Author: James Williams
Rear Facings
I’ve always considered this step as the ‘first’ step in constructing a coat, as all the technical and fitting issues are finally behind us. As such it’s also one of my favourite steps. We are going to commence construction of the tail facings, which protect the edge of the garment from wear, and give some weight and body to the area as well.
Begin by laying both back pieces, right side up, as shown. The left side should overlap the right. Take this left piece, and set aside the right piece. It’s important because each side is constructed slightly differently. The following steps all pertain to the left side.
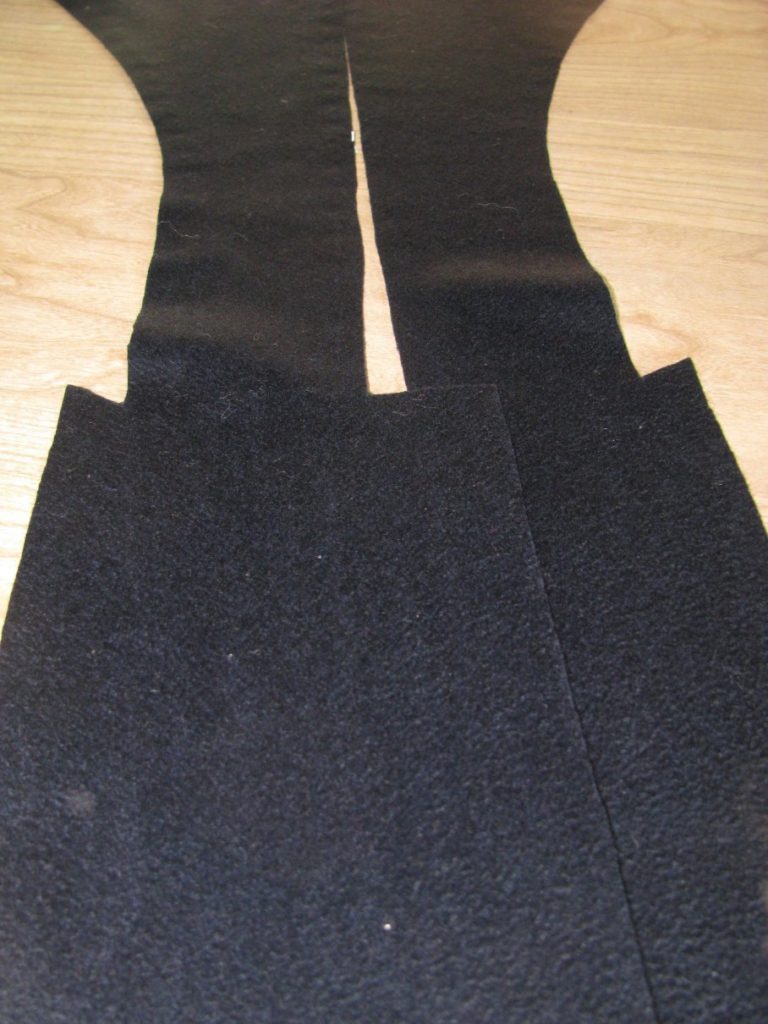
Turn the left side of the back so that the wrong side is facing up. Trim away the inlays around the waist area and center back, if you did not need them. If you made any adjustments to this area, then trim only the excess amount.
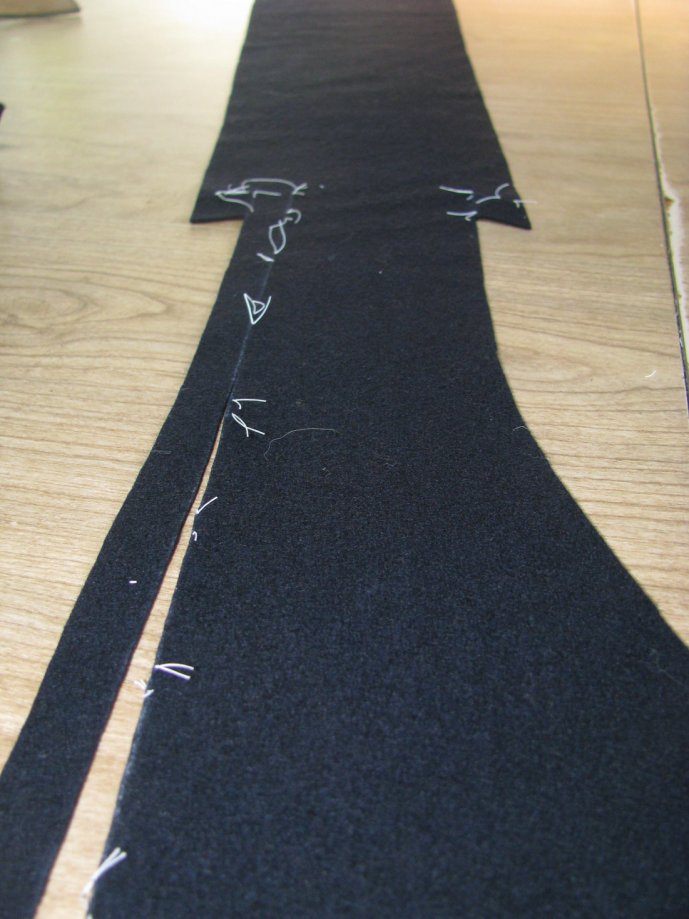
Measure and chalk a 1⁄4 inch line at the bottom of the center back, and across the top of the center back vent, as shown. Again, make sure you are working on the left side of the coat before you continue. Make a small cut from the corner of this area to the intersection of those two lines, as shown. The cut should be made just to the lines, not extending into it, as the chalk has a width to it, remember.
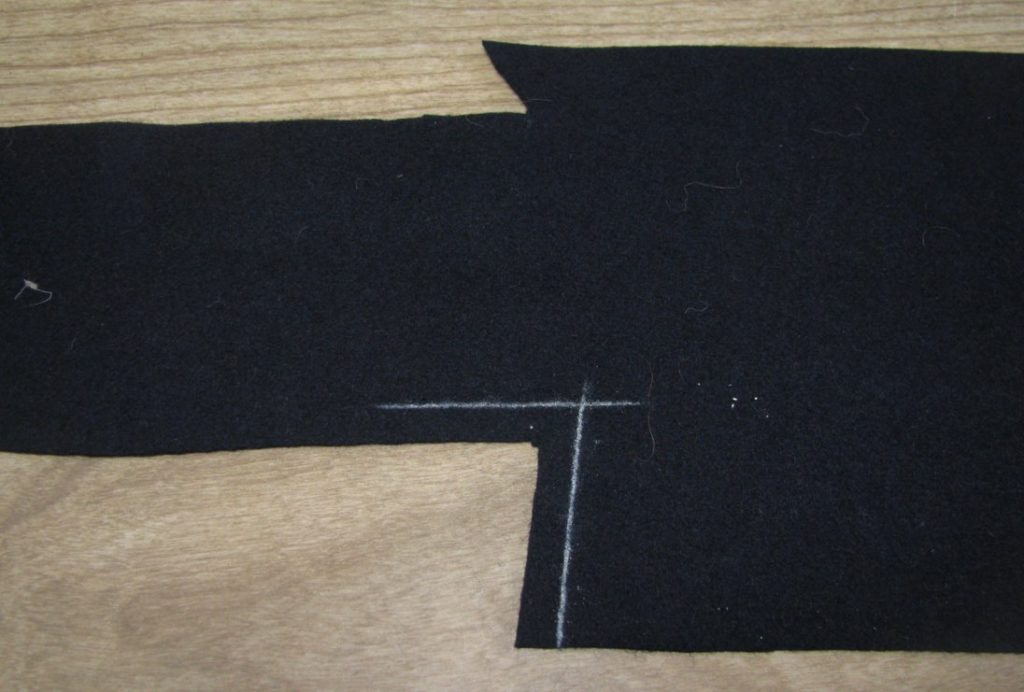
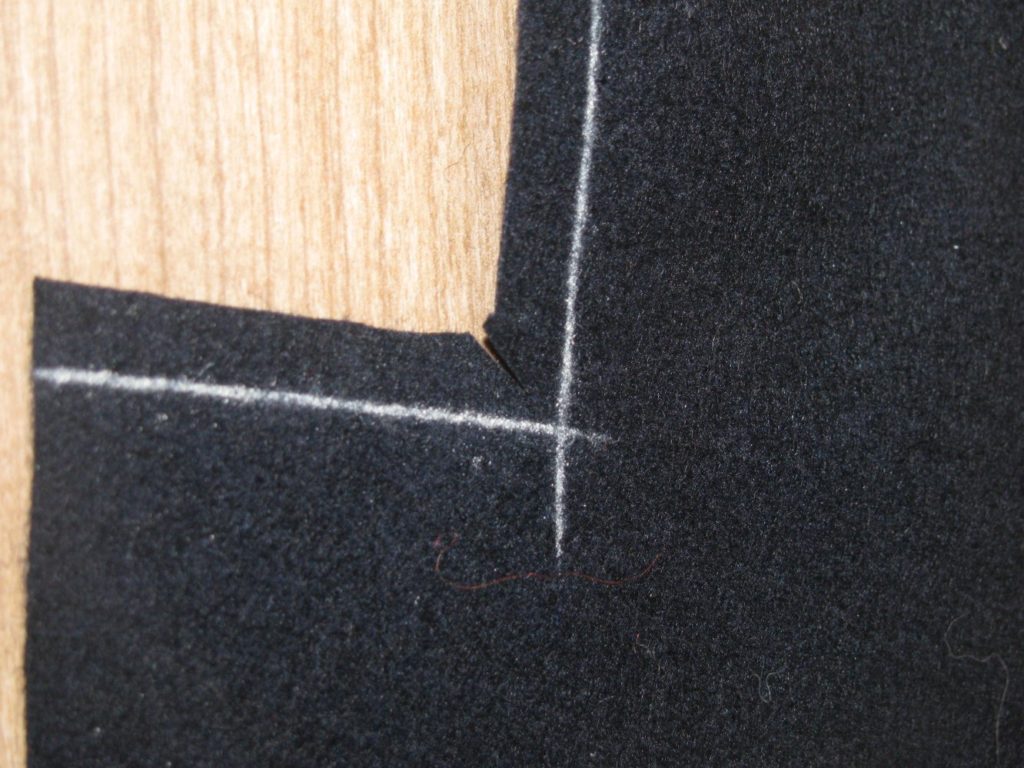
Next, mark a vertical line extending from the top of the back skirt to the bottom. I generally make this 1 3⁄4” wide, because the fabric will be folded to this point to make a 7/8” facing. This is adjustable though depending on your size. Generally, the line should be made 1⁄4 inch away from where the center back seam line will be.
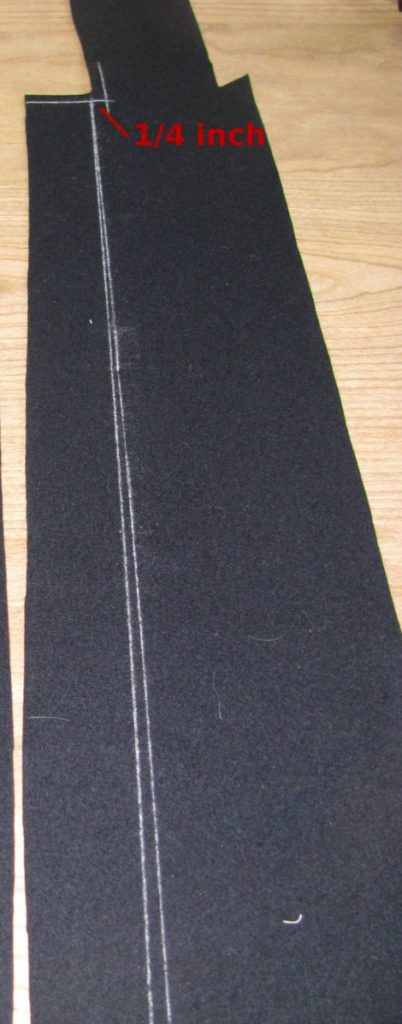
At the top, baste over the fabric 1⁄4 of an inch, and press carefully. Then baste the fabric along the center back over itself, so that the edge lines up with the vertical line you just drew. Baste carefully. There will be a little fullness at the top, because you don’t want the facing to extend above the top of the vent. Press this fold as well, gently shrinking out the fullness.
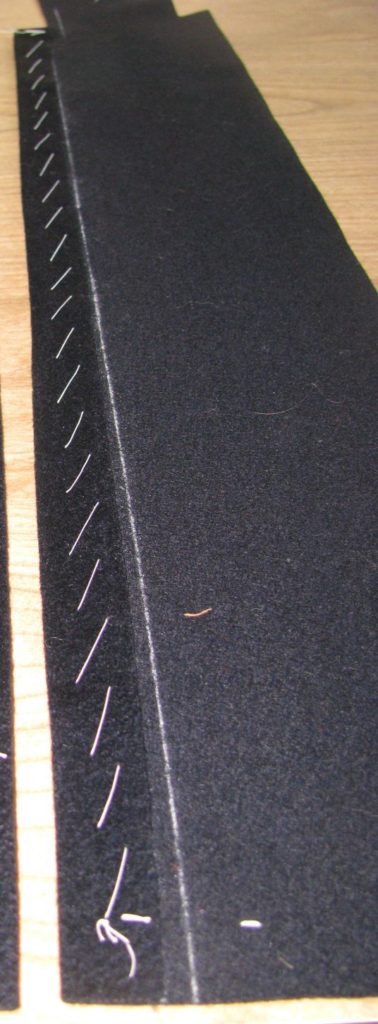
At this point, remove all basting stitches, and unfold the facing. You should have a nice crease along the edge, and top of the back vent. Use this as a guide to baste in the linen stay tape.
