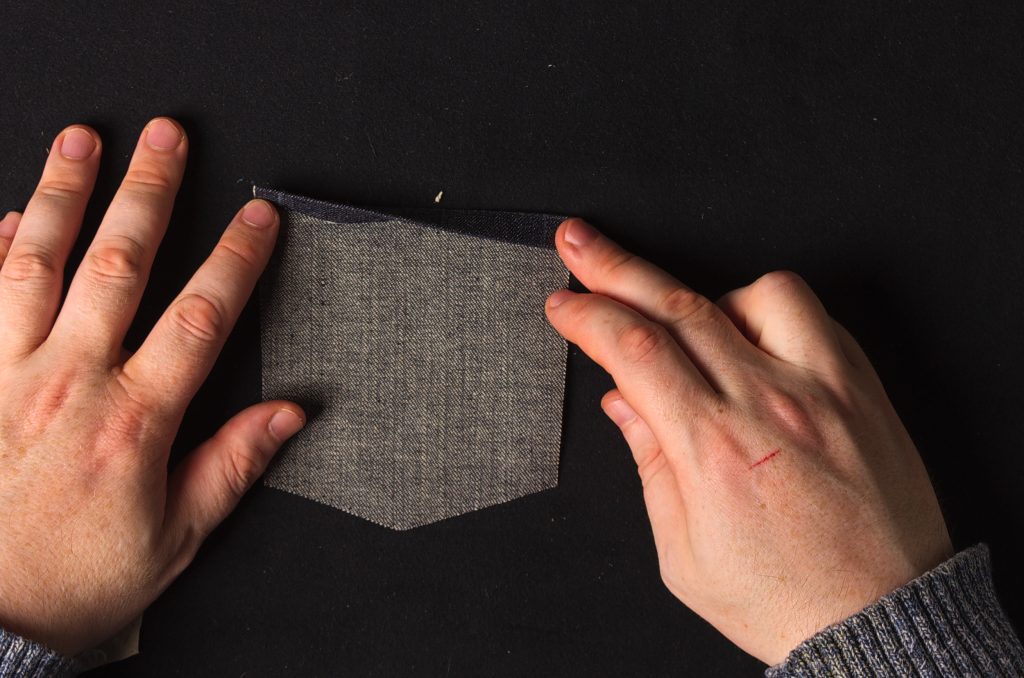
Place the watch pocket lining into position. you may need to trim the lining a little further to get a good fit.
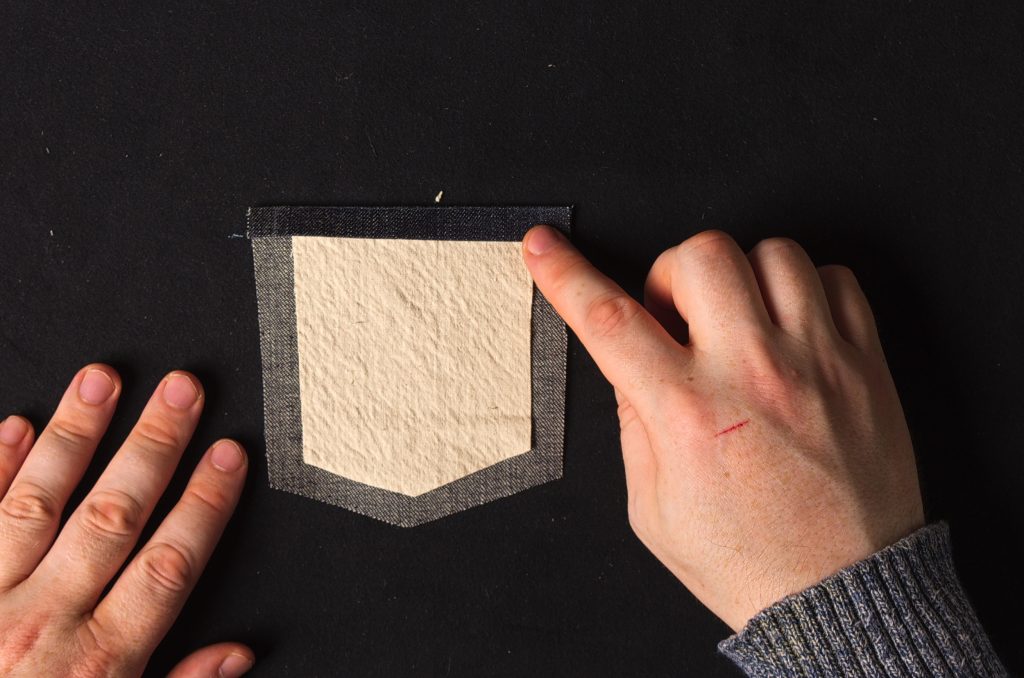
Top stitch a single row of stitching about 3/8″ from the top, catching all layers.
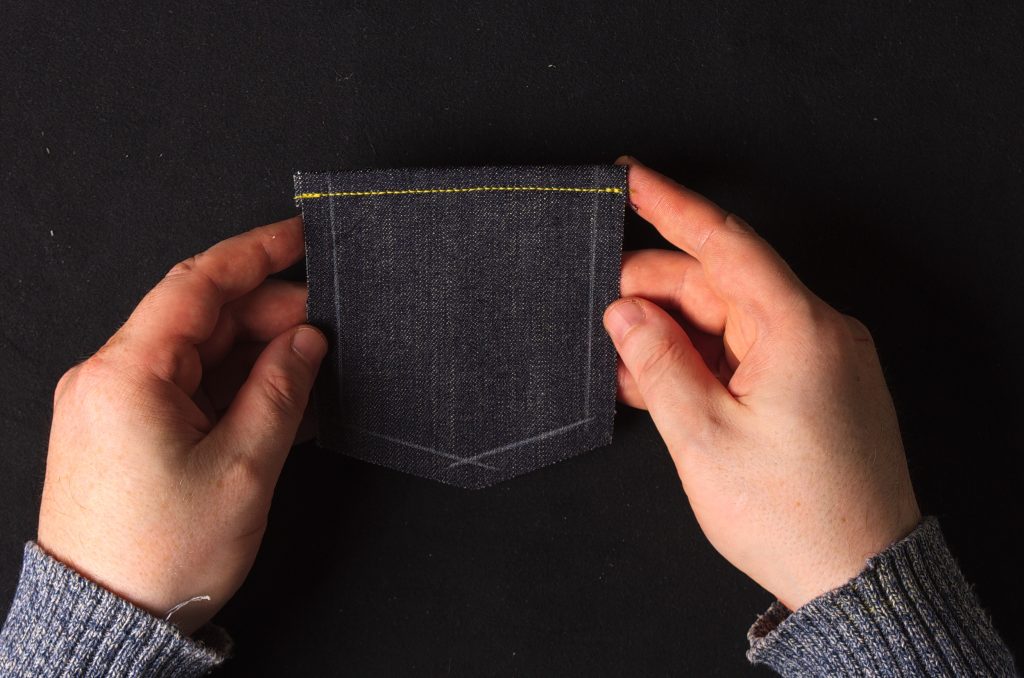
Press the remaining seam allowances to the wrong side along the chalk lines.
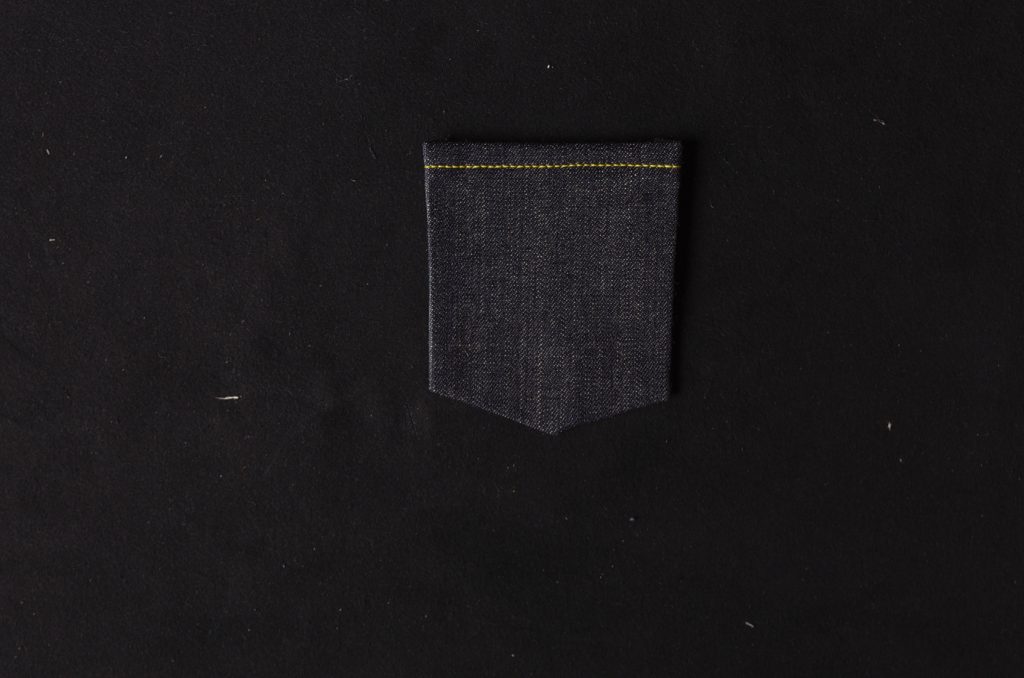
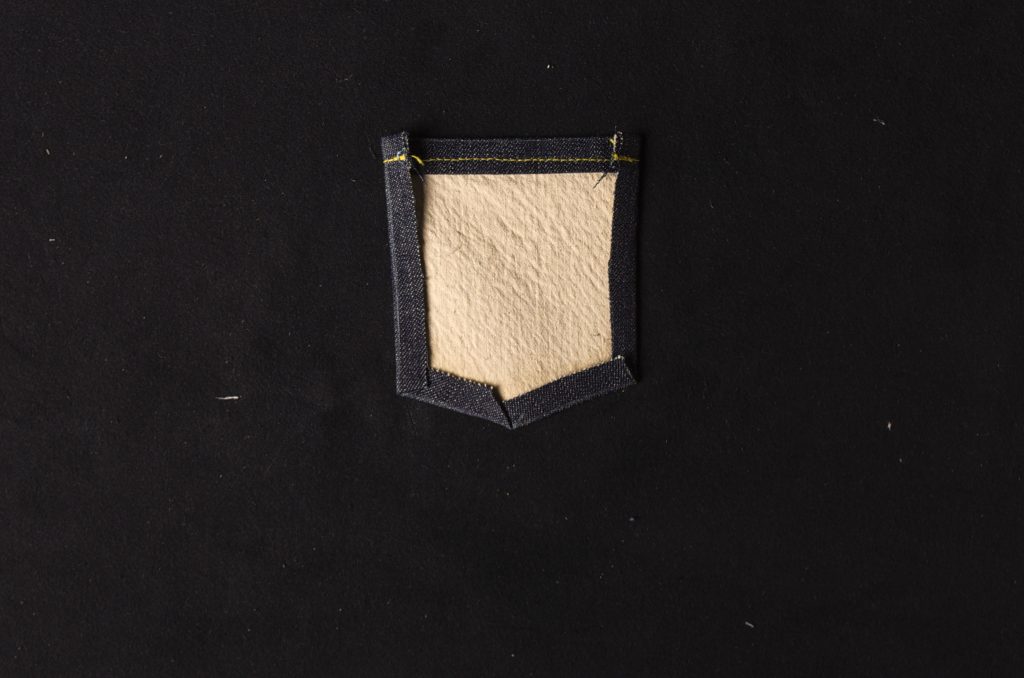
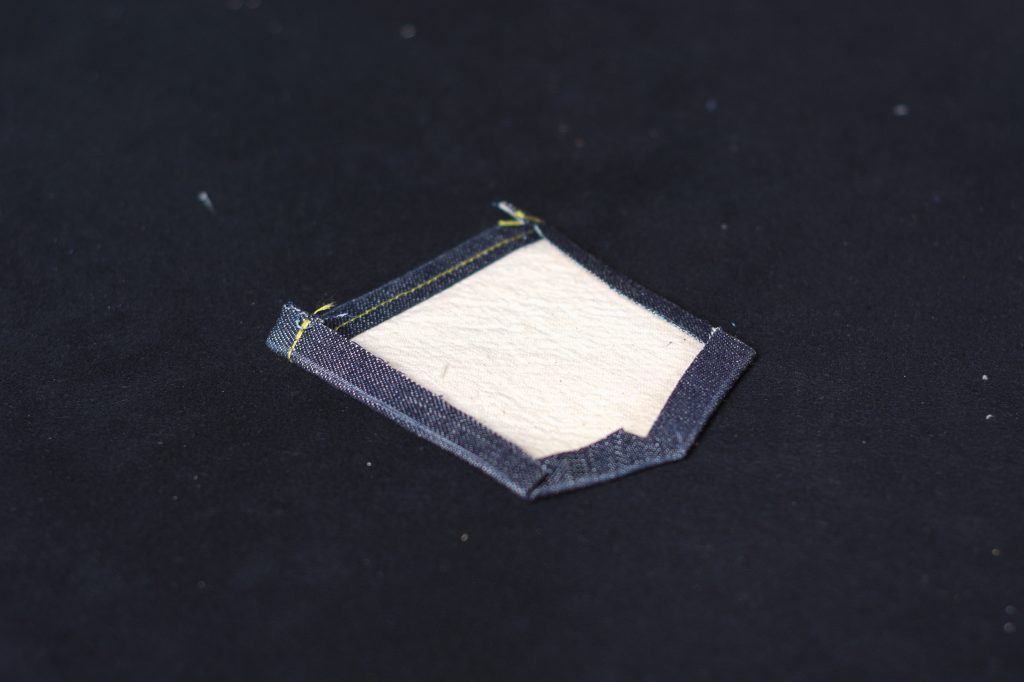
Attaching the Watch Pocket
Place the watch pocket into position on top of the right front pocket. The top of the watch pocket should extend about midway up the waistband, while the bottom edge should be just below the front pocket opening.
You can pin the pocket in place or just hold it while you sew.
Starting from the left side of the pocket (I accidentally start on the right in the video and run into trouble!), top stitch the watch pocket around the sides and bottom edge, about 1/8″ from the edge.
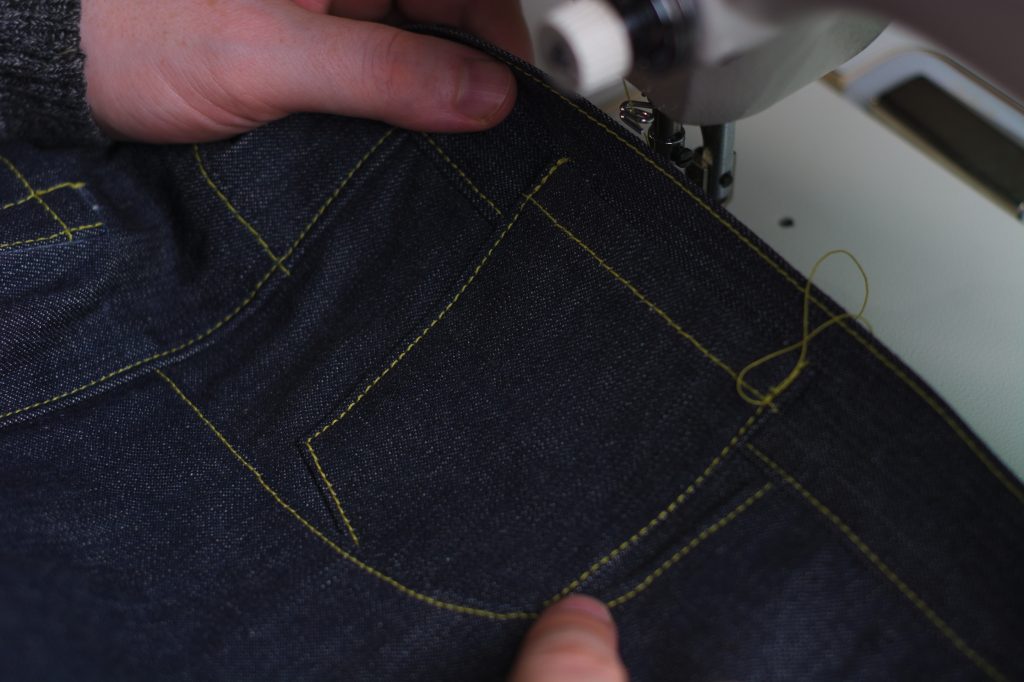
Then make another row of top stitching about 1/4″ from the first, keeping the stitches parallel throughout.
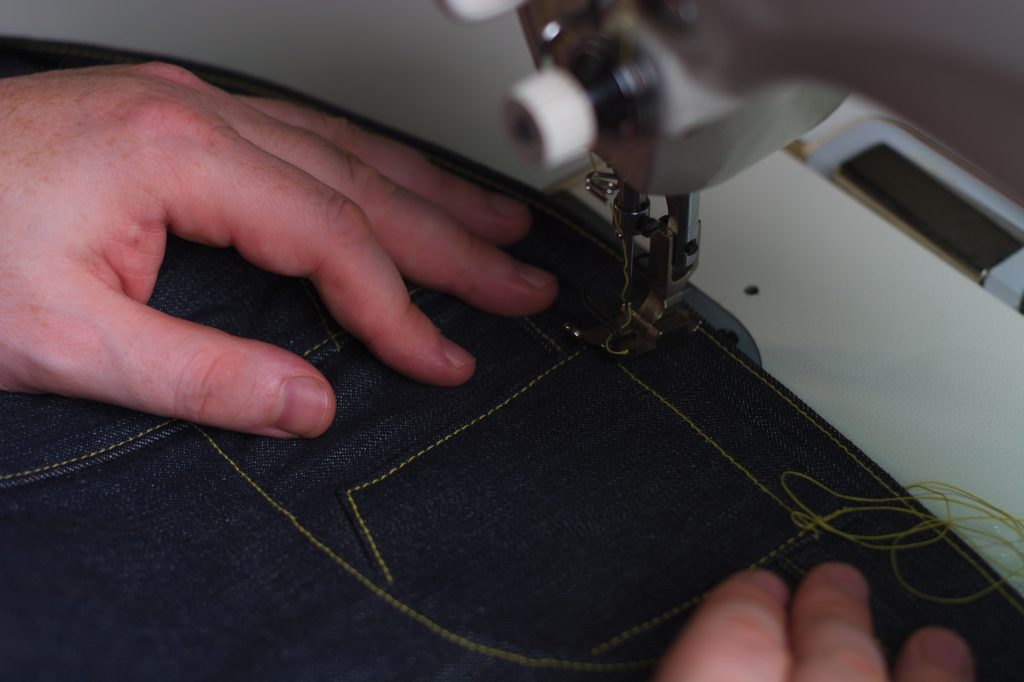
Here’s the waistband area after top stitching the watch pocket in place.
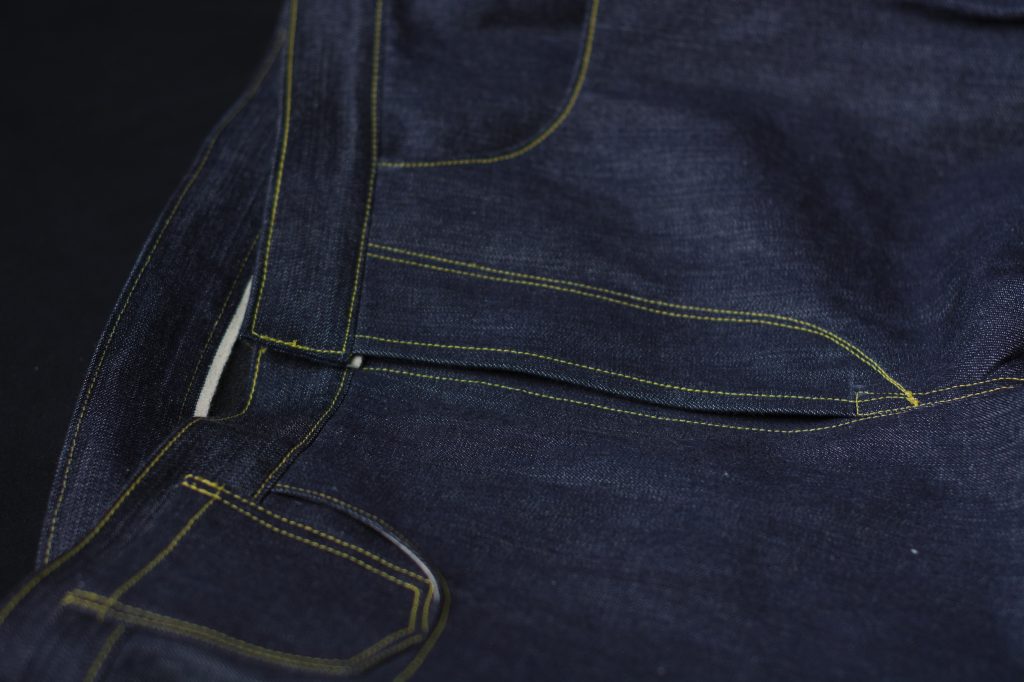
Hemming
Moving on to the hem, mark a series of points 7/8″ from the bottom. This gives us two 3/8″ seam allowances plus 1/8″ to account for the width of the fabric when turning.
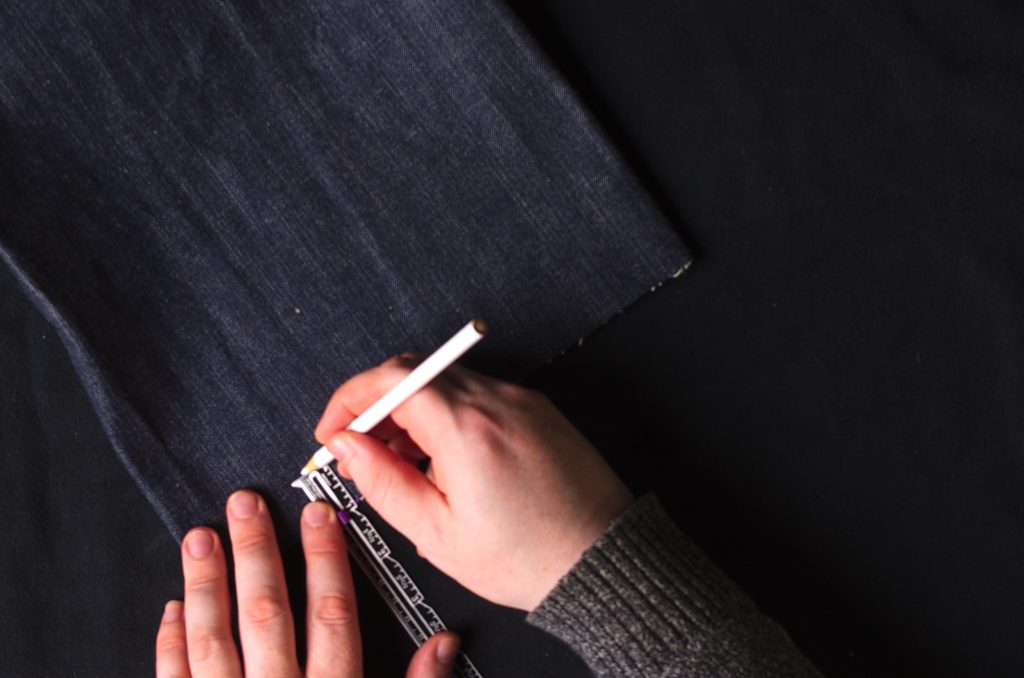
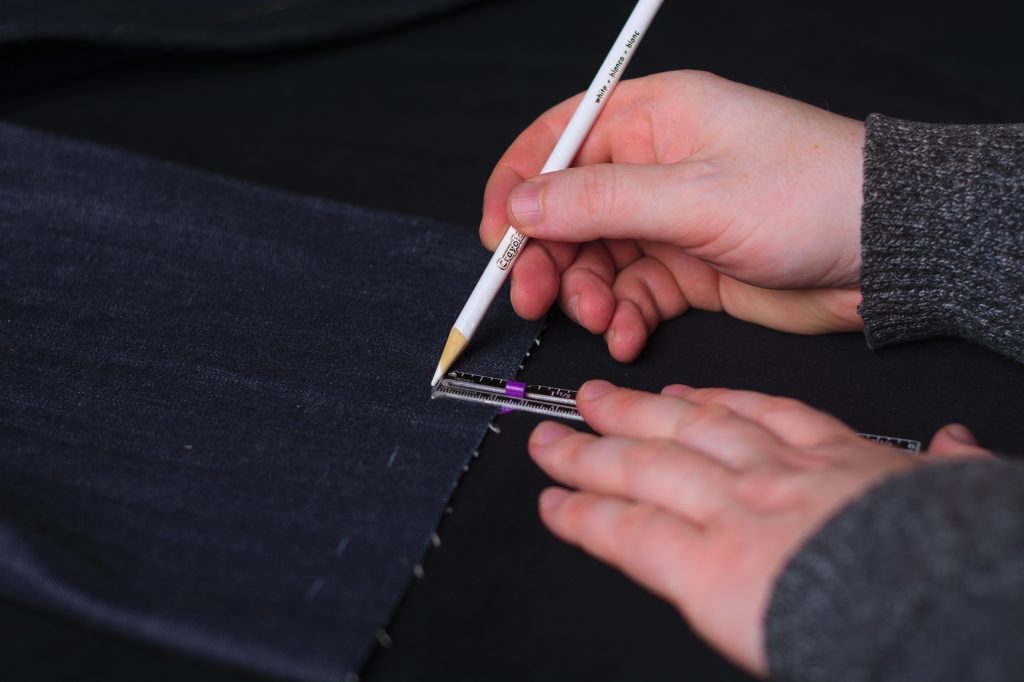
Now turn under the hem towards the wrong side, aligning the fold with the points you just made, and crease with your fingers.
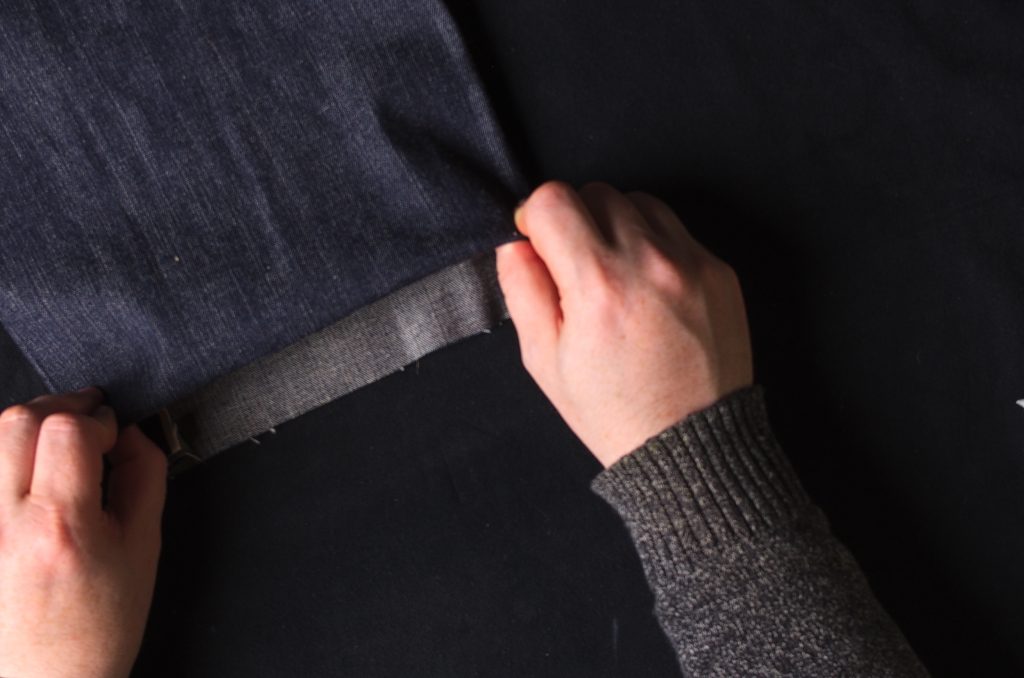
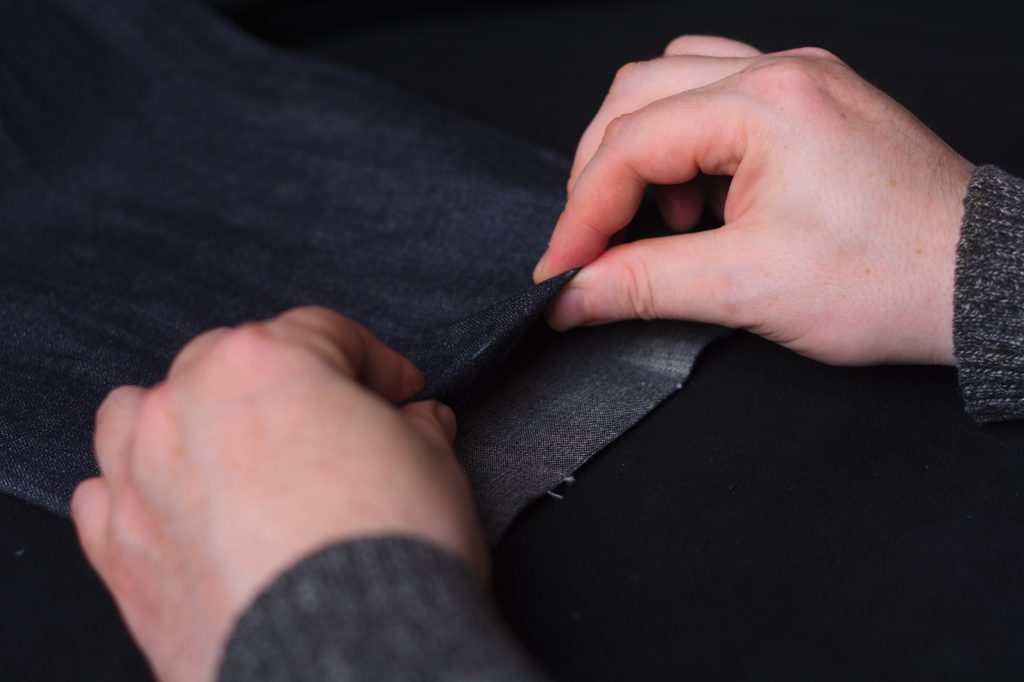
Now iron the hem all the way around the leg, concentrating especially on the seams.
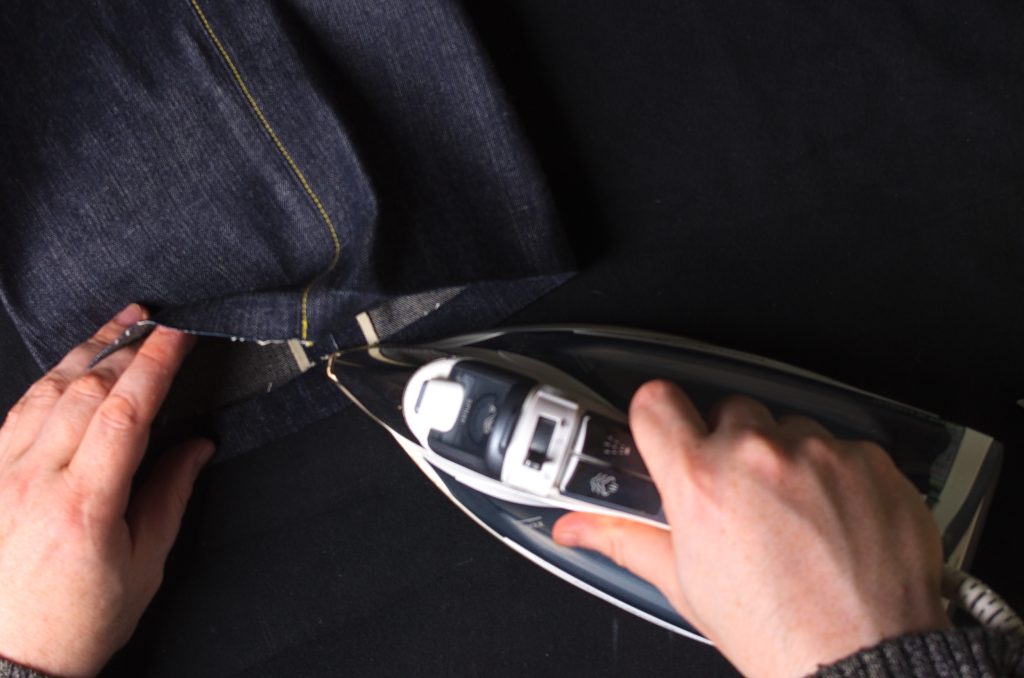
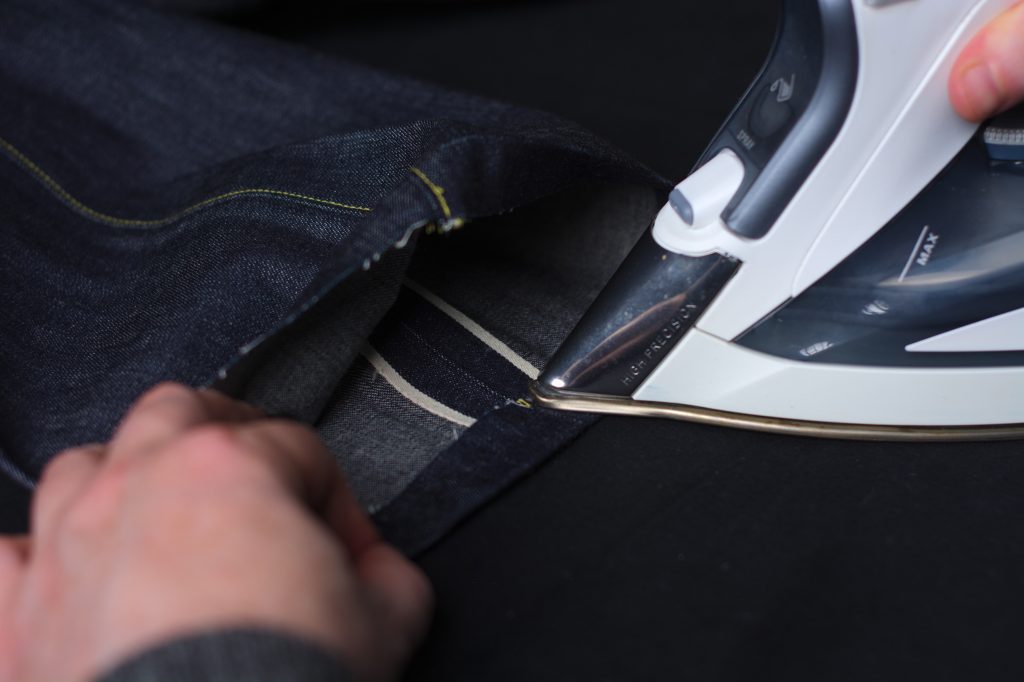
Here’s where my side seam was slightly off when sewing, so I just smoothed out the difference when folding the hem.
