Month: October 2019
The Skeleton Baste
Darts
On the wrong sides, on both the skirts and forepart, mark the darts in chalk, carefully tracing the thread tacks you put in. If you don’t have any darts, then you may skip this step. Next, baste the darts, starting with a couple of stitches in place to hold, then using the basting stitch. Make sure the stitching aligns with the chalk lines on both sides of the dart as you sew.
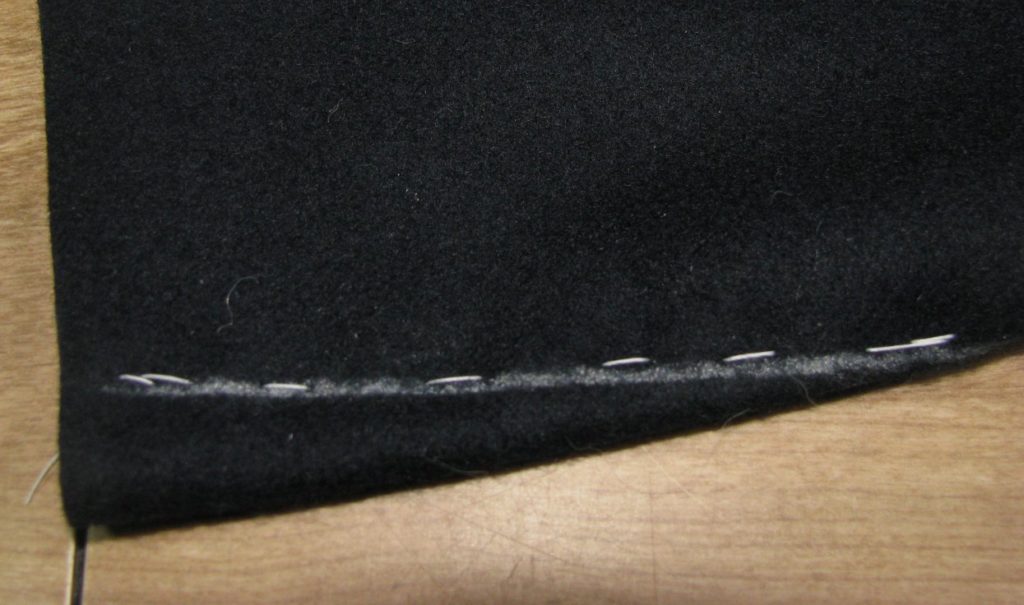
The Skeleton Baste
At this point, you will baste together all pieces of the garment by hand, to test for fit one last time. Normally, in a skeleton baste, the tailor would baste in the padding, linings, and collar as well. Since you have yet to learn how to construct these pieces, we will forgo them for now. On your next project, you may put them in.
This is done just the same way as for the full muslin, except to not clip any seams. Treat the marking threads as the edge of the cloth, the inlays are there in case you need room.
When you are basting together the center back seam, sew from the top to 1/4″ inch past the bottom of the inlays at the waist seam.
Then you can get a good idea if the opening is at the correct height or not. Press each seam as you go, but only lightly. And when sewing each seam, stop when you hit the marking threads. You don’t want to include the inlays in the seam, as they are not technically part of the coat at this point.
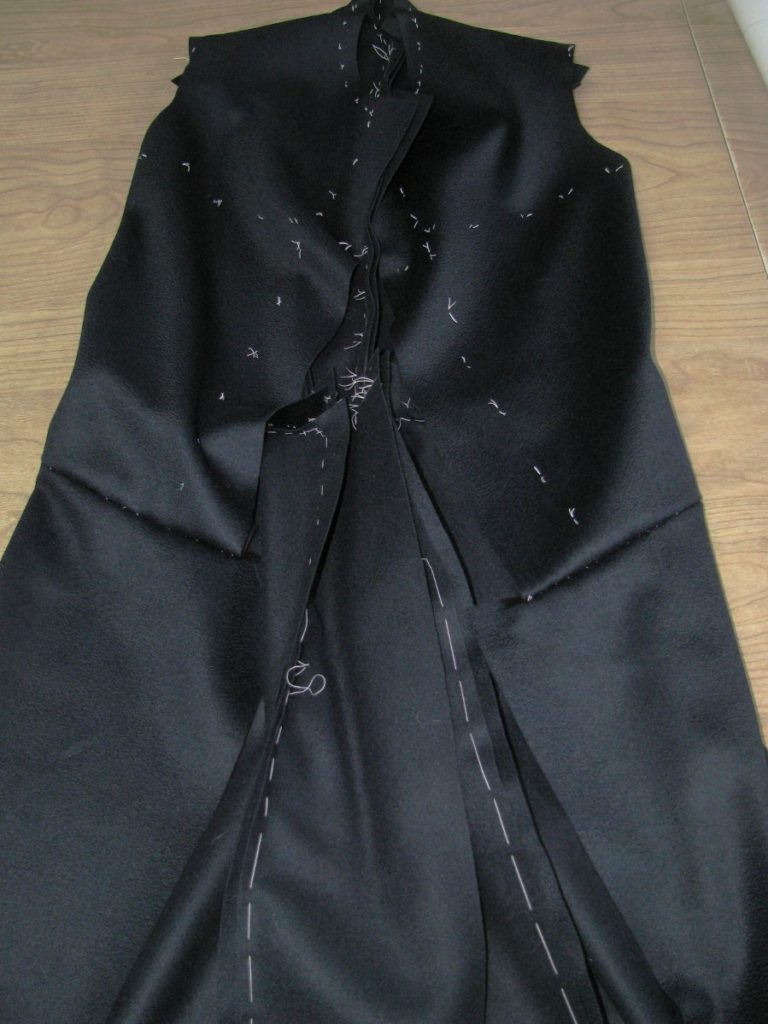
The Skirt
Now we will actually commence construction, starting with the skirt. Find the small triangular pieces you cut. Also be sure you have separated the two skirt pieces by cutting carefully on the fold line. Next, figure out which side is longest on the triangular piece, and line it up, right sides together, to the skirt piece. It may take some fiddling to figure out which piece goes where, but I assure you, they will line up, providing you added double the seam allowance when cutting.