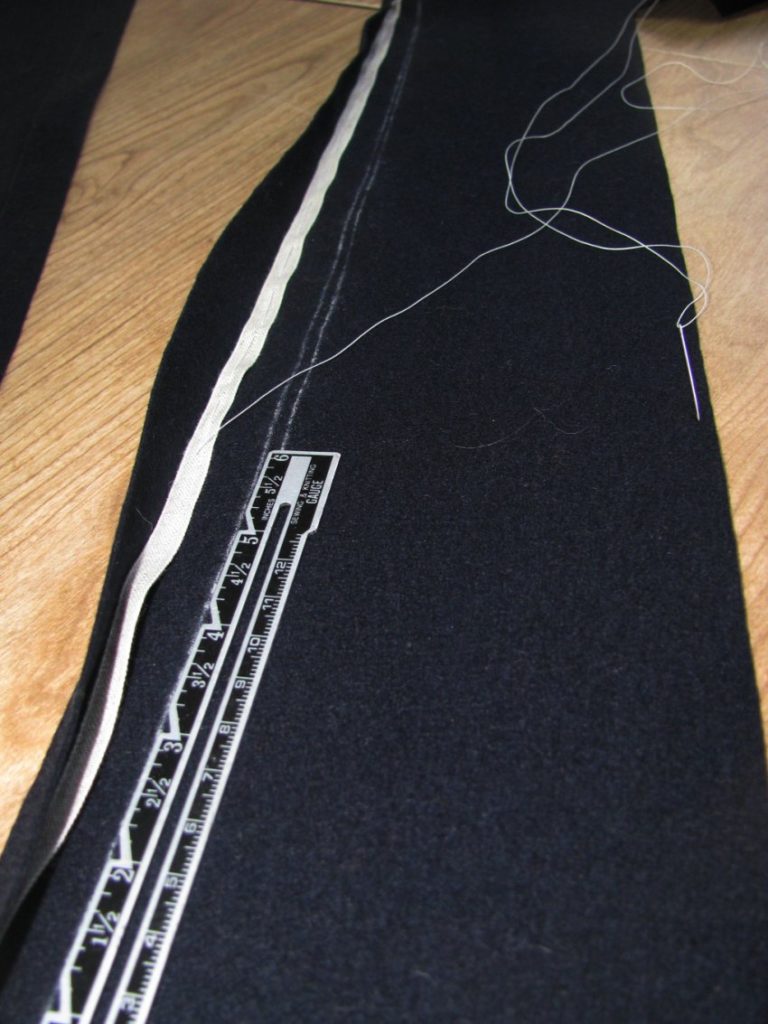
The tape should be placed right along this crease, starting at the top. Start with a back stitch with your basting thread to hold it in place at the top, and hold the tape where you want it as you baste.
About 8 inches from the bottom, make another backstitch in place. From this point on, hold the tape a little tight compared to the fabric until you get to the bottom. The tape should be about 1⁄4 inch tighter than the fabric, which is distributed equally along the 8 inches, as you baste. At the bottom, end with another backstitch in place. The stay tape should be trimmed 1/8 of an inch above the inlay at the bottom.
The stay tape is then slip stitched into place, making sure the stitches do not show through to the right side.
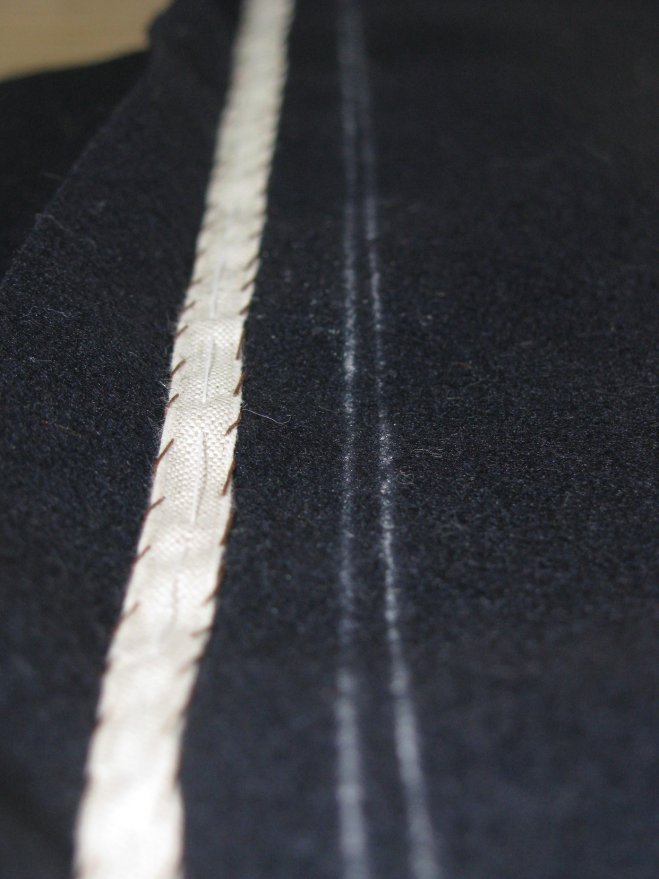
Baste the top of the vent closed again, and fell it down by hand,using 8 to 10 stitches per inch. These stitches should not appear on the right side of the fabric, and should be just little pinpricks on the wrong side of the facing. Catch only a few threads in the facing as you go.
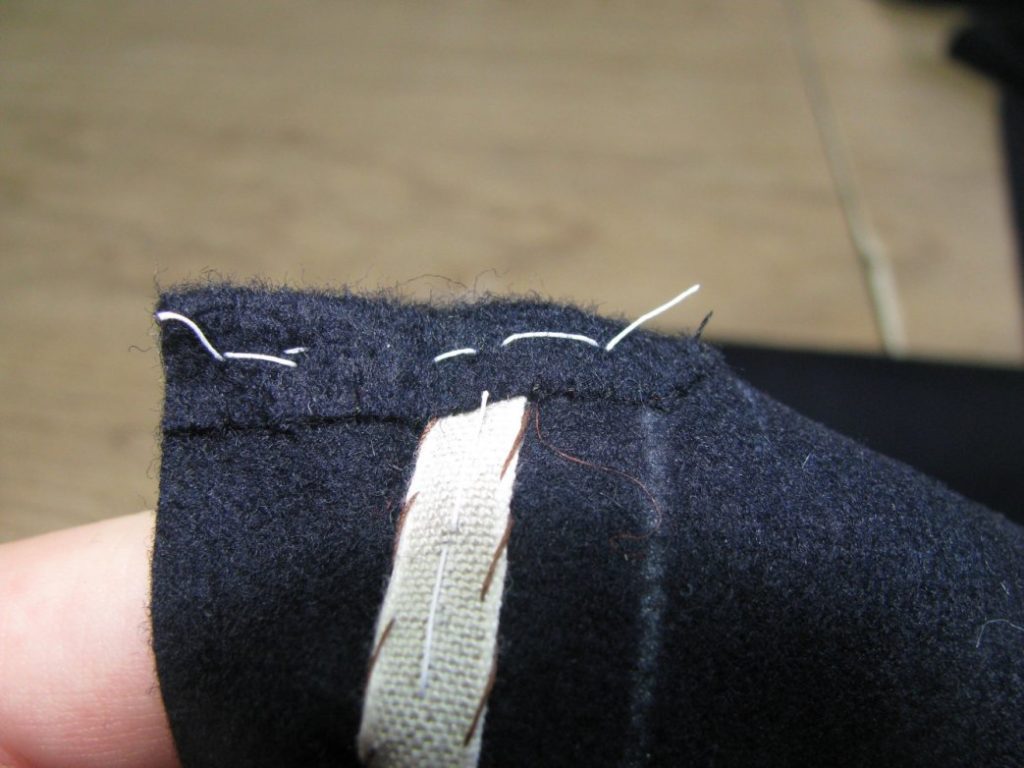
Next, baste the facing closed again, and fell this as well, as just described.
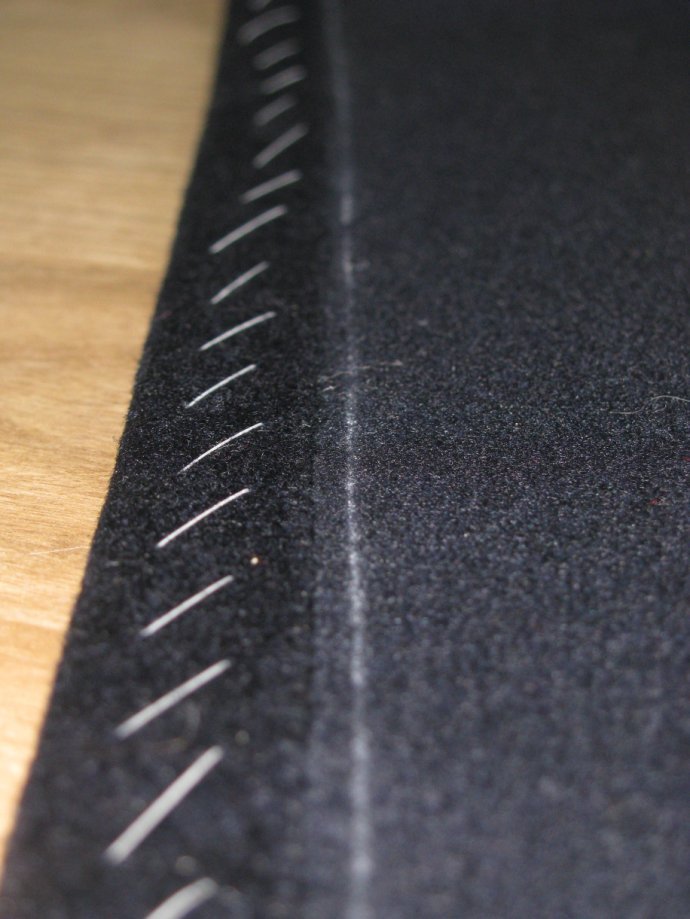
Finally, press the facing from the right side on a flat surface, to remove any wrinkles and puckering. Do not press any further than the edge of the facing, because there should be a slight fullness here from holding the stay tape tighter. This is the same principle as when shrinking the front of the forepart. The result should be a back tail piece that curves slightly inward, and helping to avoid sticking out away from the body.
Pick up the right back piece. This time, do not make the cut, but proceed to making the 1 3⁄4 inch vertical line. Baste over along just this edge, insert the stay tape, and fell just as with the left side. It’s okay if the stay tape extends above the top of the vent a little.
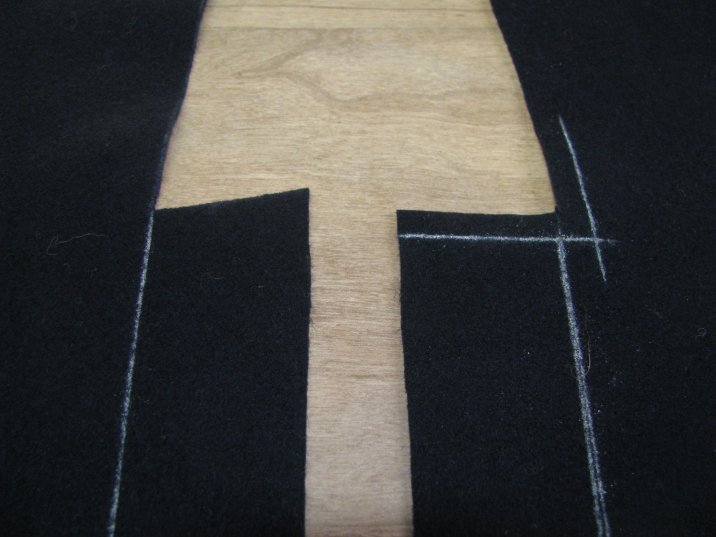
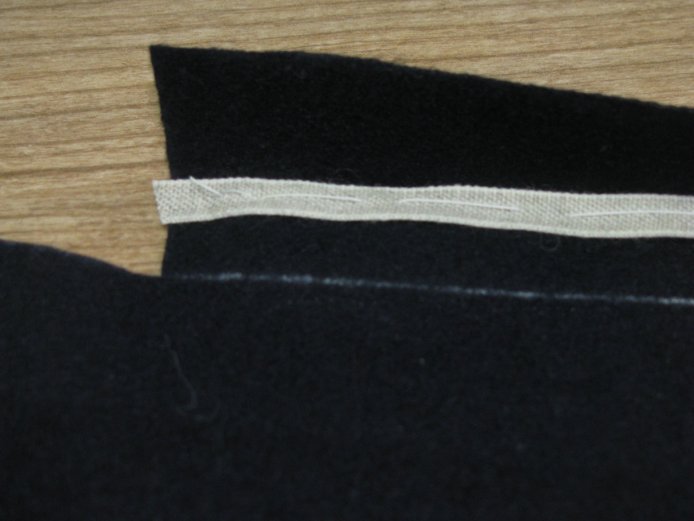
The result should be two back pieces with facings, that are different only at the top of the back vent. This will add strength to the back vent, as we’ll see in a later step.
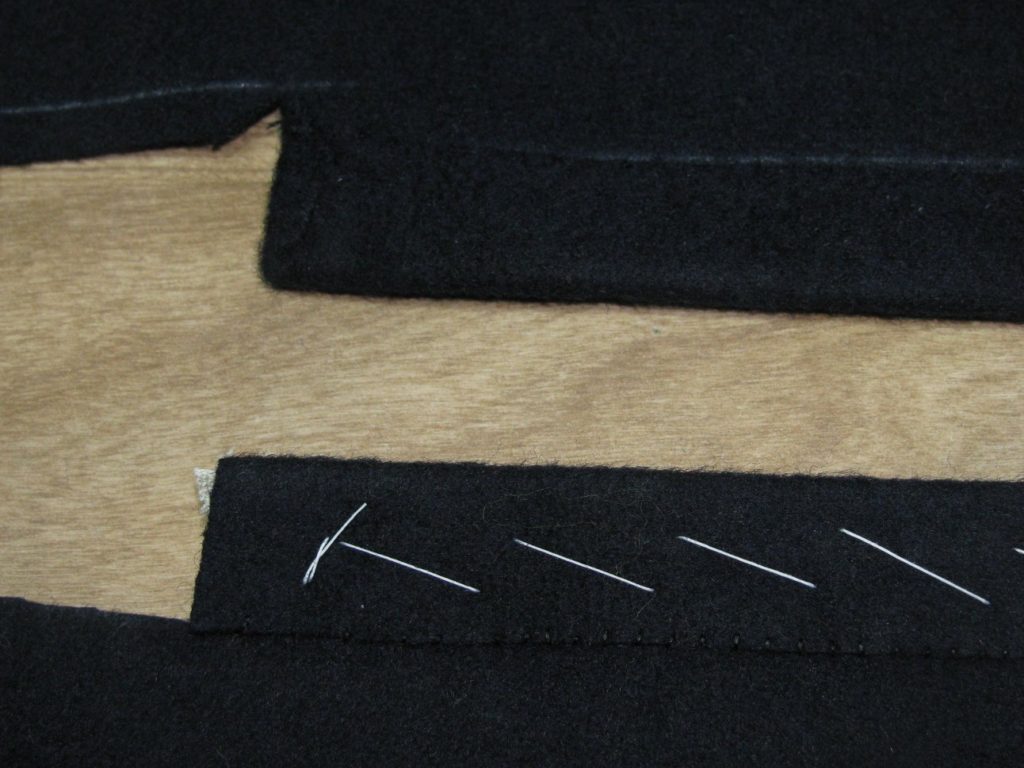
First Fitting
Congratulations, you’ve made it to your first fitting intact! The main things to check for at this fitting are the same as at the beginning of this module. If you need to make adjustments, do so now by marking the amount you need to take in or out with chalk (just draw a line), and then removing the basting stitches, and rebasting. Remember, you need to leave room for the padding and lining, so don’t fit the front too tightly. Be mainly concerned that the back hugs the back closely, that there are no unsightly creases or folds, and that all seam lines are in their proper place.