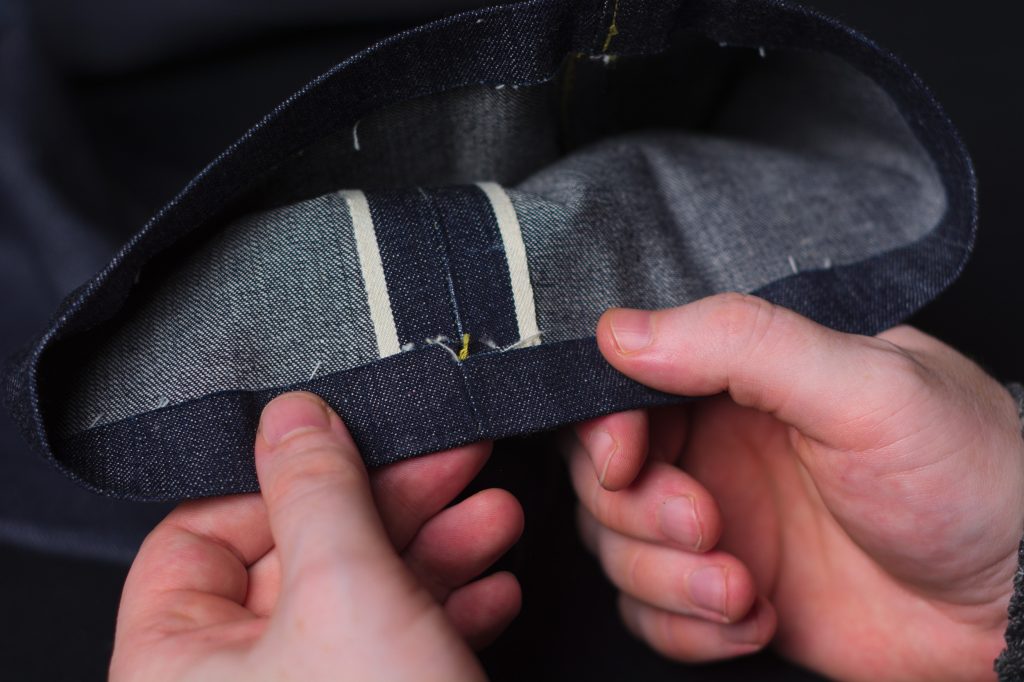
Now fold an inch or two of the raw edge under itself, forming the final hem, and crease with your fingers. Rather than turning and pressing the entire hem again, we’ll just turn a little bit at a time and sew it down as we go.
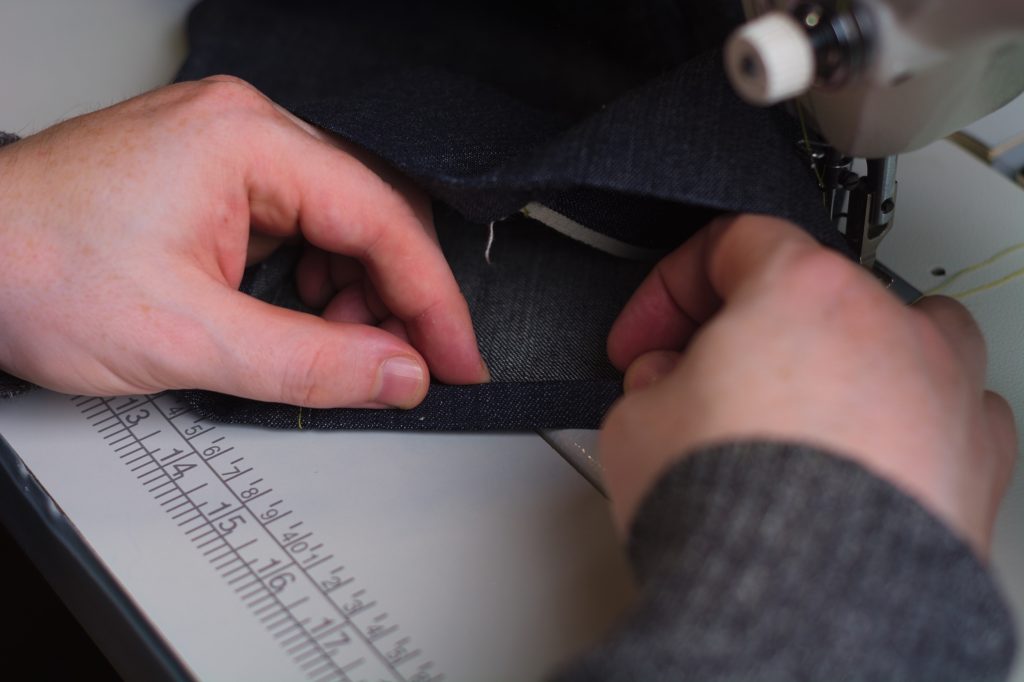
Starting near the inseam, a couple of inches before it, begin sewing down the hem using a 3/8″ seam, sewing from the wrong side.
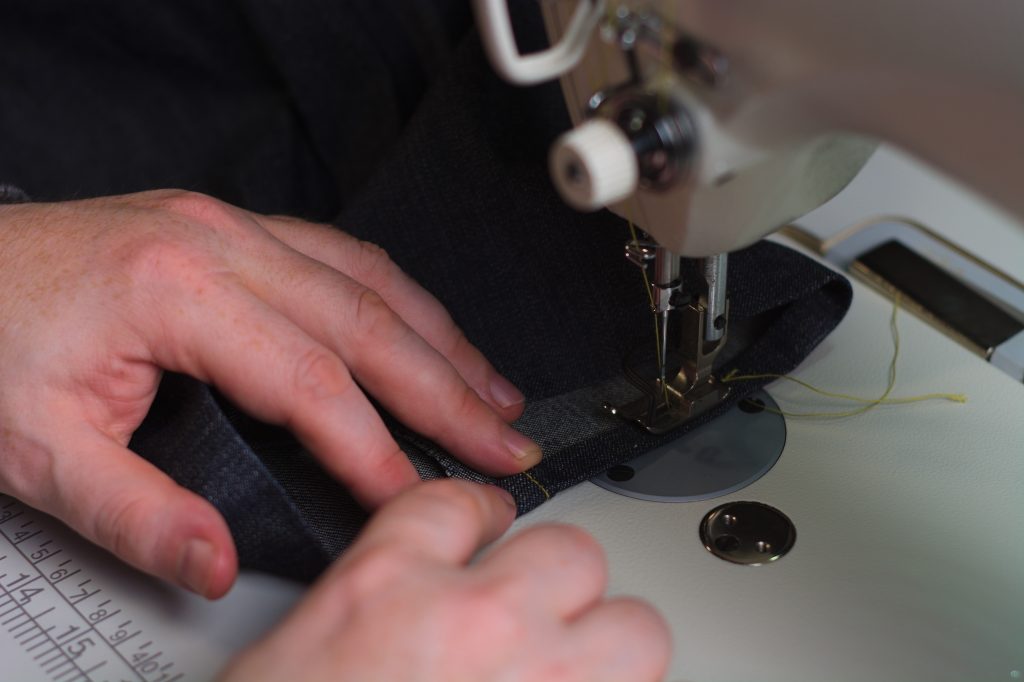
When you get to the inseam, you’ll definitely want to use the seam jumper, especially if you’ve done the felled seam.
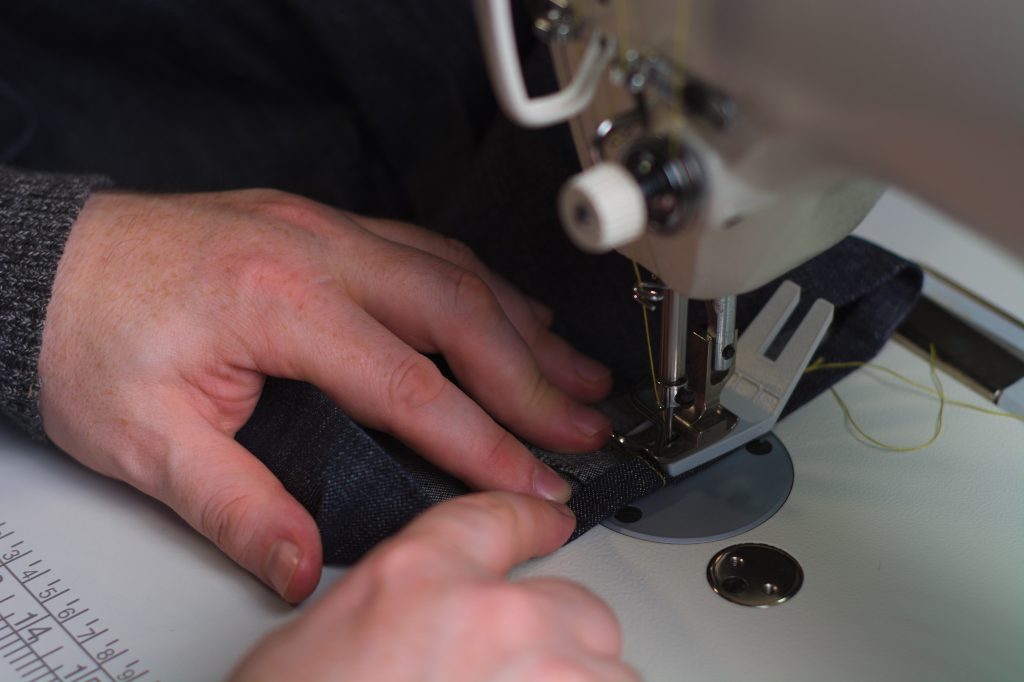
Here’s the result from the outside after sewing completely around the hem.
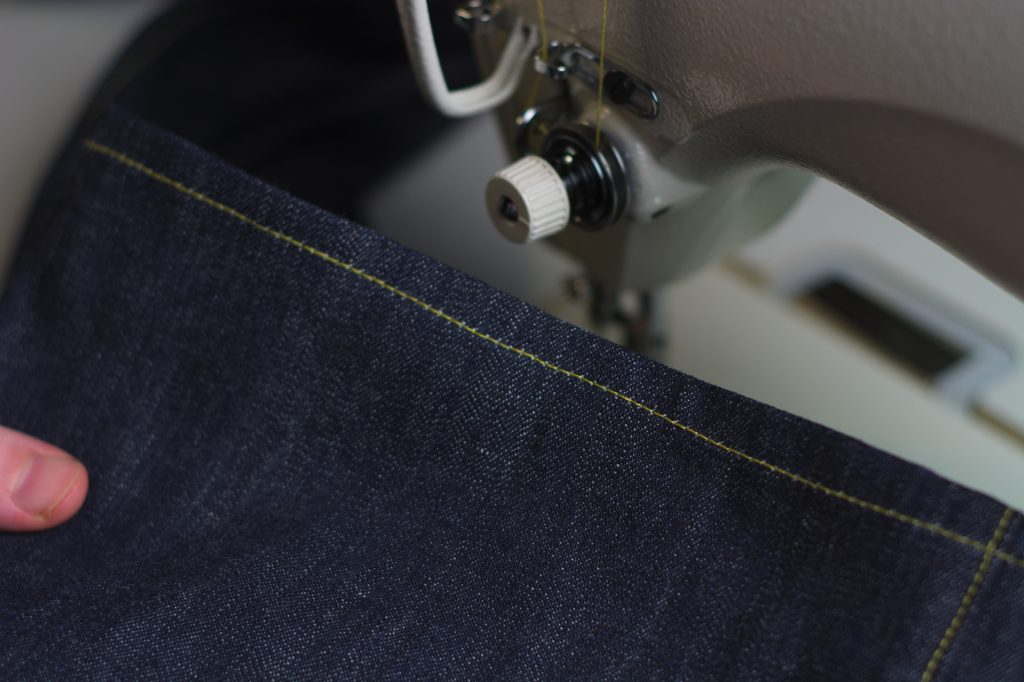
And the inside of the leg.
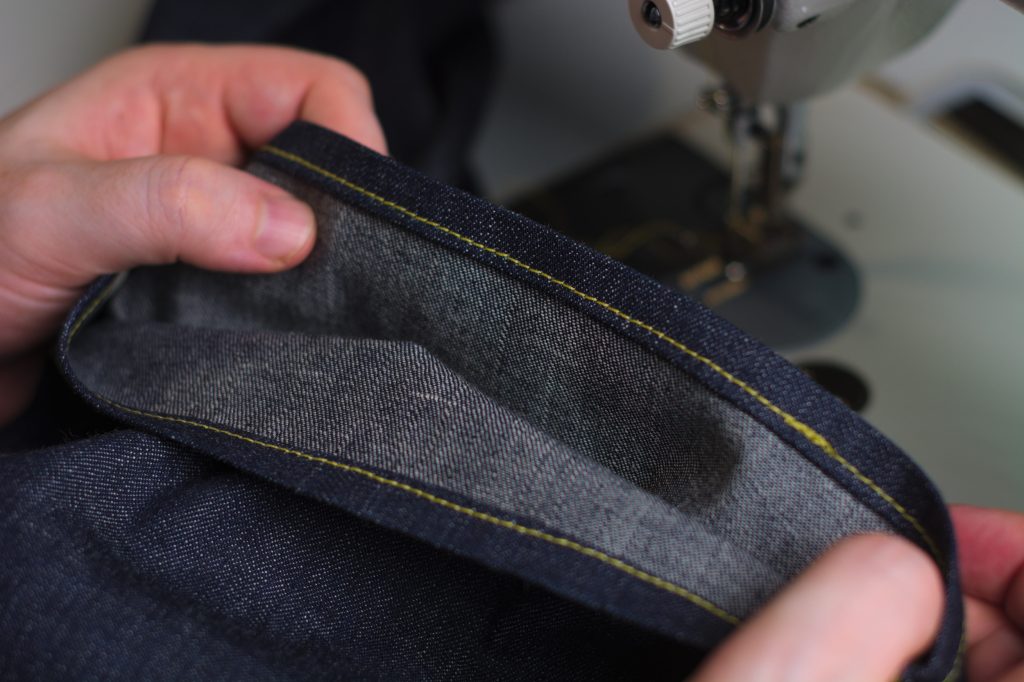
Turning to the outside of the leg, turn up the hem about 1 1/2″. Originally, the jeans were sold unhemmed or hemmed very long, and the amount of turn up would vary appropriately, but 1 1/2″ is a good starting point.
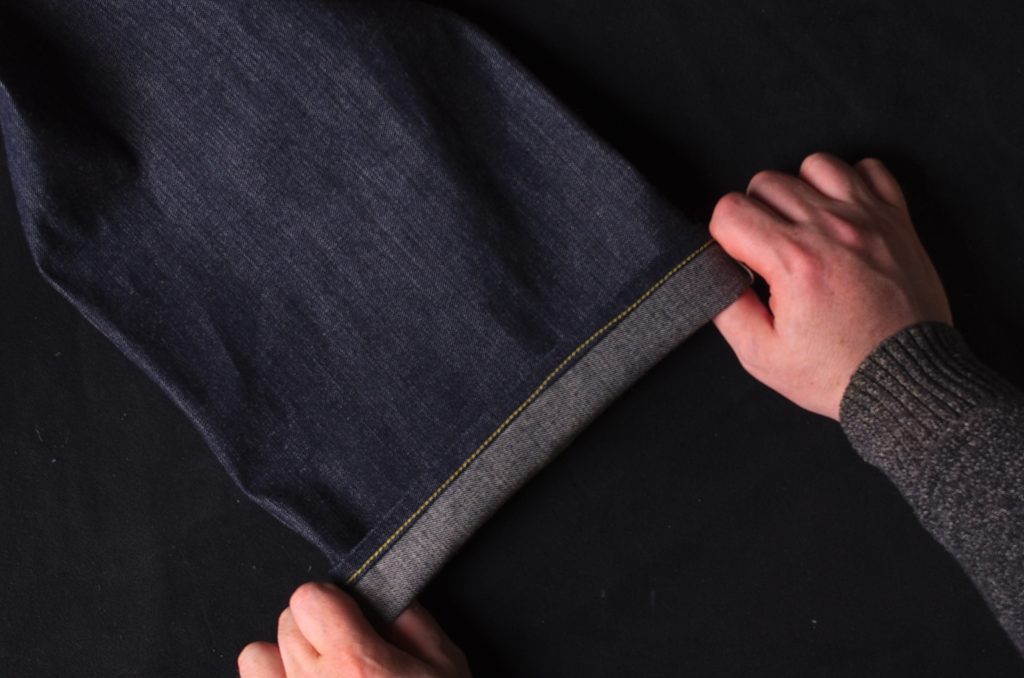
Use a ruler to get the correct width of the hem, and press the crease with your fingers as you work.
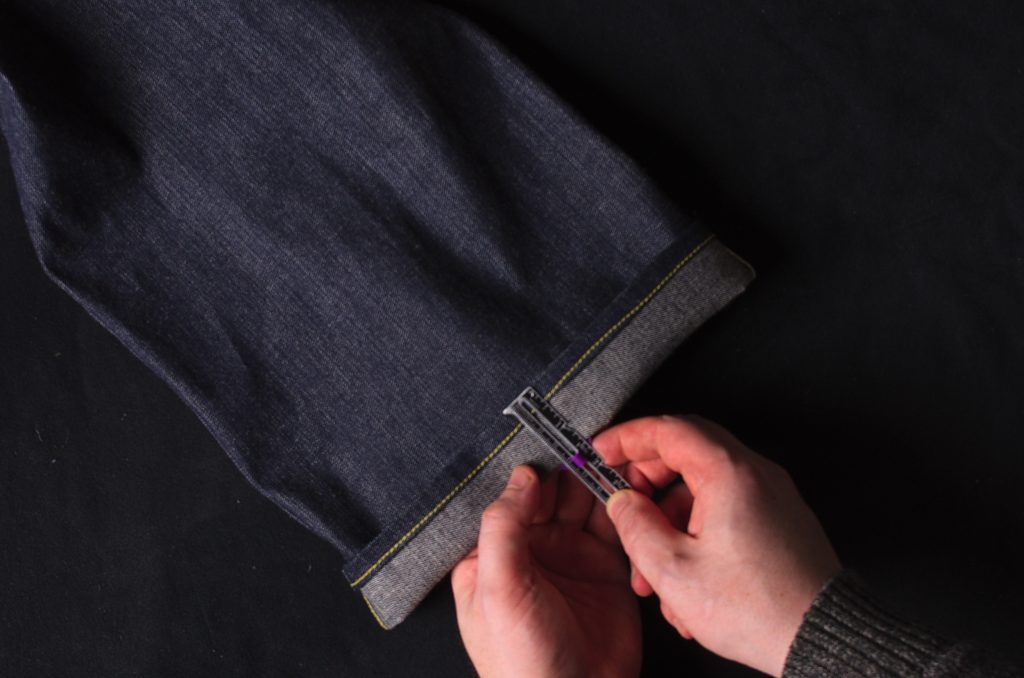
Finally, crease the turned up hem with the iron for a firm finish. You may want to wait for this step until you’ve completed the jeans entirely just to make sure you’ve got the hem spot on.

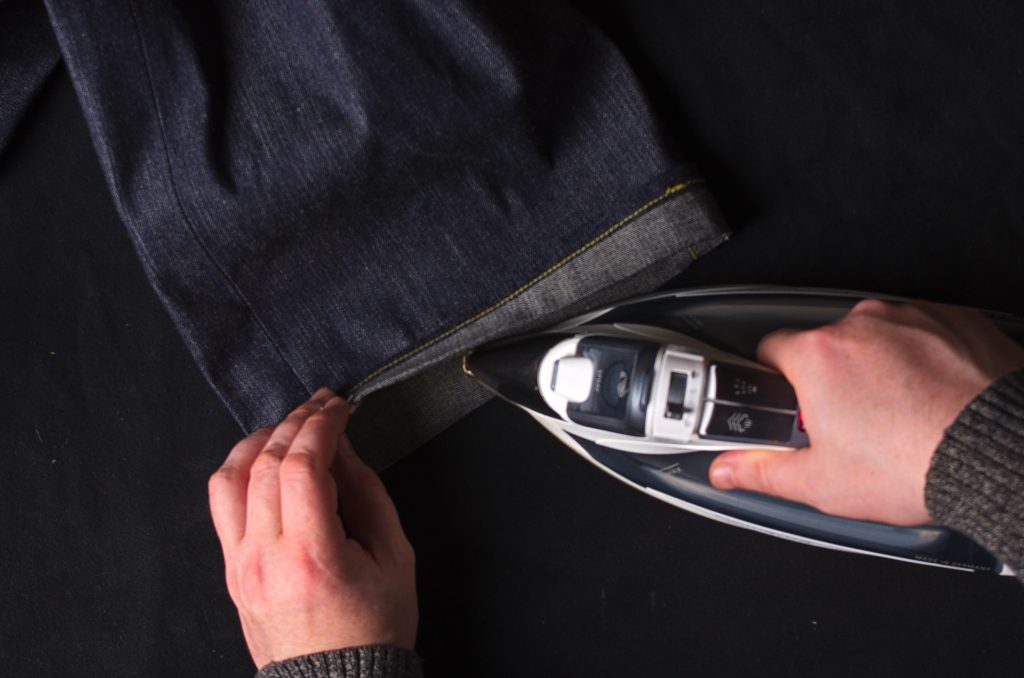
The Waistband
Finally, it’s time to sew on the waistband, giving us something that actually looks like a pair of jeans. Due to the thickness of the denim, I sew the waistband on freehand without pins or basting. It takes a little bit to get used to but is a great skill to develop.
Begin by aligning the waistband to the left fly along the waist, right sides together, with the waistband extending about 2″ beyond the edge of the fly.
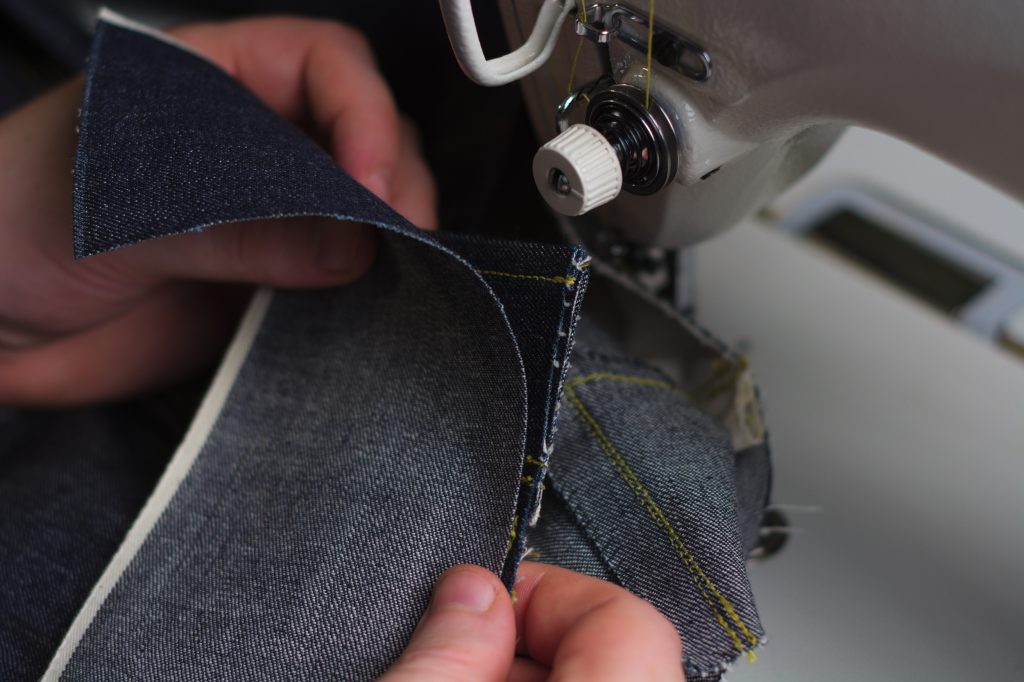
Begin sewing just at the edge of the fly using a 3/8″ seam allowance — you’ll kind of have to feel for the edge of the fly underneath. Flip the waistband back occasionally as you sew to make sure everything is lined up.
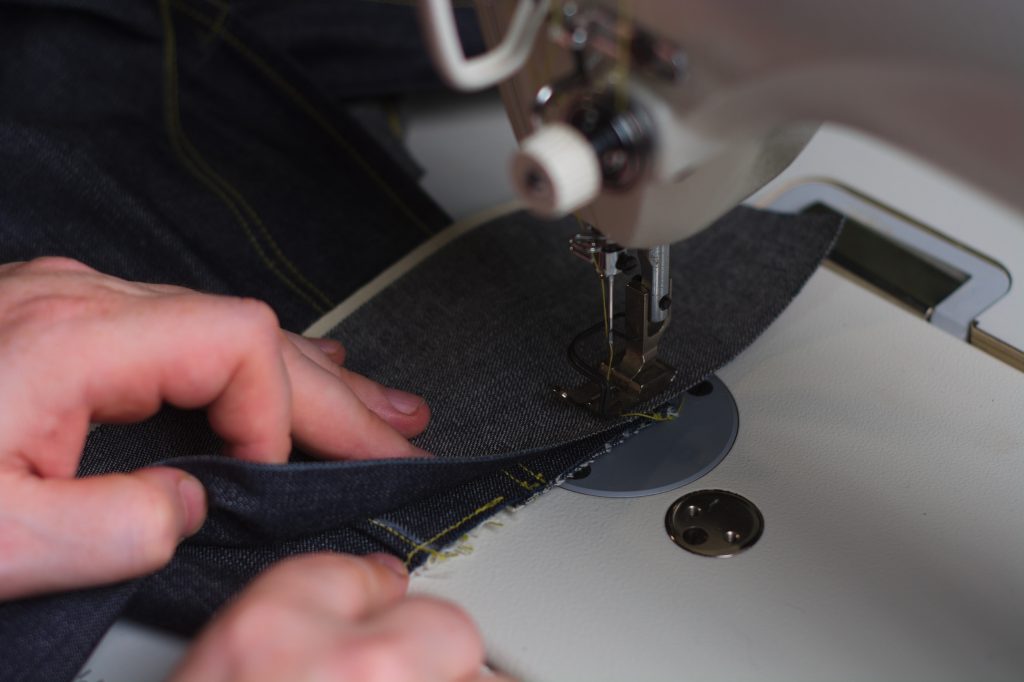
I used a seam gauge to ensure I was doing a proper 3/8″ seam the entire length.
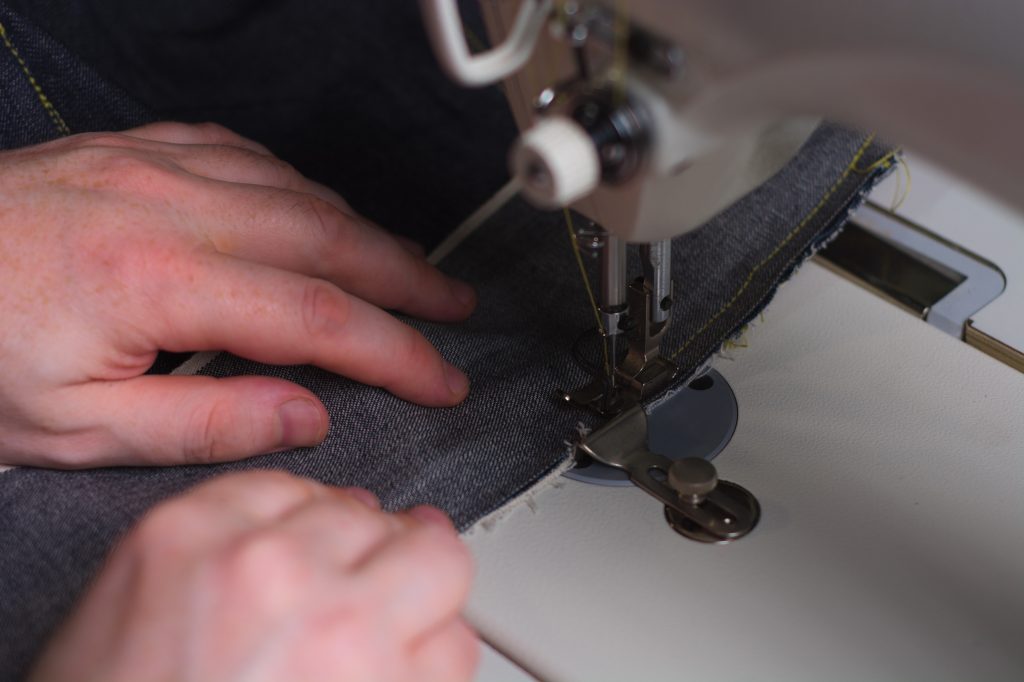
Manipulate the denim, moving it into position and checking your work as you sew to make sure everything is aligned, particularly near the side seam where the angles change slightly.
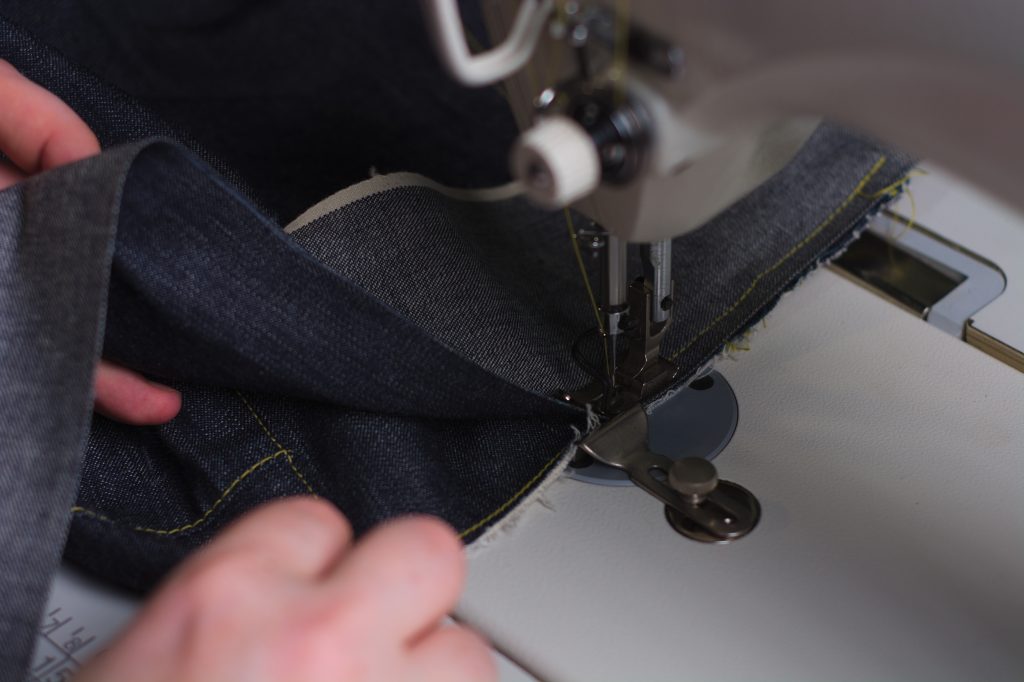
As you’re sewing, ensure that any pleats (for the 1873 jeans) or belt loops are in their correct position before you sew over them. Continue sewing through to the right fly, where you should have another couple of inches of extra waistband.
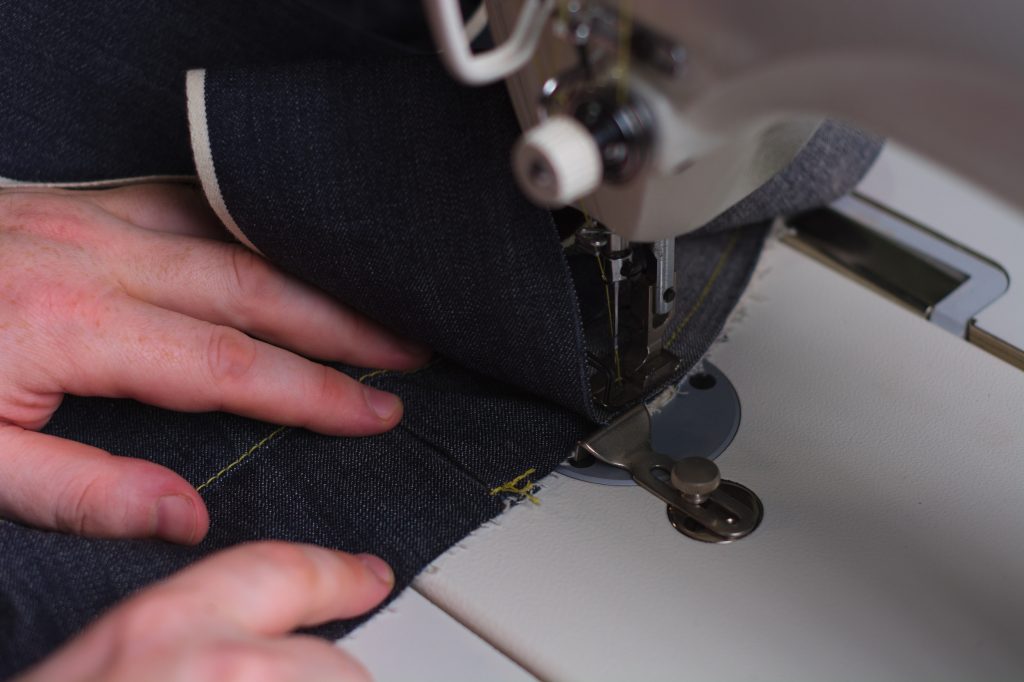
Pressing
Now open the waistband and press the waistband and seams up towards the top of the waistband.