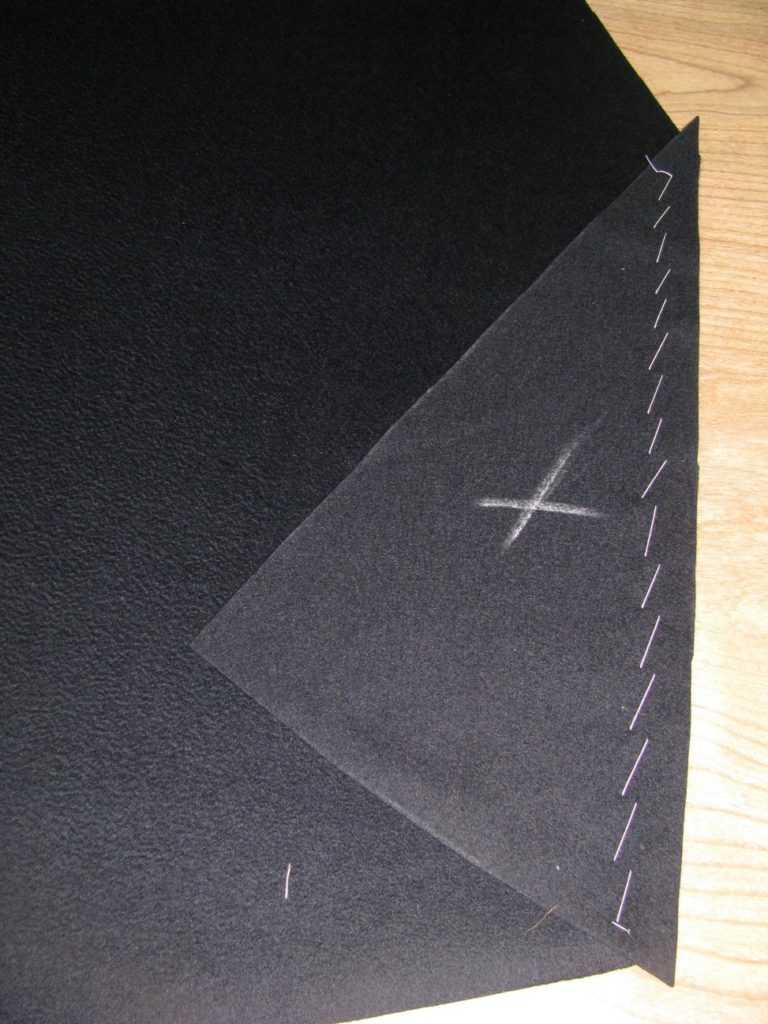
After they are lined up, baste together carefully, making sure there is no fullness on either side. Then, sew, using a 1⁄4” seam allowance, with either a backstitch, or machine stitch. If using the sewing machine, I recommend about 12 stitches per inch. Remember that machines of the period could not so backwards, so no back-tacking! Instead, leave about 4 inches of extra thread at the ends, pull the threads to one side, and tie in a secure knot. Remove the basting stitches.
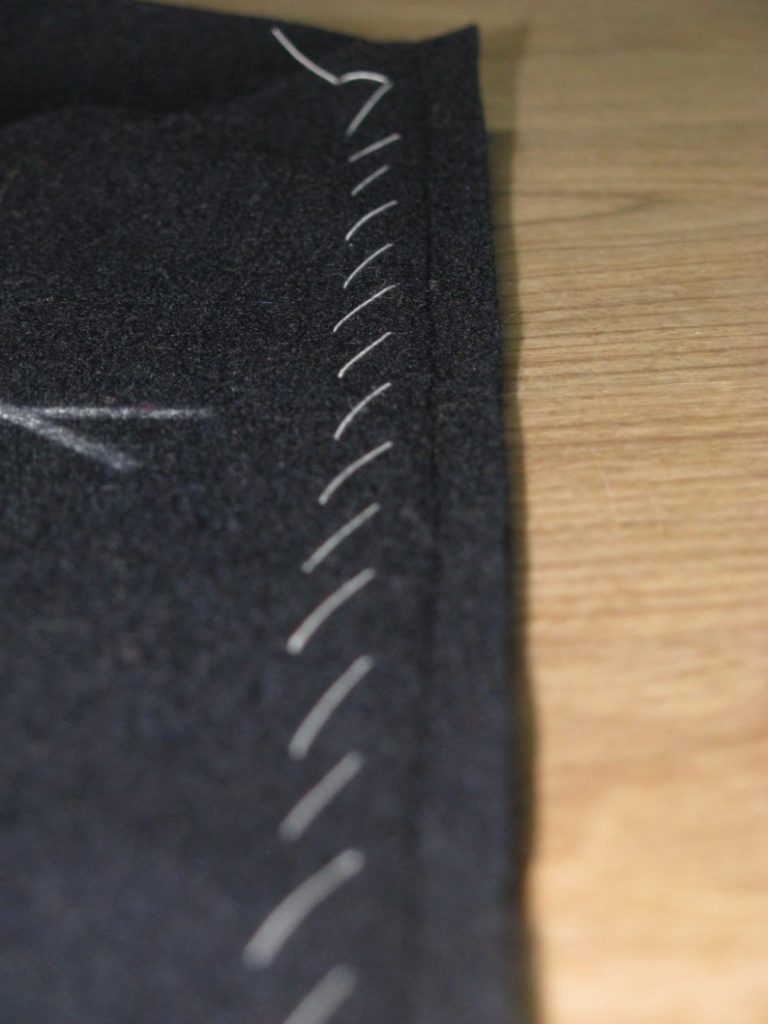
Now, press the seam, using the following technique. After pressing, snip off the little triangular pieces that form at either end of the seam allowance.
Pressing Technique and Opening Seams.
The first rule of pressing is to not move the iron up and down the seam, as this has a tendency to stretch the seam and throw it out of shape. Begin by laying the pieces, still right sides together, on the ironing board. Go over with a hot iron, with steam, and press the seam. Flip both pieces over, and repeat this process. What this is doing is setting the stitches, which will give us a tighter press of the seam.
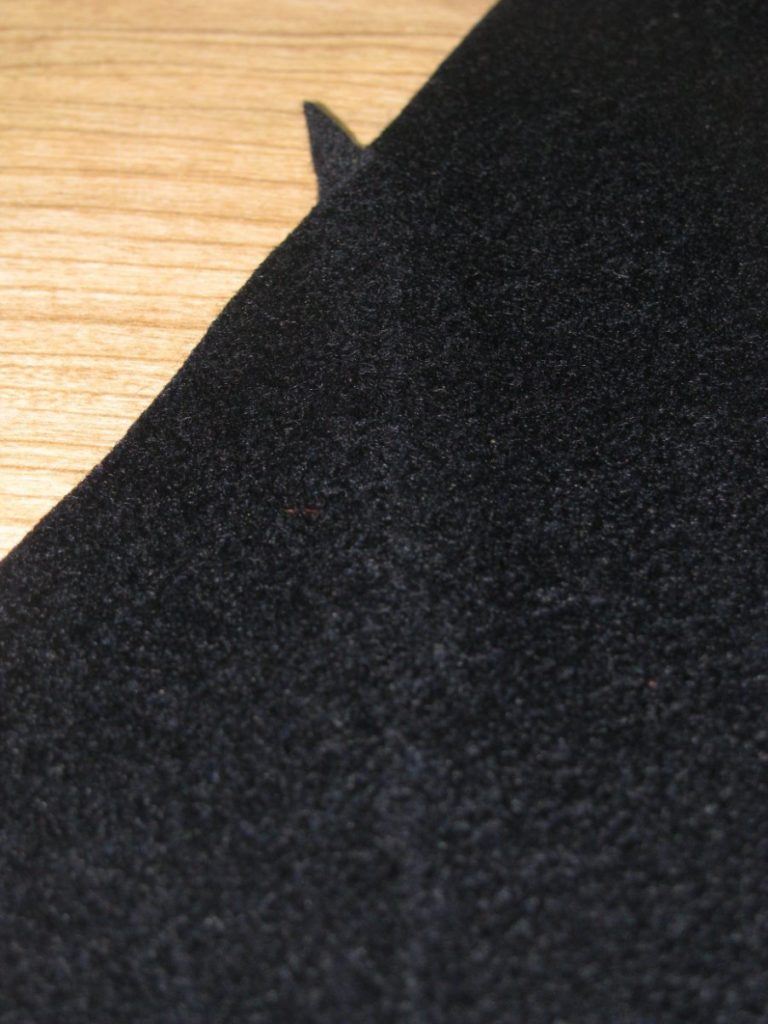
Next, open up the seam from the wrong side, and press the seam open. Take your time, and do just a small section at a time. Hold the iron for a few moments, remove, then press with a heavy goose iron, or clapper, to really set the seam. We’re trying to avoid that rolled look to the seams that one so often finds, especially in coats made of heavy fabric.