- Make sure you have lowered the waist seam of the pattern, as was the style in the 1860s. When you do that, the fabric then comes over the hips, so make sure there is a bit of spring added to the pattern.
- Try putting a belt on while you are wearing the coat. The bottom edge of the buckle should lay just above the point where the buttons will be. That’s where the skirt, back piece, and side pieces all meet.
- Ensure that the center front of the coat meets up and touches, without excessive tightness. If necessary, add to the front as previously discussed.
- Finally, make sure the front of the waist doesn’t dip down too much, and that the fronts of the coat do not fall away. If they do, raise up the front of the waist slightly (you can just use pins to test), and if that fixes the problem, you may leave it for now. Please post photos of this stage, for critique and helpful hints.
One important aspect of a good fitting coat is having a correctly balanced coat. Remember that balance is the length of the front compared to the back. As you are fitting your coat with the basted skeleton fitting, take a look at the front of the coat. Do the fronts swing away from each other? If so, temporarily remedy this by pinning the center front of the forepart until the fronts are even. Just take out an inch or maybe more as if you were putting in a dart.
Next, measure how much you had to take in to make the fronts hang evenly. If it was more than one inch, you’ll have to raise the waist seam manually. For example, if you had to pinch the front seams up 2 1⁄2”, the waist must be raised 1 1⁄2”. The remaining inch will be shrunk away with ironwork in the next step. Please keep in mind that 1 1⁄2” is just an example, and exaggerated. Hopefully you won’t have to take in that much. If the amount needed to balance the fronts is one inch or less, this can be achieved by ironwork alone.
The waist seam is raised by subtracting the amount from the bottom of the forepart. The skirt length remains the same.
Removing the Basting Stitches
After you have made all necessary corrections during the fitting, make sure you have marked the new seam lines with chalk, and that they all agree with each other. For example, the waist seam in front should be raised up equally if necessary. At this point, you will remove all of the basting pieces, and press the seam allowances flat again if necessary. Be sure not to undo your careful ironwork on the forepart though.
The Skeleton Baste
Darts
On the wrong sides, on both the skirts and forepart, mark the darts in chalk, carefully tracing the thread tacks you put in. If you don’t have any darts, then you may skip this step. Next, baste the darts, starting with a couple of stitches in place to hold, then using the basting stitch. Make sure the stitching aligns with the chalk lines on both sides of the dart as you sew.
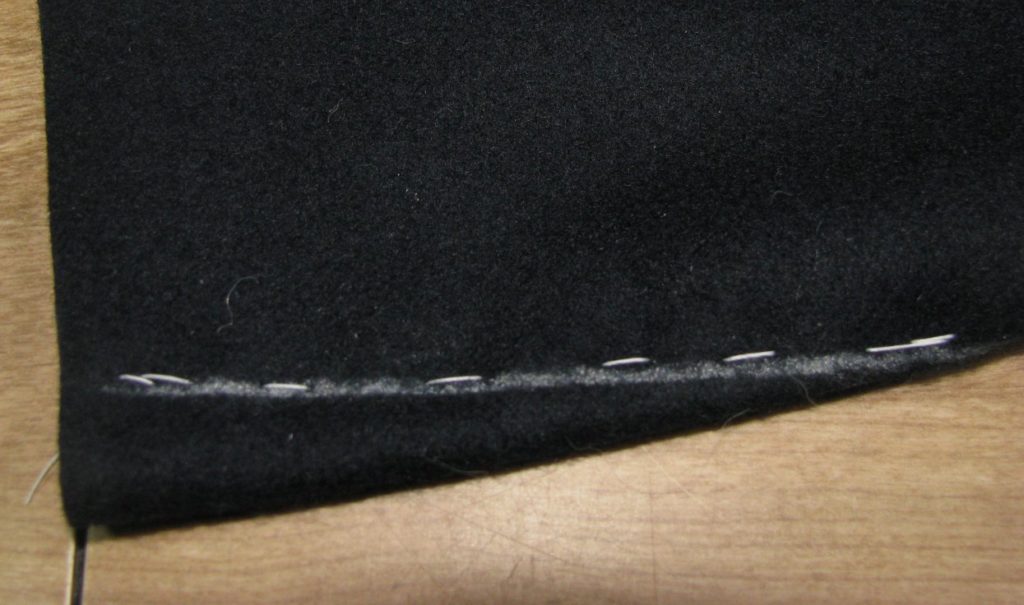
The Skeleton Baste
At this point, you will baste together all pieces of the garment by hand, to test for fit one last time. Normally, in a skeleton baste, the tailor would baste in the padding, linings, and collar as well. Since you have yet to learn how to construct these pieces, we will forgo them for now. On your next project, you may put them in.
This is done just the same way as for the full muslin, except to not clip any seams. Treat the marking threads as the edge of the cloth, the inlays are there in case you need room.
When you are basting together the center back seam, sew from the top to 1/4″ inch past the bottom of the inlays at the waist seam.
Then you can get a good idea if the opening is at the correct height or not. Press each seam as you go, but only lightly. And when sewing each seam, stop when you hit the marking threads. You don’t want to include the inlays in the seam, as they are not technically part of the coat at this point.
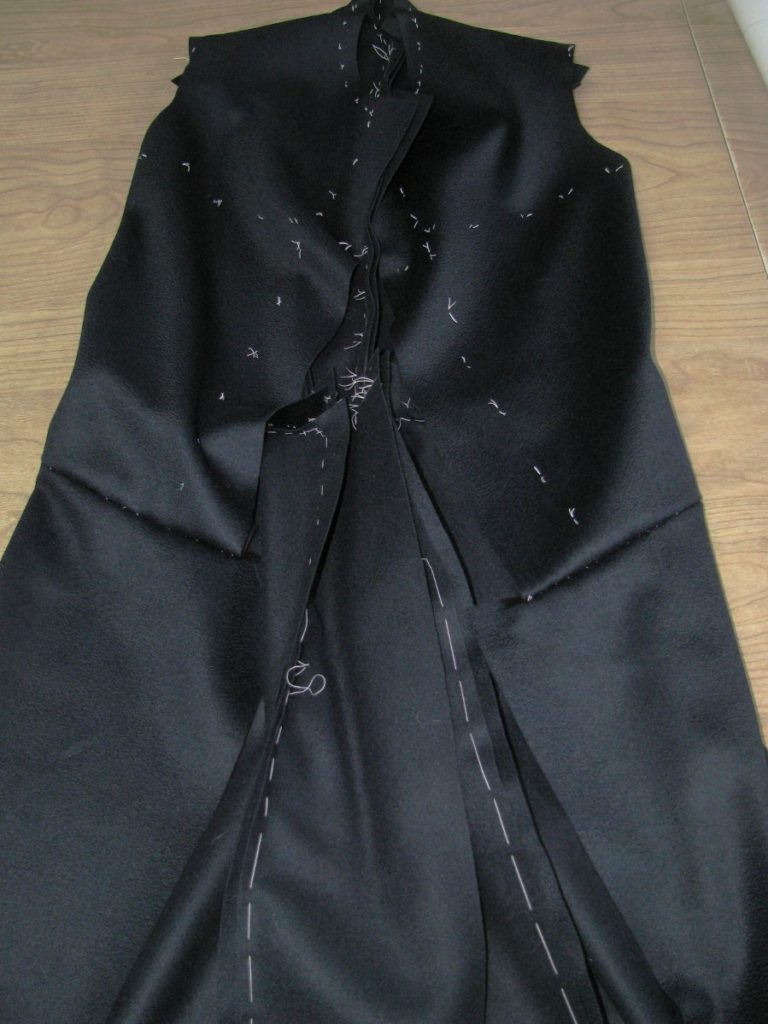
The Skirt
Now we will actually commence construction, starting with the skirt. Find the small triangular pieces you cut. Also be sure you have separated the two skirt pieces by cutting carefully on the fold line. Next, figure out which side is longest on the triangular piece, and line it up, right sides together, to the skirt piece. It may take some fiddling to figure out which piece goes where, but I assure you, they will line up, providing you added double the seam allowance when cutting.
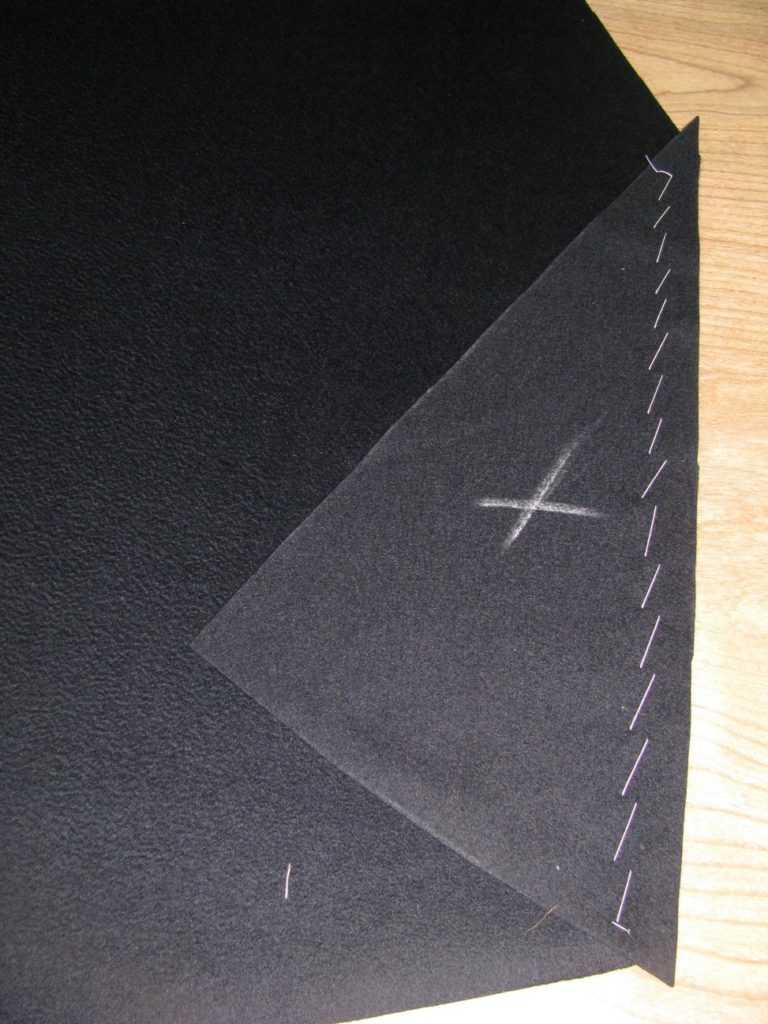
After they are lined up, baste together carefully, making sure there is no fullness on either side. Then, sew, using a 1⁄4” seam allowance, with either a backstitch, or machine stitch. If using the sewing machine, I recommend about 12 stitches per inch. Remember that machines of the period could not so backwards, so no back-tacking! Instead, leave about 4 inches of extra thread at the ends, pull the threads to one side, and tie in a secure knot. Remove the basting stitches.
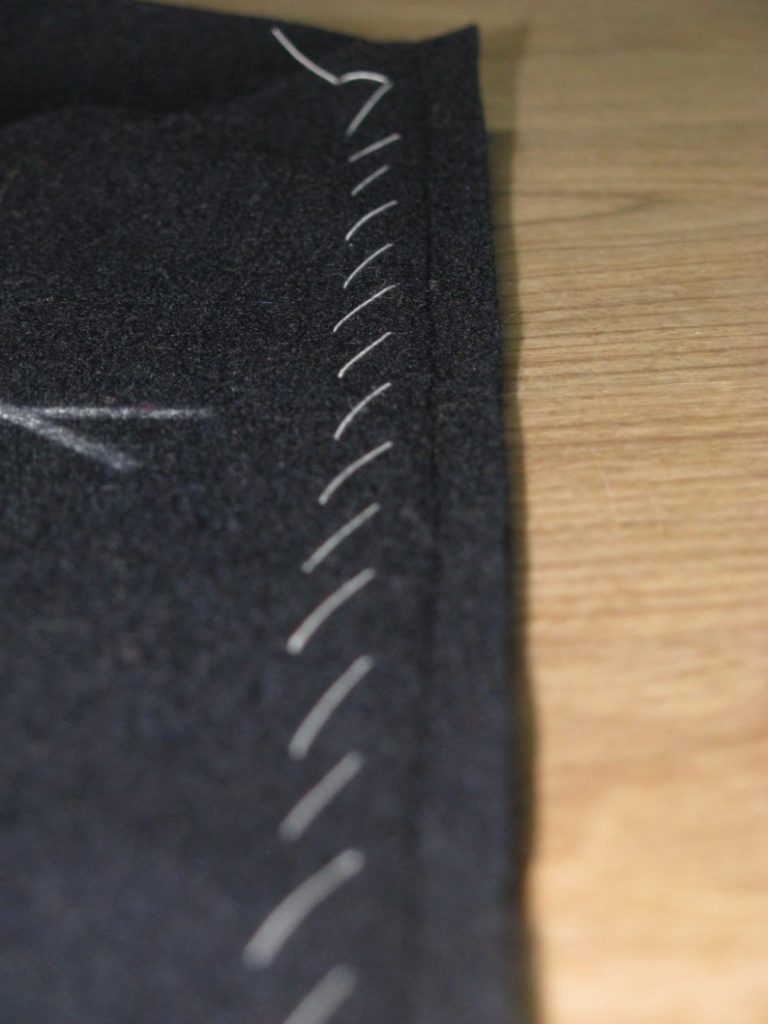
Now, press the seam, using the following technique. After pressing, snip off the little triangular pieces that form at either end of the seam allowance.
Pressing Technique and Opening Seams.
The first rule of pressing is to not move the iron up and down the seam, as this has a tendency to stretch the seam and throw it out of shape. Begin by laying the pieces, still right sides together, on the ironing board. Go over with a hot iron, with steam, and press the seam. Flip both pieces over, and repeat this process. What this is doing is setting the stitches, which will give us a tighter press of the seam.