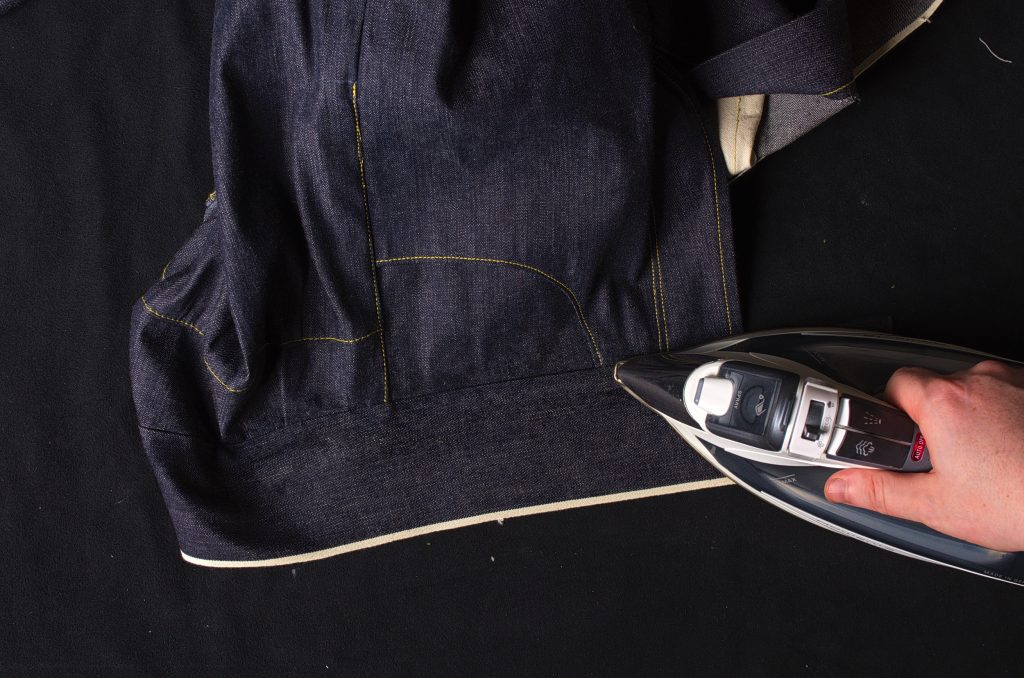
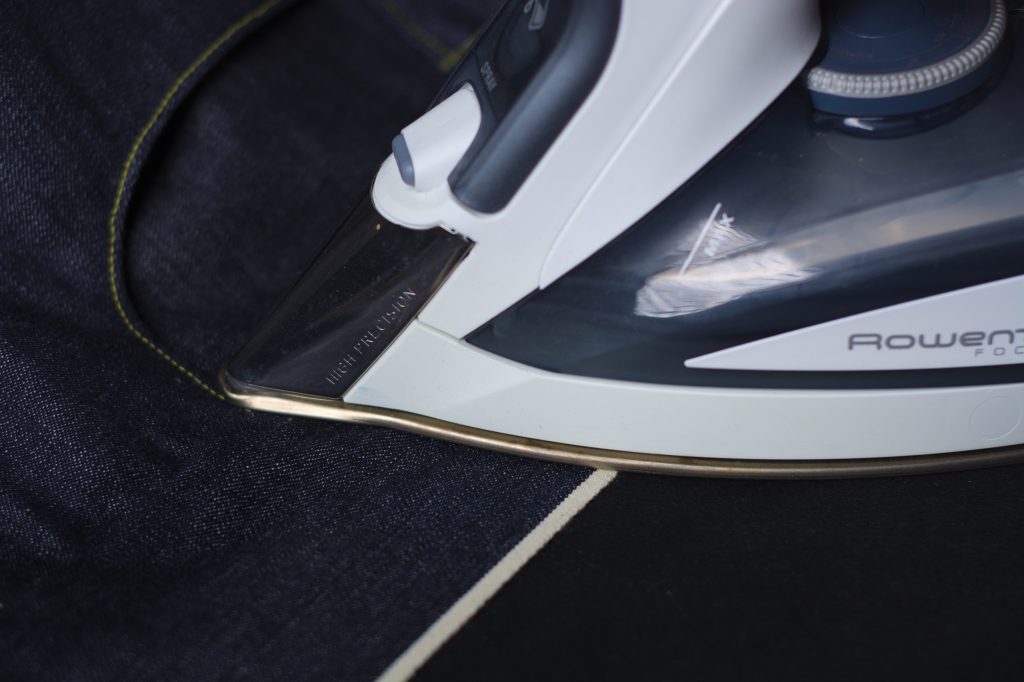
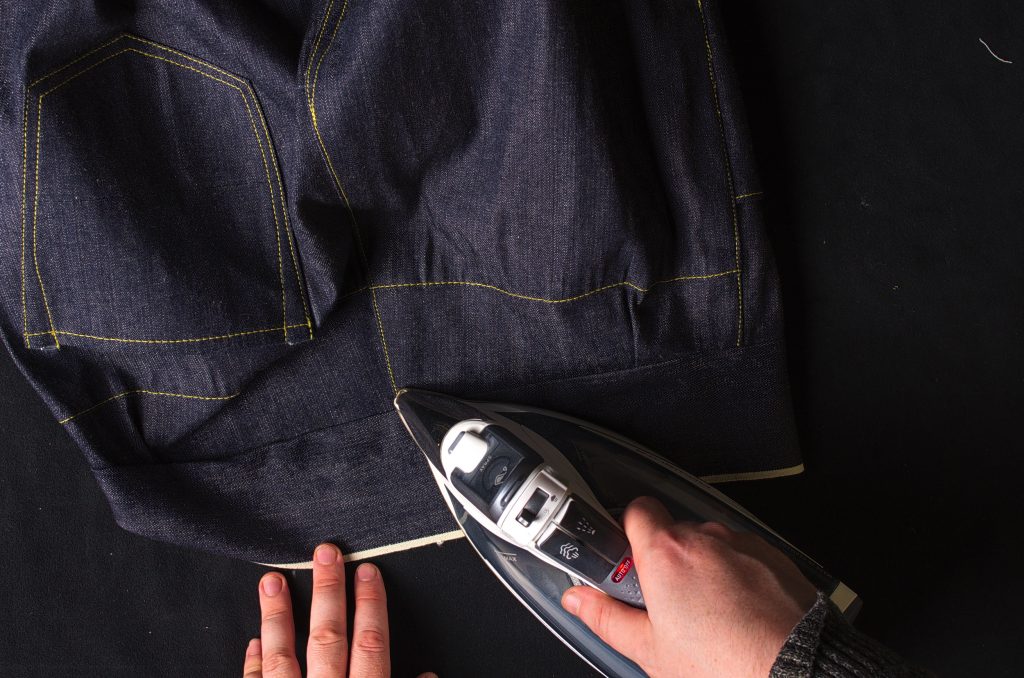
Use a ruler to mark the fold of the waistband, 1 1/2″ from the waist seam. My ruler just happens to be 1 1/2″ wide so it’s a lot easier to turn it sideways and use that for marking. Mark across the entire waistband with light marks so they’re not visible in the finished garment.
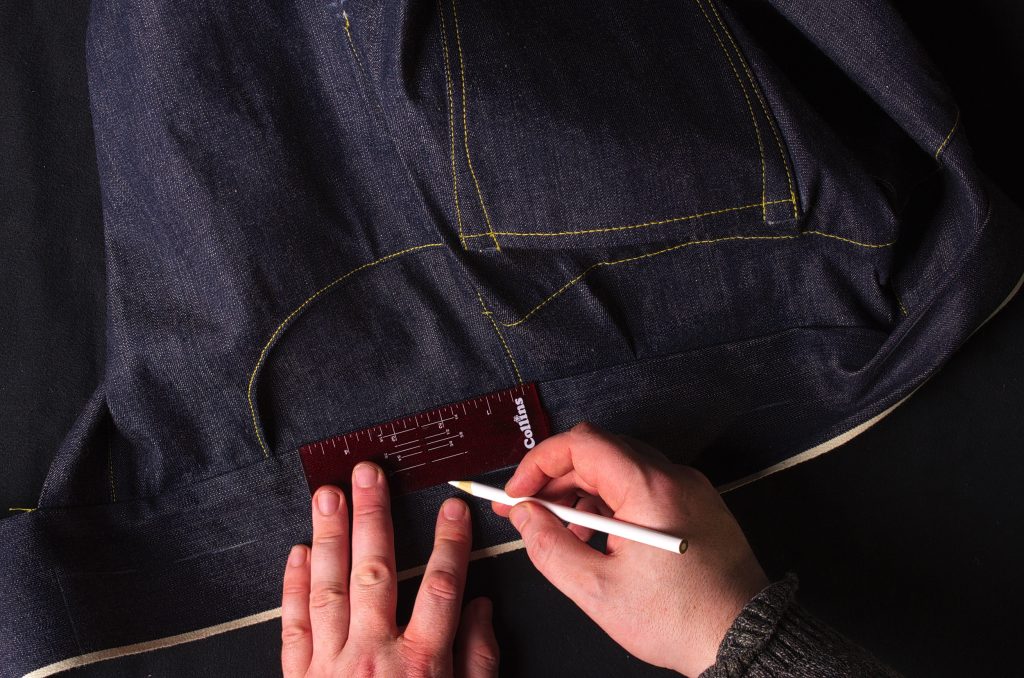
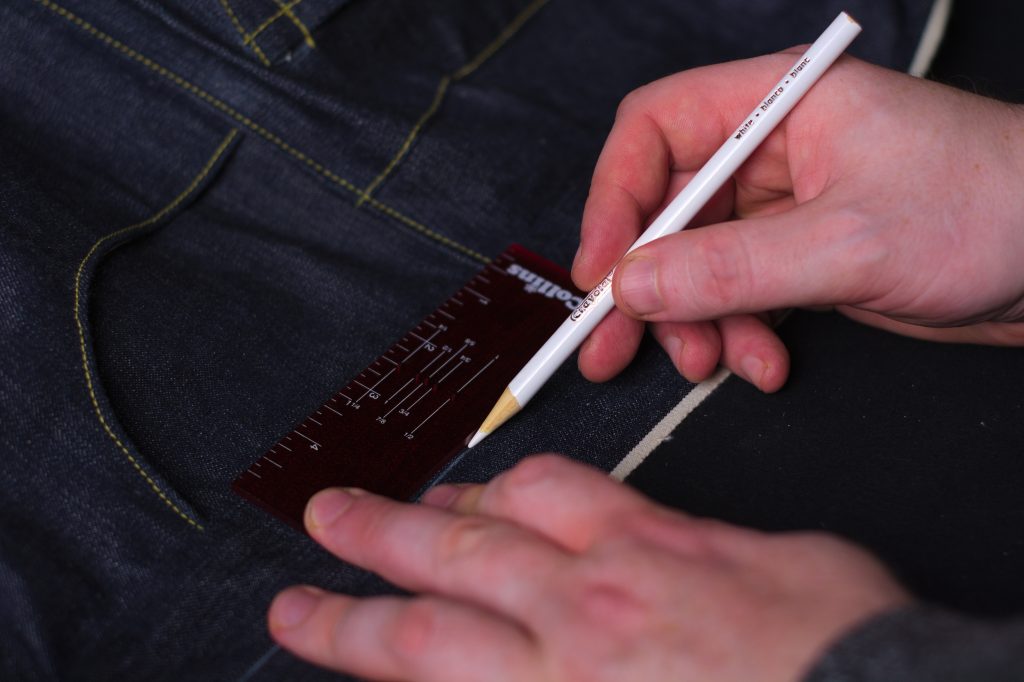
Now press the waistband in half along its entire length, turning the marks just slightly to the inside.
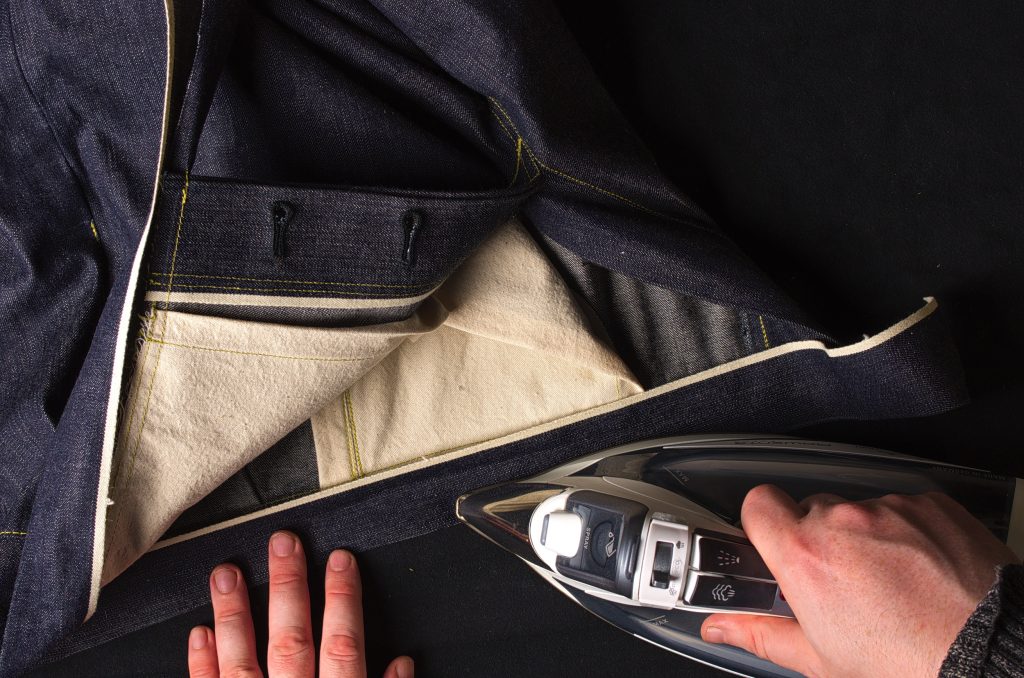
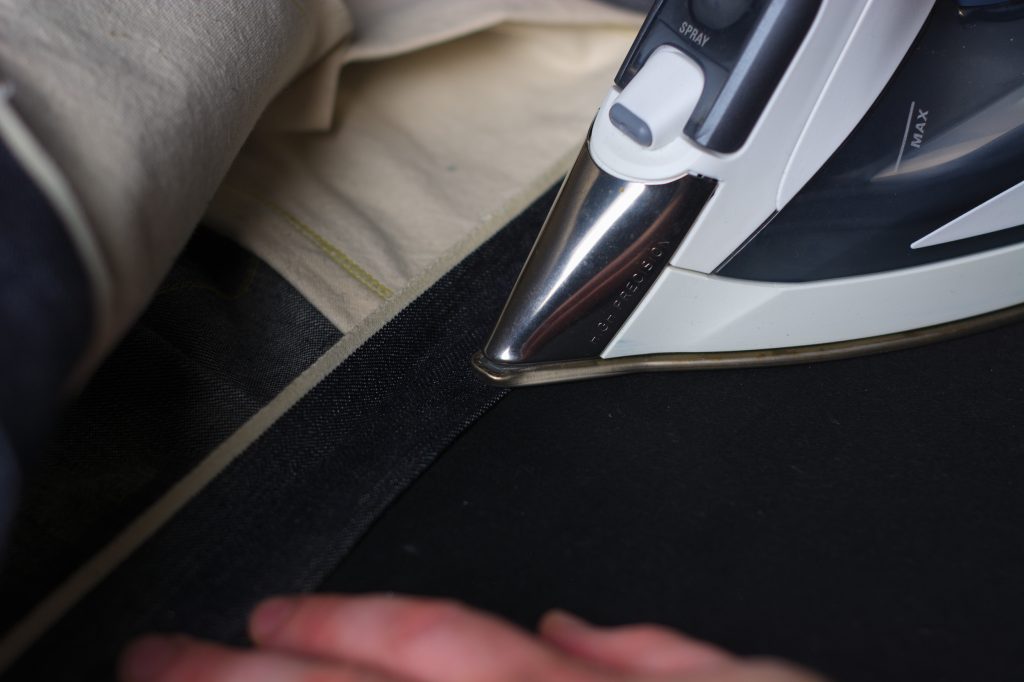
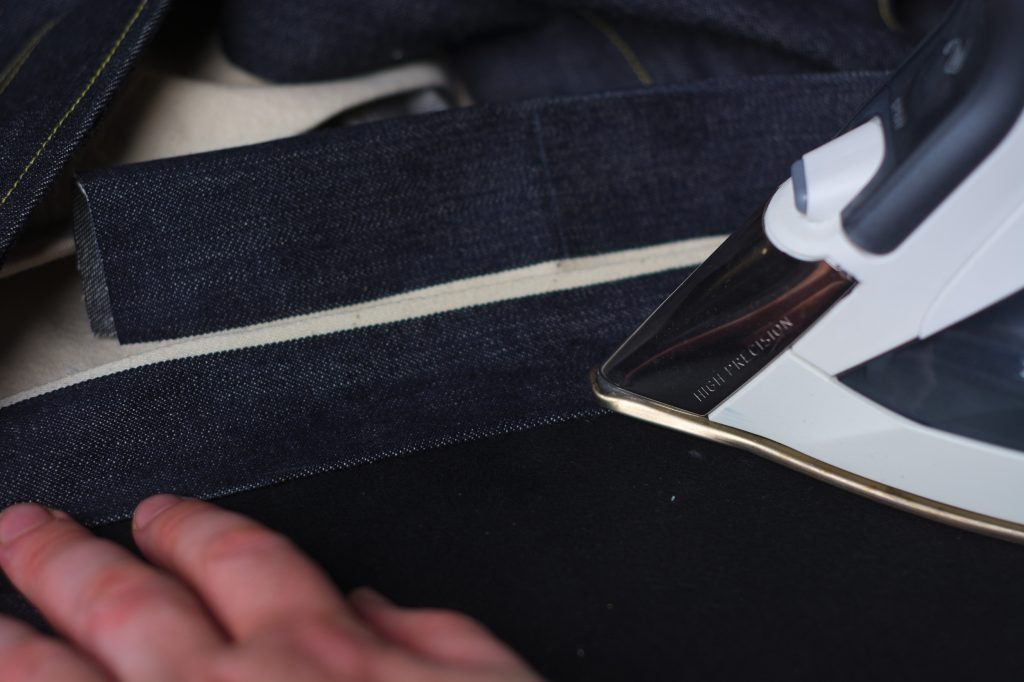
Open up the waistband on the wrong side and at each end, mark a line square with the waistband just at the edge of each fly. Press the ends of the waistband in along these two lines (not shown).
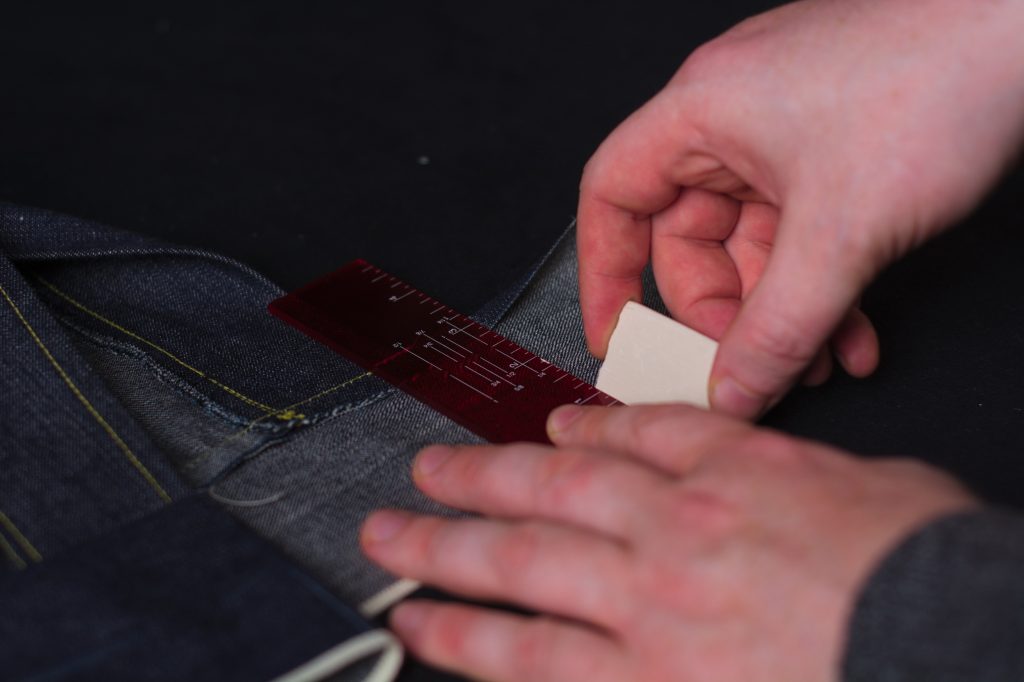
Now make another two lines about 2″ square from the edge of the fly at the ends of the waistband. You want enough here to be able to turn the ends cleanly in and have enough room for the buttonhole and button. Made a little miscalculation on the right fly area, hence the two lines.
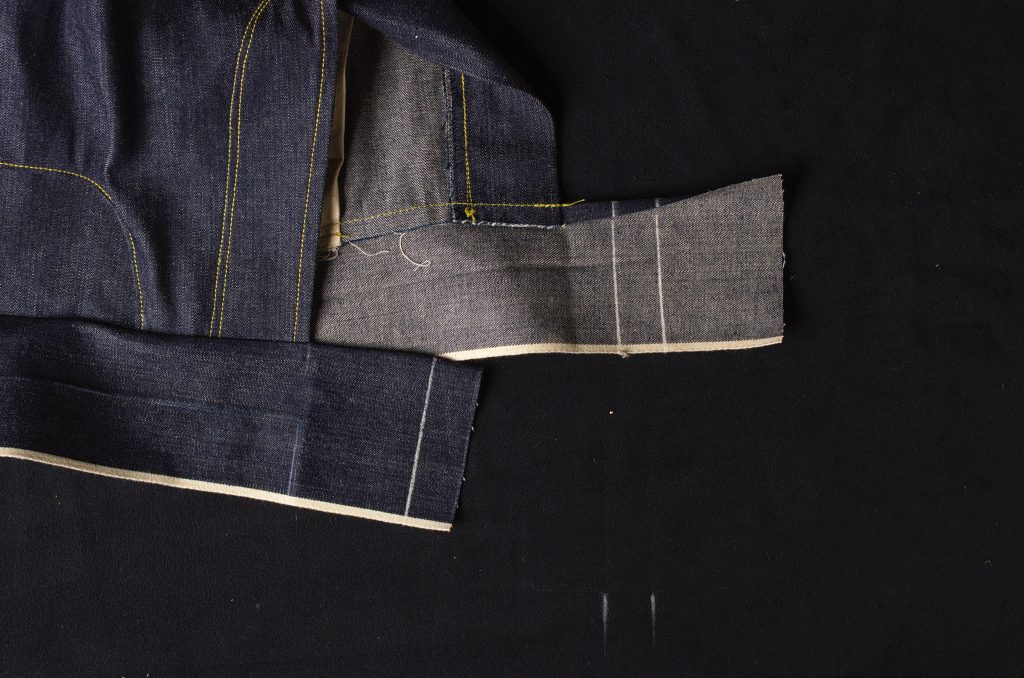
Trim off the excess waistband material.
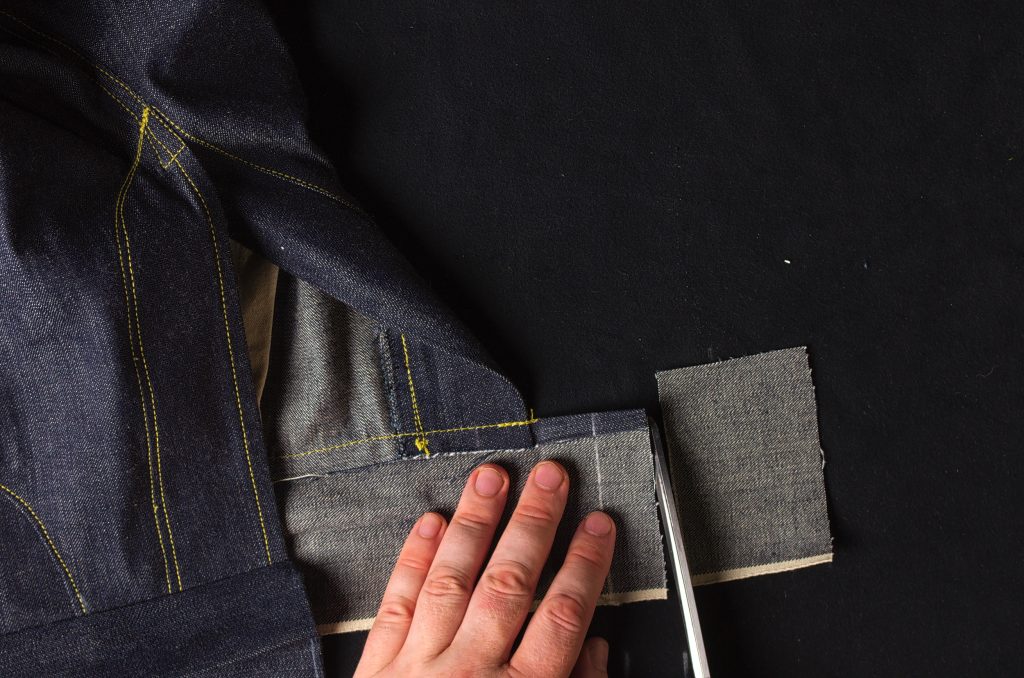
Now press the ends of the waistband over so that they’re just about aligned with the edges of the fly. The waistband should be kept square at the ends both for appearance, and so you don’t lose width if you were to cut it at an angle to match the fly.
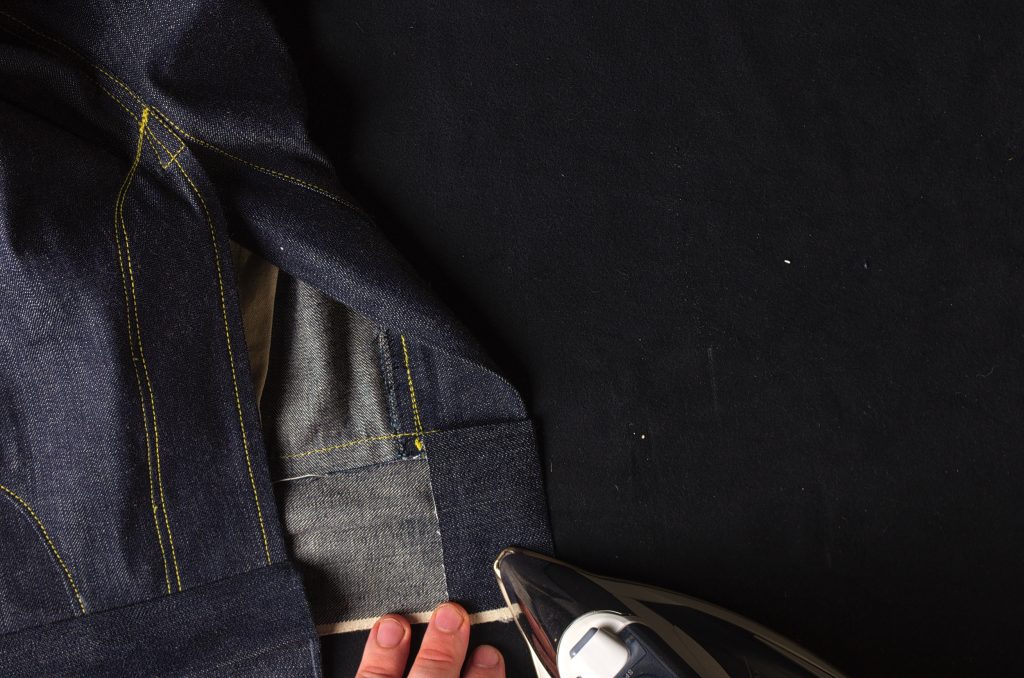
Press the waistband in half lengthwise again just to ensure a firm, crisp finish.

If you want, you can fold the cut selvedge edge under again at a bit of an angle to completely hide the cut at the end of the waistband. Press once again.
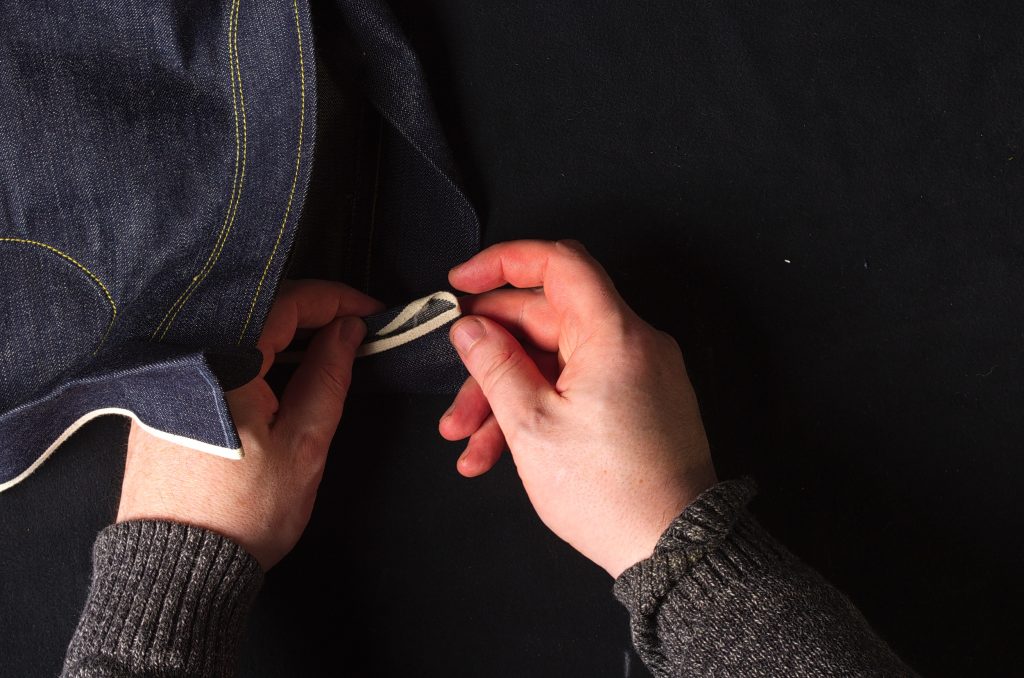
Here’s how your waistband should look after all of the pressing.
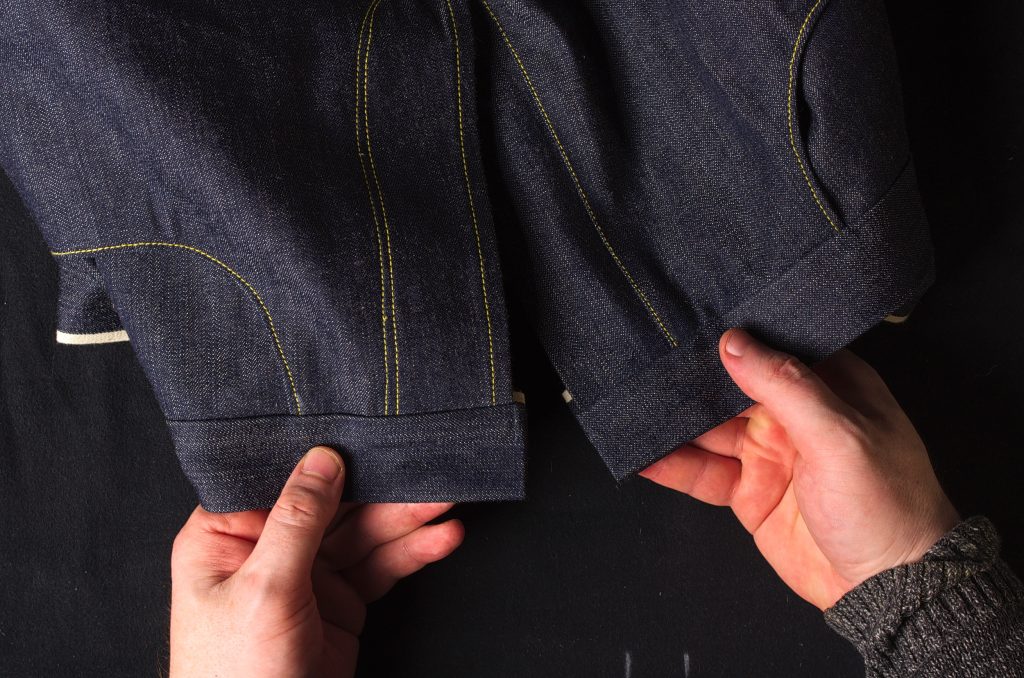
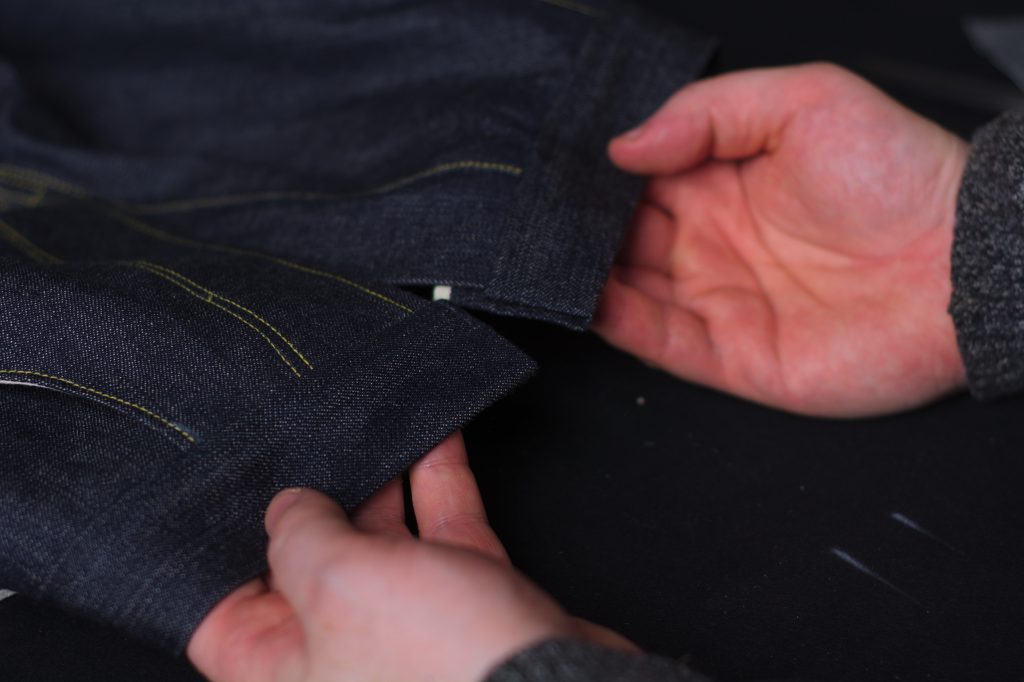
Top Stitching
To finish securing the waistband and prevent the layers from shifting, the waistband is top stitched all the way around. Before starting, you should take a look underneath and ensure that your selvedge edge extends about 1/4″ to 3/8″ below the waistband seam, ensuring it will be caught in the top stitching.
The following two photos just demonstrate the alignment of the sewing needle, about 1/8″ from the waistband seam, in relation to the selvedge underneath.