Turn the fabric over to the right side. Using a scrap of fabric as a press cloth, go over the seam again, with the steam iron, then the clapper or goose iron. When using the clapper, you may want to put the fabric seam on a hard surface such as a piece of wood. Make sure to use a press cloth whenever pressing the right sides of fabric, to prevent shine and imprinting the shape of the iron.
If you have the problem of the seam allowances showing through to the right side, press the seams with a piece of cardstock underneath each of the seam allowances.
Ironwork
Ironwork seems very intimidating to most people, as very few tailors, save the bespoke tailors on Savile Row, and some others, still practice it. The style of ironwork done in the period is almost unheard of. I know it was one aspect of tailoring that took me years to figure out. I didn’t have anyone to just show me though, and had to learn it through books and lots of practice.
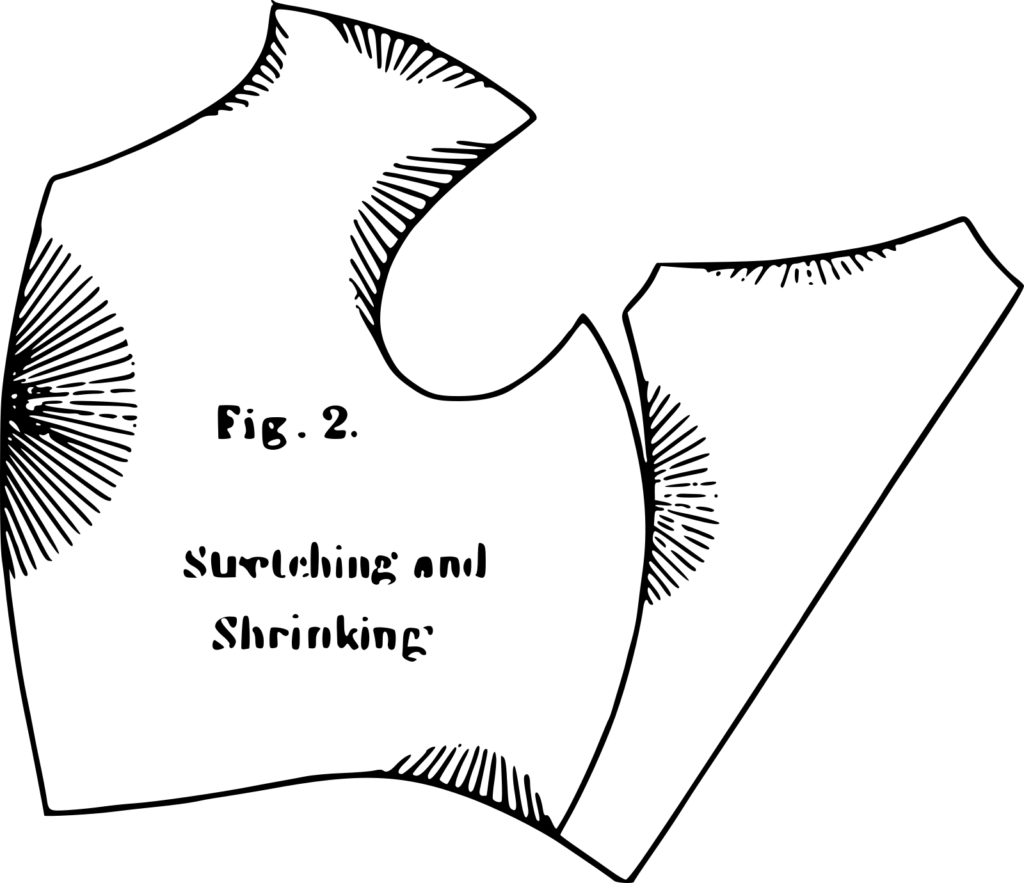
It’s a good idea to do most of the stretching on your muslin wrapper. Even though it will not stay permanently, it will give you a better idea of how the final fit will be. Shrinking will not work on the cotton muslin, so you’ll have to train your eye to recognize the adjustments needed.
If you skip the ironwork, you’ll end up with long vertical folds near the shoulder and front of scye, and the chest will not be full enough to contain the padding we will be inserting. The front of the coat will drape open, a problem often seen.
The following text comes from Practical Tailoring, The Art and Craft Simply Explained for the Student and Apprentice, by J. E. Liberty. He gives the clearest instructions for ironwork I have found yet.
Shrinking to Shape.
The material should be laid on the board and a little water applied with the fingers of the left hand, the part to be shrunk being nearest the worker. Place the iron first at the back of the material at a part where the shaping will begin, and working it from right to left and towards the front, work round the part being shrunk with the fingers of the left hand while the iron is moving. It will be seen that the shrunk section probably has one or two small pleats formed by trying to shrink too much at once, and these should be smoothed out by putting a little water on the creases and passing the iron over them. It should not be necessary to go over the shrunk part more than twice to obtain the shape required, as too much shape will not hold in the cloth, and should be taken out be seams in the cutting of the garment.
Stretching.
In stretching the process is similar to that used in shrinking, except that the material is worked out instead of in. It should be remembered that in shrinking into shape, the material will, after a time, return to its normal shape, but with stretching, it seldom, if ever, does ; also that to obtain length by stretching naturally reduces the width, and this must be allowed for in cutting.
Forepart
We will begin our ironwork by taking up the forepart, and stretching the front of the armscye. The total amount of stretching should be about 3⁄4 of an inch. Hold the fabric at the shoulder point, and put pressure down with the iron, stretching as you go. Both layers of fabric should be stretched at the same time, to ensure they are stretched equally.