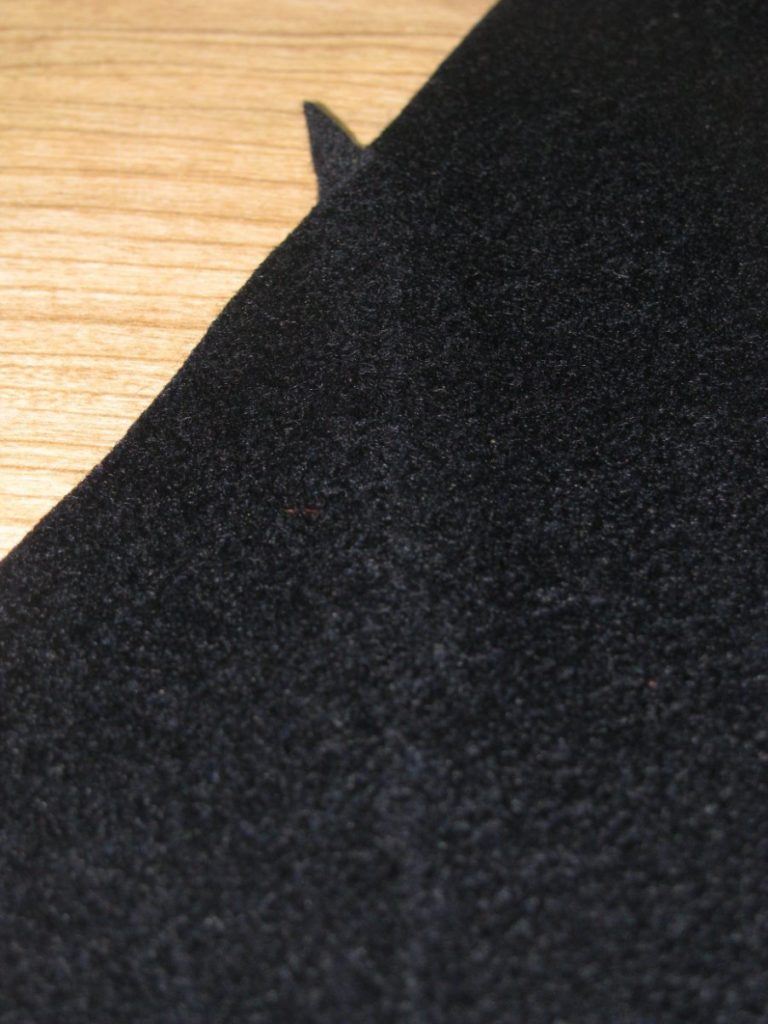
Next, open up the seam from the wrong side, and press the seam open. Take your time, and do just a small section at a time. Hold the iron for a few moments, remove, then press with a heavy goose iron, or clapper, to really set the seam. We’re trying to avoid that rolled look to the seams that one so often finds, especially in coats made of heavy fabric.
Turn the fabric over to the right side. Using a scrap of fabric as a press cloth, go over the seam again, with the steam iron, then the clapper or goose iron. When using the clapper, you may want to put the fabric seam on a hard surface such as a piece of wood. Make sure to use a press cloth whenever pressing the right sides of fabric, to prevent shine and imprinting the shape of the iron.
If you have the problem of the seam allowances showing through to the right side, press the seams with a piece of cardstock underneath each of the seam allowances.
Ironwork
Ironwork seems very intimidating to most people, as very few tailors, save the bespoke tailors on Savile Row, and some others, still practice it. The style of ironwork done in the period is almost unheard of. I know it was one aspect of tailoring that took me years to figure out. I didn’t have anyone to just show me though, and had to learn it through books and lots of practice.
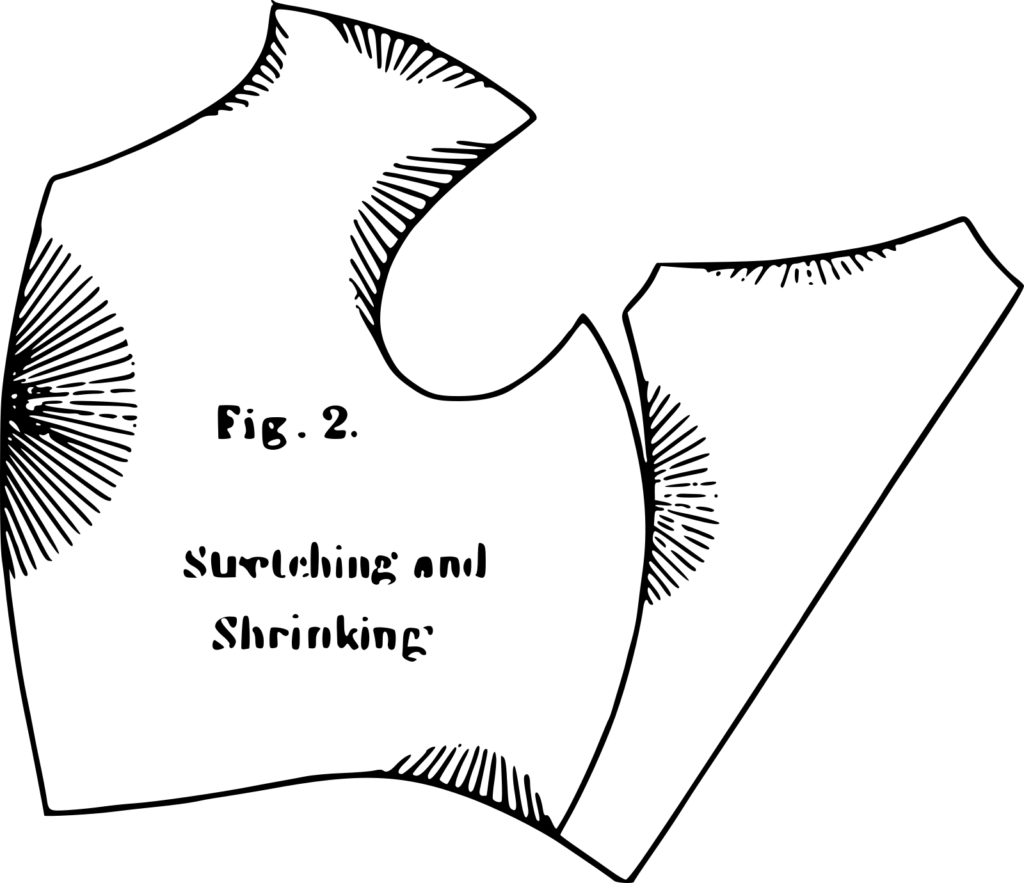
It’s a good idea to do most of the stretching on your muslin wrapper. Even though it will not stay permanently, it will give you a better idea of how the final fit will be. Shrinking will not work on the cotton muslin, so you’ll have to train your eye to recognize the adjustments needed.
If you skip the ironwork, you’ll end up with long vertical folds near the shoulder and front of scye, and the chest will not be full enough to contain the padding we will be inserting. The front of the coat will drape open, a problem often seen.
The following text comes from Practical Tailoring, The Art and Craft Simply Explained for the Student and Apprentice, by J. E. Liberty. He gives the clearest instructions for ironwork I have found yet.
Shrinking to Shape.
The material should be laid on the board and a little water applied with the fingers of the left hand, the part to be shrunk being nearest the worker. Place the iron first at the back of the material at a part where the shaping will begin, and working it from right to left and towards the front, work round the part being shrunk with the fingers of the left hand while the iron is moving. It will be seen that the shrunk section probably has one or two small pleats formed by trying to shrink too much at once, and these should be smoothed out by putting a little water on the creases and passing the iron over them. It should not be necessary to go over the shrunk part more than twice to obtain the shape required, as too much shape will not hold in the cloth, and should be taken out be seams in the cutting of the garment.
Stretching.
In stretching the process is similar to that used in shrinking, except that the material is worked out instead of in. It should be remembered that in shrinking into shape, the material will, after a time, return to its normal shape, but with stretching, it seldom, if ever, does ; also that to obtain length by stretching naturally reduces the width, and this must be allowed for in cutting.
Forepart
We will begin our ironwork by taking up the forepart, and stretching the front of the armscye. The total amount of stretching should be about 3⁄4 of an inch. Hold the fabric at the shoulder point, and put pressure down with the iron, stretching as you go. Both layers of fabric should be stretched at the same time, to ensure they are stretched equally.
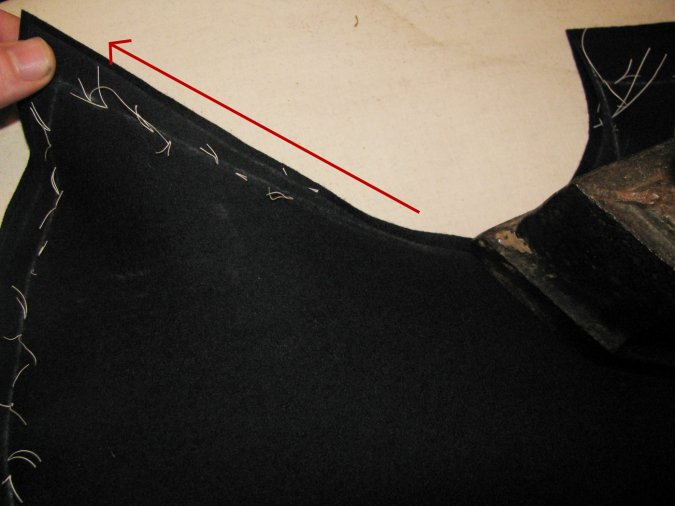
Next, stretch the shoulder seam, about a quarter inch total. This is one of those steps not explained in any book, but learned only through practice and critical thinking. If you measure the distance from the edge of the shoulder seam, and compare that to the edge of the back shoulder seam, you will see they are equal. If you add a seam allowance to that, there is no problem getting them to line up. This is what the majority of produced patterns do. Remember, we did not add a seam allowance, so instead, measure the distance of both seams, 1/4” from the edge. You’ll find that the back seam is 1⁄2” to 3⁄4” longer. By stretching the front shoulder seam, and shrinking the back shoulder seam, this distance is reduced, and the seams line up much closer. Now, stretch the hollow point of the neck seam only, about a 1/4” as well. This gives a little more shape to the shoulder area, and helps the neck hug the body more closely. Stretch the side seam as well, about 1/4”. This is not shown by Devere, but necessary to get the seam to line up with the side piece.
The center front needs to be shrunk, now. Notice how the center front is curved. You will need to shrink this carefully so that it is turned almost into a straight line. Please see the video for a demonstration of this and the other techniques.
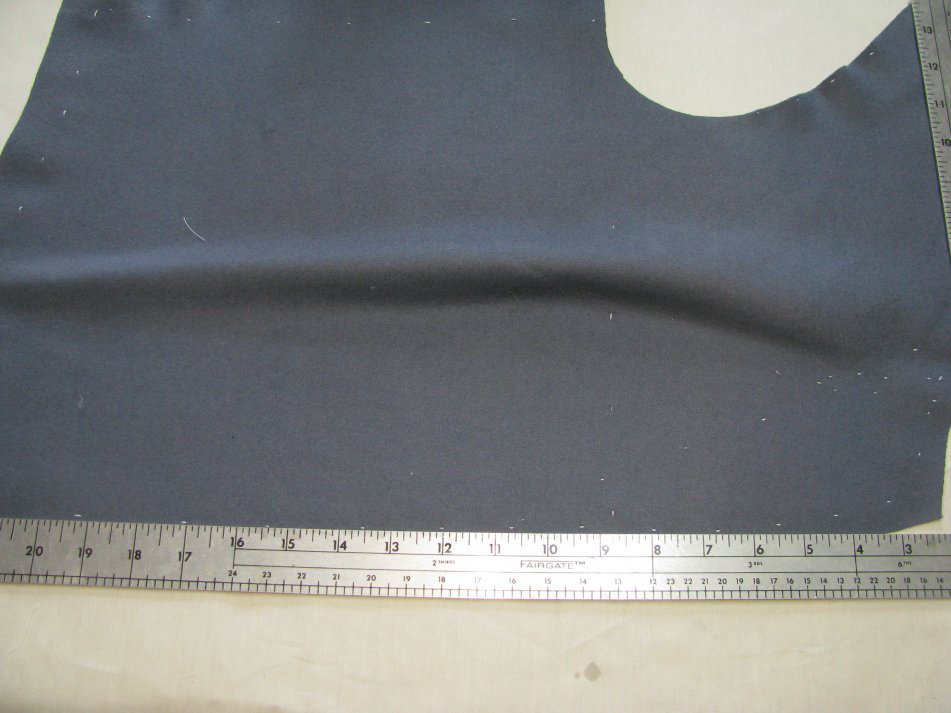
Notice how the fullness is visibly in the center of the forepart now.

This will also leave room for the padding later on. The shoulder area should have a lot of shape to it as well.
Sidebody
The goal of the ironwork on the side piece, is mainly to impart more shape into the coat. In this step you are basically folding the fabric over, and stretching the seams, while shrinking the middle. It will take some practice, but you will get it. Try not to crease the middle of the piece as you’re doing the ironwork, as it’s hard to get rid of.

The following is a description from The Art of Garment Making, by Phillip Dellafera.
Fold the sidebodies as indicated, then proceed by shrinking away all the ‘loose’ material that will show itself at the waist. This work must be done carefully, until a nice hollow is formed at the waist; it will then be seen that the outer edges will have become slightly stretched. This is exactly what is required, and it will be found that a well-defined waist is obtained by adopting this method.
Sometimes this effect is obtained by slightly stretching the seams in a downward direction only. This, of course, will certainly help to get the desired shape; but the best plan is to shrink the centre of the side body, which will automatically give the extra length to the seams.
Also, stretch the bottom of the side piece slightly, again about 1⁄4”.
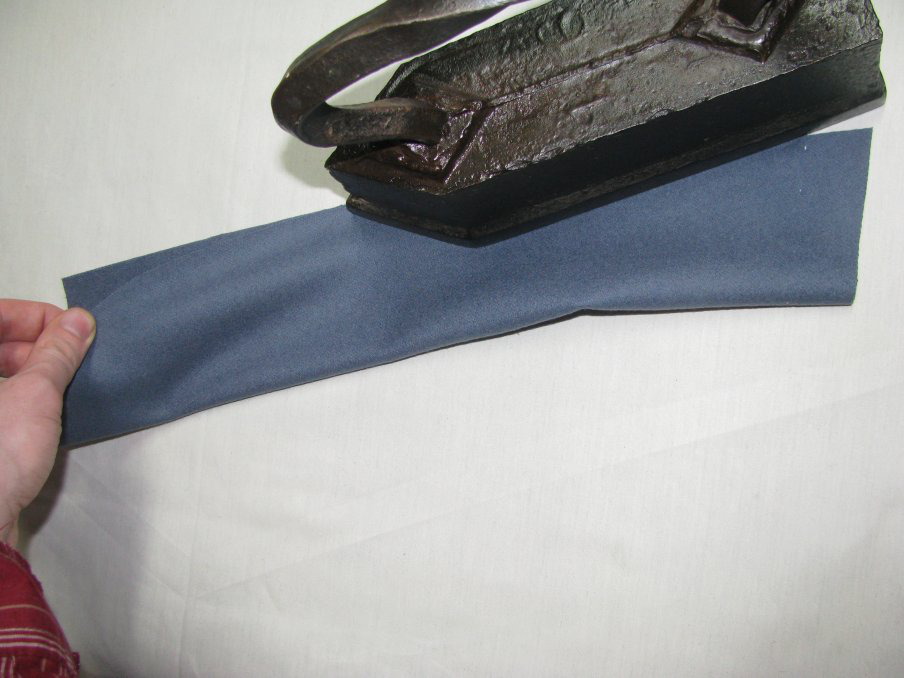
Here’s a video of the entire process showing the ironwork I usually do on a frock coat.