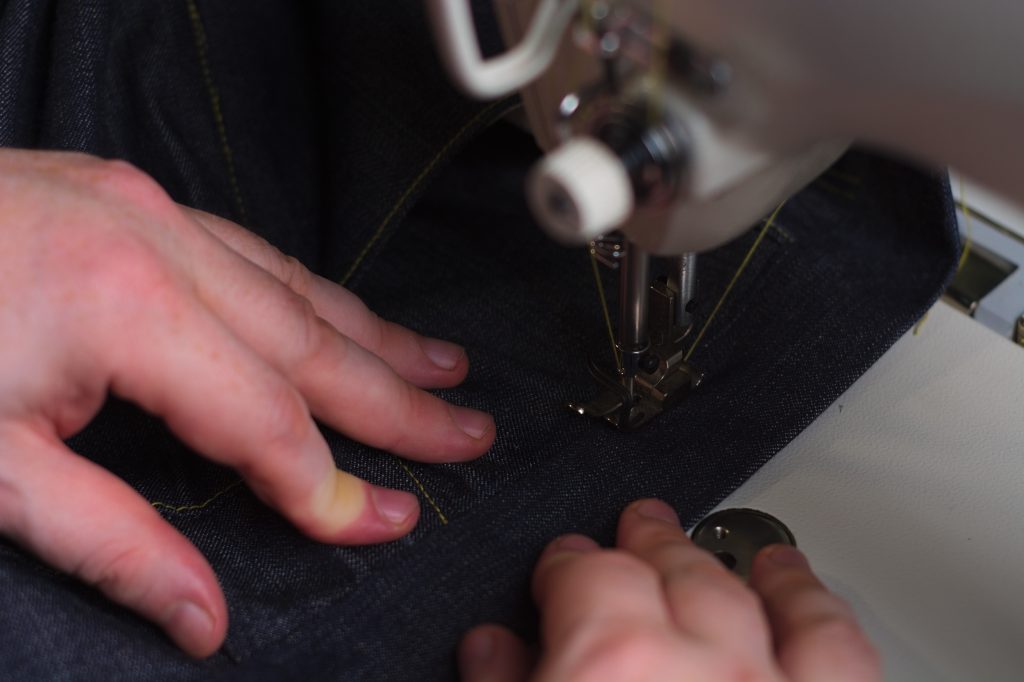
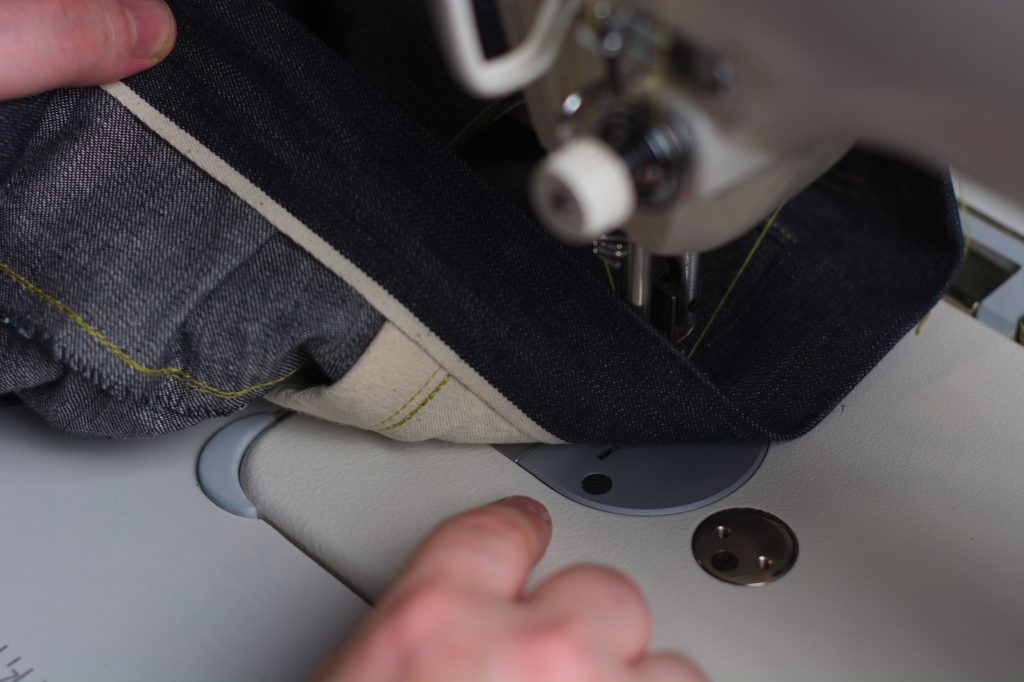
Begin top stitching at the front edge of the waistband at the left fly, down to and across the waist seam, using a 1/8″ seam allowance, being sure to catch the selvedge underneath as you sew.
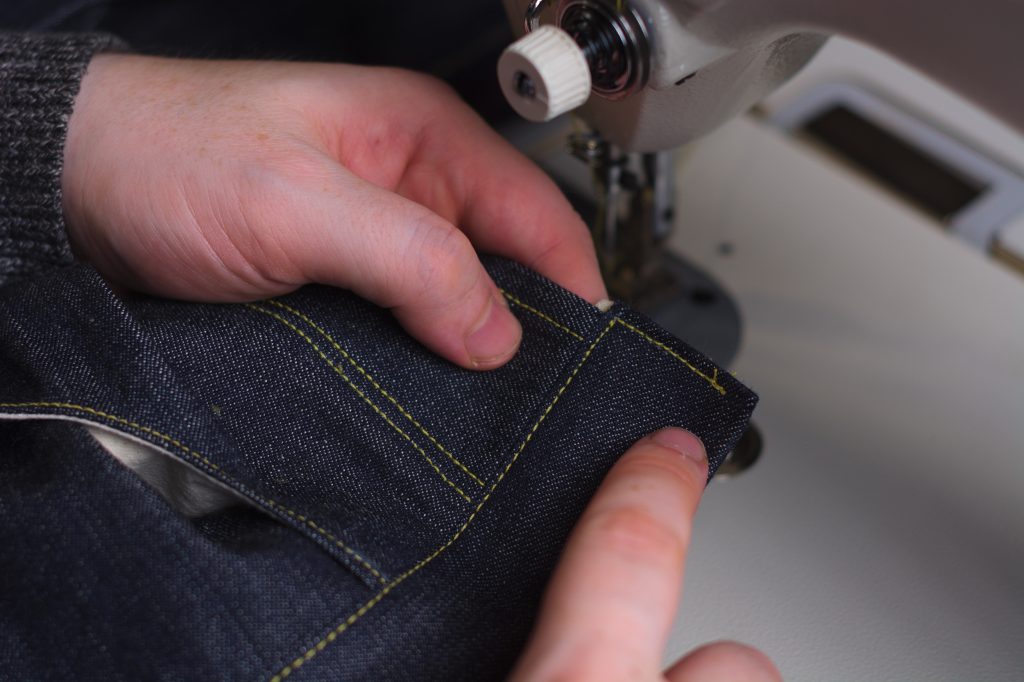
I recommend sewing a couple of inches at a time, turning back the waistband after to ensure a perfect alignment.
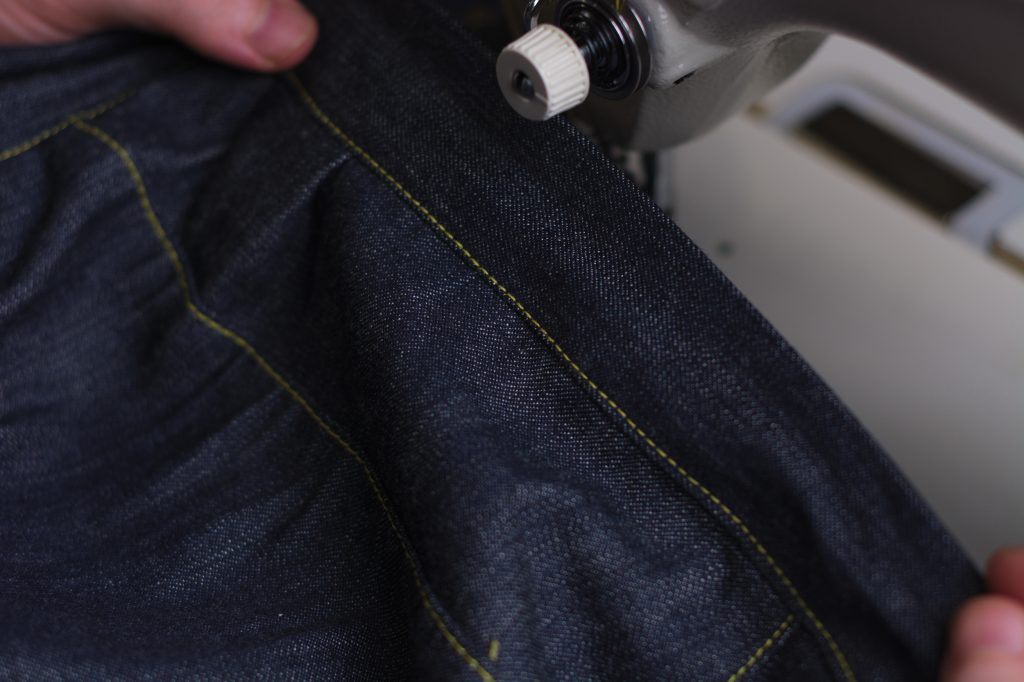
Continue sewing to the other end of the waistband, and about halfway up the right fly. The top stitching is done in two passes so that we don’t have to have the entire pair of jeans under the arm of the sewing machine as would be the case if we kept sewing.

Double check your work here to ensure the stitches are properly aligned underneath. I’ve accounted for the seam allowances in the waistband pattern so that the stitching should ideally end up just above the selvedge.
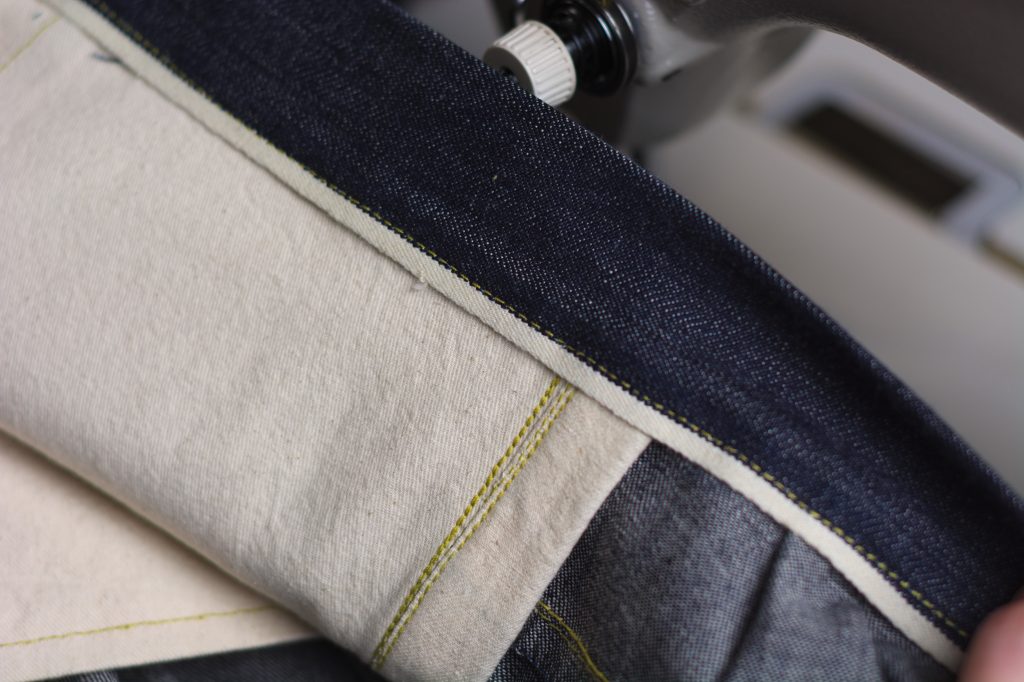
Starting again at the left fly, top stitch the remaining fly end, and then turn and top stitch the top edge of the waistband.
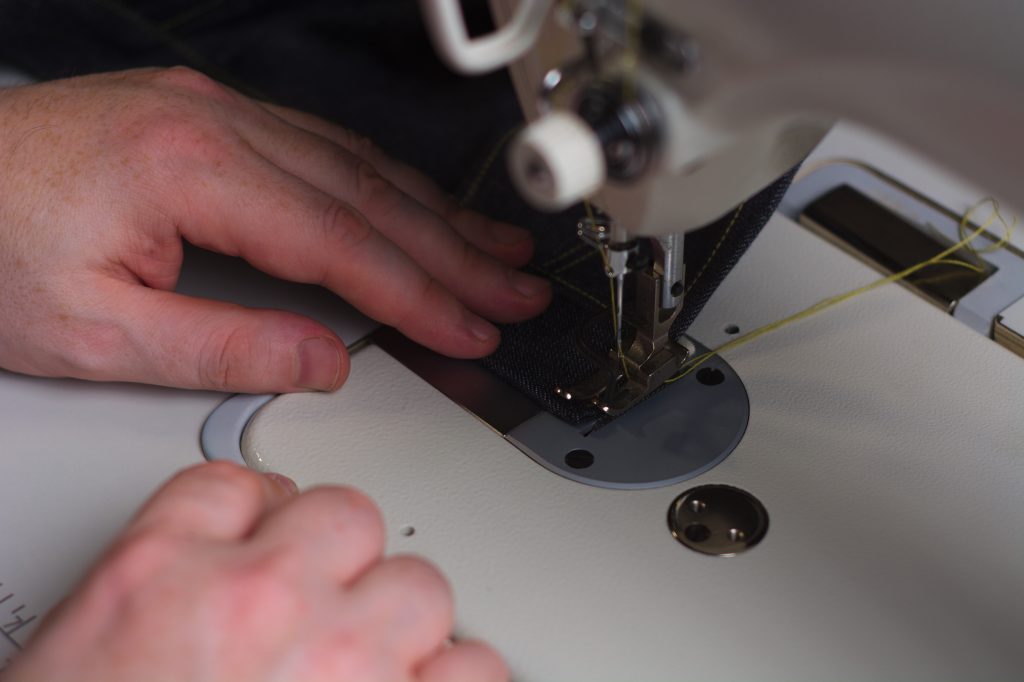
Sew across the top of the waistband.
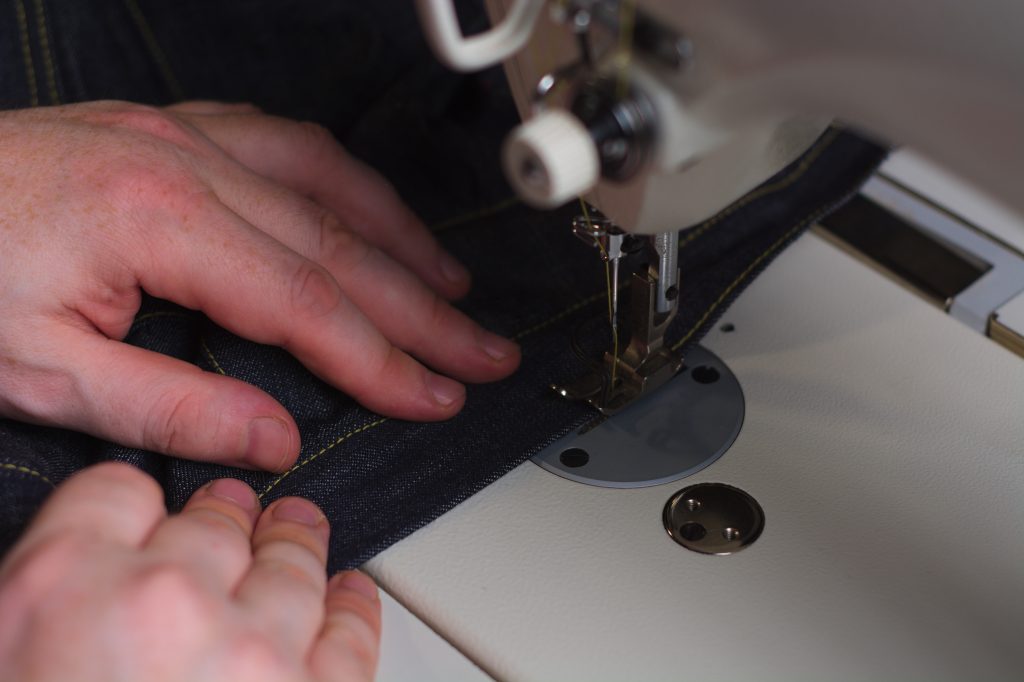
Here are the results of the top stitching. There should be some overlap of stitches at the fly ends, but everything should be nice and square and even across the entire waistband.
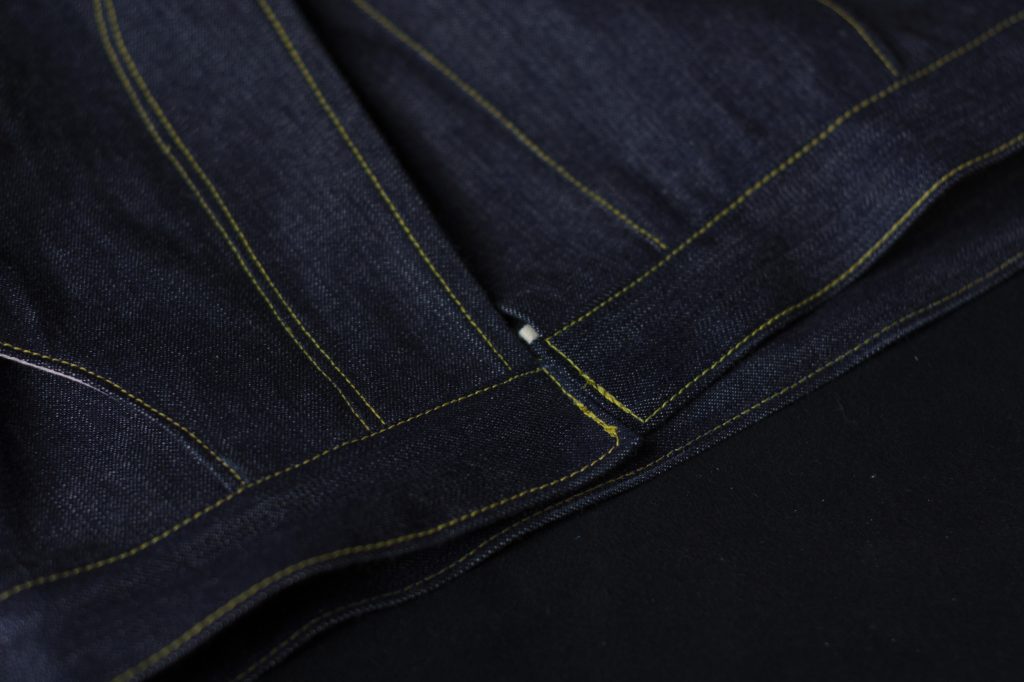
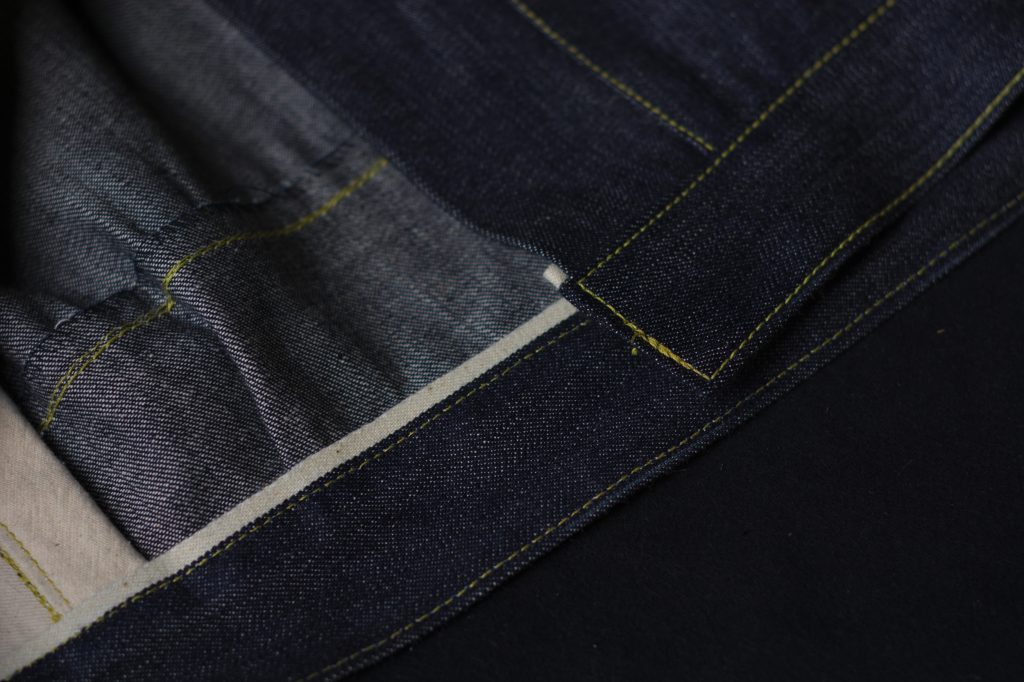
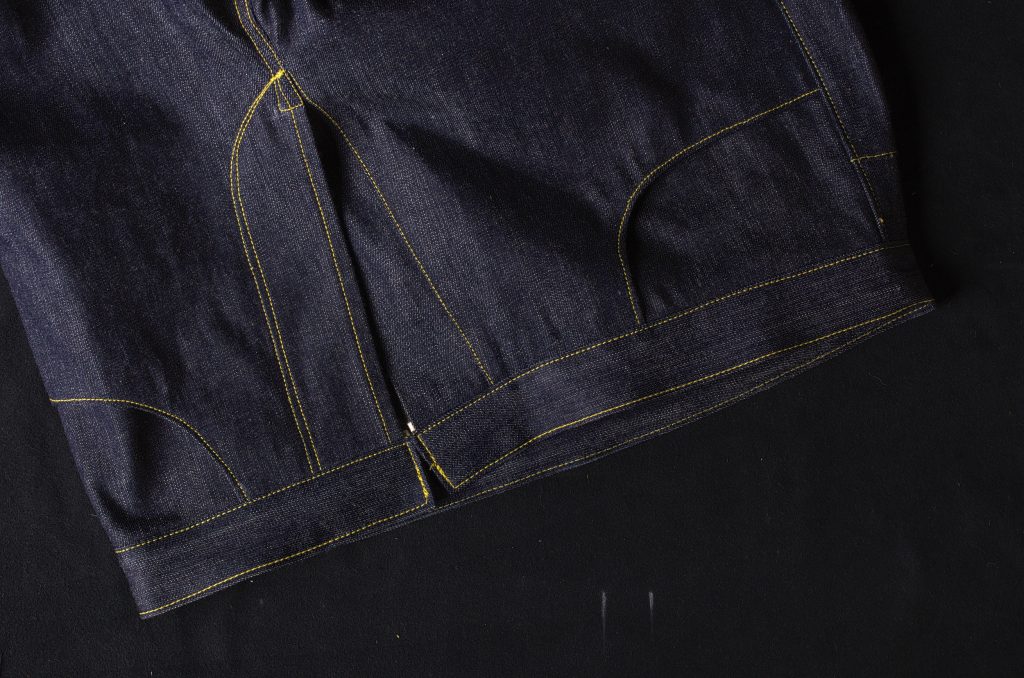
Belt Loops I – Modern
For those making a modern pair of jeans, now is the time to begin attaching the belt loops. Note that I’m using the 1873 pair here only as a demonstration – will update this when I make another modern pair.
Positioning the Belt Loops
To determine the positions of the belt loops, first lay your front pattern on the front leg and find the center line. This is usually at the point where the waistband meets the pocket opening. Move the point 1/2″ in either direction (whatever looks best to you) to make sure there is room for the rivet. Repeat for the other leg.
Then about 1/2″ past the side seam towards the back, mark another point for the next belt loop. Depending on your size and preference you might want one spaced evenly between the two.
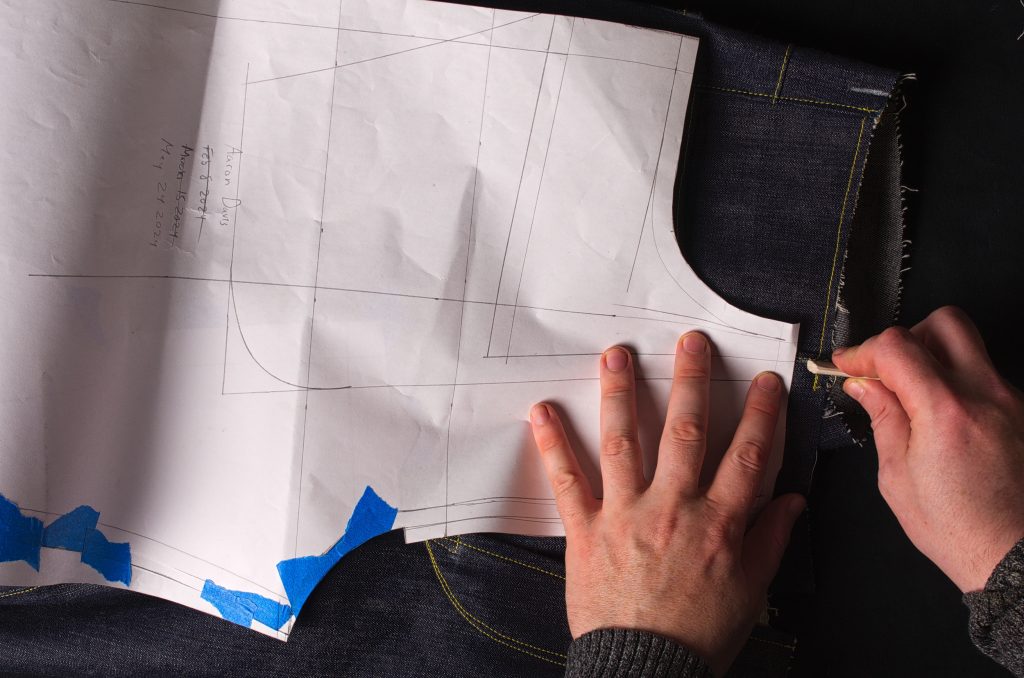

Turning to the back side, evenly space out two or three more belt loops (you could have one at the center back). This was a smaller pair and the belt loops were close enough together without adding a third.
The key is no matter how many you add, to keep them spaced evenly.
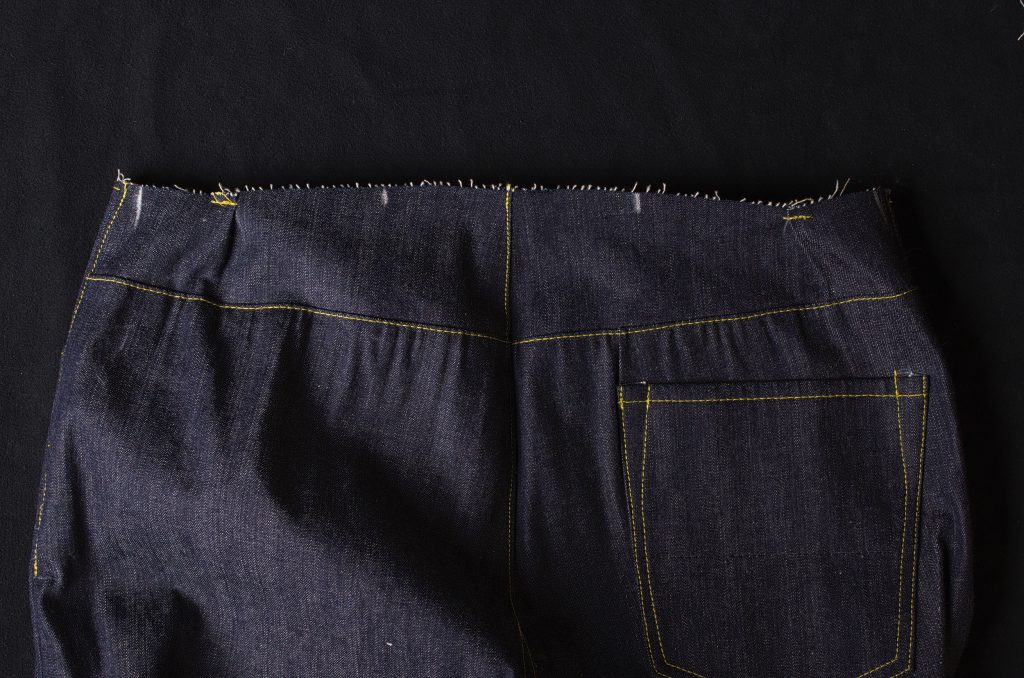
Cutting the Belt Loops
Mark out a length of denim, ideally on the selvedge, giving 4″ minimum for each belt loop, and about 1 1/2″ wide for a 1/2″ belt loop. The final width is up to you, but I find 1/2″ is a good size for the finished belt loop.
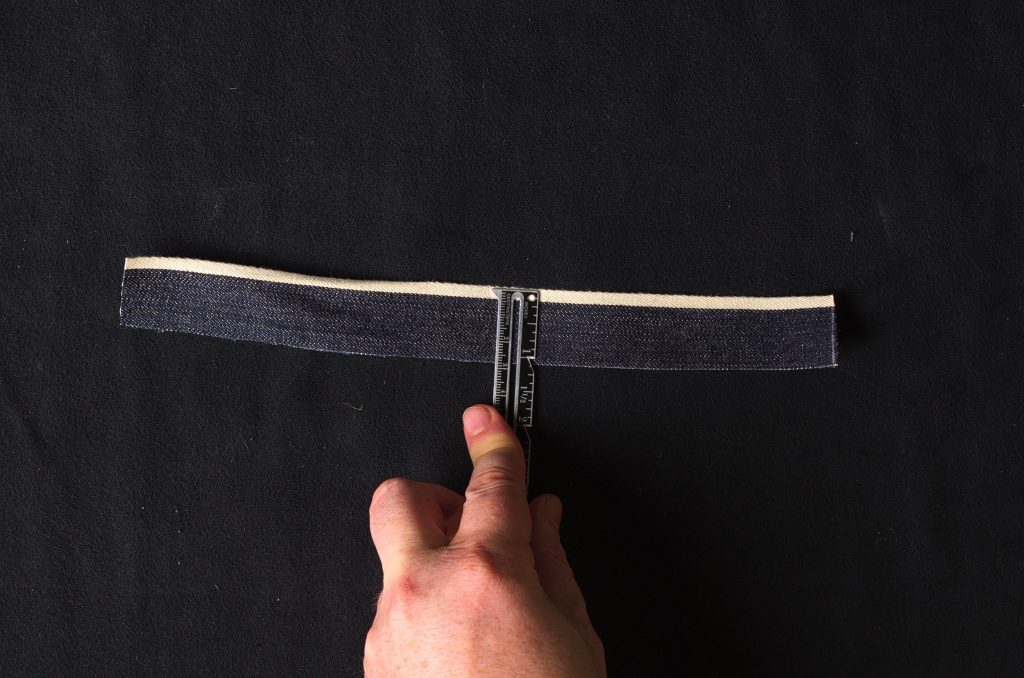
Press over the raw edge to the wrong side by just under 1/2″.
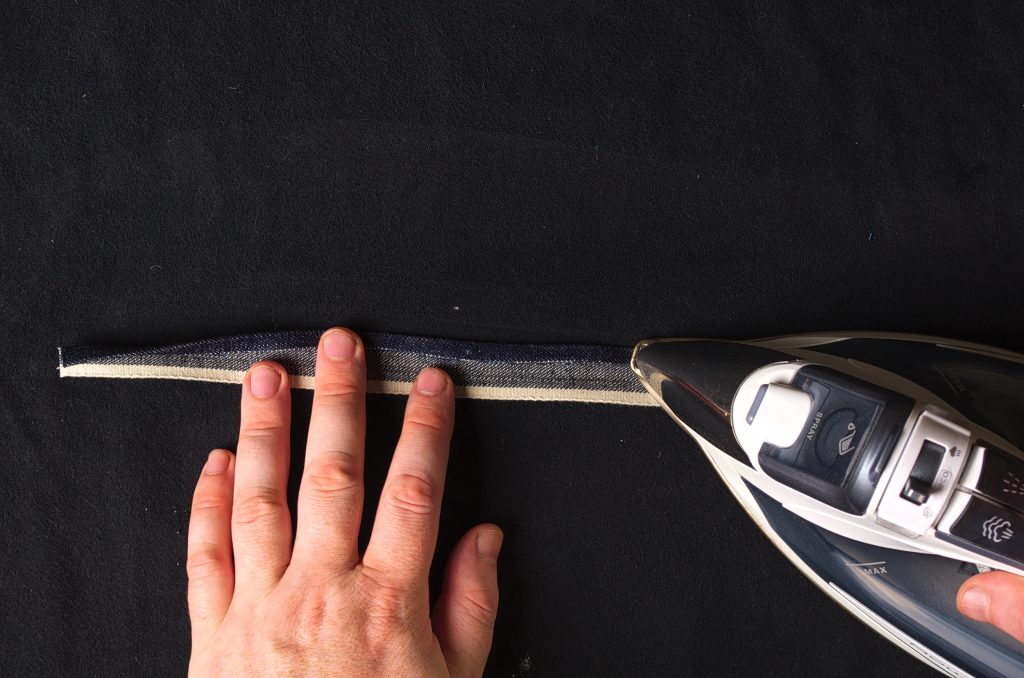
And then press over the selvedge edge, giving you the final 1/2″ width. Normally you’d have a much longer piece to cover all the belt loops – just demonstrating with a smaller piece.
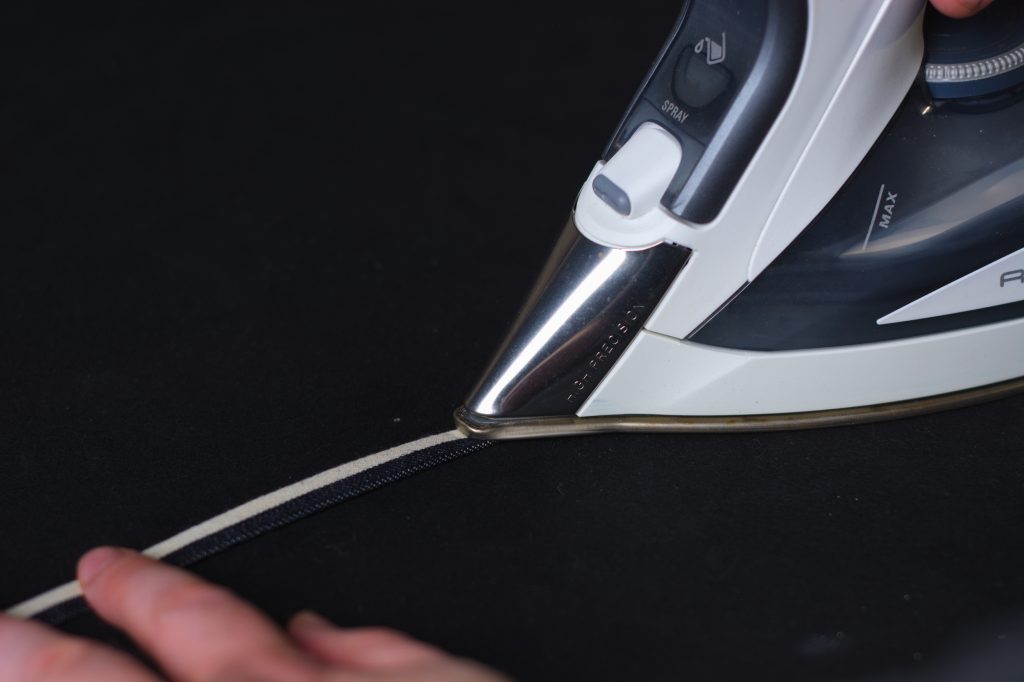
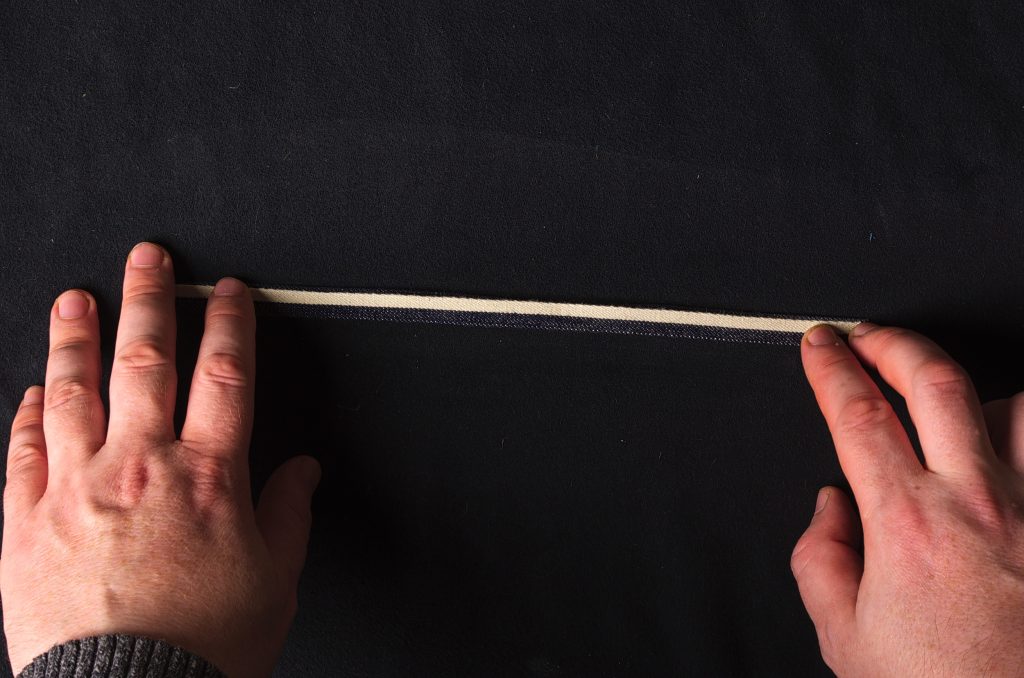
Top stitch along each long edge of the belt loops, about 1/16″ from the edge.