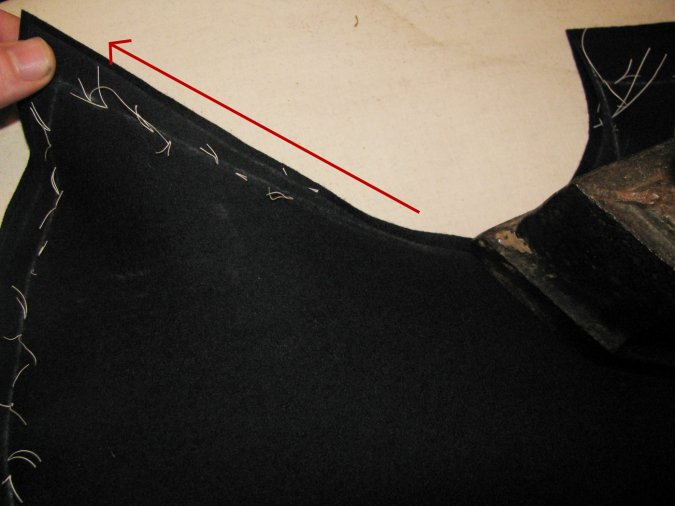
Next, stretch the shoulder seam, about a quarter inch total. This is one of those steps not explained in any book, but learned only through practice and critical thinking. If you measure the distance from the edge of the shoulder seam, and compare that to the edge of the back shoulder seam, you will see they are equal. If you add a seam allowance to that, there is no problem getting them to line up. This is what the majority of produced patterns do. Remember, we did not add a seam allowance, so instead, measure the distance of both seams, 1/4” from the edge. You’ll find that the back seam is 1⁄2” to 3⁄4” longer. By stretching the front shoulder seam, and shrinking the back shoulder seam, this distance is reduced, and the seams line up much closer. Now, stretch the hollow point of the neck seam only, about a 1/4” as well. This gives a little more shape to the shoulder area, and helps the neck hug the body more closely. Stretch the side seam as well, about 1/4”. This is not shown by Devere, but necessary to get the seam to line up with the side piece.
The center front needs to be shrunk, now. Notice how the center front is curved. You will need to shrink this carefully so that it is turned almost into a straight line. Please see the video for a demonstration of this and the other techniques.
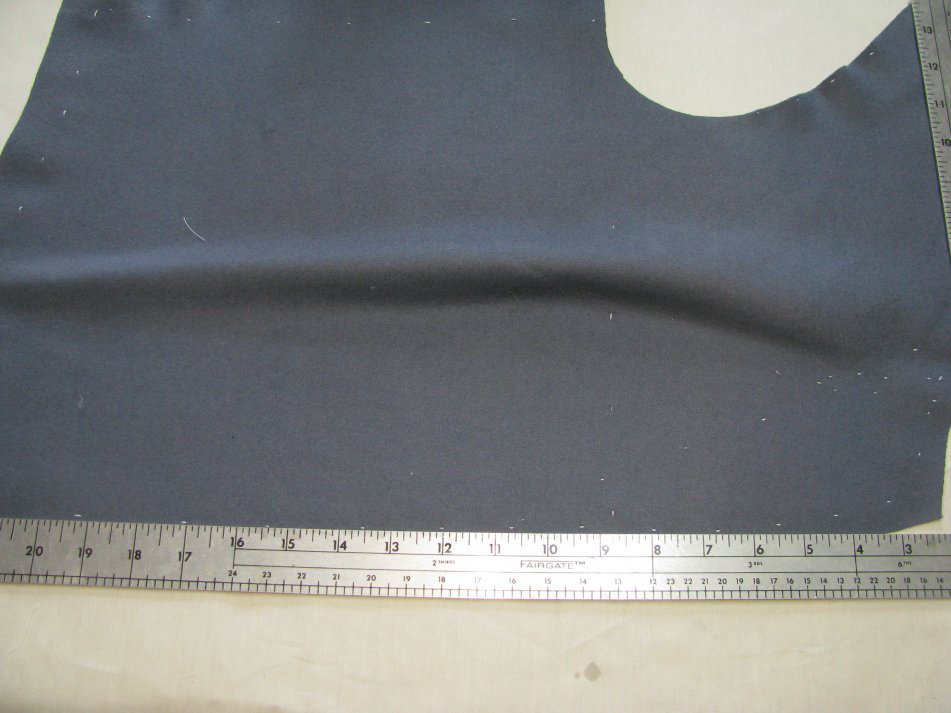
Notice how the fullness is visibly in the center of the forepart now.

This will also leave room for the padding later on. The shoulder area should have a lot of shape to it as well.
Sidebody
The goal of the ironwork on the side piece, is mainly to impart more shape into the coat. In this step you are basically folding the fabric over, and stretching the seams, while shrinking the middle. It will take some practice, but you will get it. Try not to crease the middle of the piece as you’re doing the ironwork, as it’s hard to get rid of.

The following is a description from The Art of Garment Making, by Phillip Dellafera.
Fold the sidebodies as indicated, then proceed by shrinking away all the ‘loose’ material that will show itself at the waist. This work must be done carefully, until a nice hollow is formed at the waist; it will then be seen that the outer edges will have become slightly stretched. This is exactly what is required, and it will be found that a well-defined waist is obtained by adopting this method.
Sometimes this effect is obtained by slightly stretching the seams in a downward direction only. This, of course, will certainly help to get the desired shape; but the best plan is to shrink the centre of the side body, which will automatically give the extra length to the seams.
Also, stretch the bottom of the side piece slightly, again about 1⁄4”.
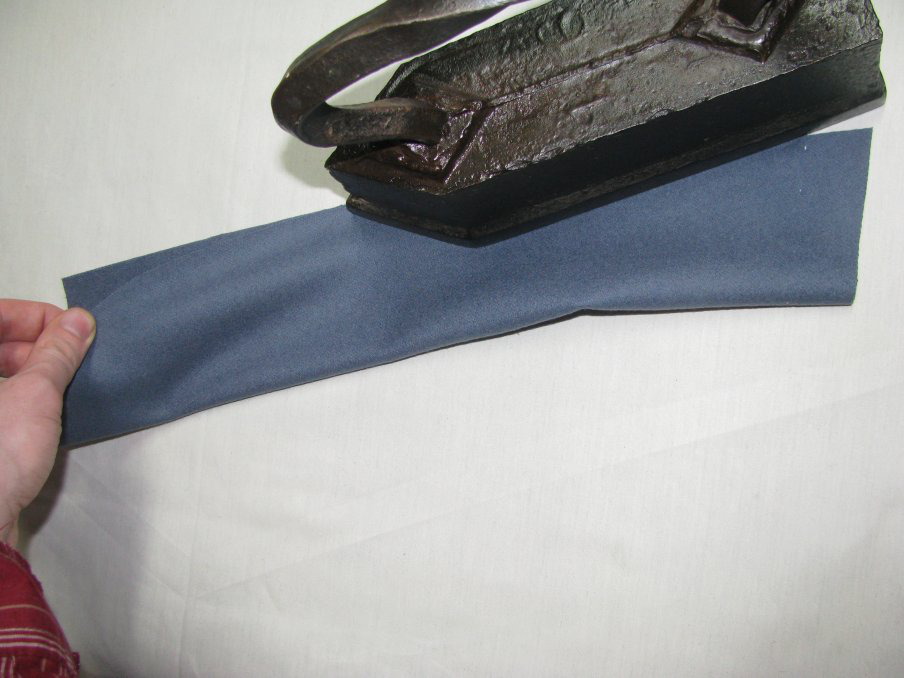
Here’s a video of the entire process showing the ironwork I usually do on a frock coat.