Inlays
If you are not confident in the fit of your pattern, or perhaps just want some extra security before you cut into your expensive fabric, it’s a good idea to add inlays – little extra bits of fabric in strategic areas – to give you extra room to work with if necessary.
Add inlays to each piece as follows. As you are learning to do this, measure out each inlay carefully. With experience, you’ll eventually be able to do this freehand, and anticipate how much inlay to add
based on the figure you are fitting.
Forepart
At the side and bottom, leave 1” inlays. At the center front, leave 2 inches. This is very important, and if you forget, the coat will not button. At the neck and shoulder, leave 1⁄2 inch, and at the armscye, start at half an inch, tapering to nothing about halfway down the front of the scye.
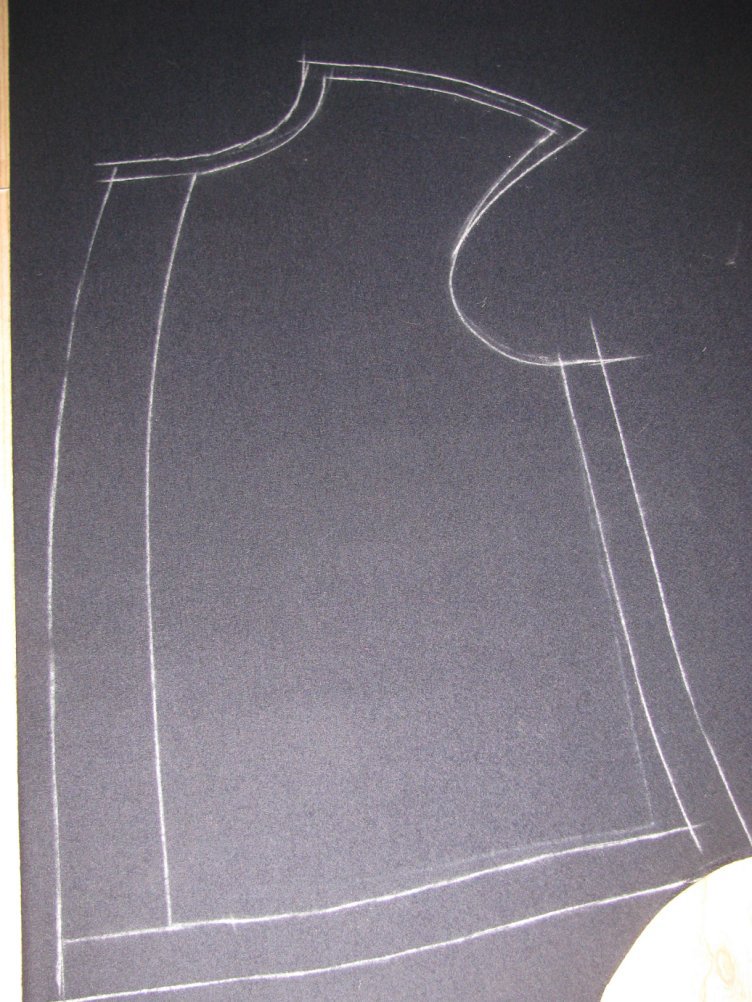
Also, if your pattern has darts, chalk those, and then close the bottom of the dart by drawing a line as if the dart were not there. The edges of the dart represent the seams, not the cutting point.
Also, as you are laying out the forepart, transfer the chest line to the fabric. This will be helpful in aligning the front later on.
Side Body
At the bottom, leave a 1” inlay. At the top, leave a small inlay, 1⁄2 inch at the widest point, tapering down, as shown.
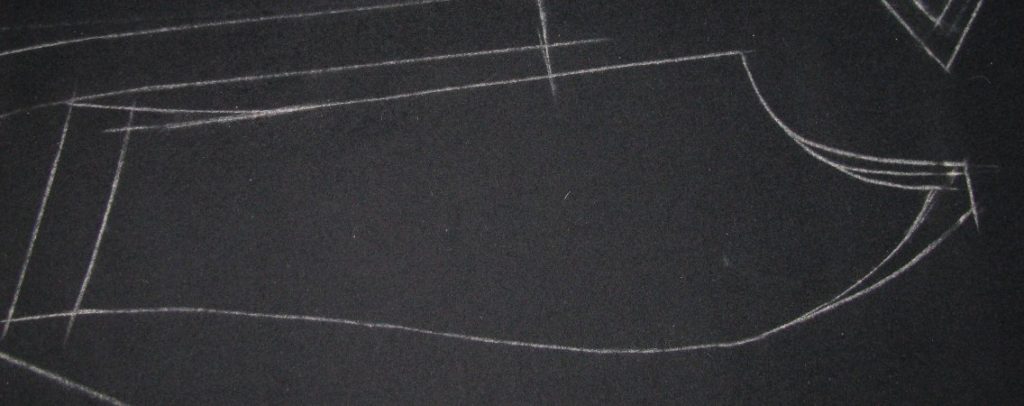
Back
Leave a 1/2” inlay at the top of the neck, as well as down the center back, as shown. At the top of the plait areas, add a 1 inch inlay, extending the height. This is in case you need to raise the back button points up. And finally, at the bottom, leave a 1⁄2” inlay, to allow for any stretching of the back of the skirt that may occur during making up.
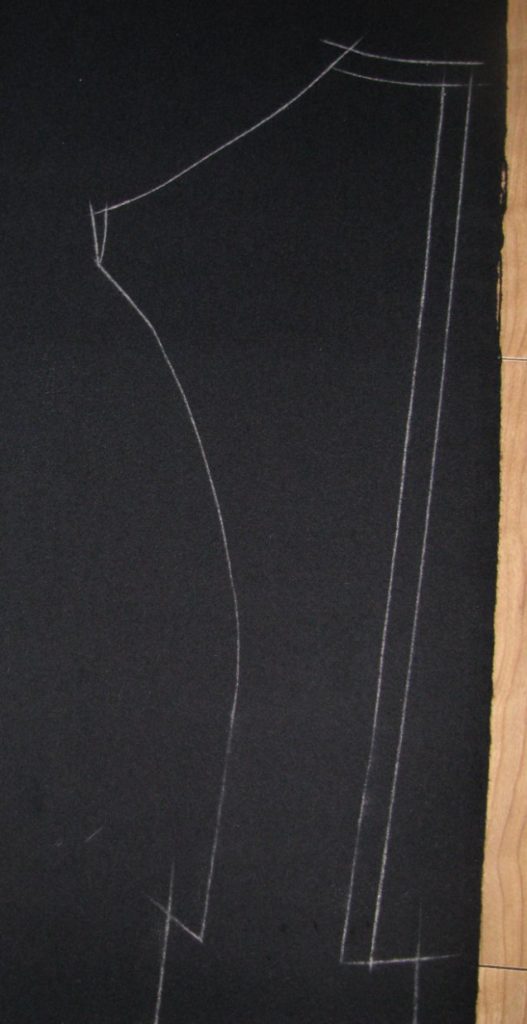
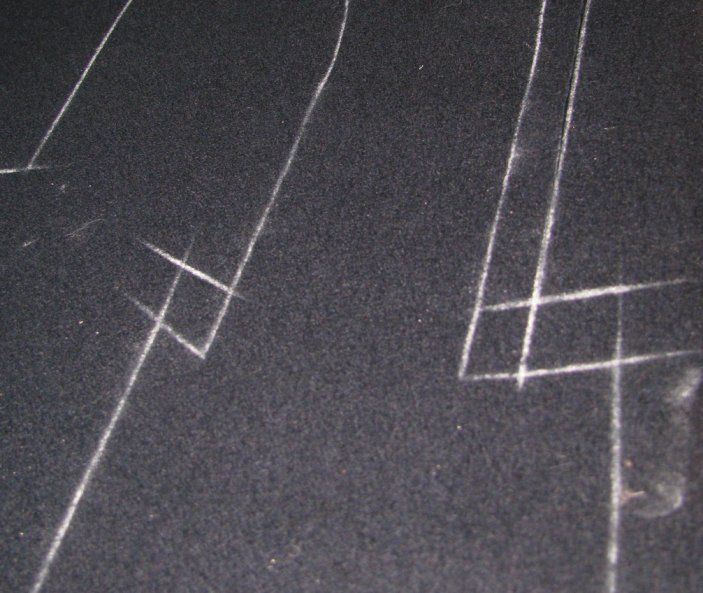
When you’re laying out the back section, make sure the pattern is on the grainline. The center back should be on a slight diagonal when lined up properly.
The Skirt
If you haven’t already accounted for it in your draft, add about 2″ inlay to the front of the skirt. The skirt needs to be able to fold over itself in the front to form the facing, and you need the extra fabric to do that.
There is a special period technique for laying out the skirt pattern, that helps to save fabric. In the majority of cases, the skirt is too wide to fit on the fabric. Don’t turn it sideways or unfold the fabric! Instead, lay the pattern out, with the front of the pattern against the edge of the selvage. The back of the skirt should be hanging off the edge of the skirt. Take a ruler, place it on the edge of the fabric, on top of the pattern, and draw a line on the pattern, indicating the edge of the fabric.
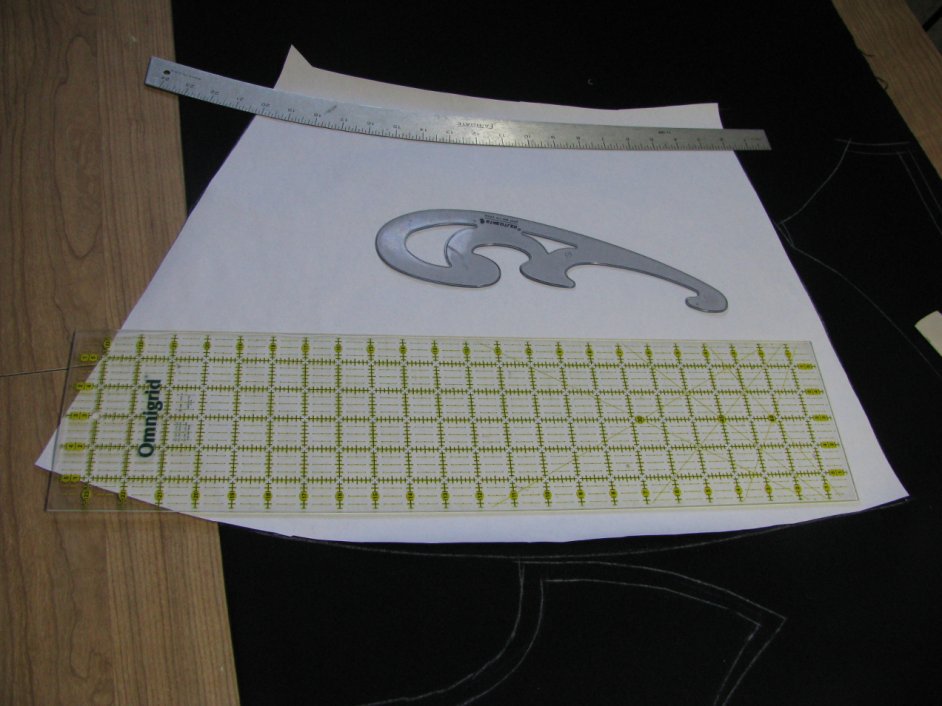
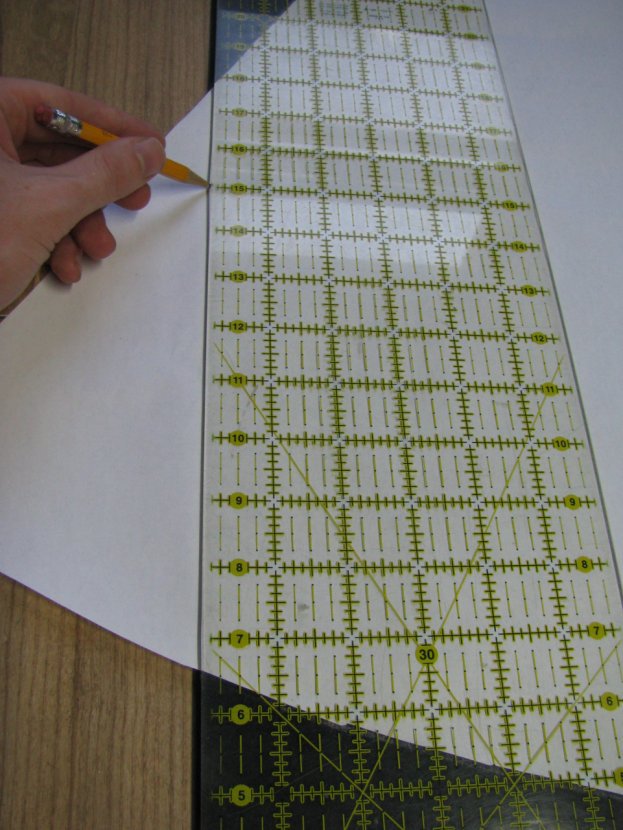
Now, add twice the seam allowance to this small triangle, which would be a 1⁄2 inch in our case (we’re using 1⁄4” seam allowances, remember). Then cut out this small piece of the pattern, and place it elsewhere on the fabric where it will fit. Snug it up into those little spaces you have still. The longest edge, which has the seam allowance, should be on the grain line.