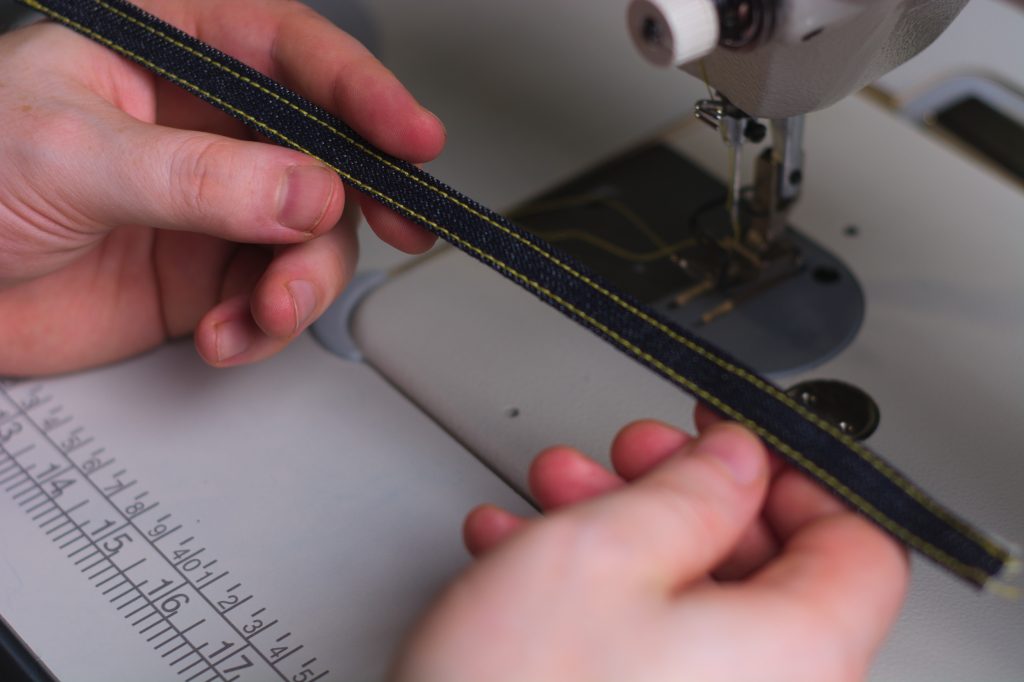
The stitches should catch the selvedge completely underneath.
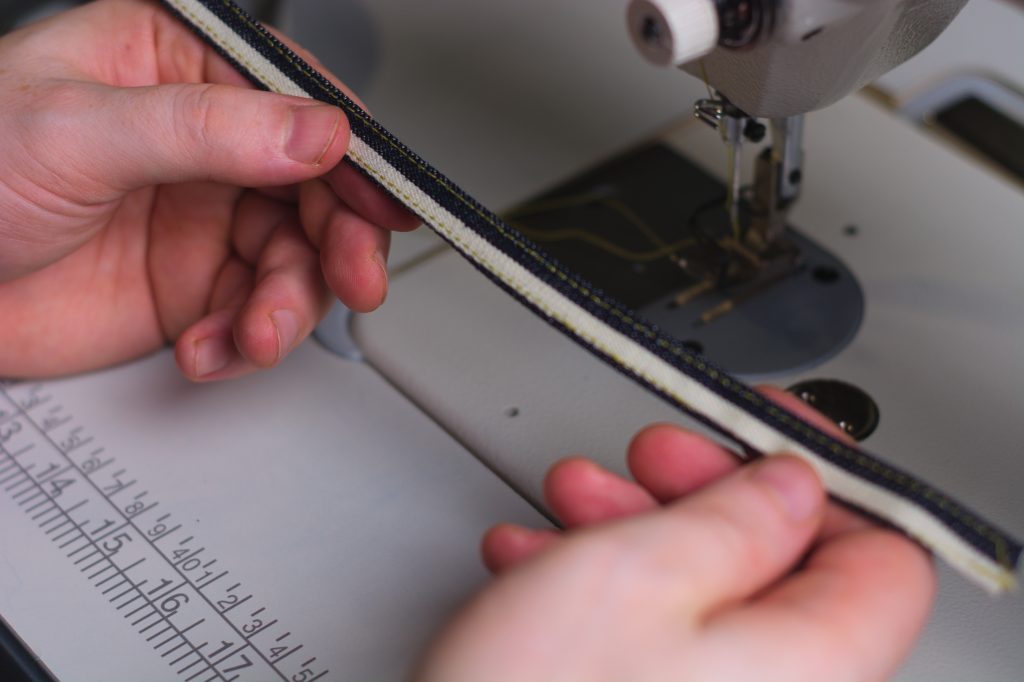
Here’s what happens if you run off the edge.
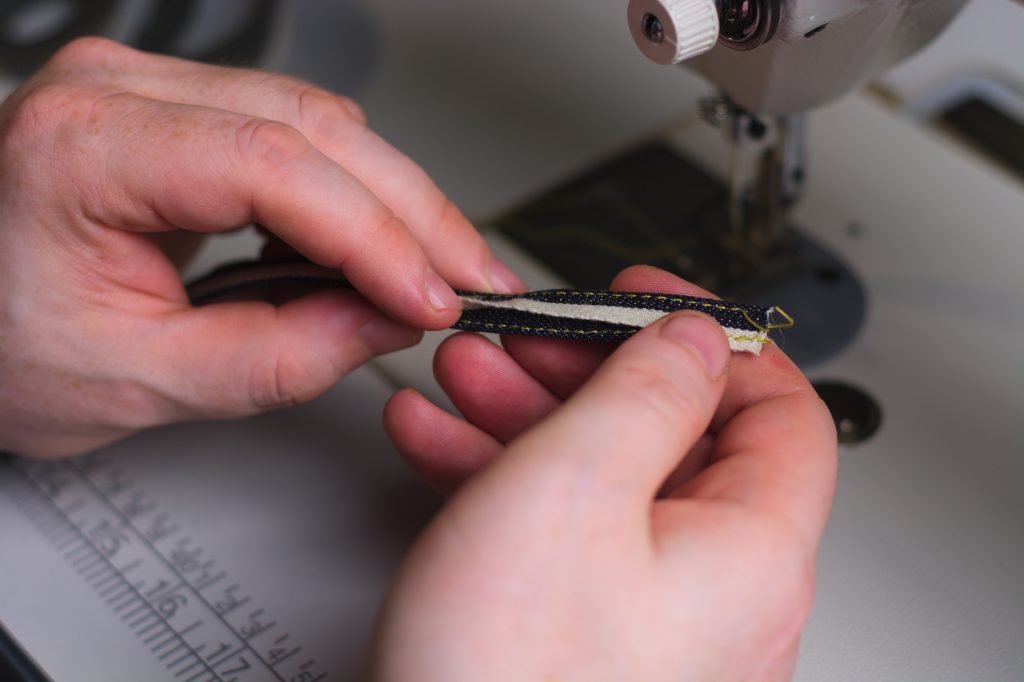
Mark off about 4″ per belt loop and cut each one to length.
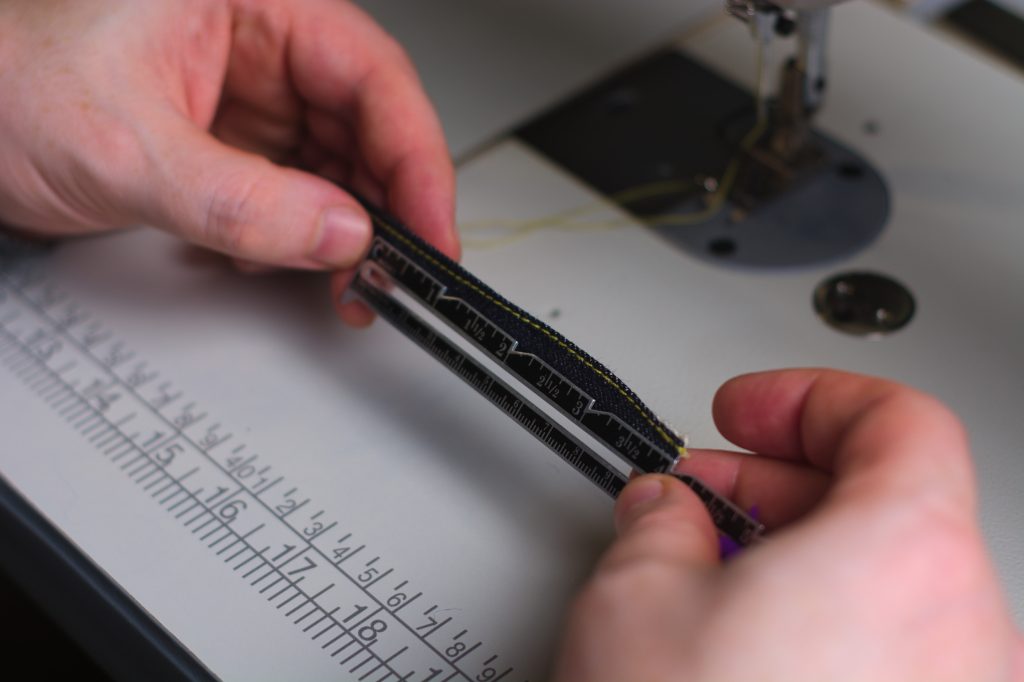
Place the belt loop in position, right sides together, on the mark you made at the waist (I should have shifted this one over to make room for the rivet).
Ensuring that the belt loop is at right angles to the waist seam (use a ruler if necessary), bar tack across the belt loop about 1/4″ from the waist. This way the bar tack will be hidden under the waistband.
Repeat for each belt loop.
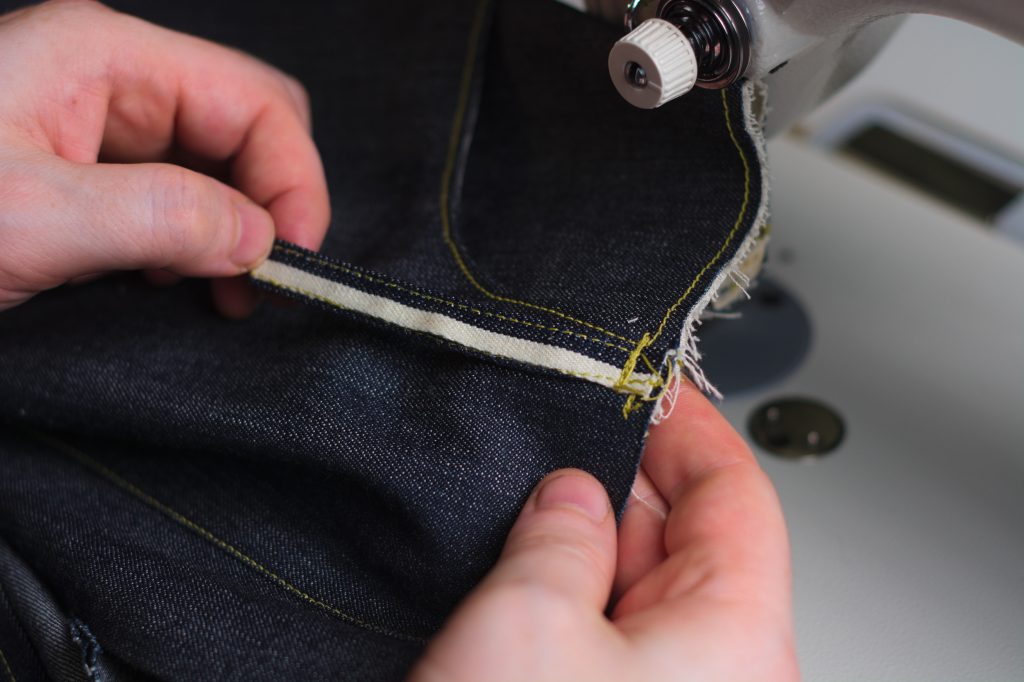
The Side Seam
Before sewing the side seam I like to open up each leg to ensure I’m sewing the correct seams together.
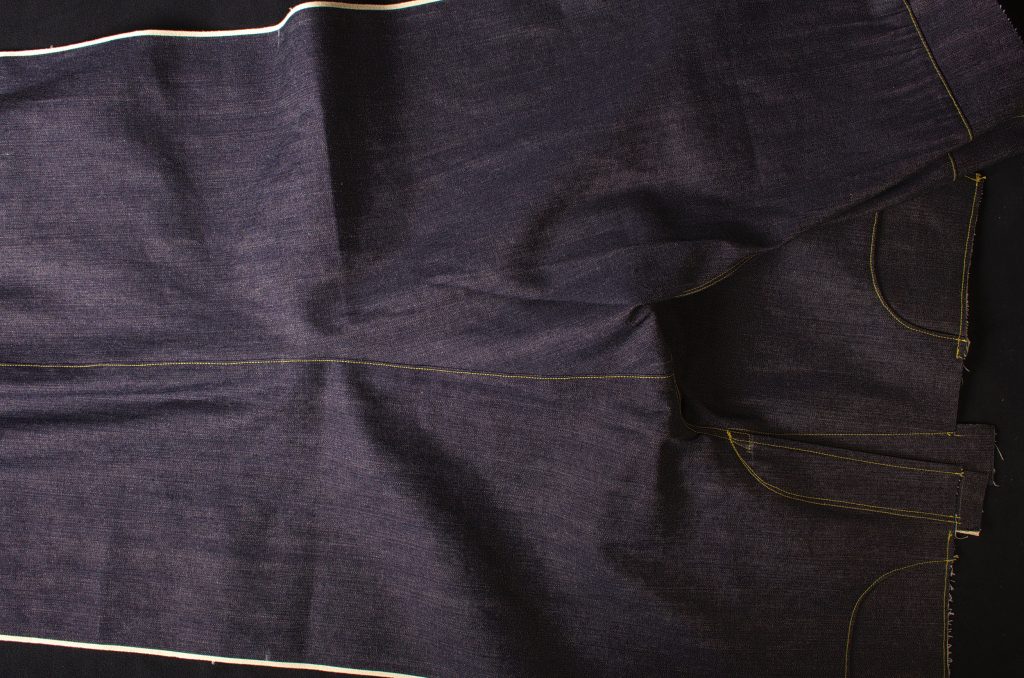
Fold each leg in half, right sides together, matching the side seams at the waist and hem. You can pin this if you like, but it’s a good skill to develop to not need the pins. If you are going to pin, pin the waist and hem, then the knee and hip marks, and then in between as necessary.
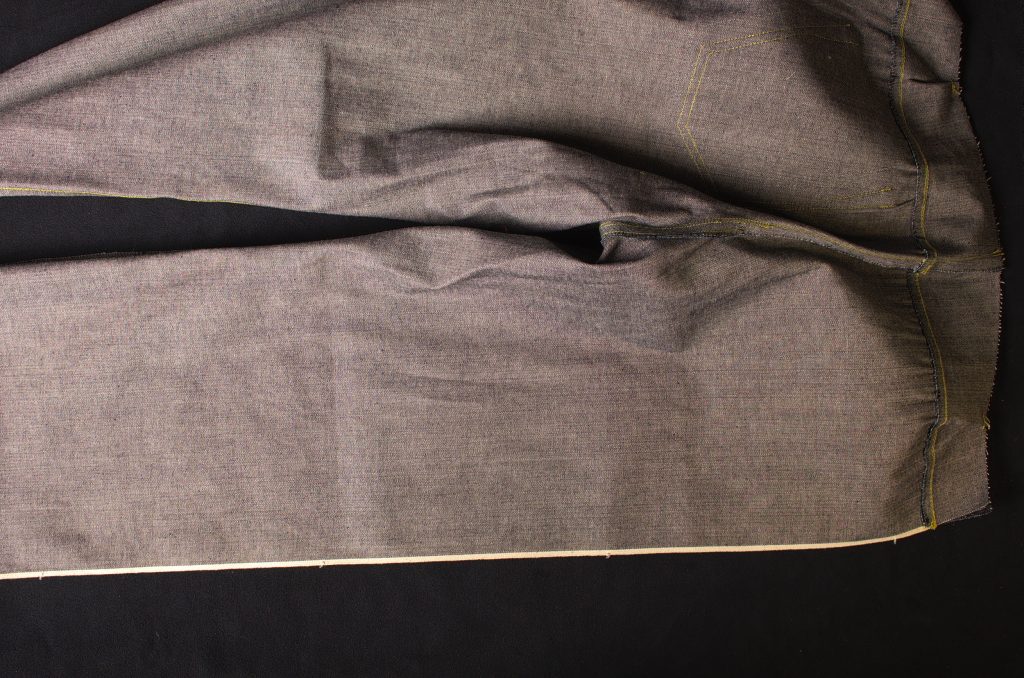
Beginning at the waist, sew the side seam through all layers using a 3/4″ seam allowance.
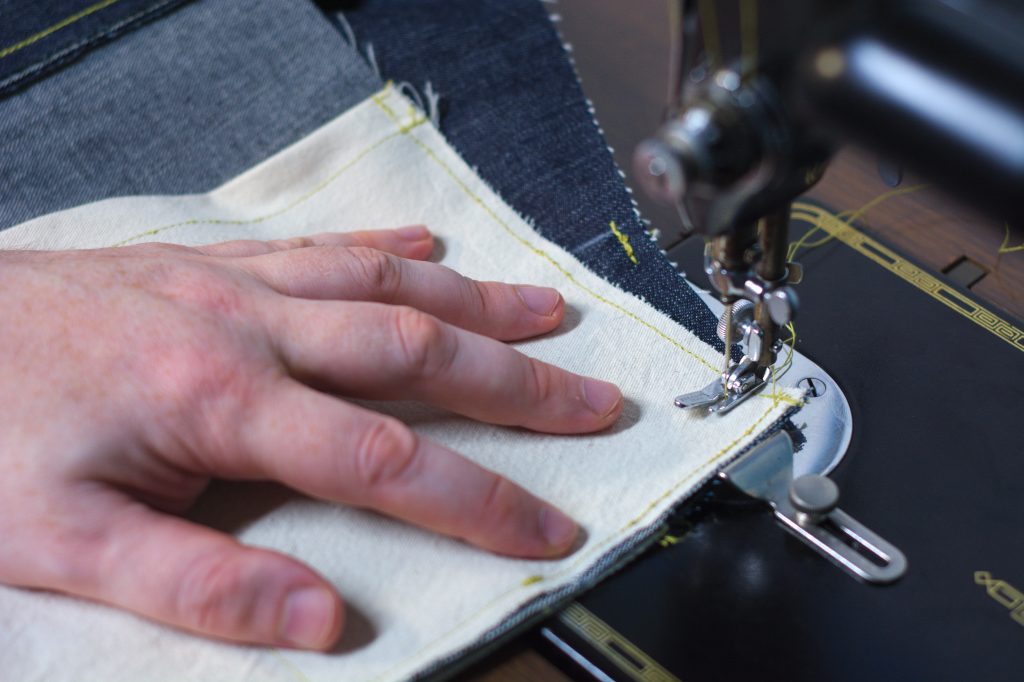
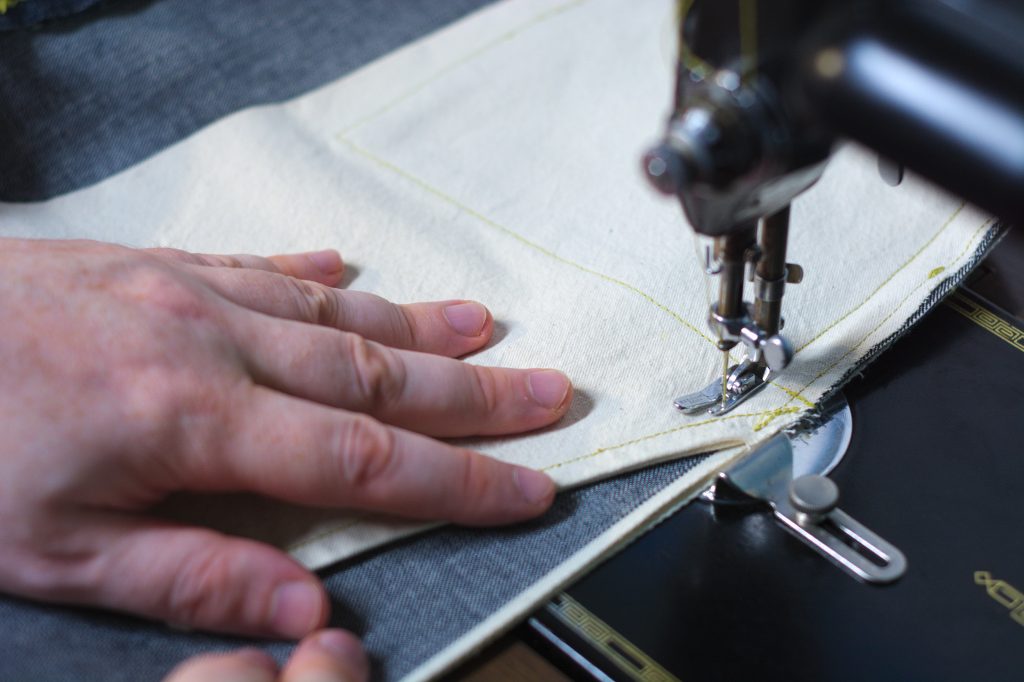
As you’re sewing, be sure that the hip and knee marks are aligned. If not, you’re basically introducing a twist into your legs.
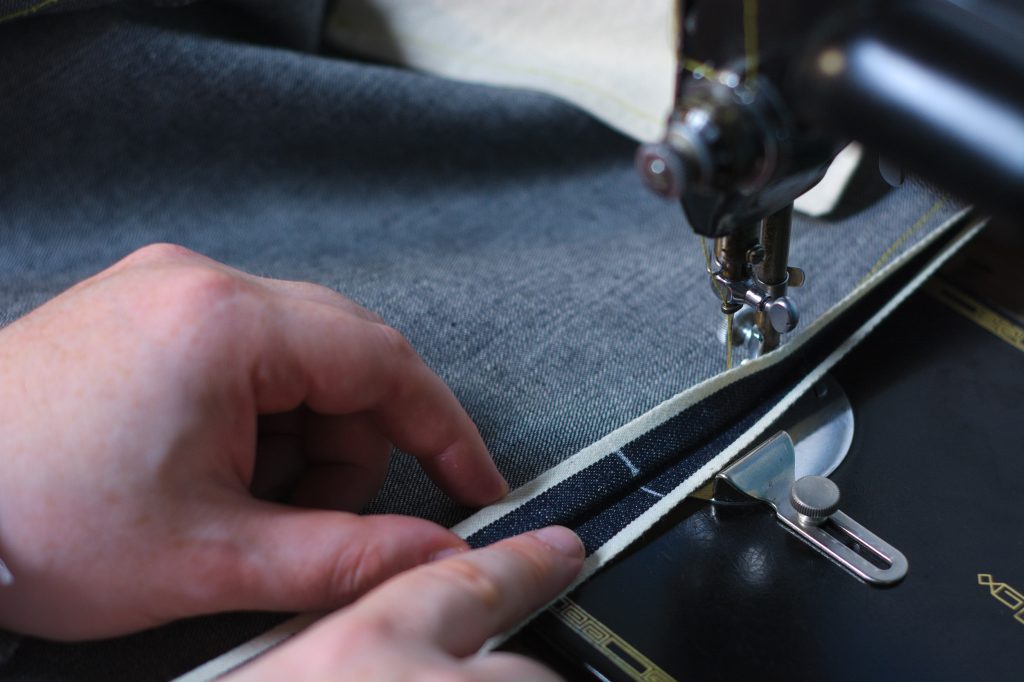
Continue sewing until you reach the hem. Ideally, the hem should match up perfectly with the underside but it’s possible you’ll be slightly off. As long as you’re within 1/4″ I’d say don’t worry about it.

Pocket Covering
This is an optional step to cover up all of the raw edges of the pockets that are left on the side seam. On the 1873 originals, these were just left raw. I’d recommend using a light to medium weight muslin – if you have an industrial machine you can use the pocketing fabric itself like I am. It just introduces a lot of layers that may make your machine struggle.
Begin by cutting a rectangular piece of muslin or pocketing a couple of inches longer than the pocket at the side seam, and about 2 1/2″ wide. Press over about 1/2″ at one of the narrow ends. or you could use the selvedge instead, something I prefer to do.
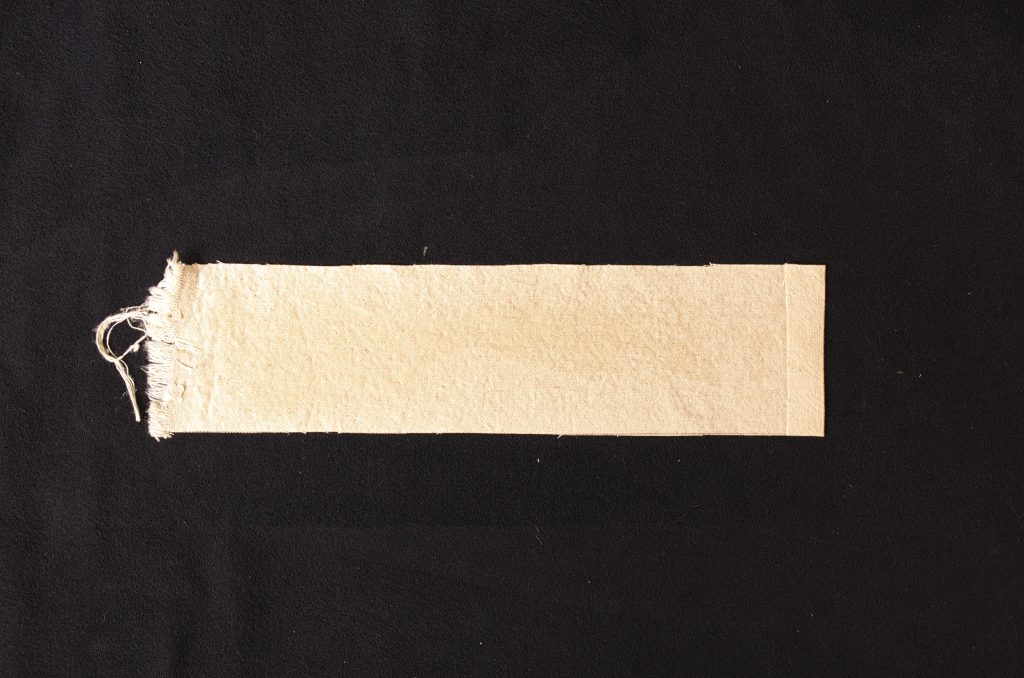
Now along one long edge, press over about a 3/8″ seam.
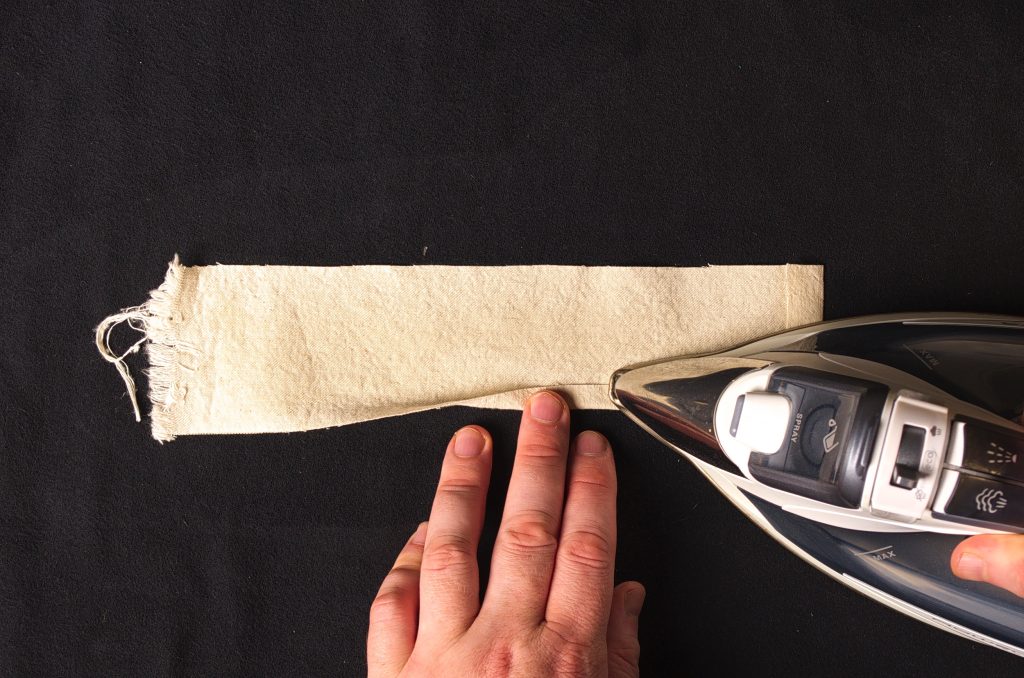
Now open up the muslin along the long seam and lay the it onto the pocket just inside the side seam’s seam allowance, so that the folded narrow end is just meeting the pocket on that curved seam. Keep the long fold about 1/8″ away from the side seam.
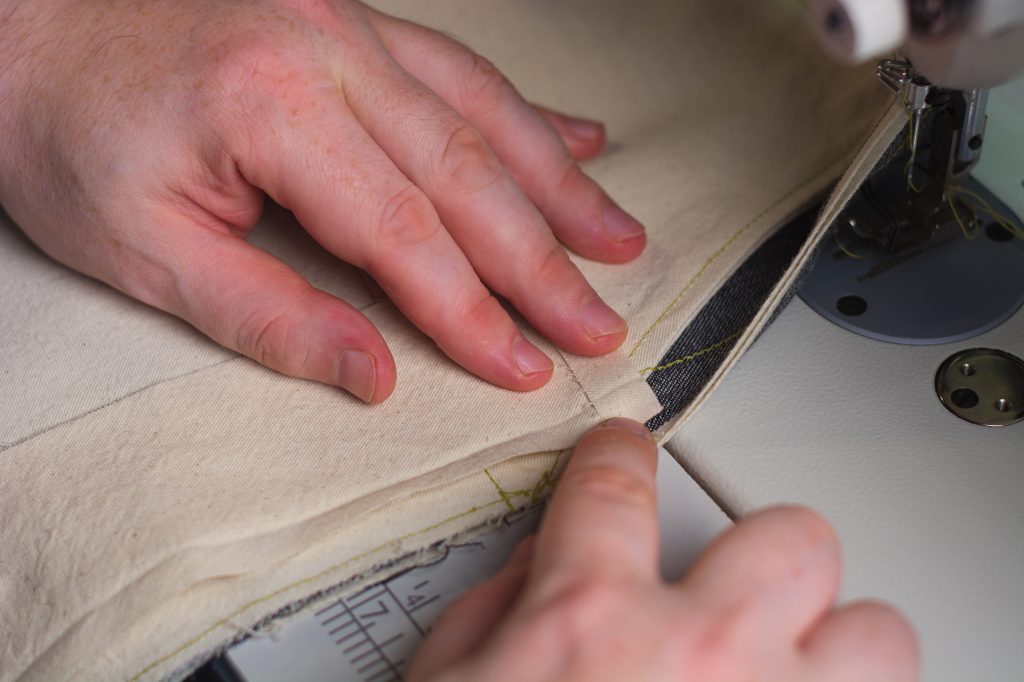
Begin sewing along the long folded edge, lifting the muslin as necessary to make sure you’re still in alignment.
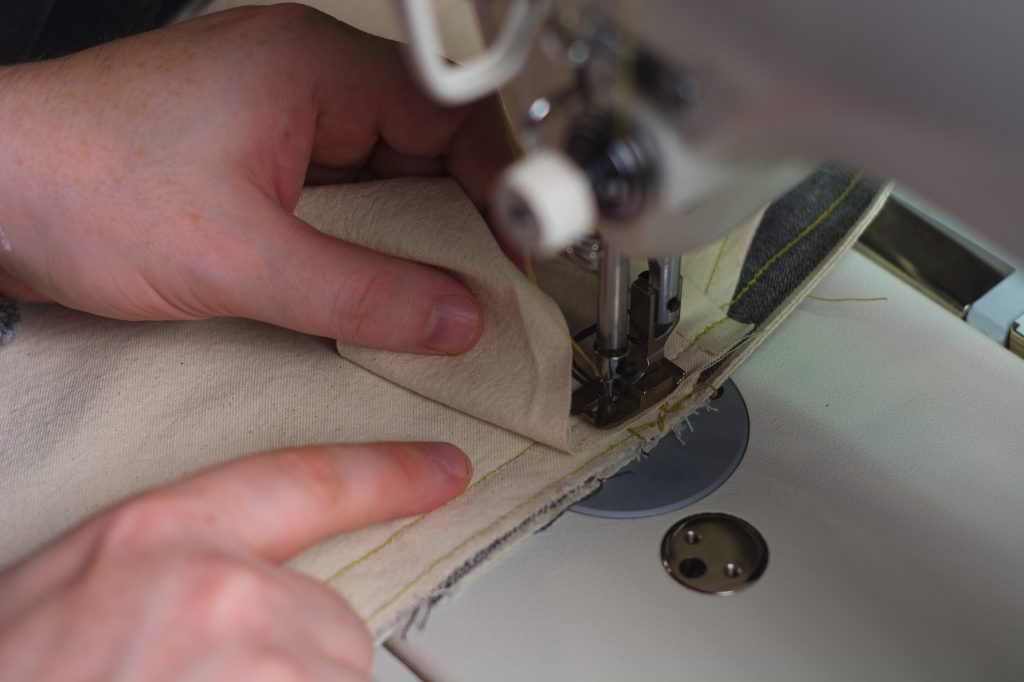
Continue sewing to the waist seam.