Inlays
If you are not confident in the fit of your pattern, or perhaps just want some extra security before you cut into your expensive fabric, it’s a good idea to add inlays – little extra bits of fabric in strategic areas – to give you extra room to work with if necessary.
Add inlays to each piece as follows. As you are learning to do this, measure out each inlay carefully. With experience, you’ll eventually be able to do this freehand, and anticipate how much inlay to add
based on the figure you are fitting.
Forepart
At the side and bottom, leave 1” inlays. At the center front, leave 2 inches. This is very important, and if you forget, the coat will not button. At the neck and shoulder, leave 1⁄2 inch, and at the armscye, start at half an inch, tapering to nothing about halfway down the front of the scye.
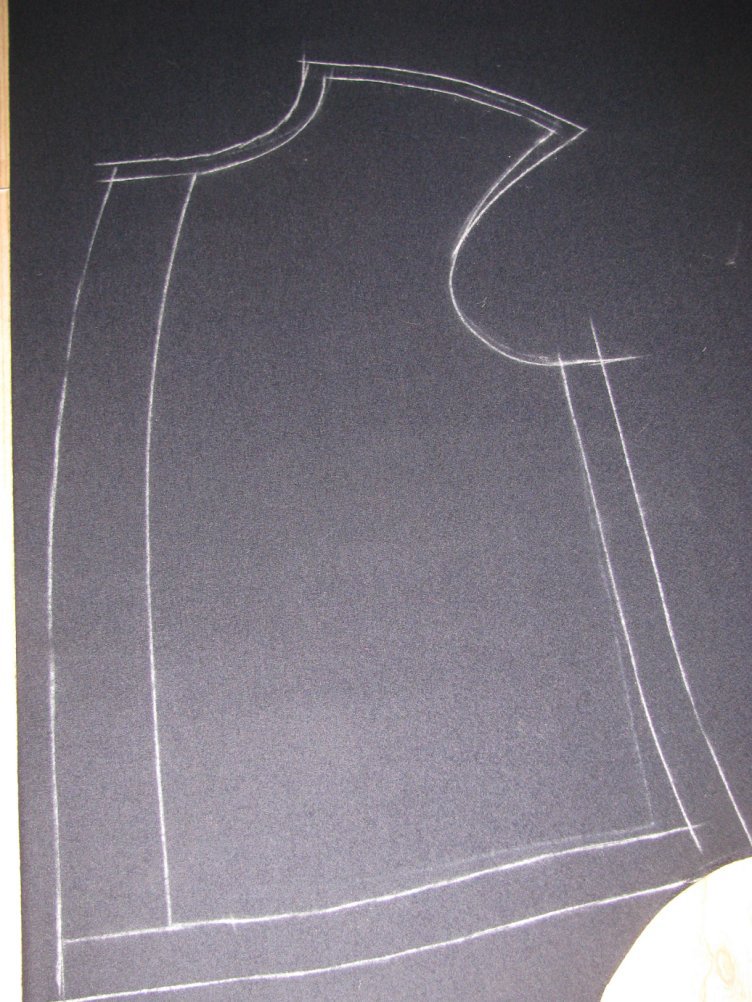
Also, if your pattern has darts, chalk those, and then close the bottom of the dart by drawing a line as if the dart were not there. The edges of the dart represent the seams, not the cutting point.
Also, as you are laying out the forepart, transfer the chest line to the fabric. This will be helpful in aligning the front later on.
Side Body
At the bottom, leave a 1” inlay. At the top, leave a small inlay, 1⁄2 inch at the widest point, tapering down, as shown.
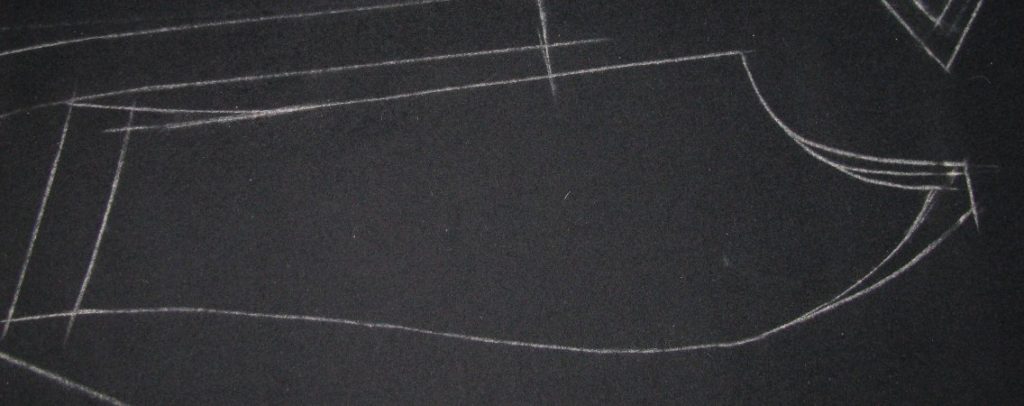
Back
Leave a 1/2” inlay at the top of the neck, as well as down the center back, as shown. At the top of the plait areas, add a 1 inch inlay, extending the height. This is in case you need to raise the back button points up. And finally, at the bottom, leave a 1⁄2” inlay, to allow for any stretching of the back of the skirt that may occur during making up.