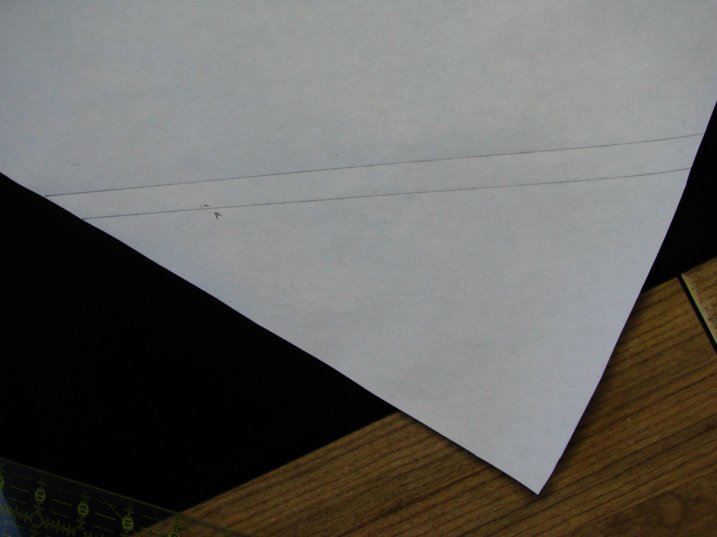
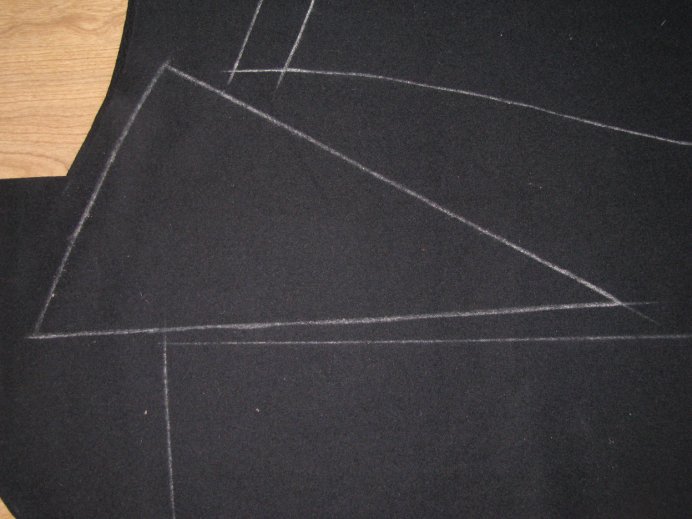
As you are chalking out the skirt, mark the darts, and then mark the tops, as if you had not cut out any darts in the pattern. This is important as you will not cut out the darts. They are just seam lines. Very important.
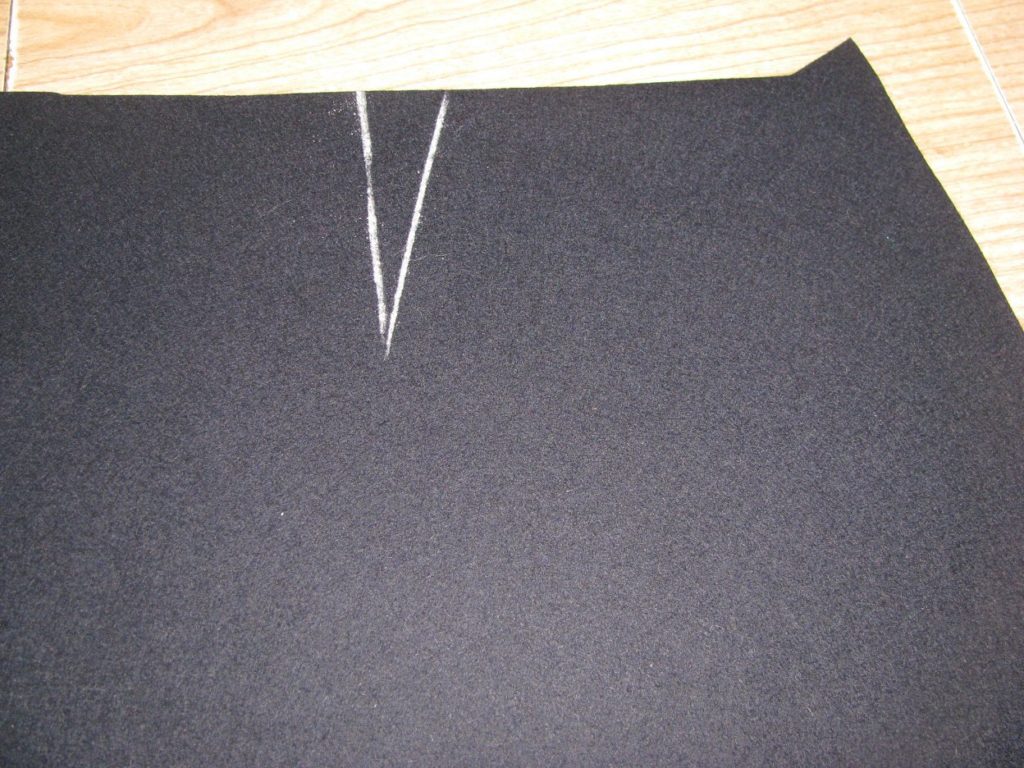
Cutting
This can be a nerve-wracking step for some people, especially if you are using expensive fabric like Hainsworth. It’s potentially hundreds of dollars down the drain if you make a major mistake. I remember reading about a tailor cutting an overcoat with fabric that was about $800 dollars a yard. He was very nervous as well! But if you are careful and check everything twice, you should be okay.
To cut, make sure the shears are held completely straight, not slanting to the left or right. This will help make sure both pieces are cut equally. Cut inside the lines, as the chalk line adds some width to each piece. Make sure you are cutting the inlays with the pieces! After a piece is cut, carefully move the pieces aside, keeping them together as one. This is necessary for the next step. It’s also a good idea to mark an X on the wrong side of each piece, especially if the right and wrong sides are similar in texture.
Tacking
Now, you must mark the inlays more permanently with thread, using tailor tacks. You learned the stitch in the previous module. Do the stitches, cut the threads, separate the pieces slightly, and then cut the stitches in between. I made a video of this process, sent to you in the email. Please view it if you are unsure. Make sure to mark any darts, as well as the chest line on the front of the coat, as well.
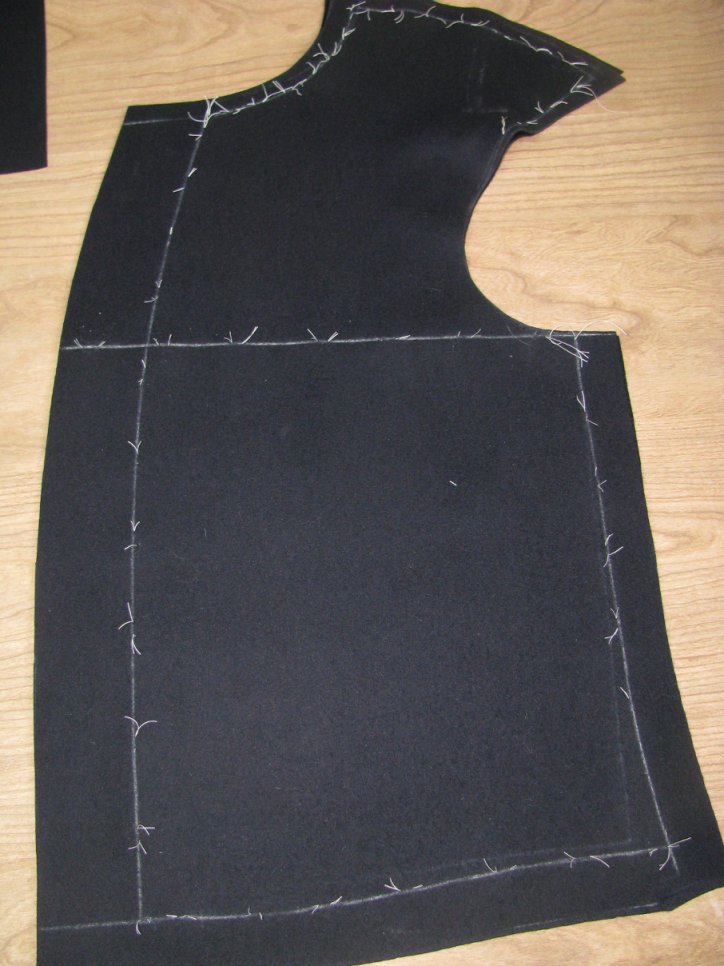
Keep the pieces together, still, for we have some ironwork to do.
Pattern Details
Before starting on the construction of this Federal enlisted frock coat, it’s important to have drafted and fitted a basic frock pattern using the instructions found in my frock coat drafting course.
There are no major changes to the pattern needed, though one thing is you may need to raise the neck point up an inch or so, which you can check for during the fitting of your muslin toile.
Ensure you have the following before continuing:
Forepart
Should be drafted as normal. Add a 1/4″ seam allowance along the top of the shoulder, neck, front, waist, and side seam. No allowance is necessary in the armscye as Devere seems to account for this in his drafts.
Side
Add a 1/4″ seam allowance along the side, bottom, and back seams. No allowance necessary in the armscye.
Back
A 1/4″ is needed around the entire piece except for the armscye. A 1/2″ seam allowance is recommended along the bottom so that it is slightly longer than the skirt piece, to account for any stretching during construction. This can be trimmed off later.
Skirt
Add a 1/4″ seam allowance along the front, waist, and back seams. No seam allowance is necessary along the bottom because you’ll account for the total length in the draft and it’s left as a raw edge anyway. Also accounted for in the draft is an extra 2″ in width along the front edge, that will be turned in and used as a self-facing later on.
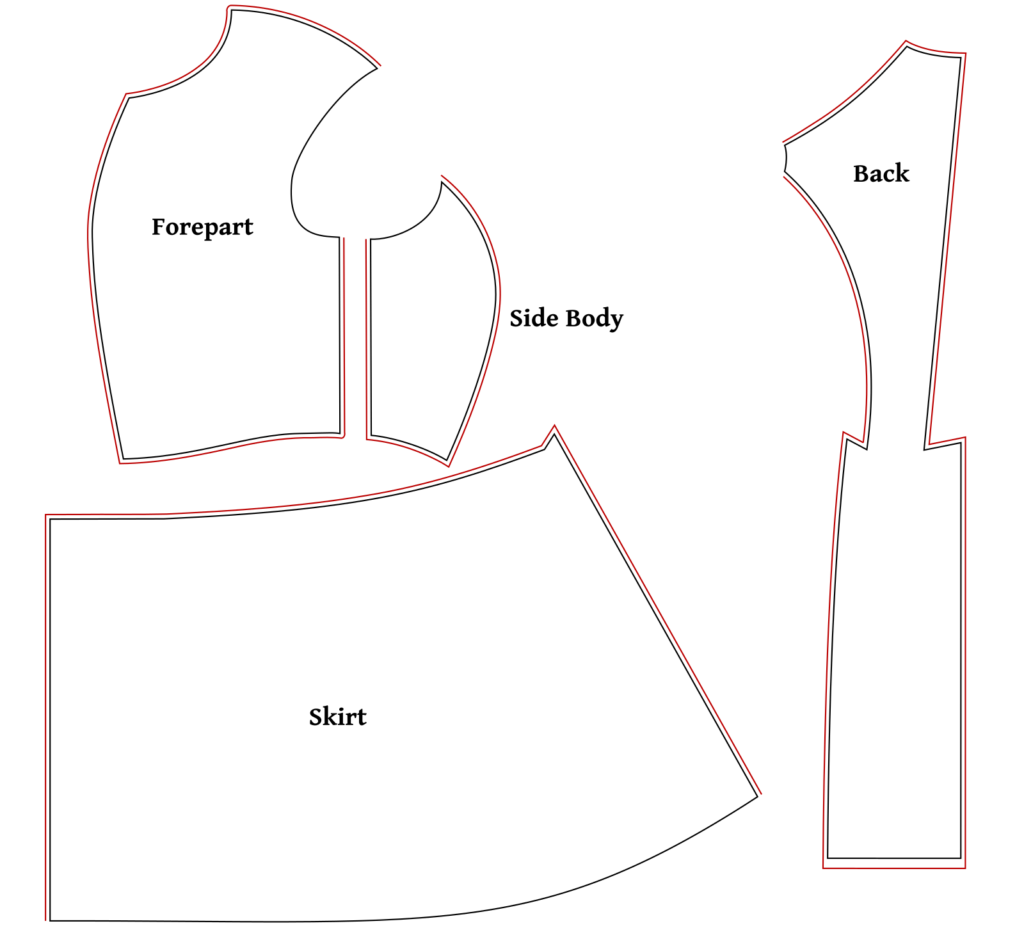
Skirt Fullness
As you are trying on your full completed muslin, check out the back of the skirt. Does it hang straight down, or does it spread apart at the back vent? Also, take a look at the hips. Does the fabric seem a little tight here, giving a pulled or strained look? If any of these cases is true, you will need to add some fullness to the skirts, and perhaps some fishes (darts).
To create more fullness, instead of rising three graduated inches from point 0 in the skirt draft, rise up 4 1⁄2 to even 6 graduated inches, and also give more spring to the back seam, as shown. You can give up to 45 degrees of spring, instead of the standard 30, if desired. This will give the coat plenty of room in the seat area, and the skirt will drape nicely.
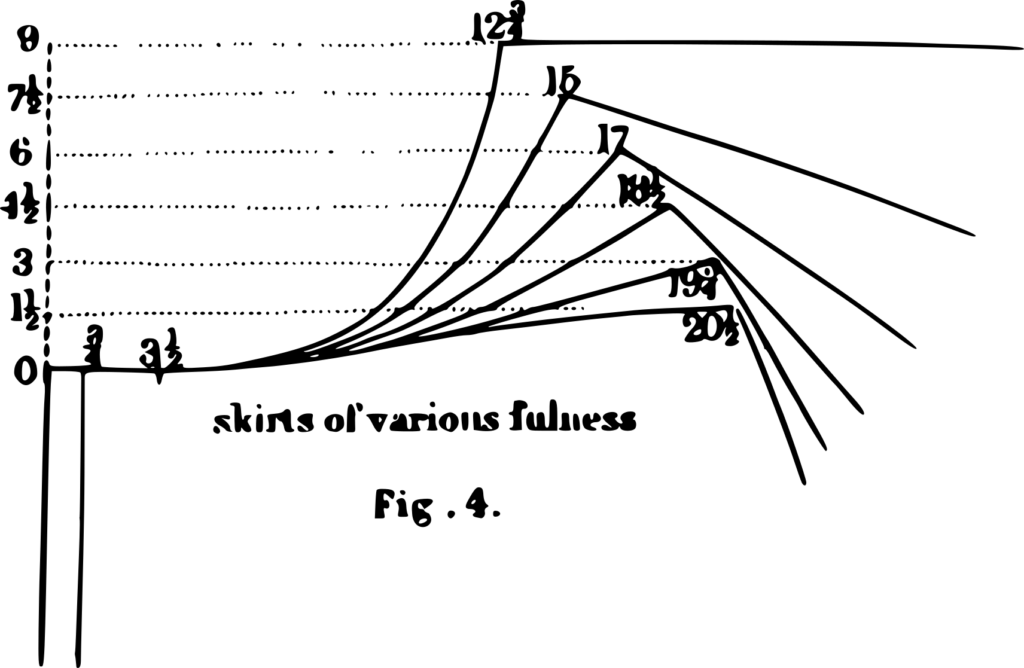
Darts in the Skirt
If you are adding spring to the skirts, as above, it is also advisable to add in one or two small darts, depending on how much fullness you want. The main dart needs to lay directly underneath the where the side seam will be. To figure this out, lay the side piece of your pattern onto the skirt pattern, ‘right sides’ touching.