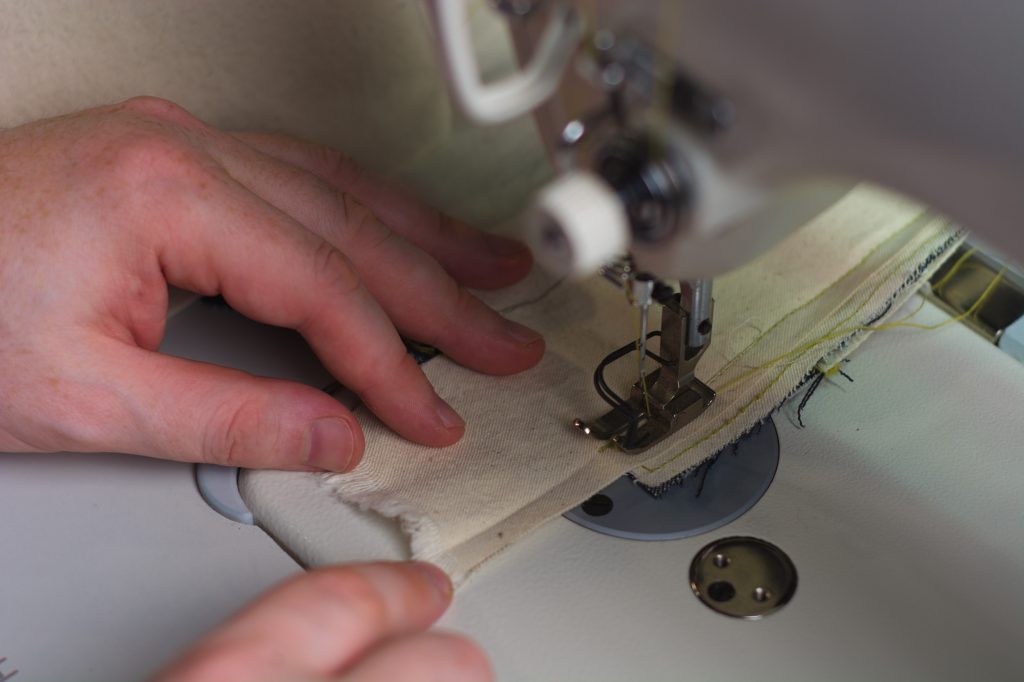
Press the muslin firmly towards the selvedge.
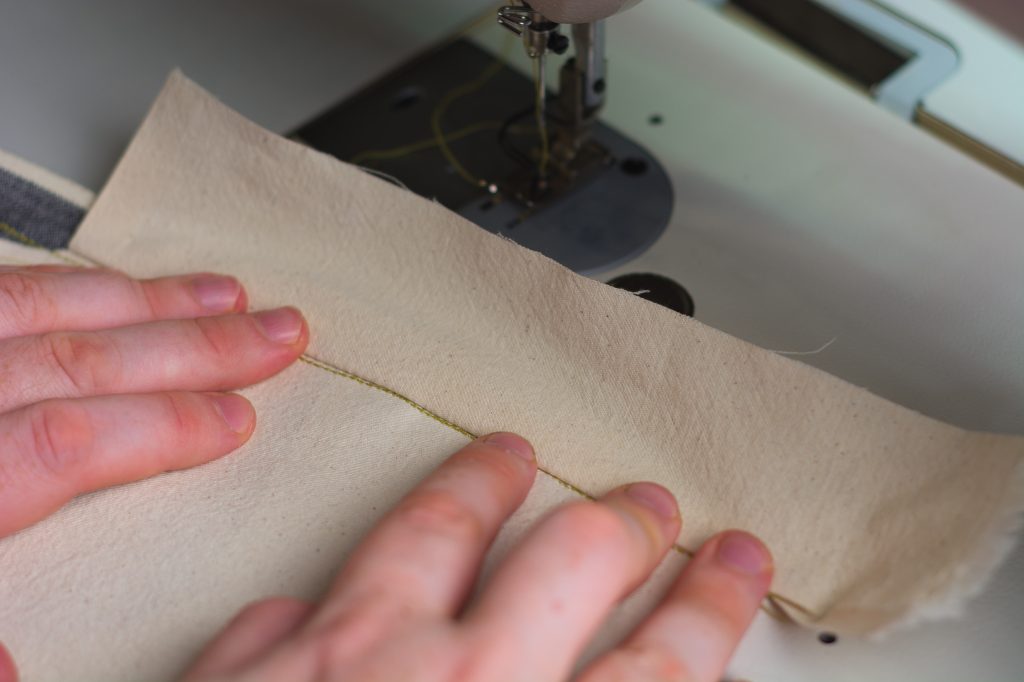
And wrap it around the selvedge to the back side of the jeans.

Here’s the view from the back leg side of the jeans (that’s the yoke near my left hand).
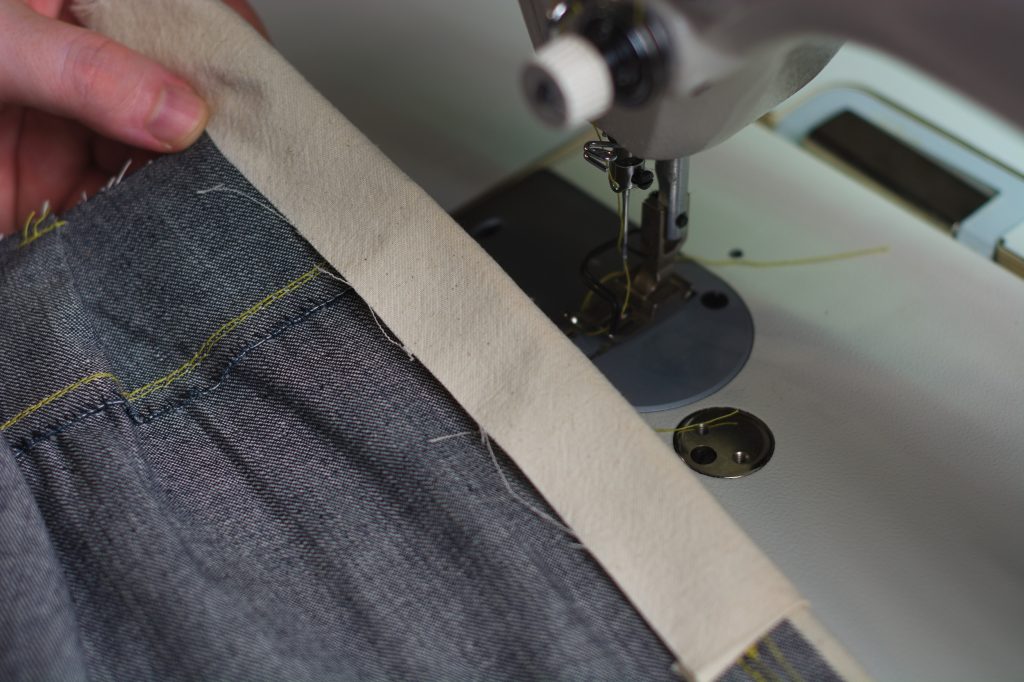
Turn under the remaining long raw edge, again positioning the fold about 1/8″ from the sewn seam underneath.
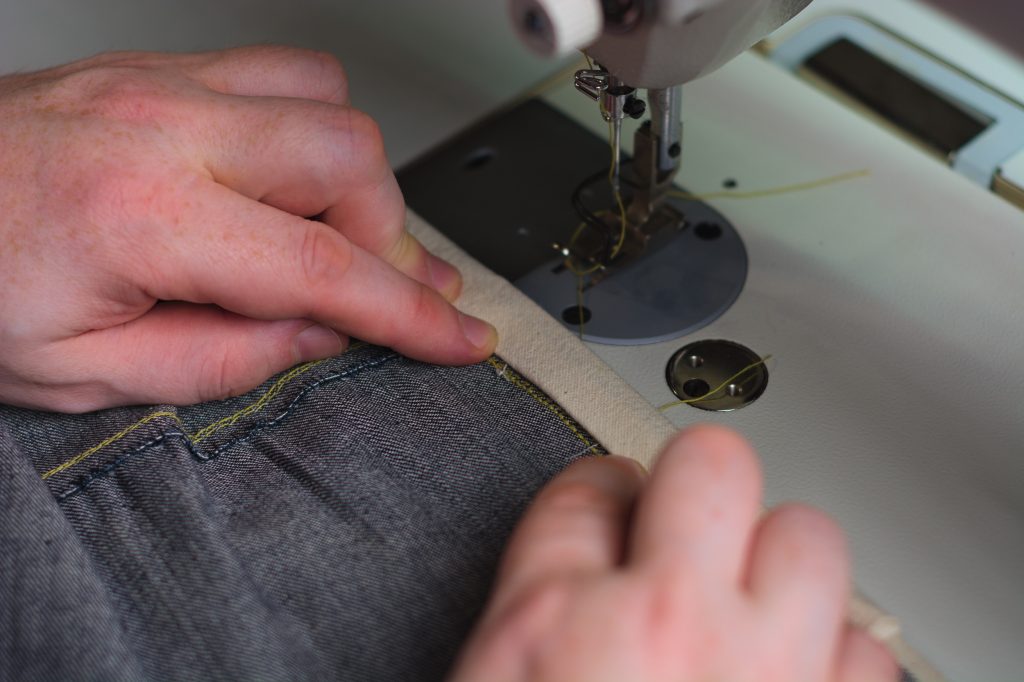
You can press this to keep everything in place a little more easily.
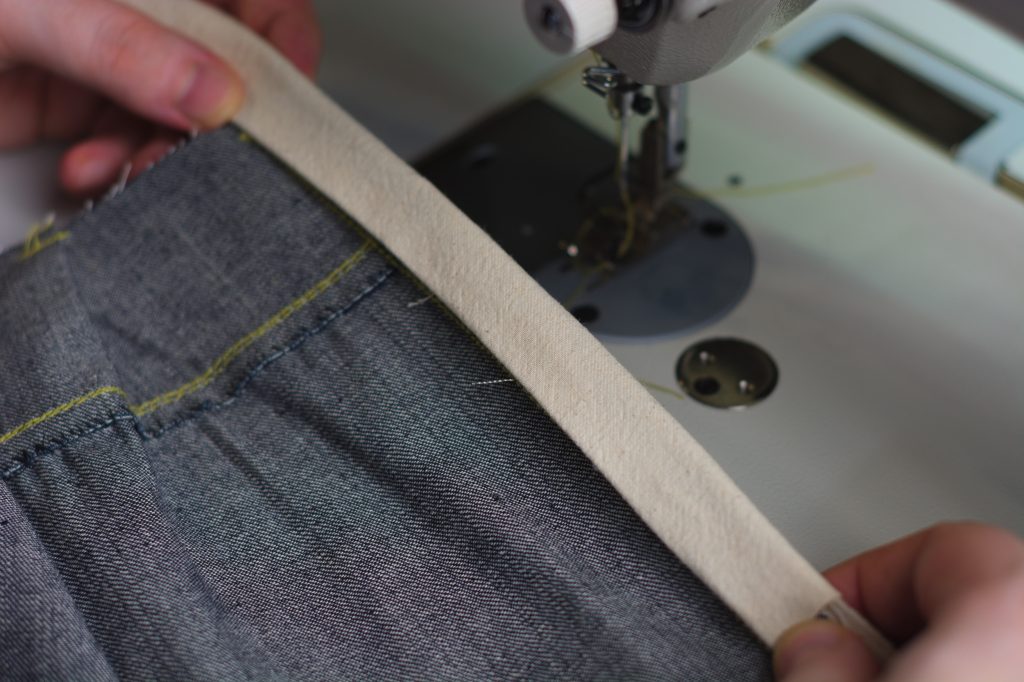
Now sew the pocket covering closed about 1/8″ from the folded edge along the length of the muslin.

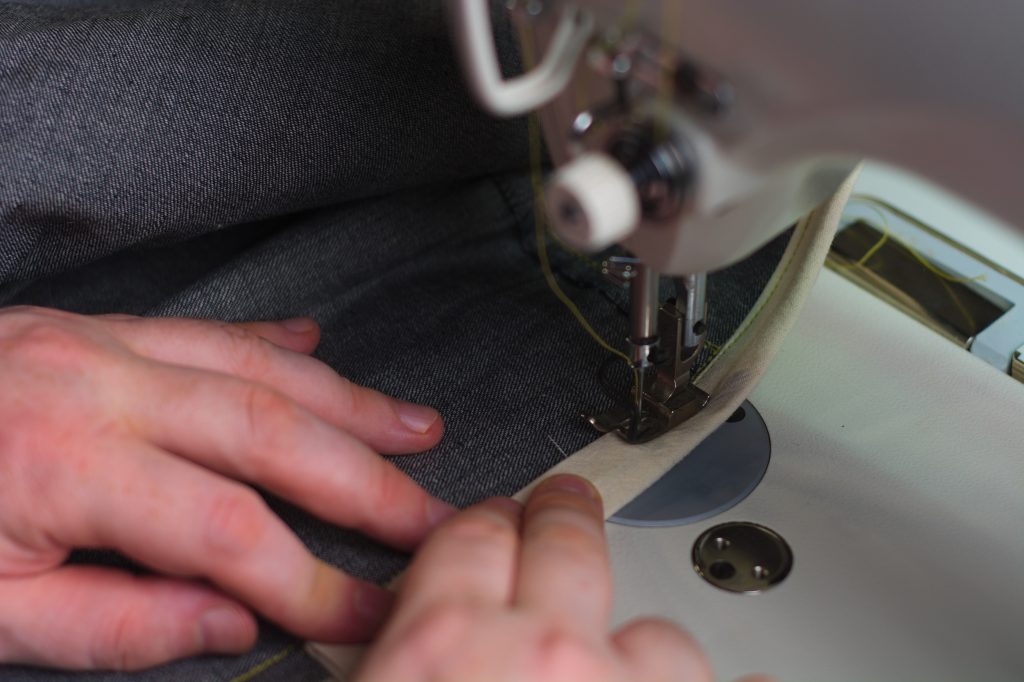
Here’s what it should look like. It’s just a very clean way of finishing the pocket’s raw edges.
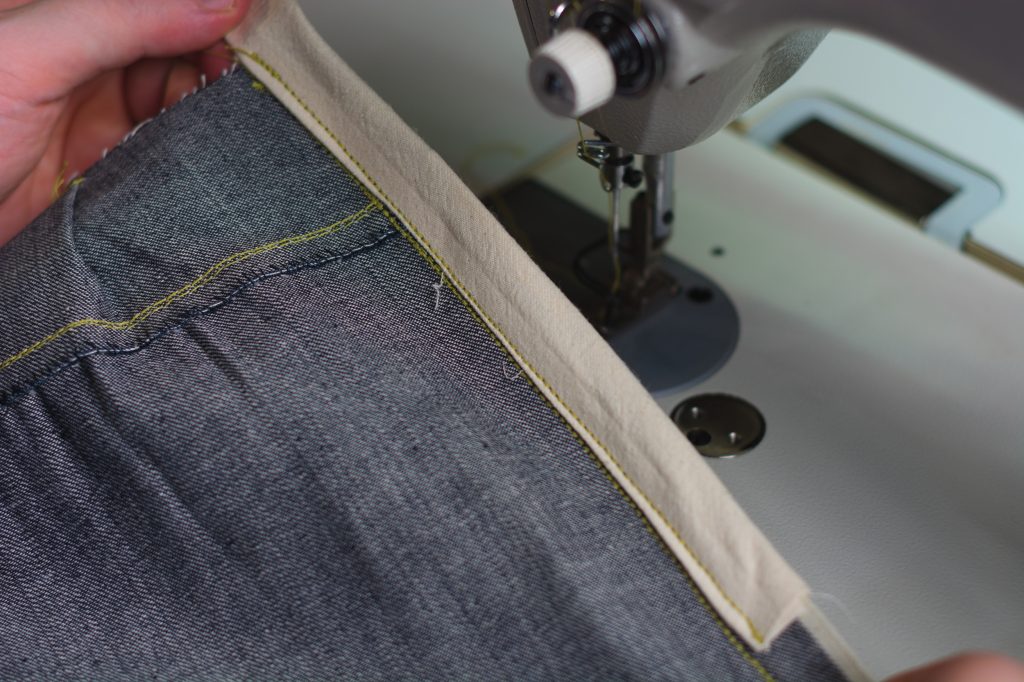
Pressing
Turning out attention back to the side seam, press the side seam open from the hem to a couple of inches below the pocket.
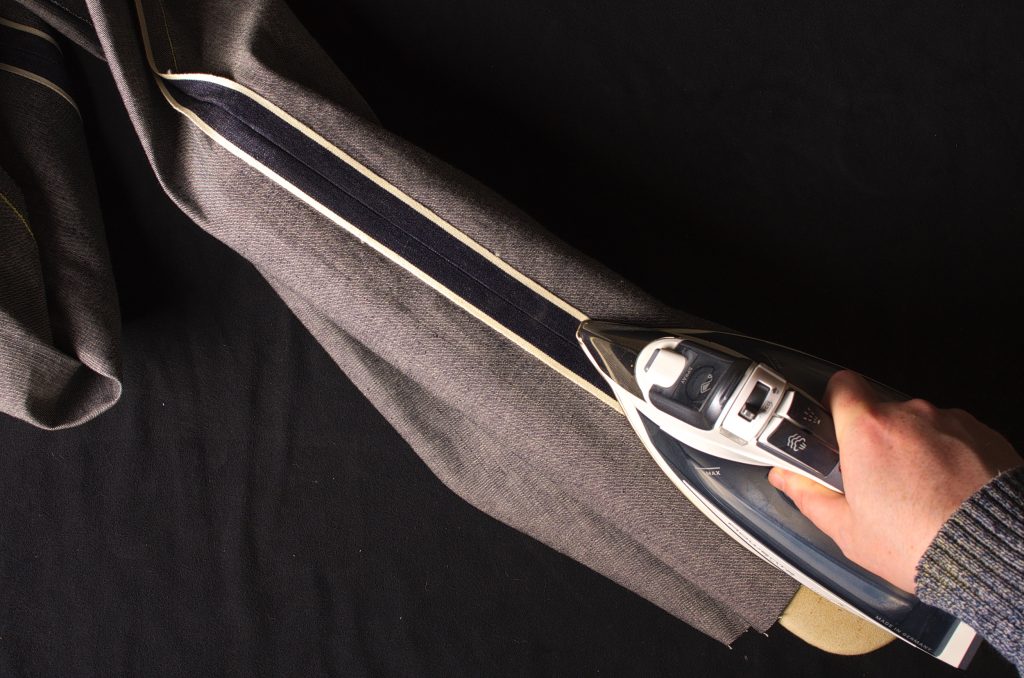
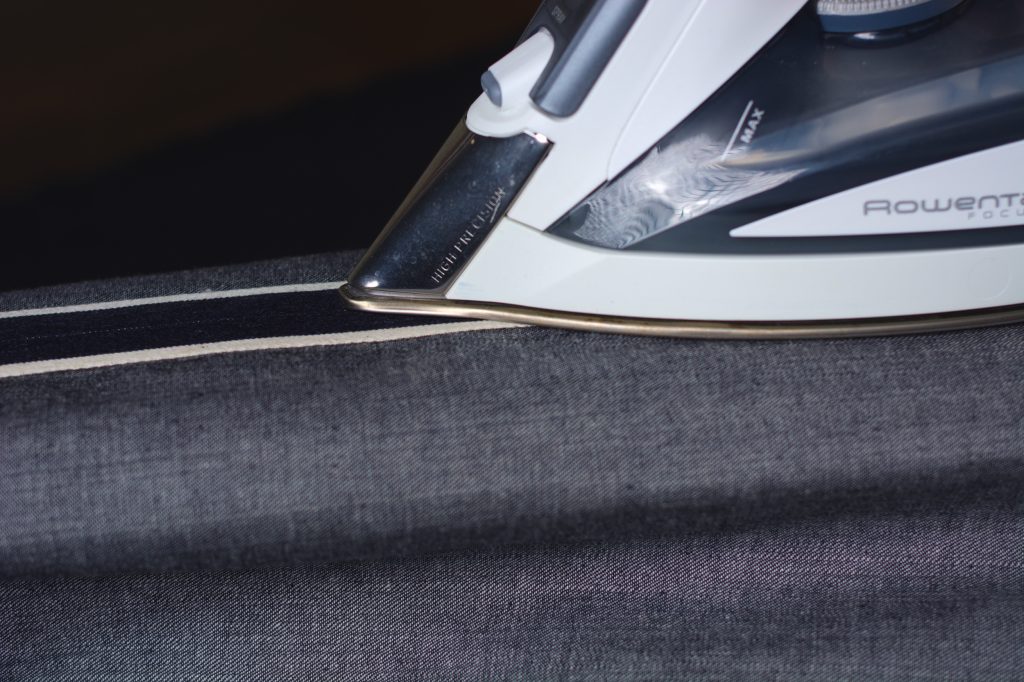
At the pocket area, press the pocket and covering towards the back, as firmly as you can. Then press the front side seam at a diagonal so that it can open up fully again.
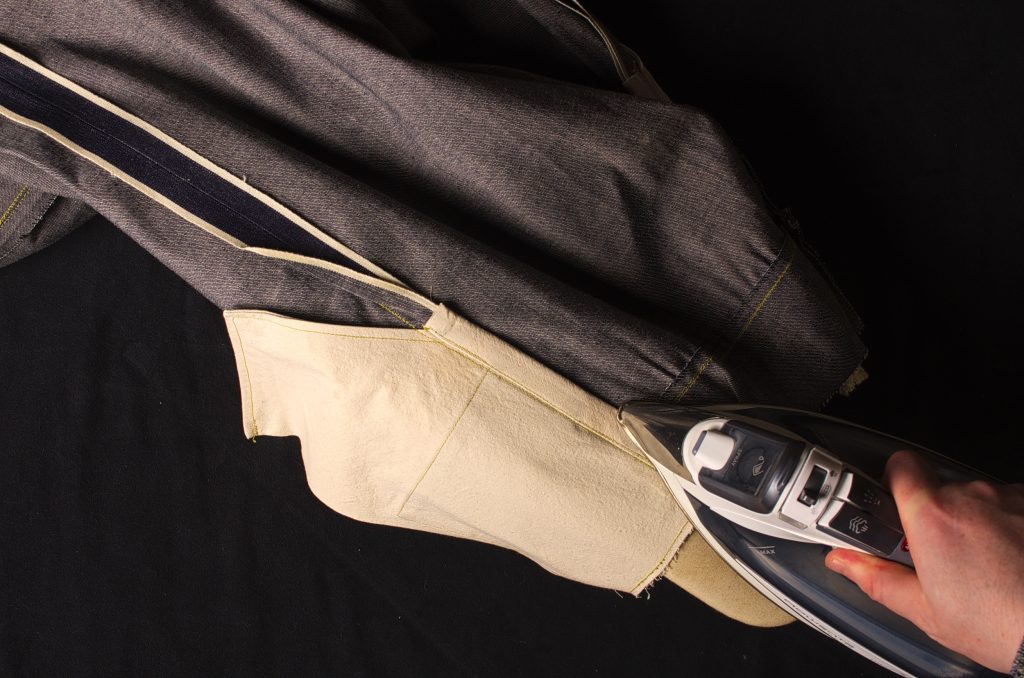

There are a lot of layers here so I like to press the pocket area very firmly.
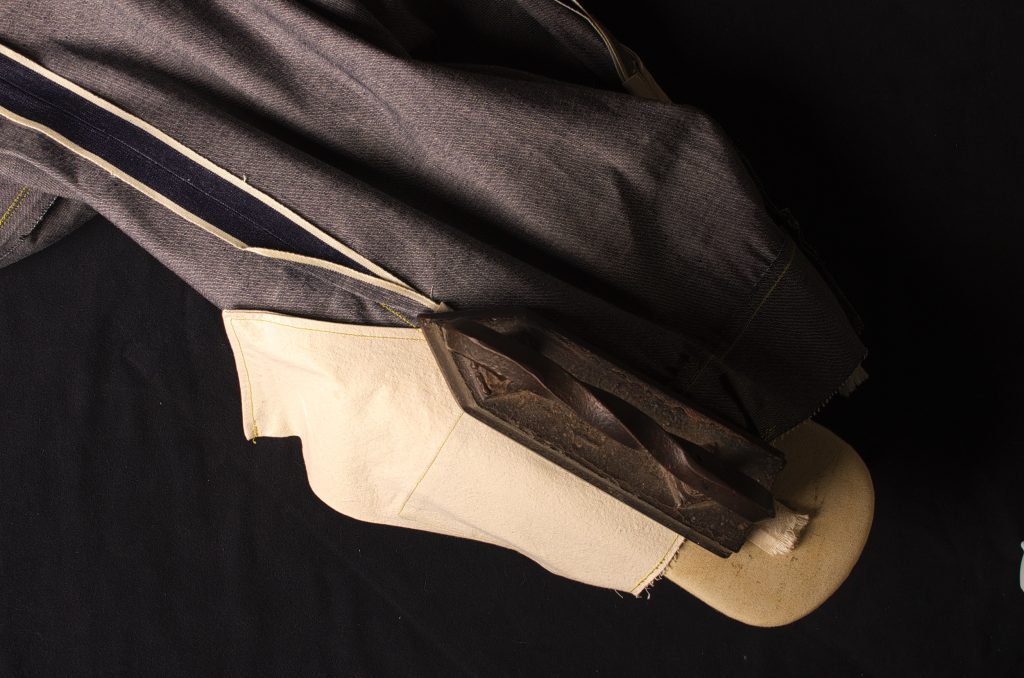
Turn the jeans right sides out and press the side seam and pocket area again as necessary.
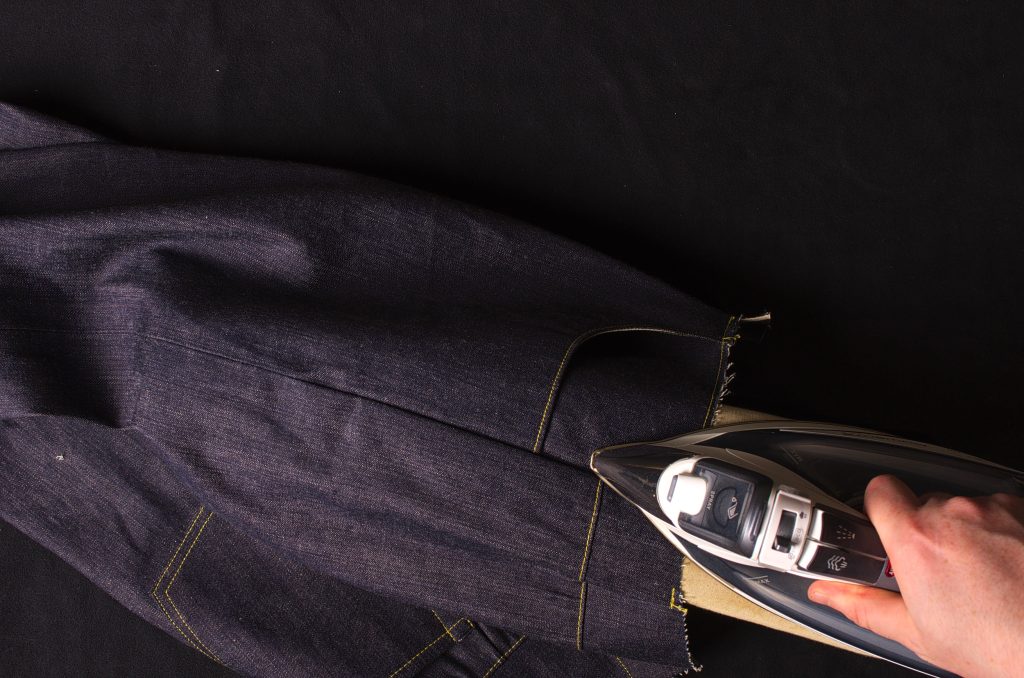
Top Stitching
From the right side, feel for the bottom of the pocket covering and mark along the side seam about 1/4″ below that. Repeat for the other leg, ensuring both marks are positioned identically.
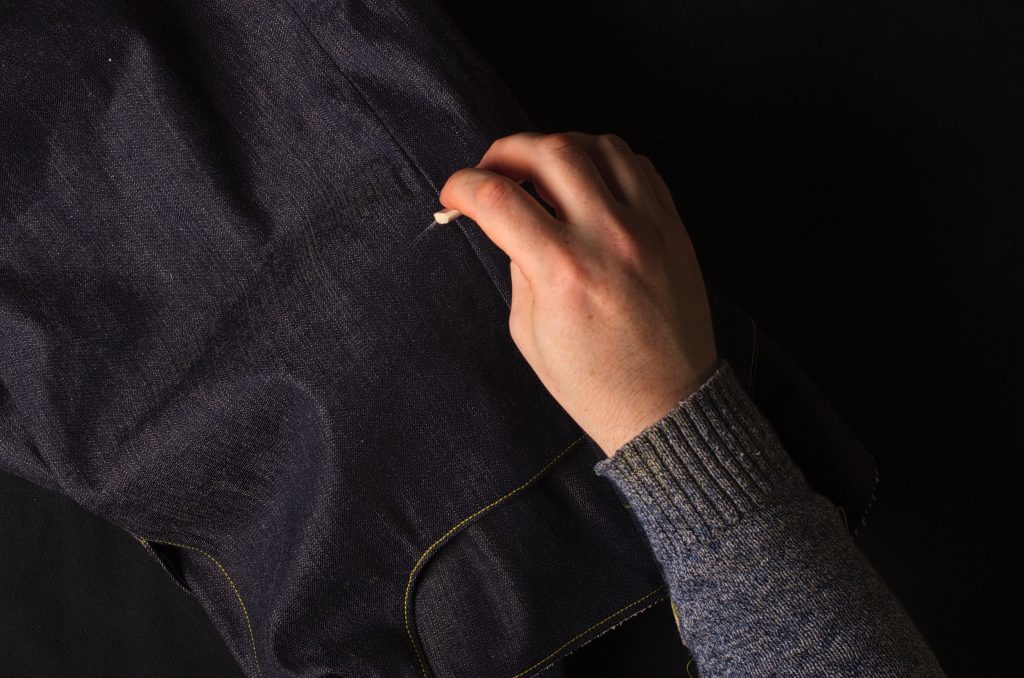
Couldn’t make up my mind here . . .
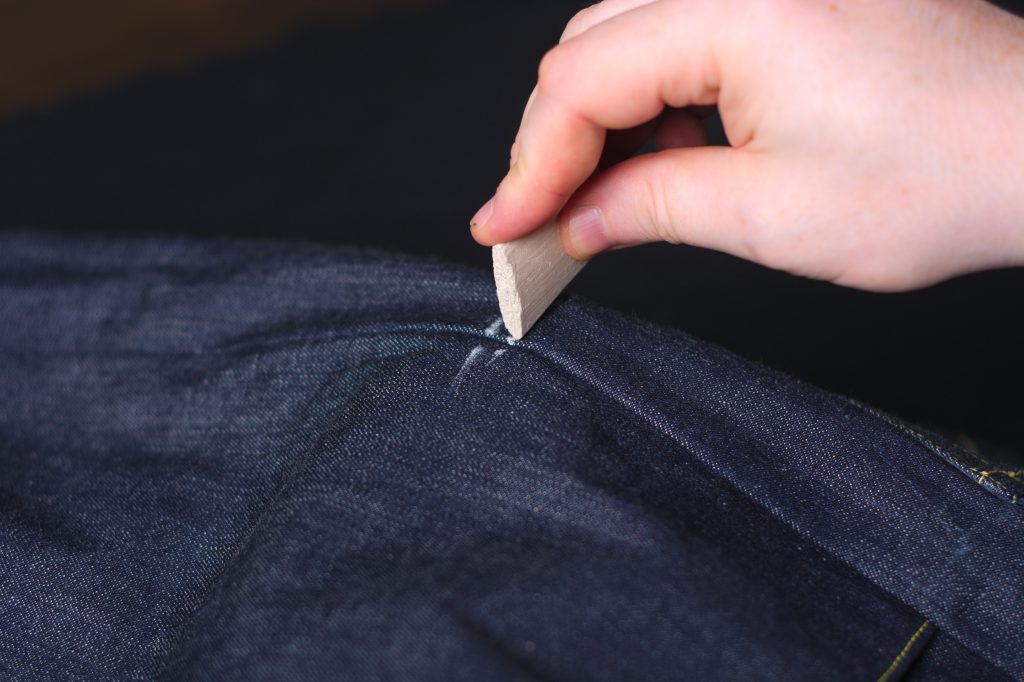
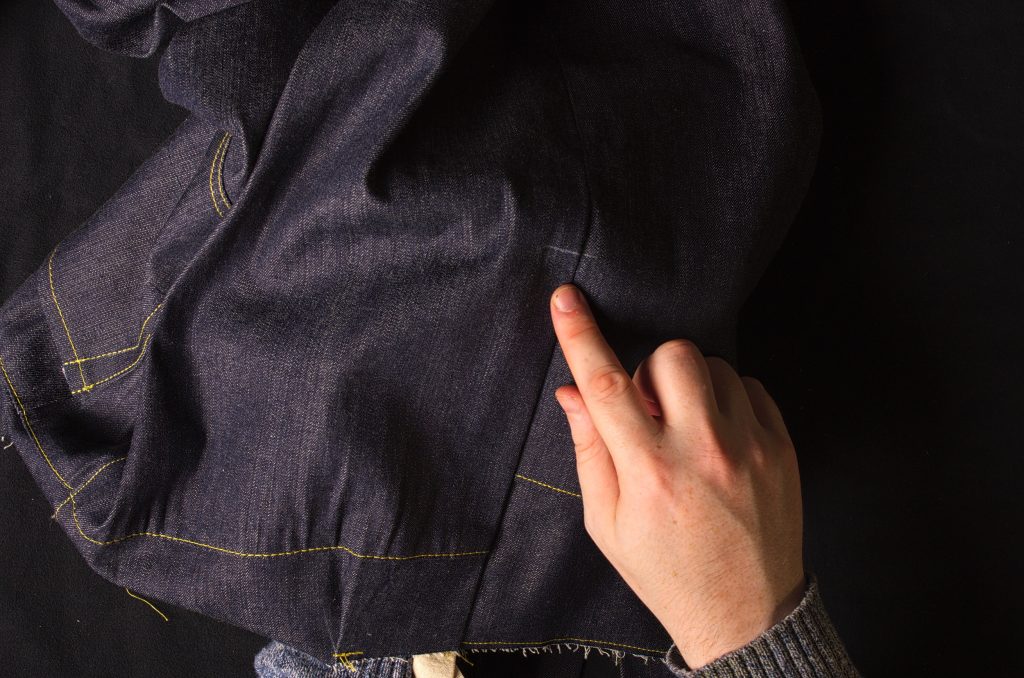
Beginning at the waist, top stitch the side seam through all layers of the pocket / seam allowance / muslin covering to the mark. Space the top stitching about 1/8″ from the seam towards the back leg.