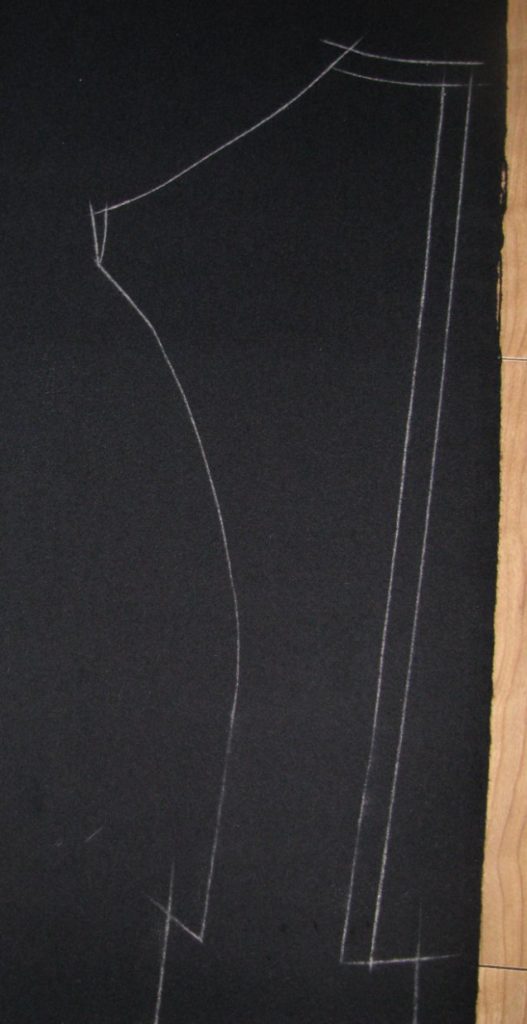
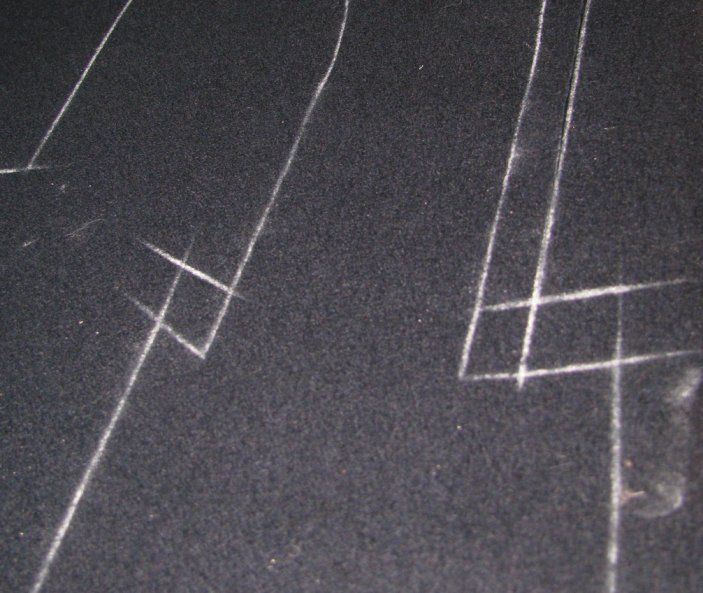
When you’re laying out the back section, make sure the pattern is on the grainline. The center back should be on a slight diagonal when lined up properly.
The Skirt
If you haven’t already accounted for it in your draft, add about 2″ inlay to the front of the skirt. The skirt needs to be able to fold over itself in the front to form the facing, and you need the extra fabric to do that.
There is a special period technique for laying out the skirt pattern, that helps to save fabric. In the majority of cases, the skirt is too wide to fit on the fabric. Don’t turn it sideways or unfold the fabric! Instead, lay the pattern out, with the front of the pattern against the edge of the selvage. The back of the skirt should be hanging off the edge of the skirt. Take a ruler, place it on the edge of the fabric, on top of the pattern, and draw a line on the pattern, indicating the edge of the fabric.
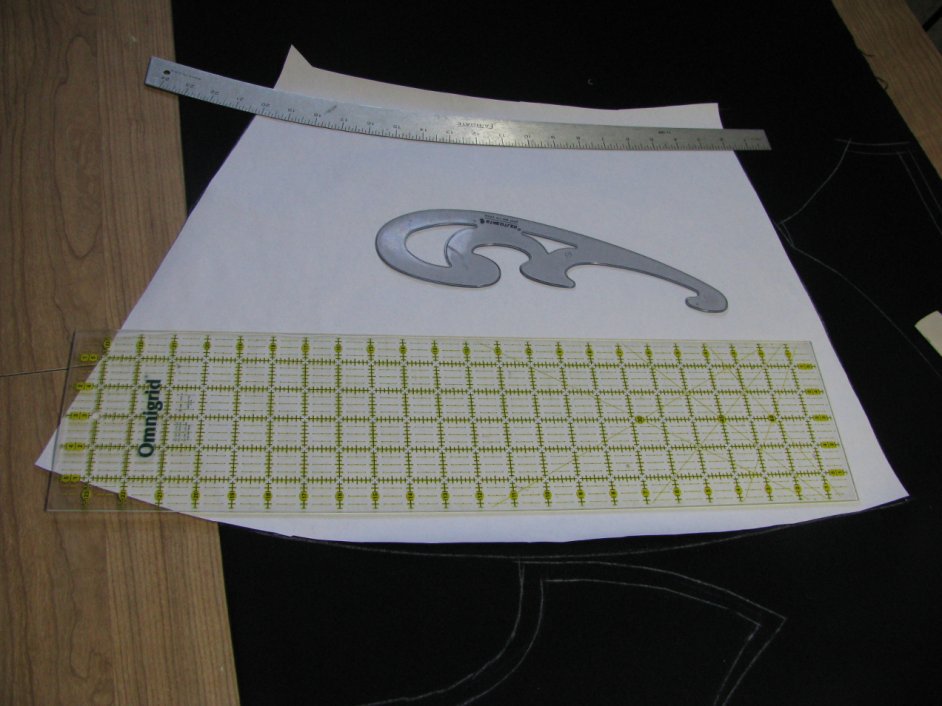
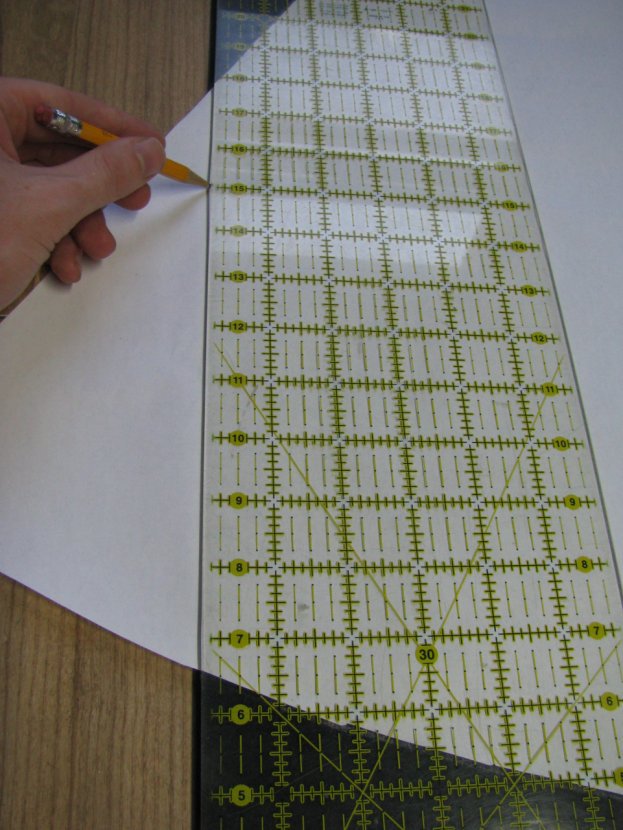
Now, add twice the seam allowance to this small triangle, which would be a 1⁄2 inch in our case (we’re using 1⁄4” seam allowances, remember). Then cut out this small piece of the pattern, and place it elsewhere on the fabric where it will fit. Snug it up into those little spaces you have still. The longest edge, which has the seam allowance, should be on the grain line.