Mark the point where the seam allowance of the side seam begins. Then measure out to the left 1/2 inch. From the midpoint of those two points, on the skirt waist line, draw a line about 2 to 3 inches long, and connect the three points, creating the main dart.
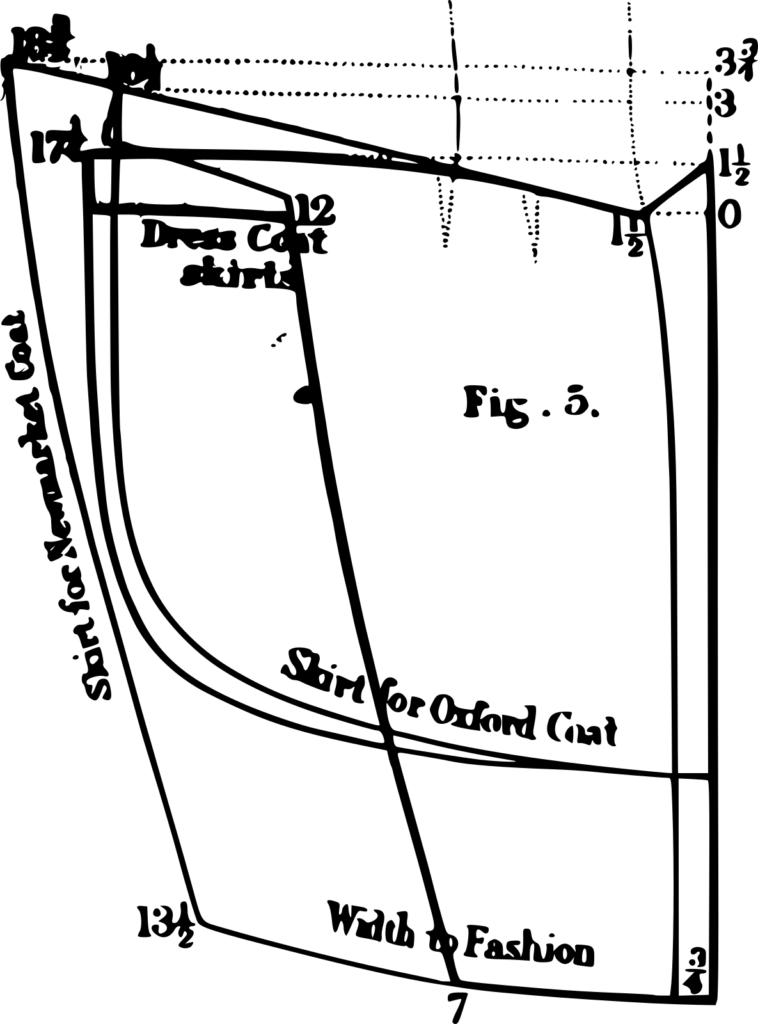
If you wish to have a second dart, it needs to be centered under the side piece, i.e. between the first dart, and the inlay of the skirt where it springs up. Make this dart 1/2 inch wide, and about half an inch shorter than the first dart. After these are drawn on your pattern, they are cut out directly on the lines you just drew, which will be the seam line of the dart. Note that the above diagram gives several skirt styles – feel free to experiment with them.
Drafting the Skirt
To draft the main skirt, start by drafting a vertical line on the left side of the paper. Mark point 0 near the top, for the placement of the waist seam.
Rise up 3 graduated inches, and mark that point for the fullness of the skirt.
Finally, measure down 3/4 common inches less than the length you used for the back. In my case, I’m using 17 3/4 inches.
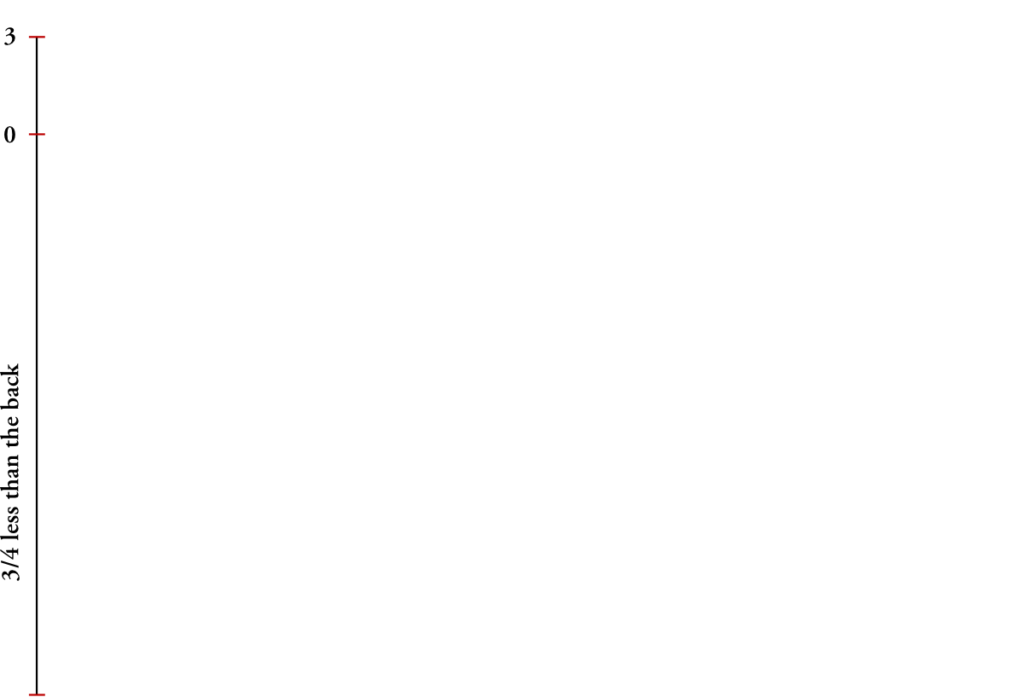
Square across from the three points. The top and bottom lines aren’s measured at this point, but measure 5 graduated inches on the line from point 0. This line gives us room for the Lapel, the turn-in (facing), and one inch extra in case of error.
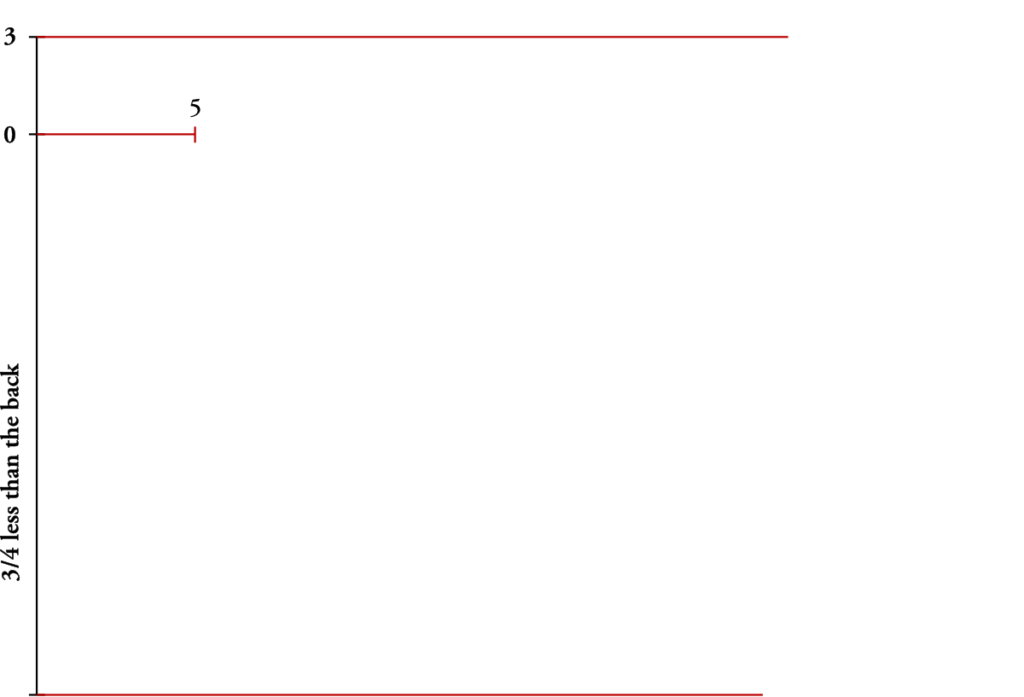
Measure from point 5 up to the construction line from point 3, the waist to measure (half the full waist, remember).
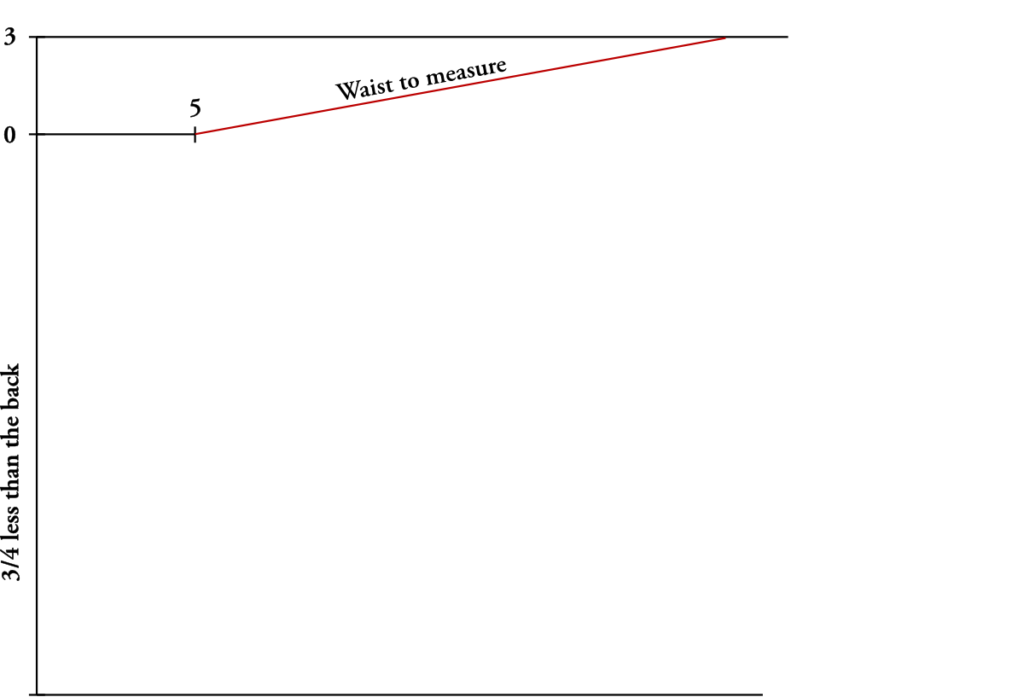
At the point where the waist line meets the construction line, draw a vertical construction line as shown. Length is not important, you just need to be able to register your protractor against the line.
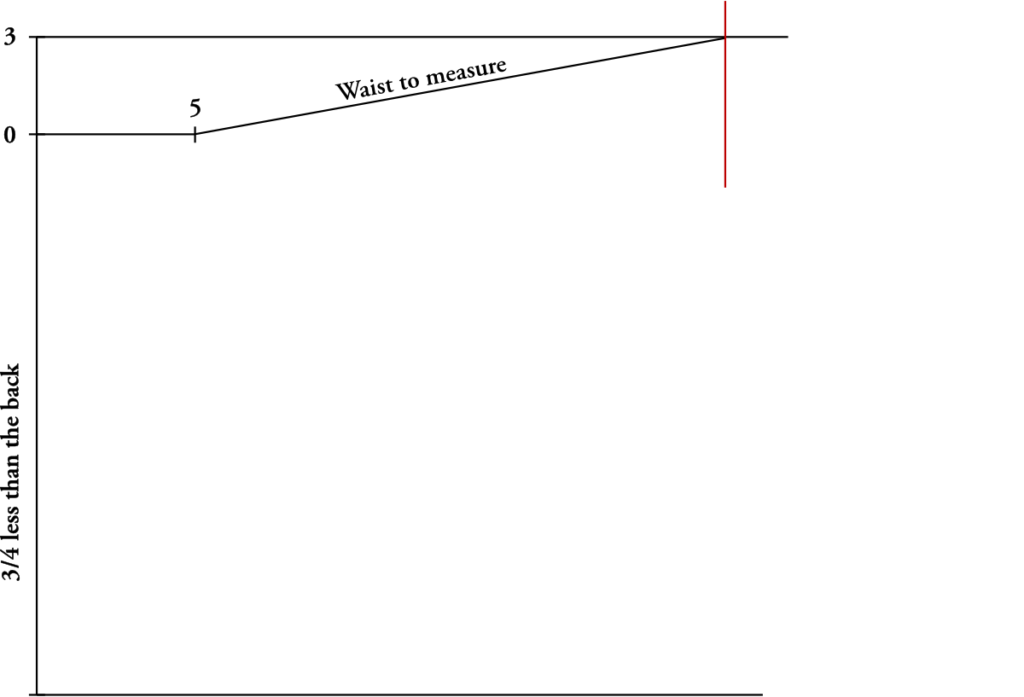
Measure a 30 Degree angle using your quilters square or protractor, and draw a line equal to the length of the back skirt – in my case 18 inches.
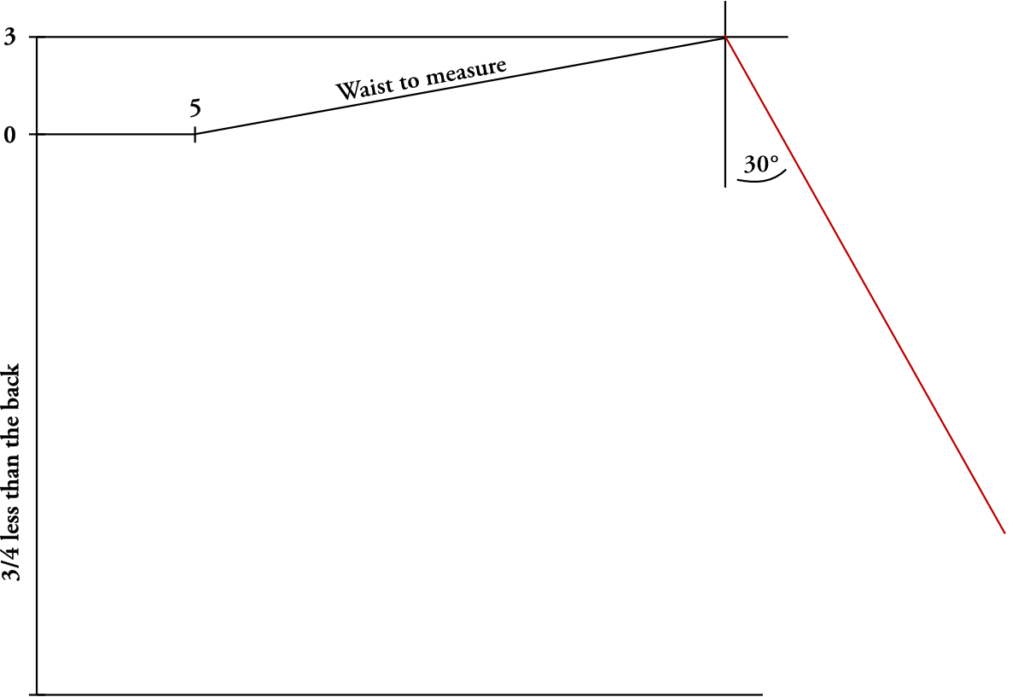
Draw the bottom of the skirt, staying with the construction line for about a third of the distance, then gradually curving up to meet the side point.