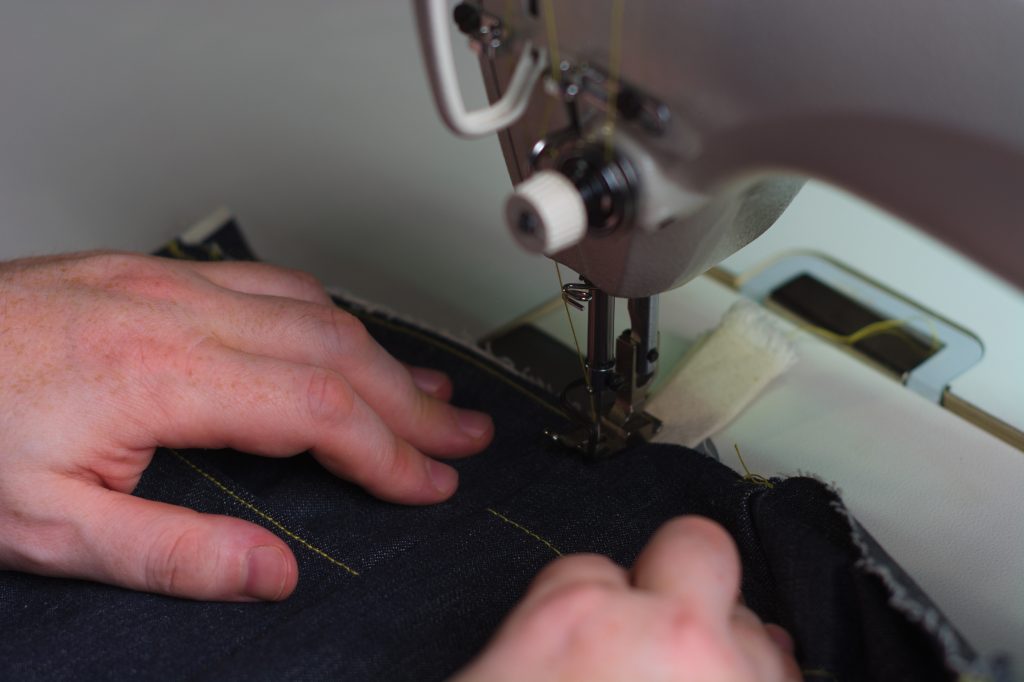
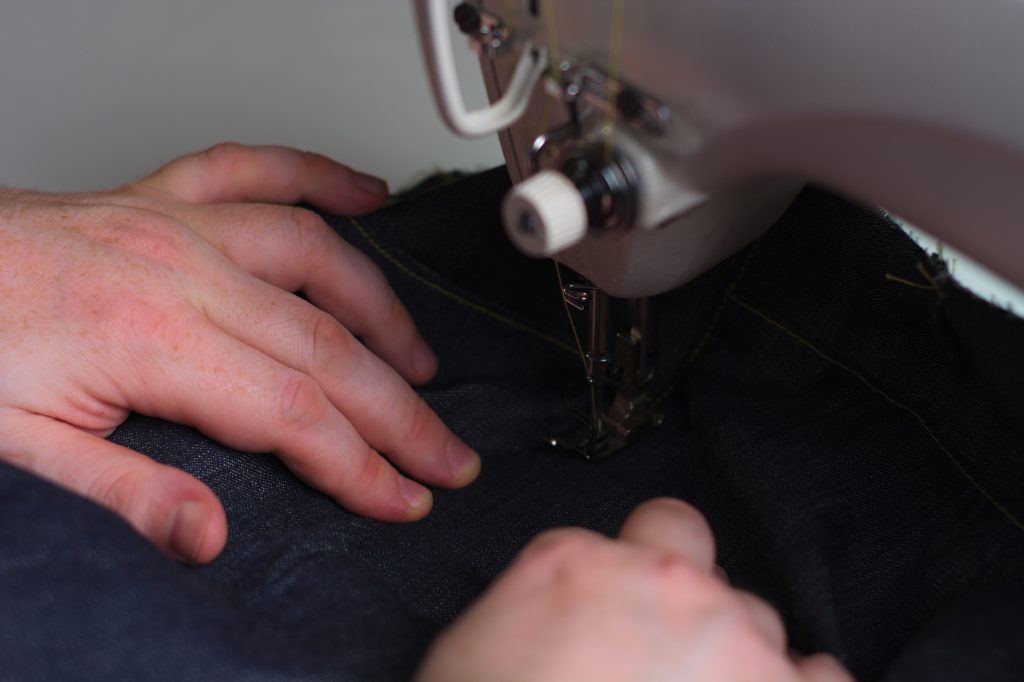
Sorry the pictures are hard to see! It’s kind of tricky to sew here, be sure to keep the underside clear of any other parts of the jeans as you sew.
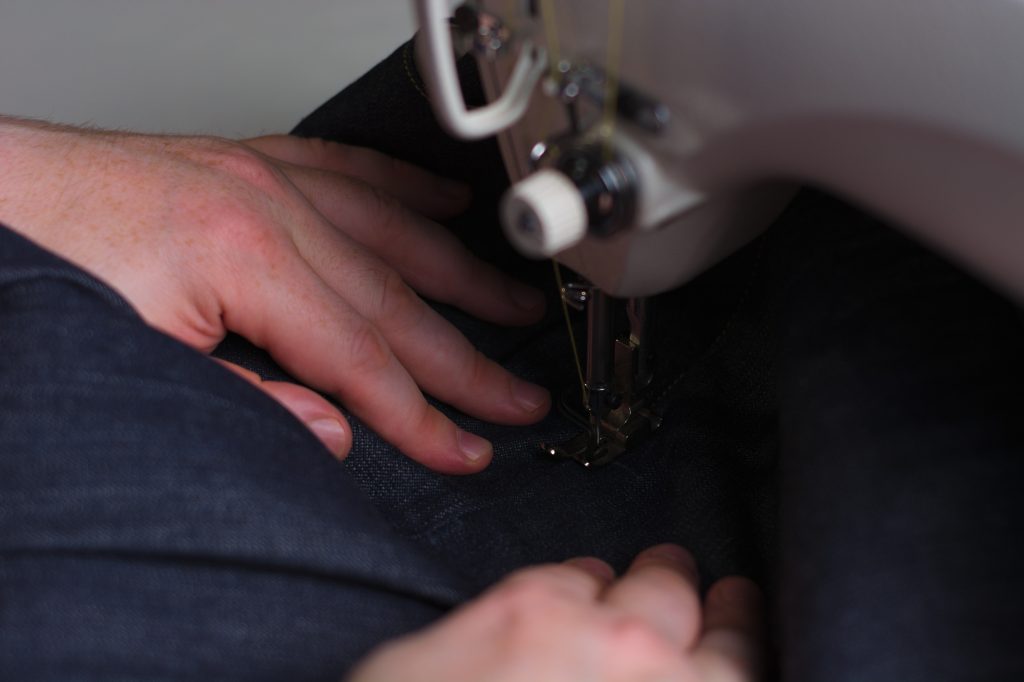
Here are the jeans after top stitching the side seam. The top stitching ends just below the pocket because it’s basically impossible to sew much further due to the closed legs.
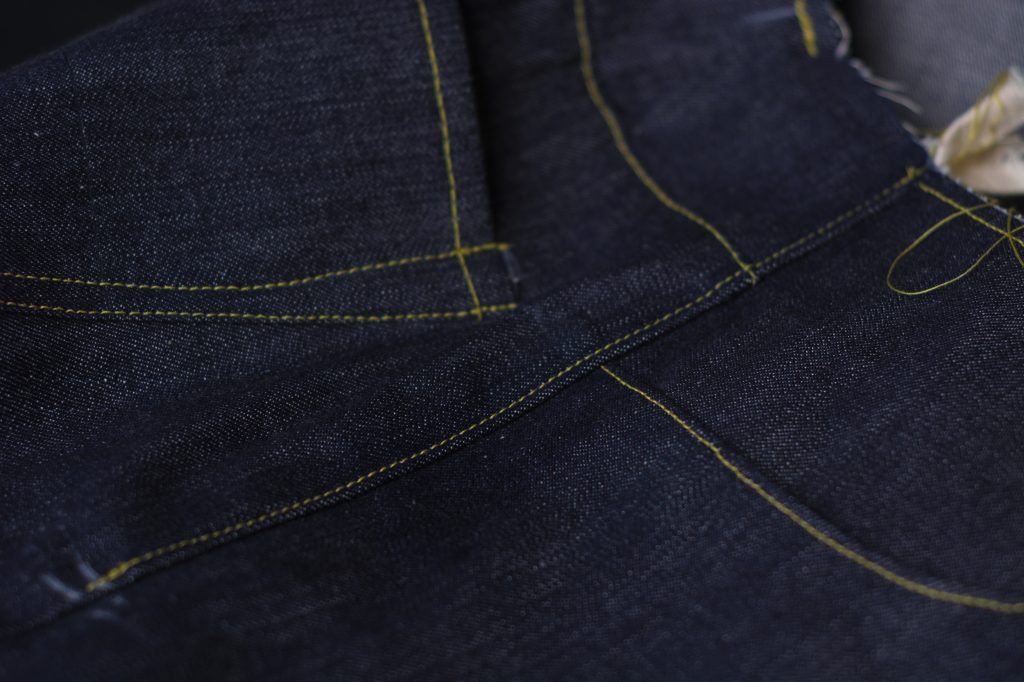
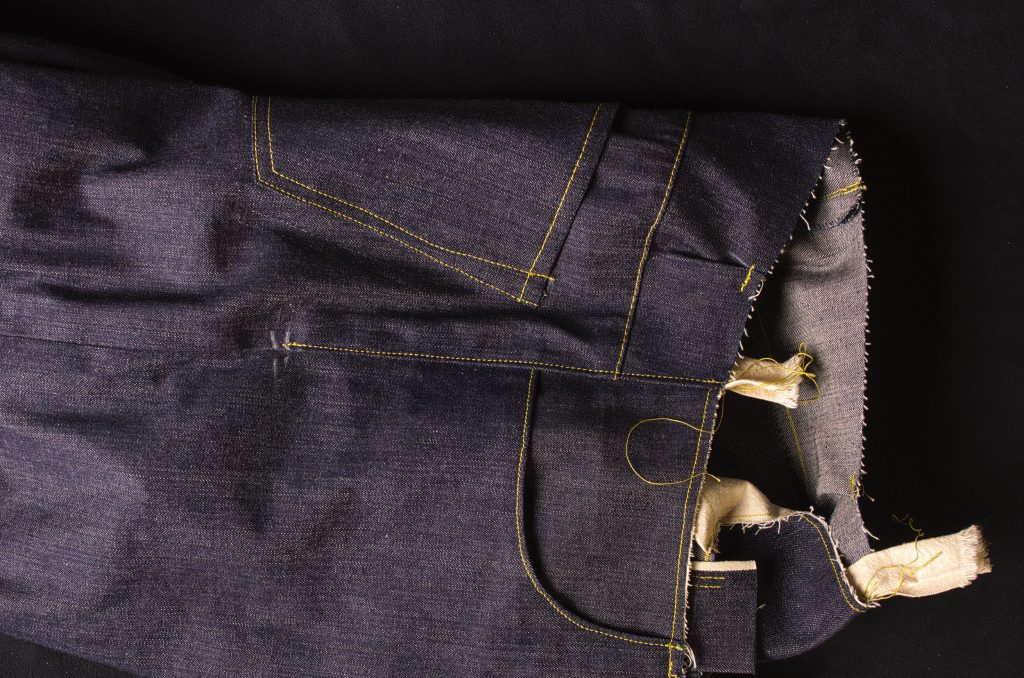
Finally, I like to trim any excess from the top of the fly.
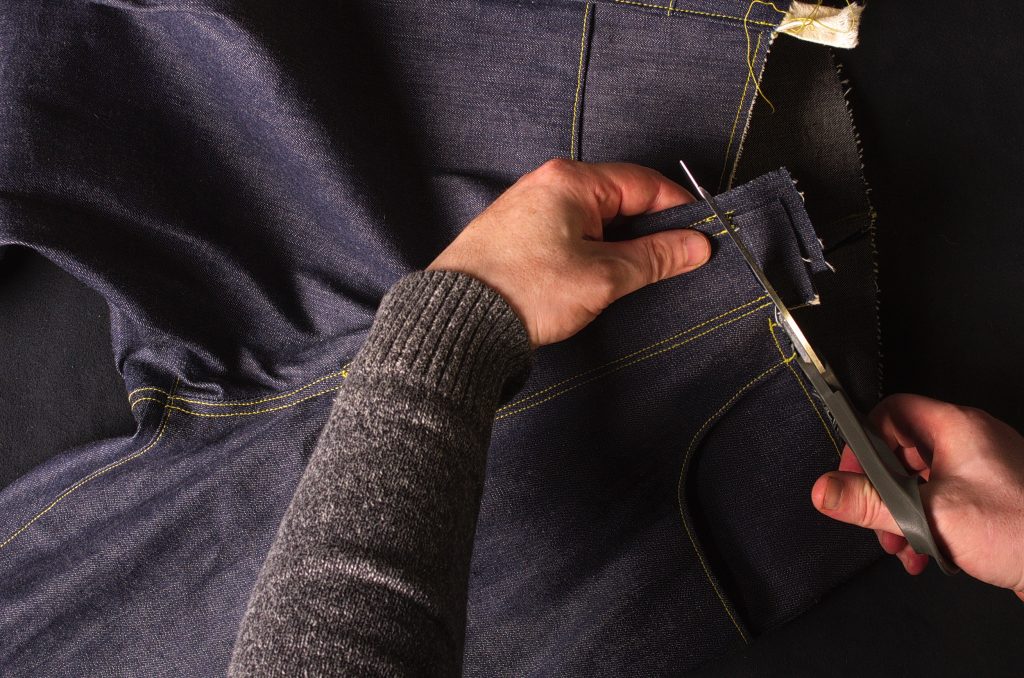
And then trim the tops of the pocket coverings flush with the waist as well.
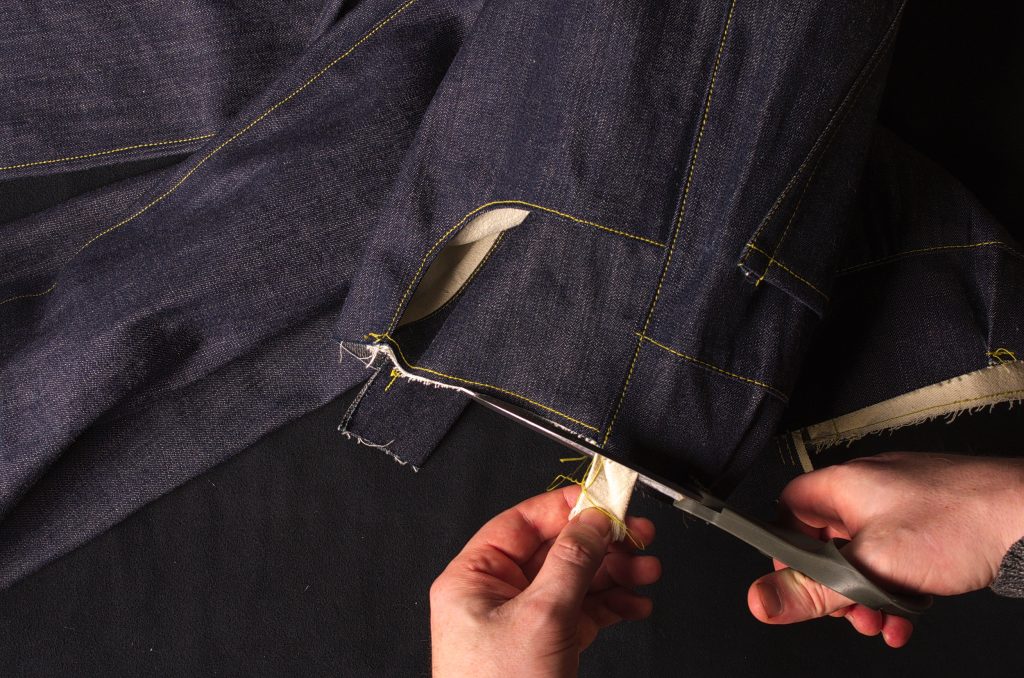
The Inseam
Now that both the front and back legs are complete, we can finally begin joining them together.
If you haven’t already done so, trim the back and front crotch so that there is more of a smooth transition between the two legs.
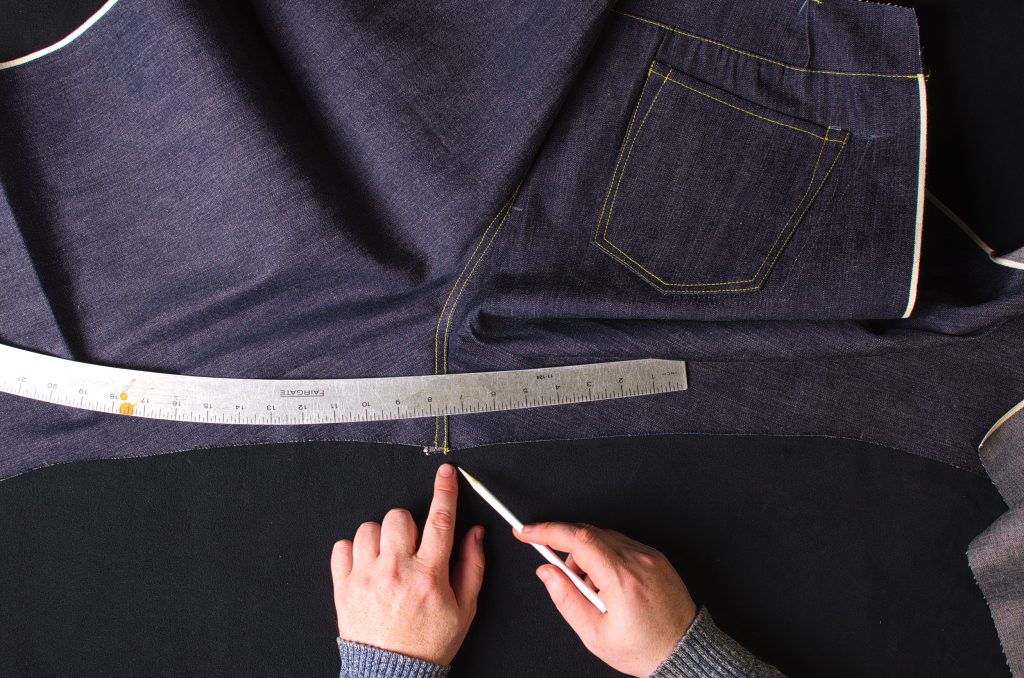
I used my hip curve just to smooth out the crotch by about 3/16″. It really does make a big difference with the ease in which things go together.
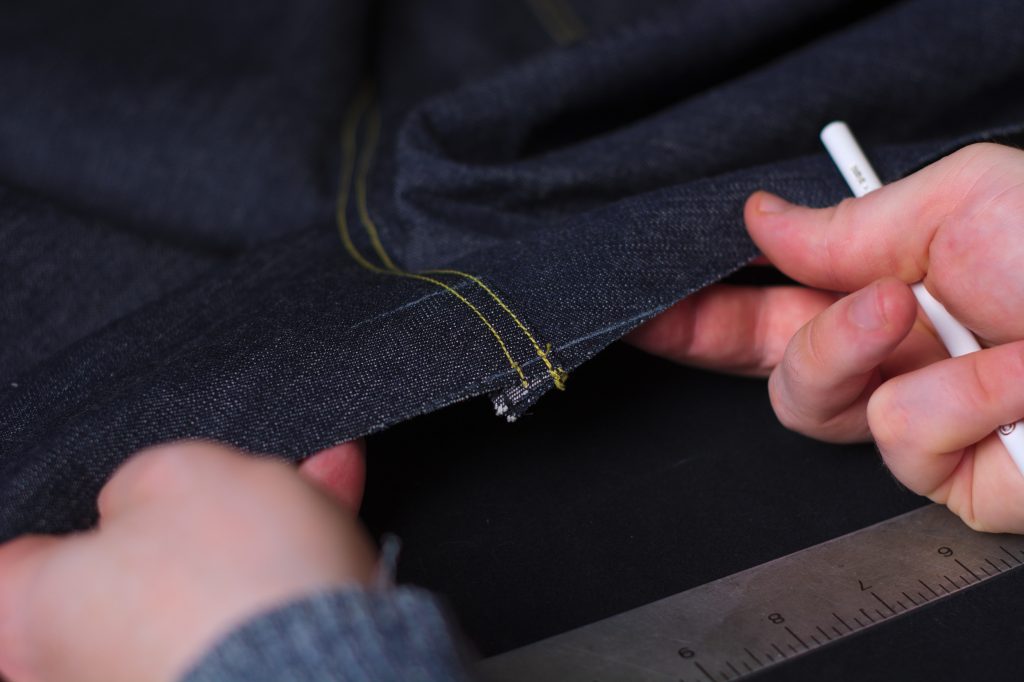
Be sure to overcast the cut area again to prevent fraying.
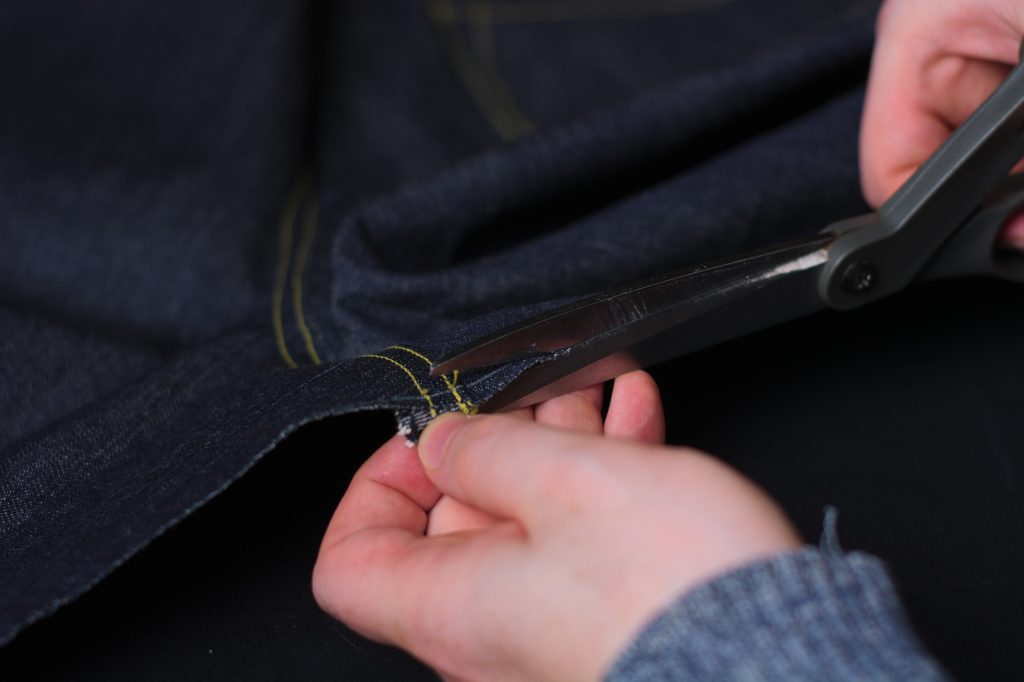
Mark a 3/8″ seam allowance on the back inseam, from hem, through the crotch, to the other hem.
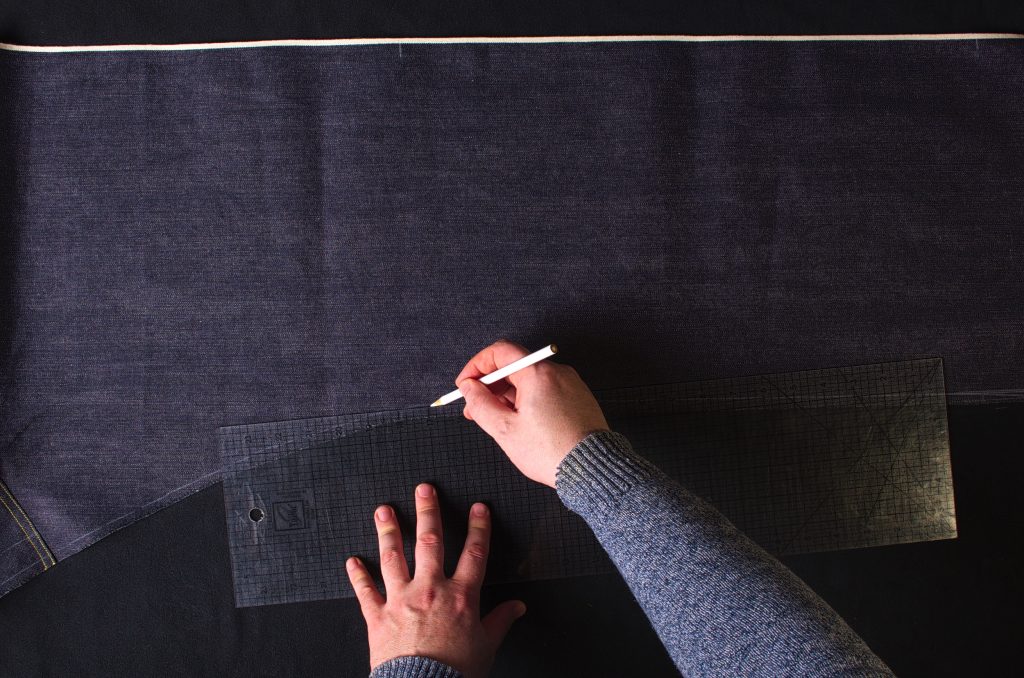
Lay the front legs on top of the back legs, right sides together. Align the edge of the front inseam with the line you just marked, just barely covering the line.
Pin the inseam together at the knee mark, hem, and crotch area. Then pin in between these points as necessary.
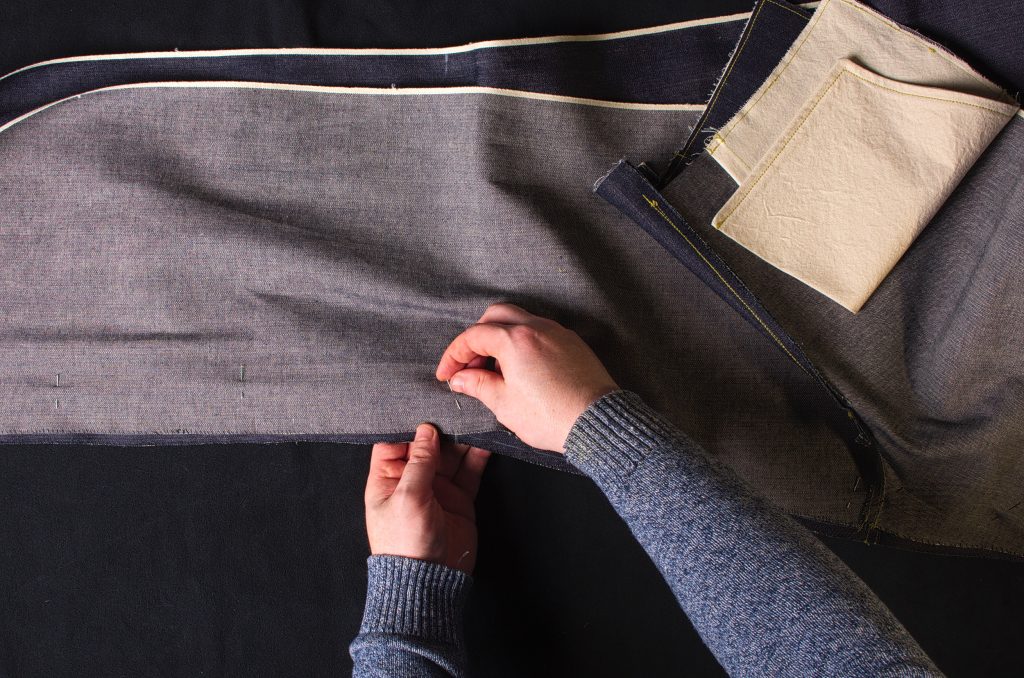
As you’re pinning between the knee and the crotch, you may notice some excess in the front leg. If you gently stretch the back leg with your hands, you can pin away this excess.
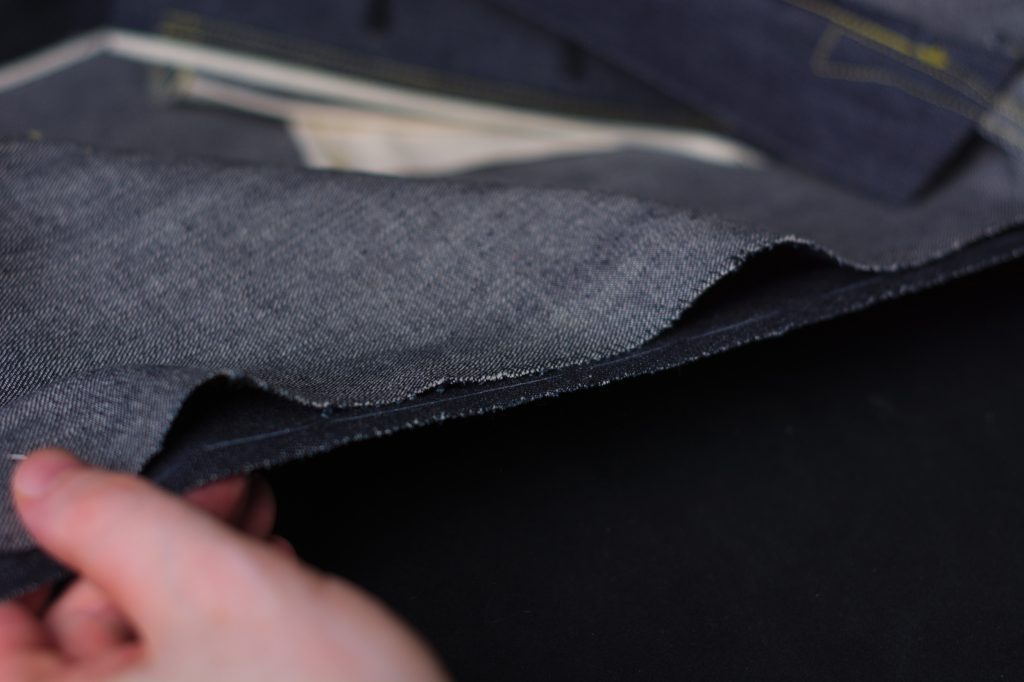
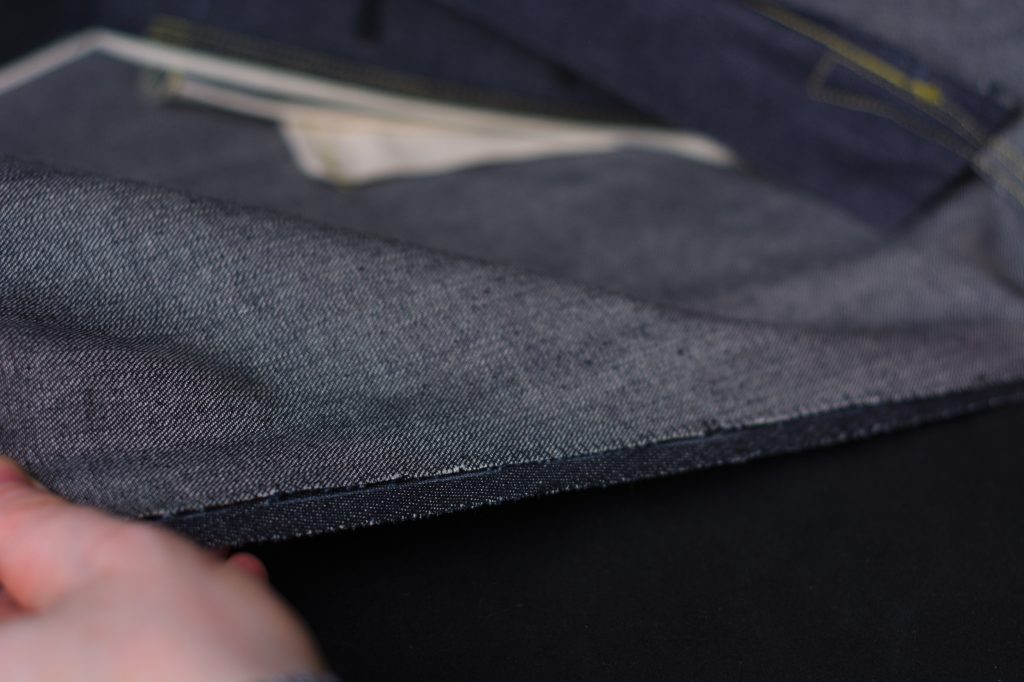
Here’s what your jeans should look like after pinning the inseam together.
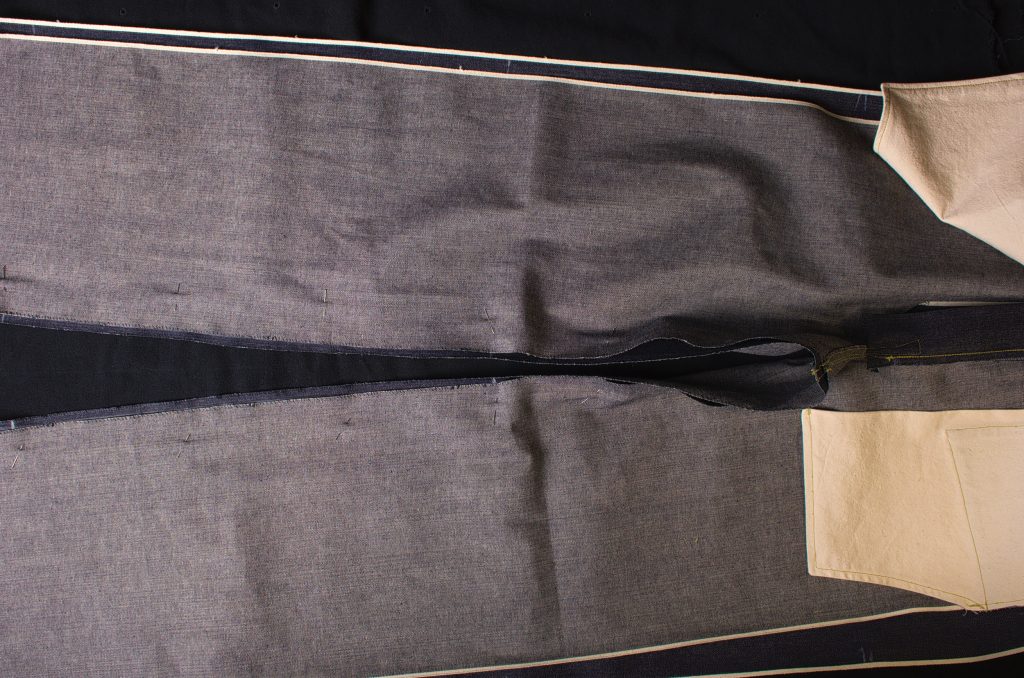
Sew from hem through the crotch to the hem along the inseam, using a 3/4″ seam allowance. You’ll be 3/4″ away from the edge of the back legs, and 3/8″ away from the front inseam.