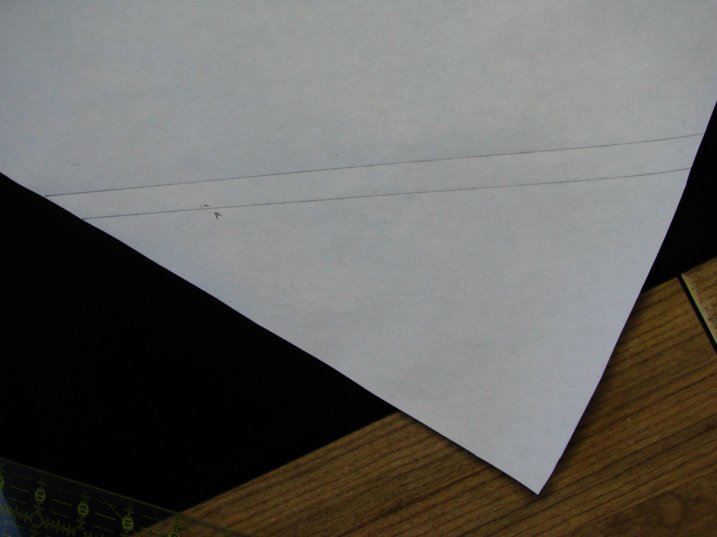
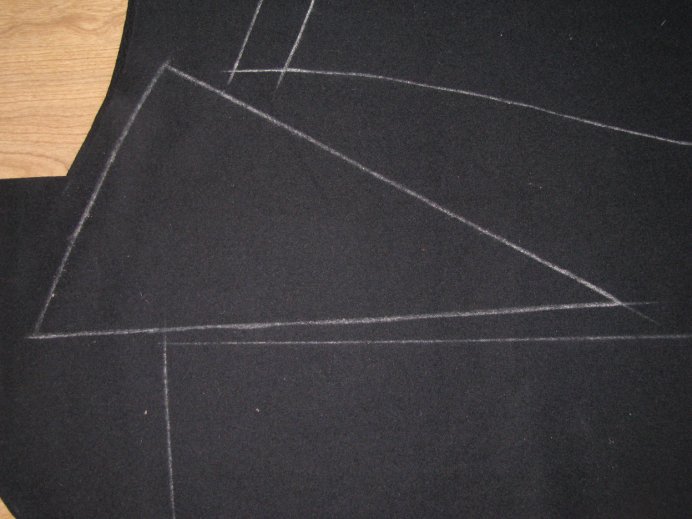
As you are chalking out the skirt, mark the darts, and then mark the tops, as if you had not cut out any darts in the pattern. This is important as you will not cut out the darts. They are just seam lines. Very important.
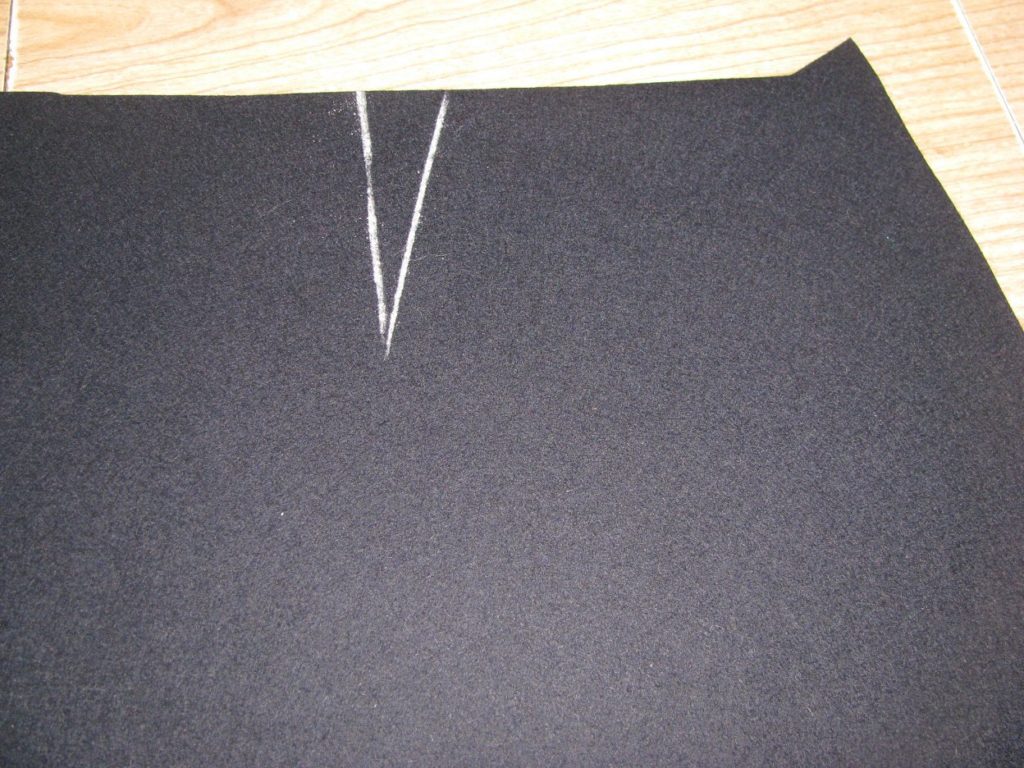
Cutting
This can be a nerve-wracking step for some people, especially if you are using expensive fabric like Hainsworth. It’s potentially hundreds of dollars down the drain if you make a major mistake. I remember reading about a tailor cutting an overcoat with fabric that was about $800 dollars a yard. He was very nervous as well! But if you are careful and check everything twice, you should be okay.
To cut, make sure the shears are held completely straight, not slanting to the left or right. This will help make sure both pieces are cut equally. Cut inside the lines, as the chalk line adds some width to each piece. Make sure you are cutting the inlays with the pieces! After a piece is cut, carefully move the pieces aside, keeping them together as one. This is necessary for the next step. It’s also a good idea to mark an X on the wrong side of each piece, especially if the right and wrong sides are similar in texture.