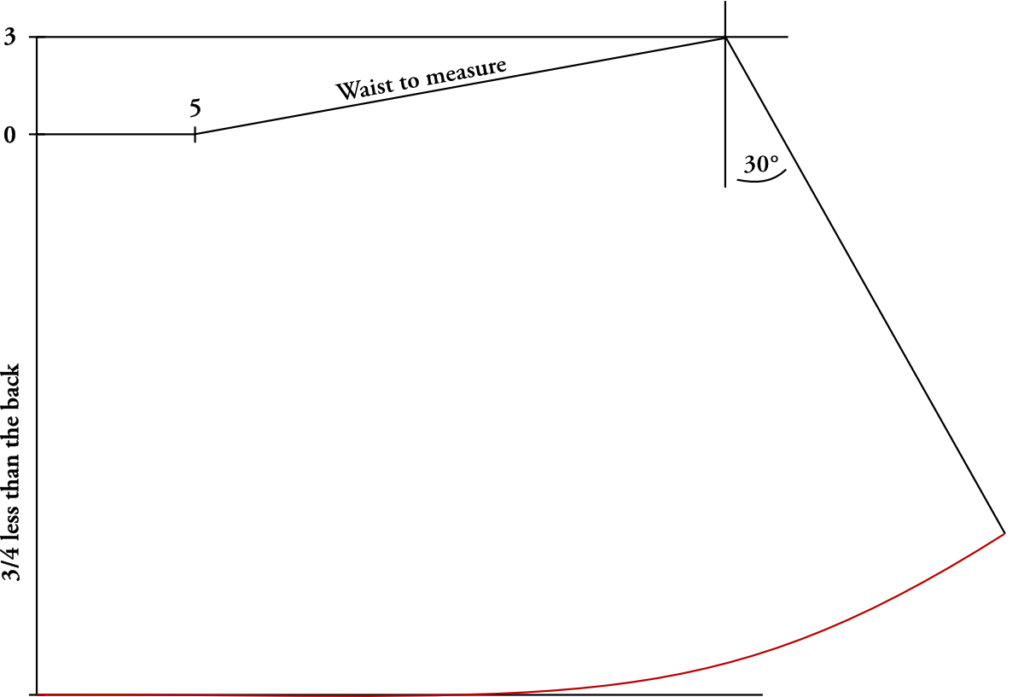
The waistline is now curved as shown, dipping about 3/4″ from the waist construction line.
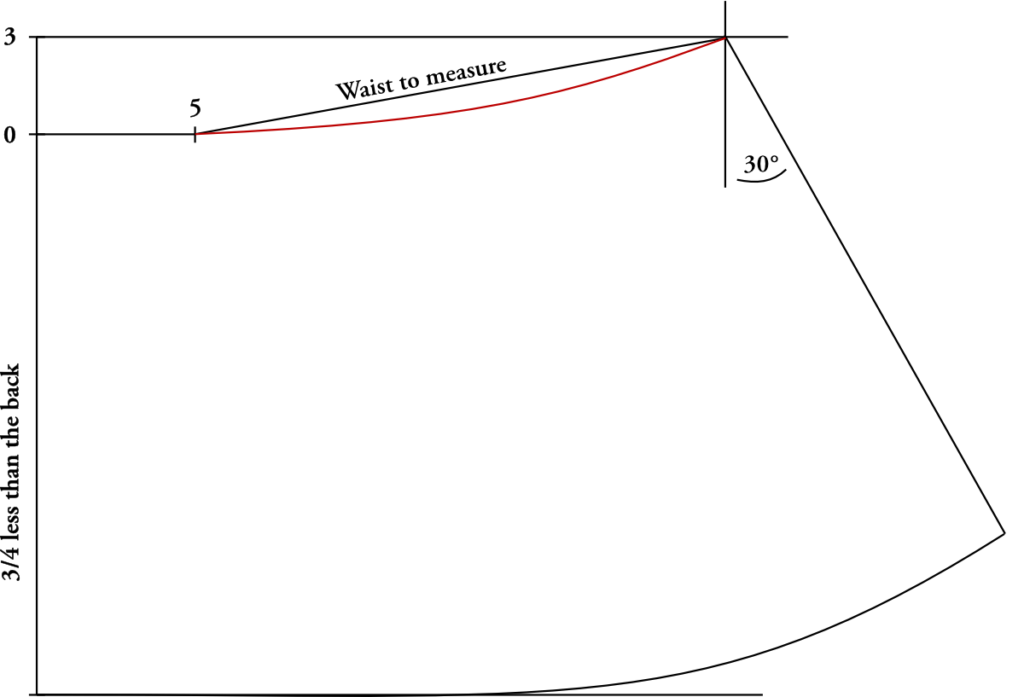
On the side seam, an inlay is added for the skirt plate. This should be 7/8″ wide to match the back skirt, and spring up at the top.
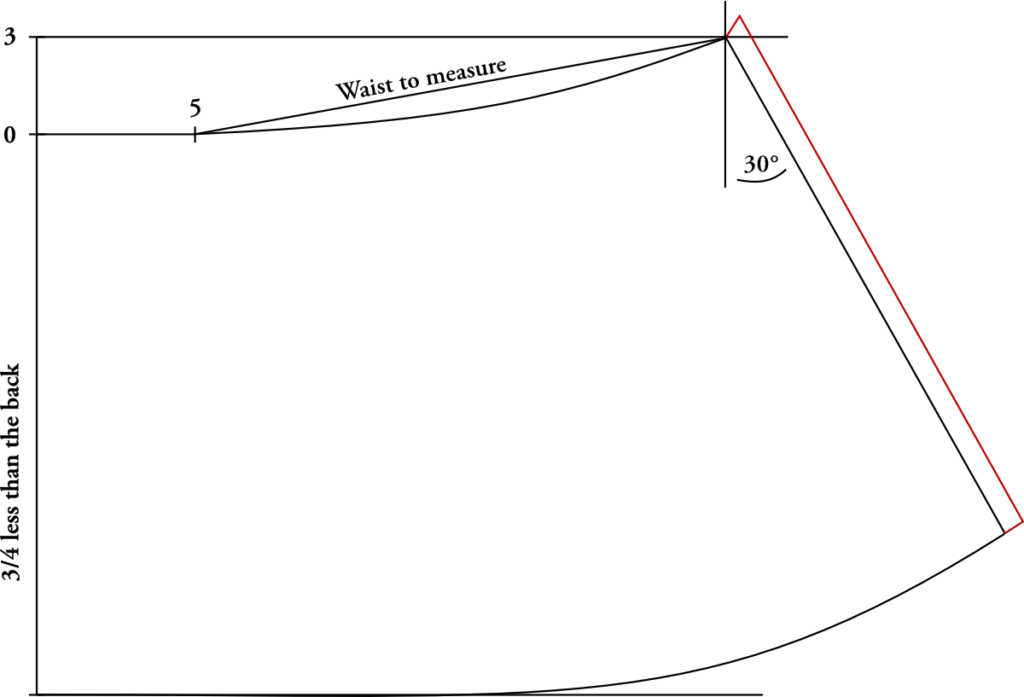
Finally, a 1/4 inch seam allowance is added to the top. The skirt draft is complete.
The Back Skirt
It is now time to draft the skirts, completing the draft of the coat body. To begin, make sure you have plenty of space on your paper, as the skirt can get quite large. We will start with completing the back skirt, as it’s length determines the length of the main skirt.
I generally have the skirt fall to two or three inches above the knee, but this is a matter of preference and following the styles of the period you are reproducing.
The Back Skirt
Begin by tracing the back piece onto a fresh sheet of paper, making sure you have room underneath to draft the skirt. Orienting the pattern sideways is a good way to ensure this. Also copy the construction line, and extend it, as shown. If you subtract the “Length of Back to Hip Buttons” from “Length to Bottom of Skirt”, you will find how long to extend this construction line. In the sample draft, I am assuming a length of 18 inches. Measure from the waist construction line (that is now vertical in the diagram).
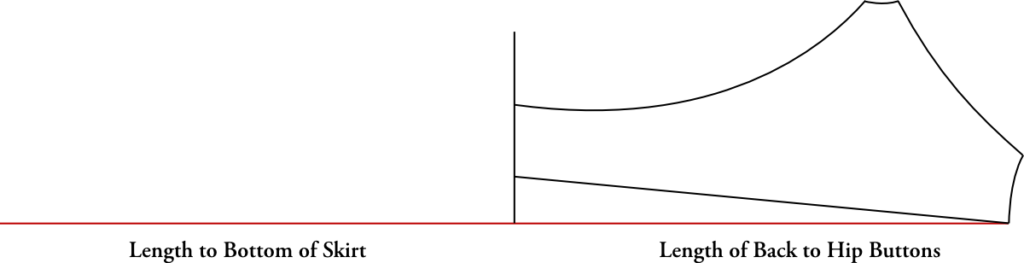
Next, measure 7/8″ graduated inches on the waistline, and mark that as shown for the plait. Now measure the entire distance from that mark, down the waistline to the horizontal construction line. Keep a note of that for the next step.
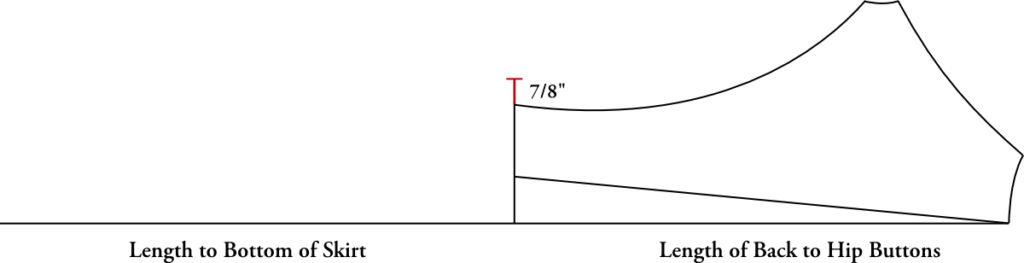
At the bottom of the skirt, the length should be 3/4″ graduated inches wider than at the waist line, and is drawn square with the main construction line.
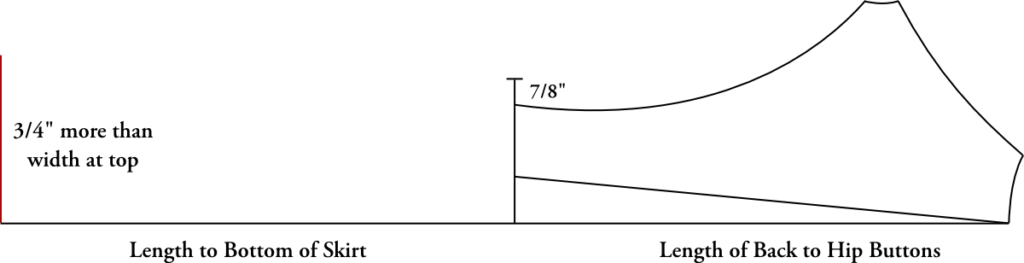
Draw a straight line representing the side seam, extending about a half inch past the waistline, as shown.
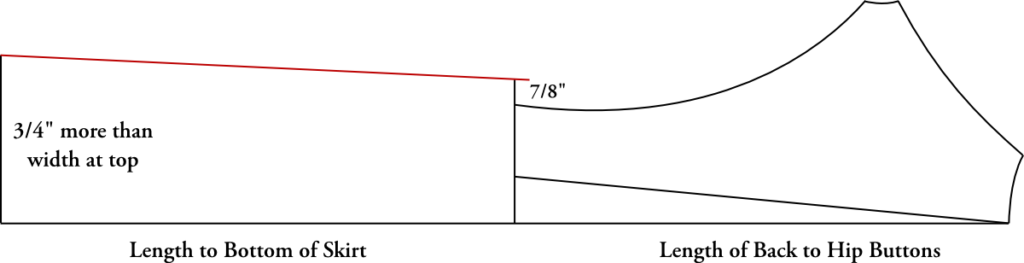
Draw two short lines ‘springing out’ from the waistline as shown.
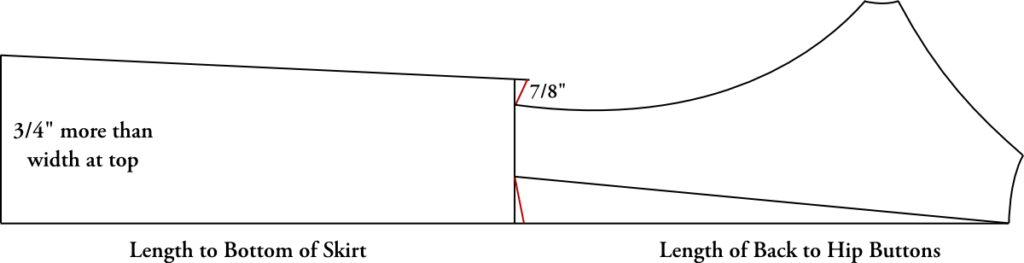
Here is the completed draft of the back. Note no seam allowances have been added yet. An optional step is to shape the center-back seam of the skirt into a slight curve – 1/4″ depth at the fullest point. This will allow you to give some extra shape in the skirt later on.
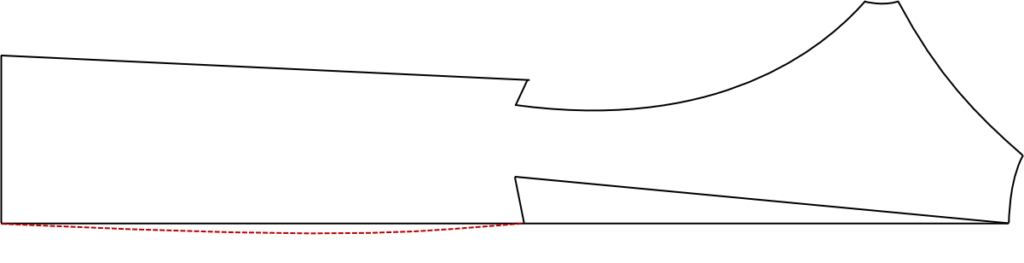