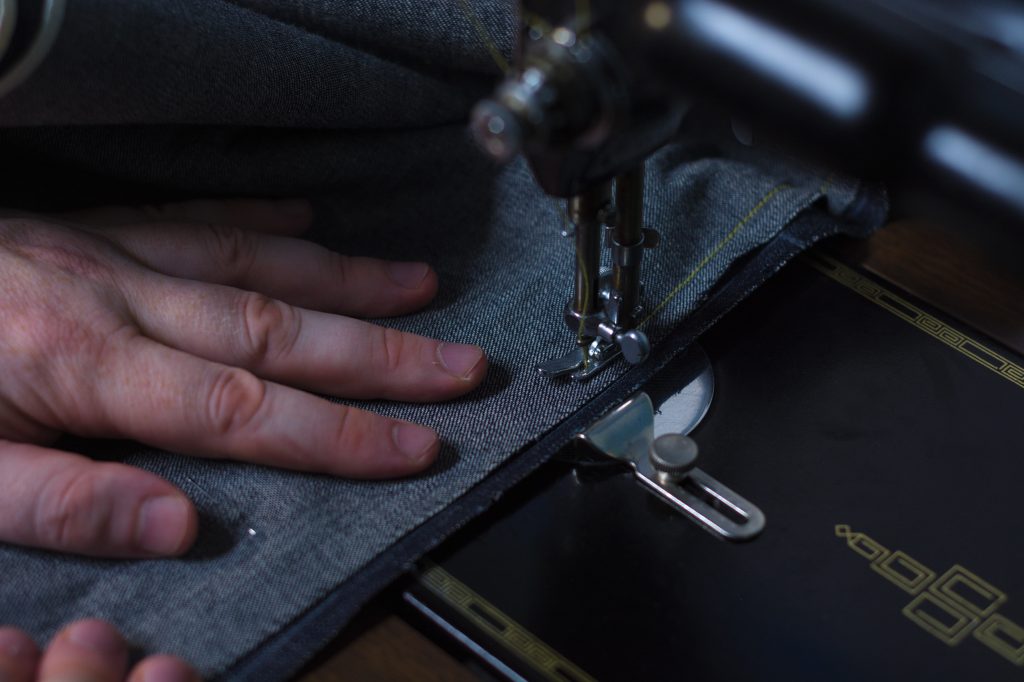
Here’s the inseam after sewing. There are two ways to finish the inseam, shown in the next section below.
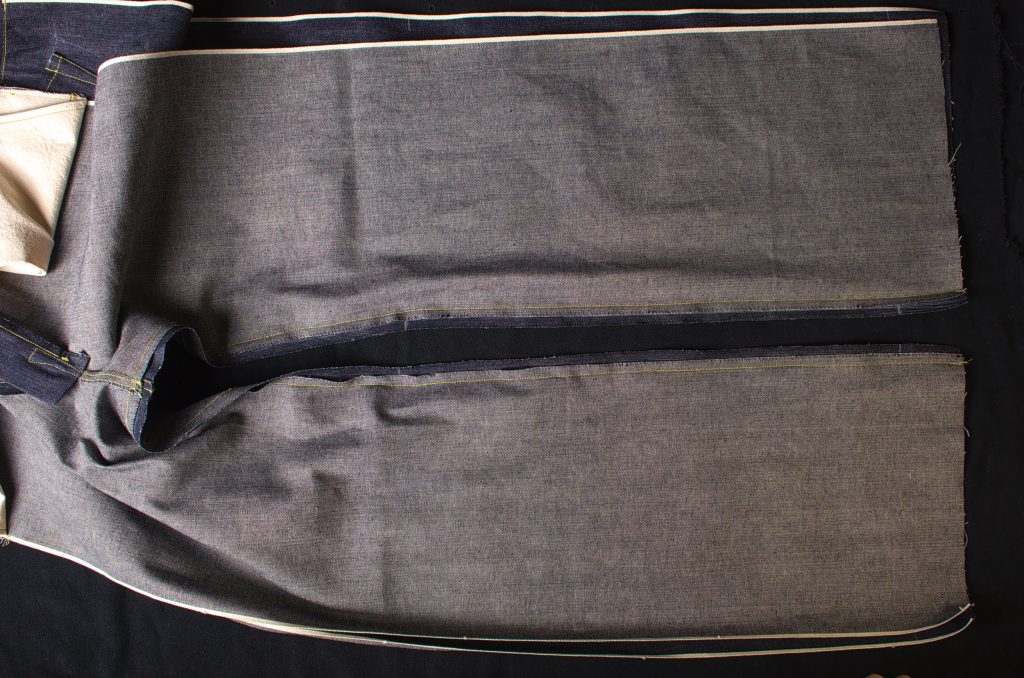
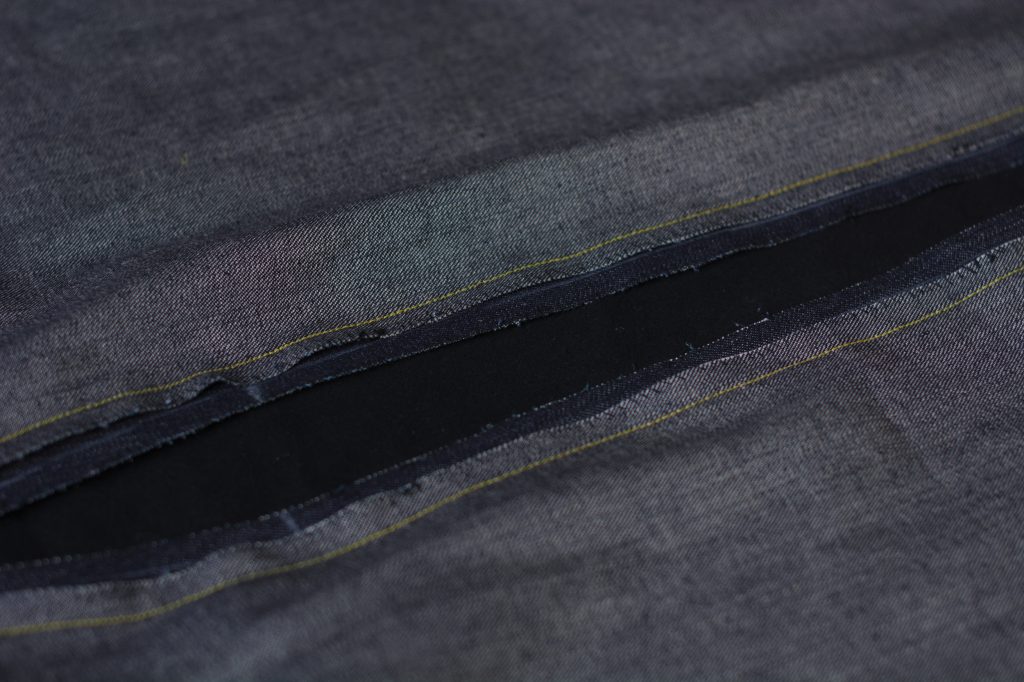
Hopefully your crotch seams line up properly – mine shifted slightly out of position.
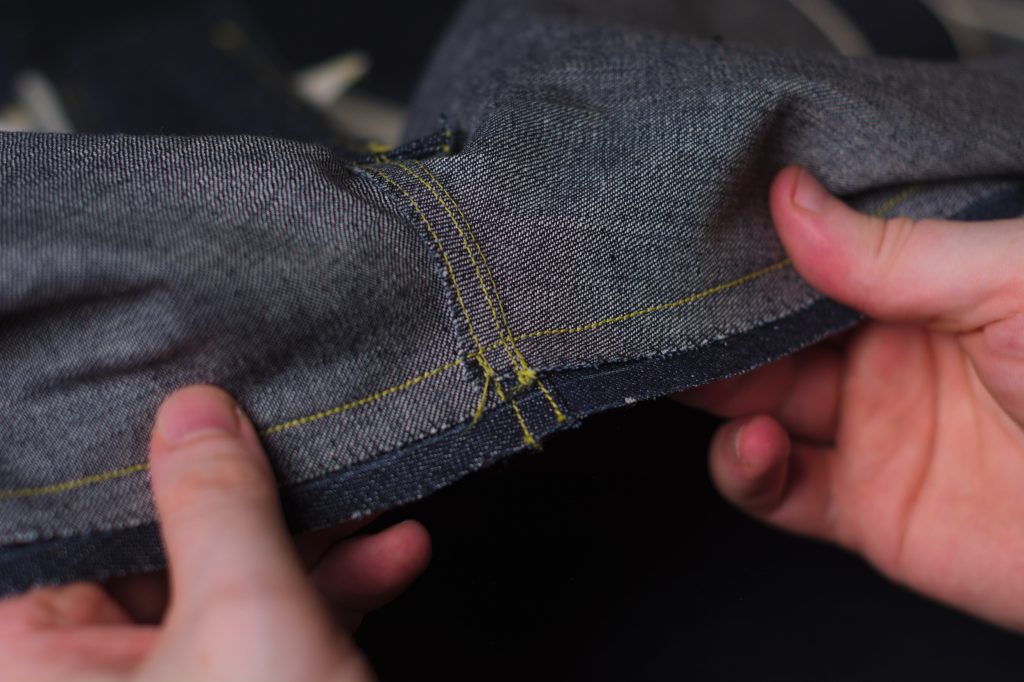
Which leaves the slightly misaligned seams on the front. It’s up to you if you want to redo that or not – I chose to press on as the originals were definitely not perfect either.
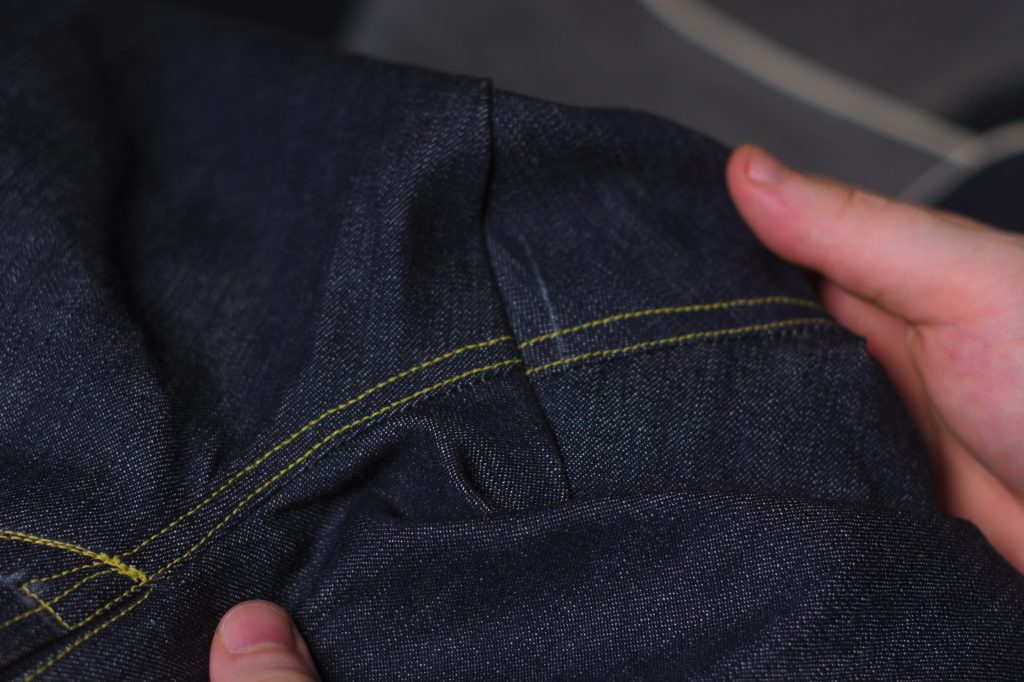
Finishing the Inseam – Modern Jeans
If you’re doing a more modern pair of jeans, and your sewing machine can handle the 16 layers, this is the method that provides the best finish. For the 1873 jeans and those that have a less powerful sewing machine, you’ll want to stick with the 1873 version below.
Begin by pressing the back leg seam allowance over the front inseam by about 3/8″, or just before it touches the stitch line.
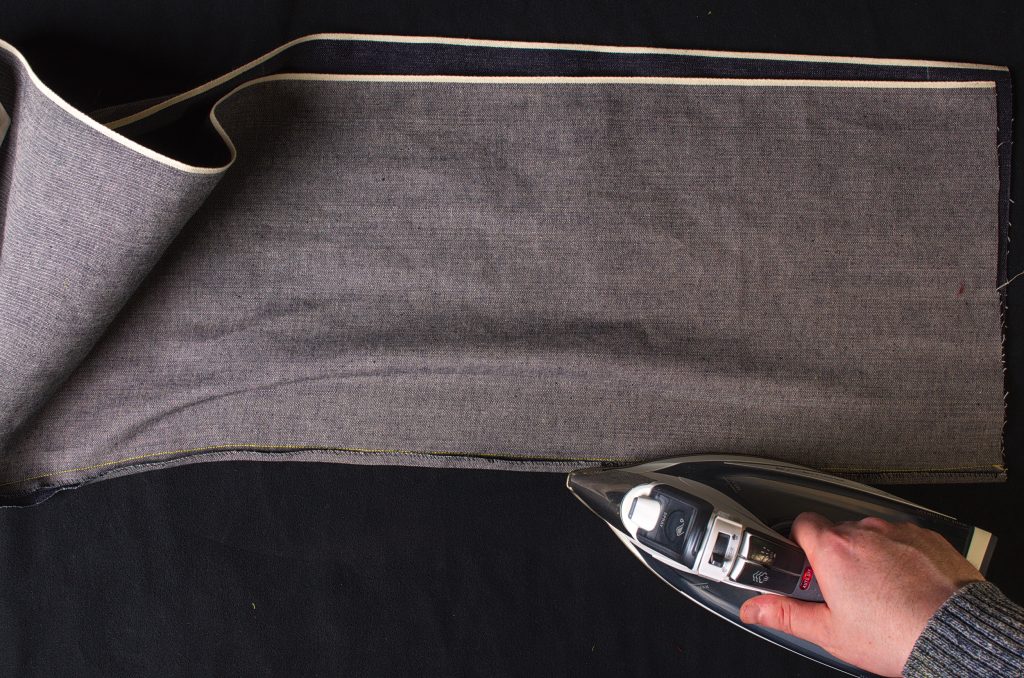
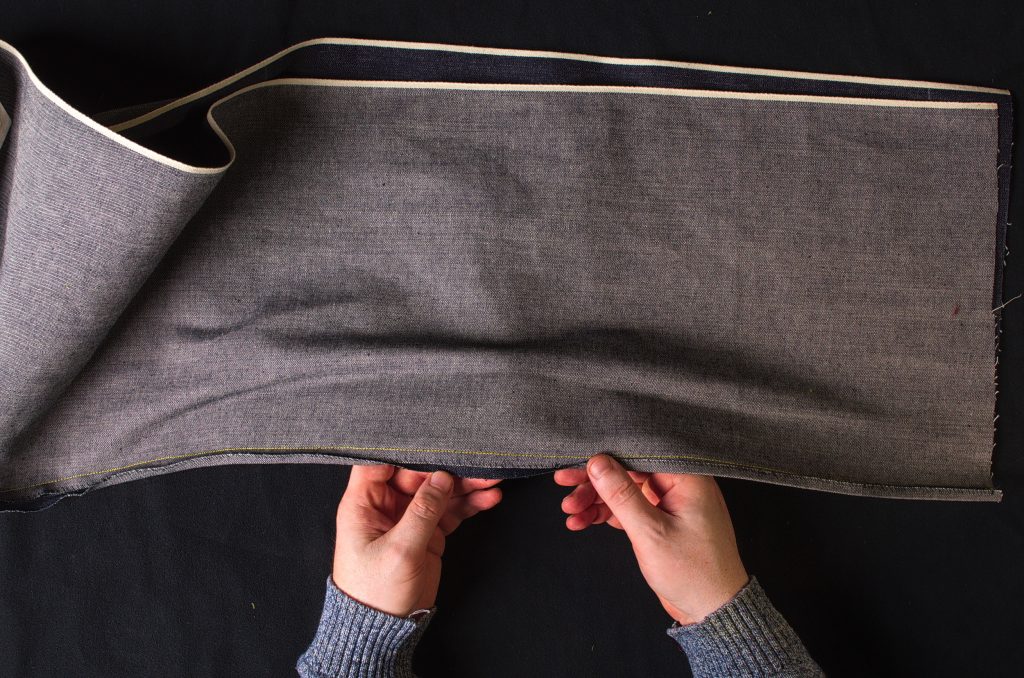
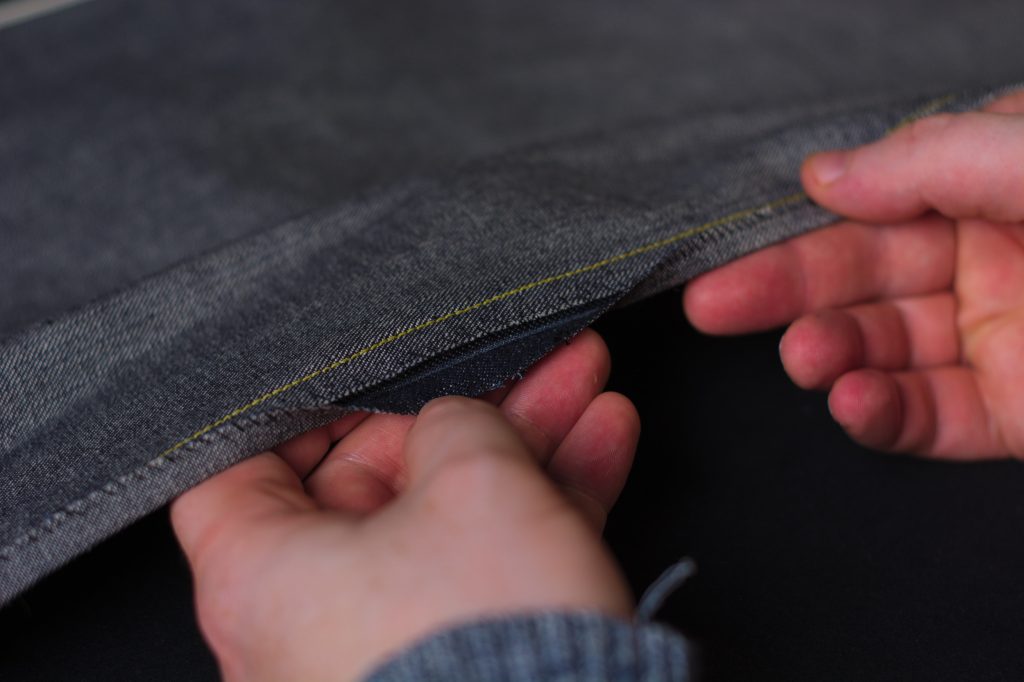
Now here’s the tricky part. Open up the legs, keeping them right side up. About 3/8″ from the seam, top stitch through all layers. You’ll have to check frequently that the crease you put in with the iron is still in place as you’re sewing. Top stitch from the hem, along the inseam through the crotch, to the other hem.
You can put a second row of top stitching about 1/16″ – 1/8″ away from the seam if you want but I usually just do the one row.
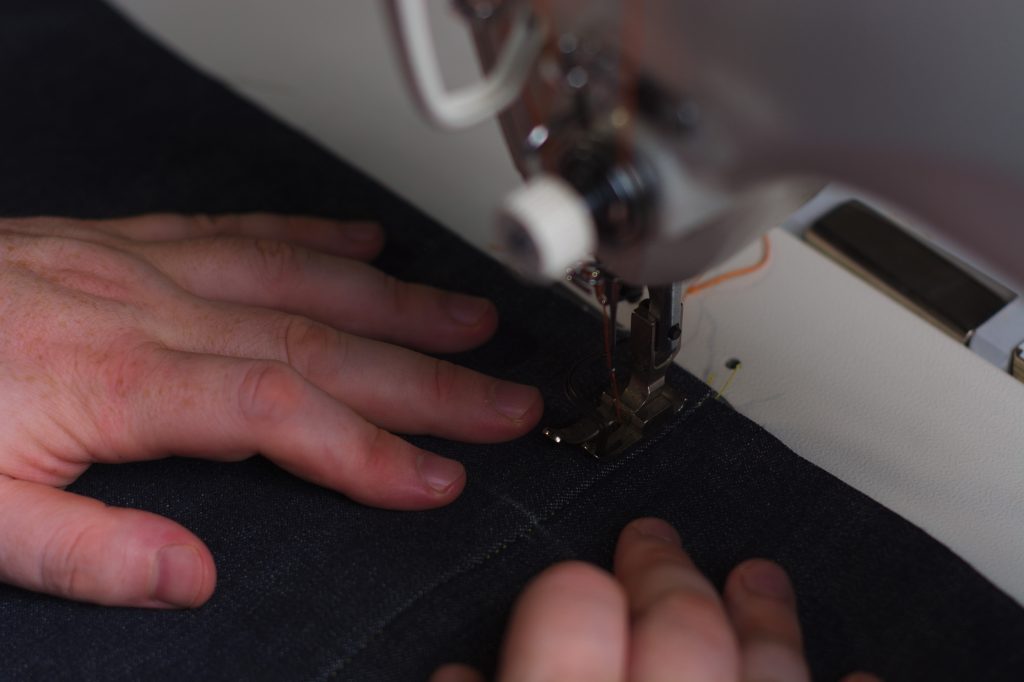
Here I’m flipping the leg to the underside to make sure the seam is still in place.
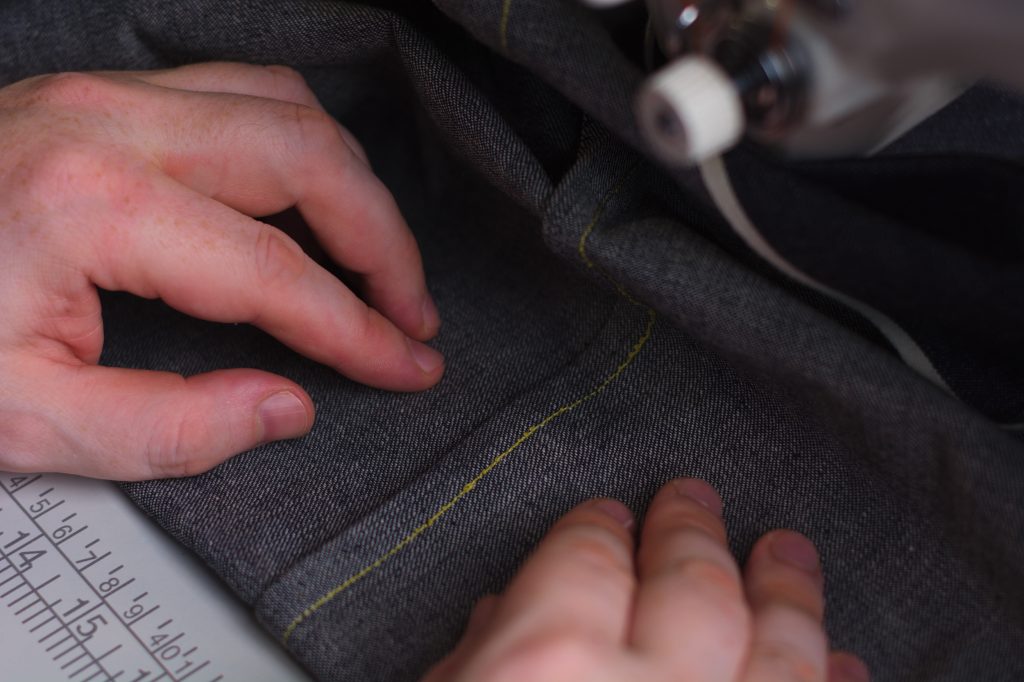
I’ll be adding additional photos here when I make my next pair of modern jeans. Be particularly careful around the crotch area and use a hammer to flatten all of those layers, along with the seam jumper when sewing.
Finishing the Inseam – 1873 Jeans
For those doing the 1873 jeans, or with less powerful sewing machines, this is the method to use.
Begin by pressing the seam allowance of the inseam towards the front leg, so that the larger seam allowance is covering the smaller one.

Top stitch from the hem, through the crotch, and down the other half of the inseam to the hem, through all layers, about 1/8″ from the seam. Be sure to check the underside frequently as you’re sewing to be sure that everything is still in its proper place. It’s easy for things to shift out of position.
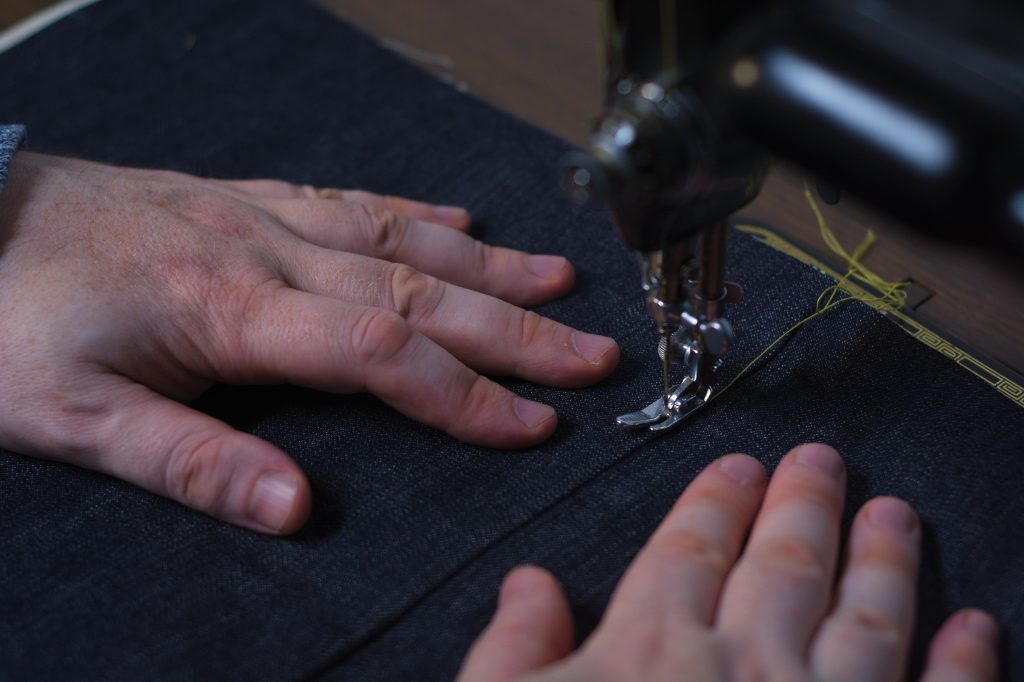
Here’s one half of the inseam after top stitching.
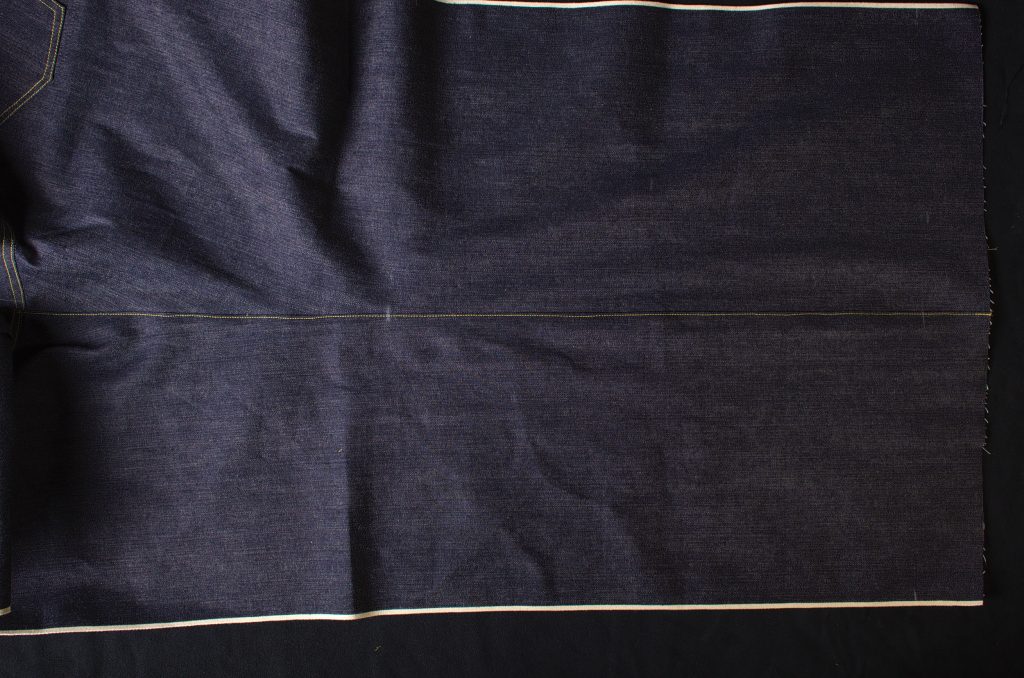
And here’s a photo of the crotch area. The misaligned top stitching is barely noticeable now.
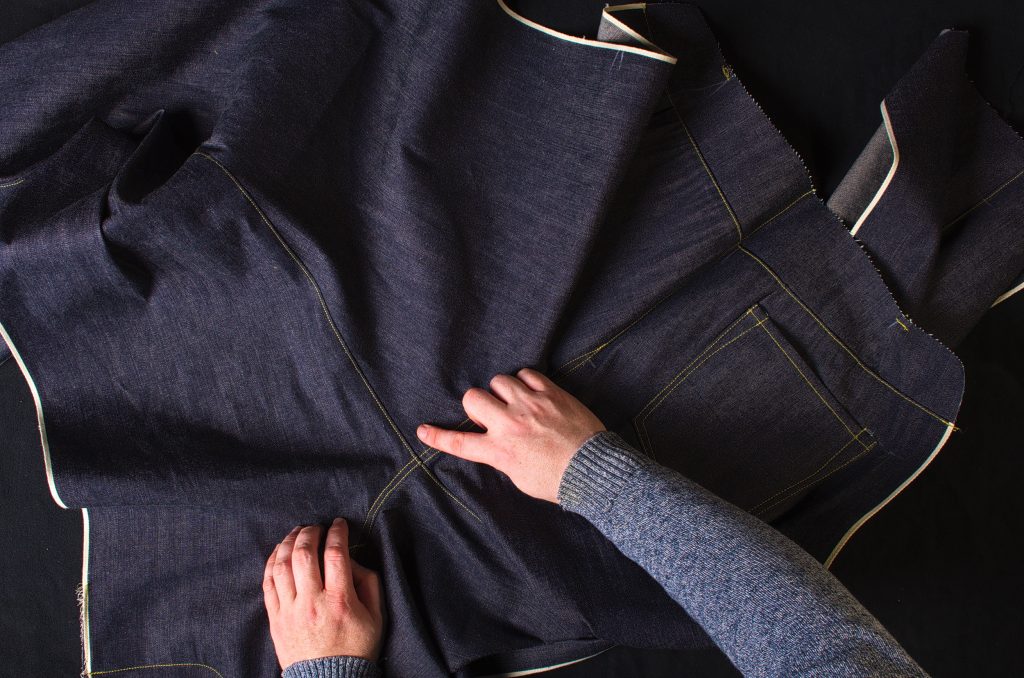
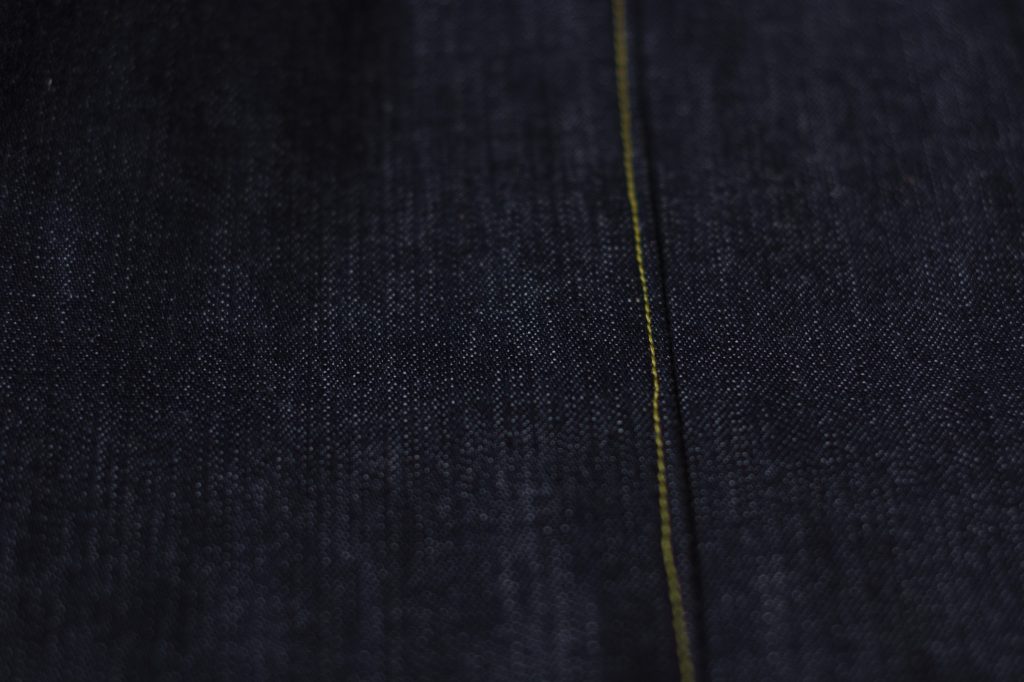
A view of the wrong side of the inseam after top stitching.
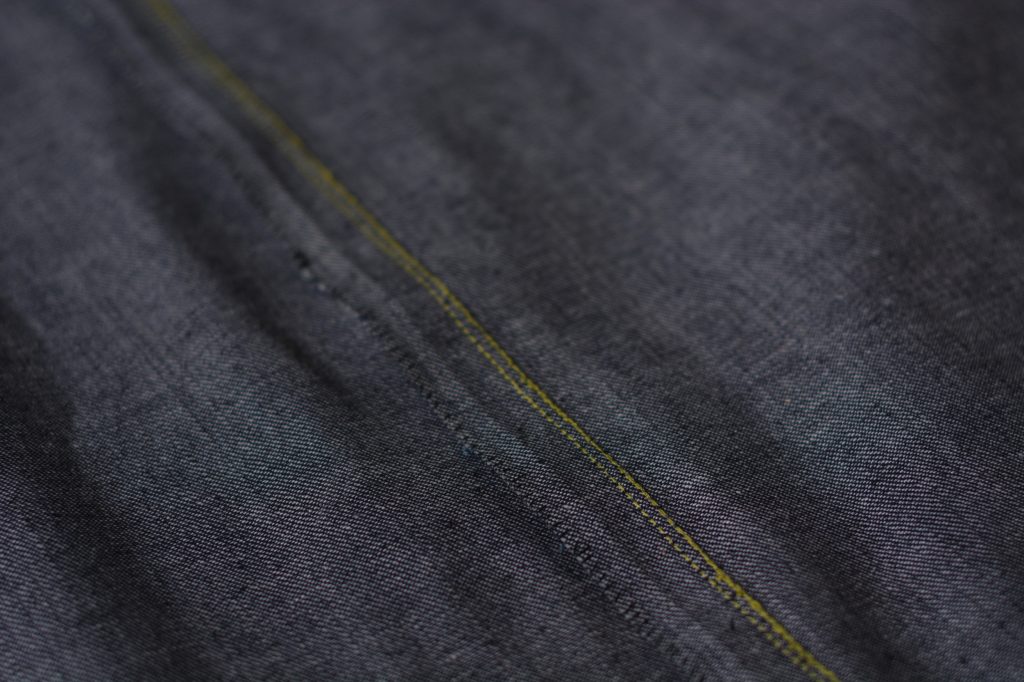