Tacking
Now, you must mark the inlays more permanently with thread, using tailor tacks. You learned the stitch in the previous module. Do the stitches, cut the threads, separate the pieces slightly, and then cut the stitches in between. I made a video of this process, sent to you in the email. Please view it if you are unsure. Make sure to mark any darts, as well as the chest line on the front of the coat, as well.
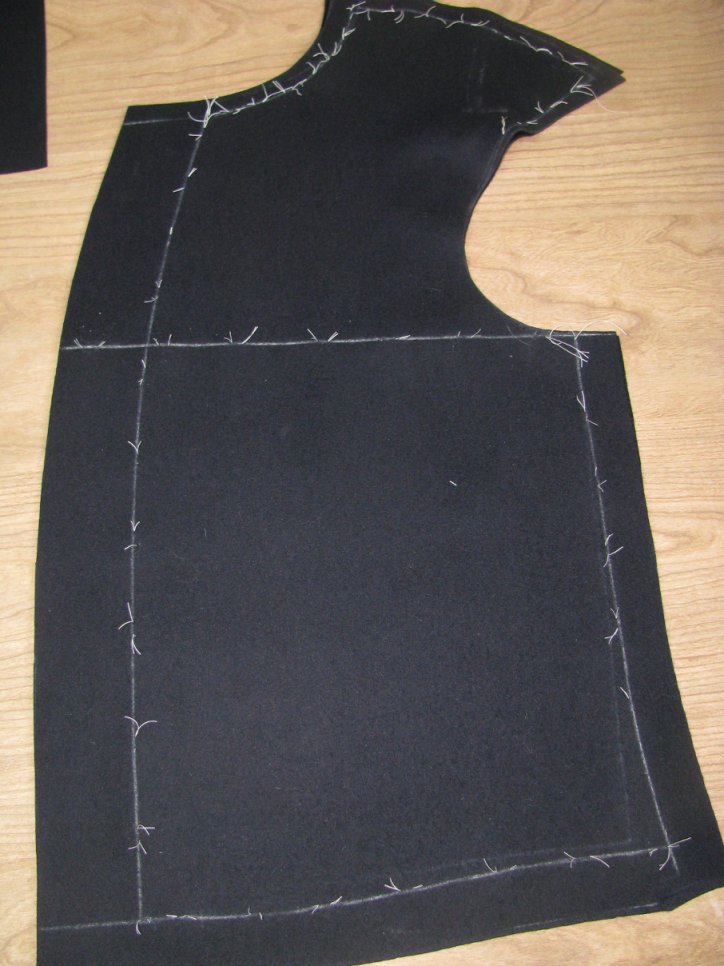
Keep the pieces together, still, for we have some ironwork to do.
Pattern Details
Before starting on the construction of this Federal enlisted frock coat, it’s important to have drafted and fitted a basic frock pattern using the instructions found in my frock coat drafting course.
There are no major changes to the pattern needed, though one thing is you may need to raise the neck point up an inch or so, which you can check for during the fitting of your muslin toile.
Ensure you have the following before continuing:
Forepart
Should be drafted as normal. Add a 1/4″ seam allowance along the top of the shoulder, neck, front, waist, and side seam. No allowance is necessary in the armscye as Devere seems to account for this in his drafts.
Side
Add a 1/4″ seam allowance along the side, bottom, and back seams. No allowance necessary in the armscye.
Back
A 1/4″ is needed around the entire piece except for the armscye. A 1/2″ seam allowance is recommended along the bottom so that it is slightly longer than the skirt piece, to account for any stretching during construction. This can be trimmed off later.
Skirt
Add a 1/4″ seam allowance along the front, waist, and back seams. No seam allowance is necessary along the bottom because you’ll account for the total length in the draft and it’s left as a raw edge anyway. Also accounted for in the draft is an extra 2″ in width along the front edge, that will be turned in and used as a self-facing later on.
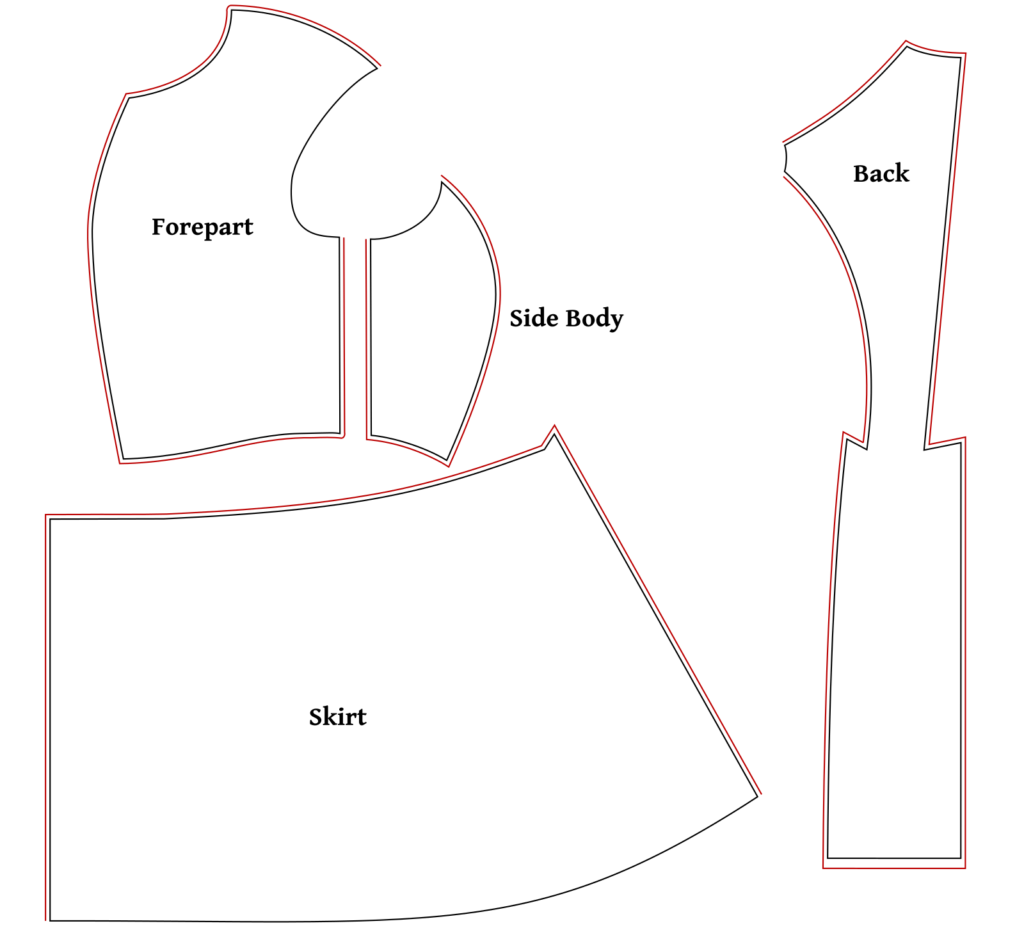